連載コラム『Jコスト改革の考え方』 第 1回目
従来の現場改善とどう違うのか
これをお読み頂いている方達は,全員が工場現場に詳しいと言う訳ではないので,製造現場を昔ながらの未決箱・既決箱のある事務所に置き換えて説明します。
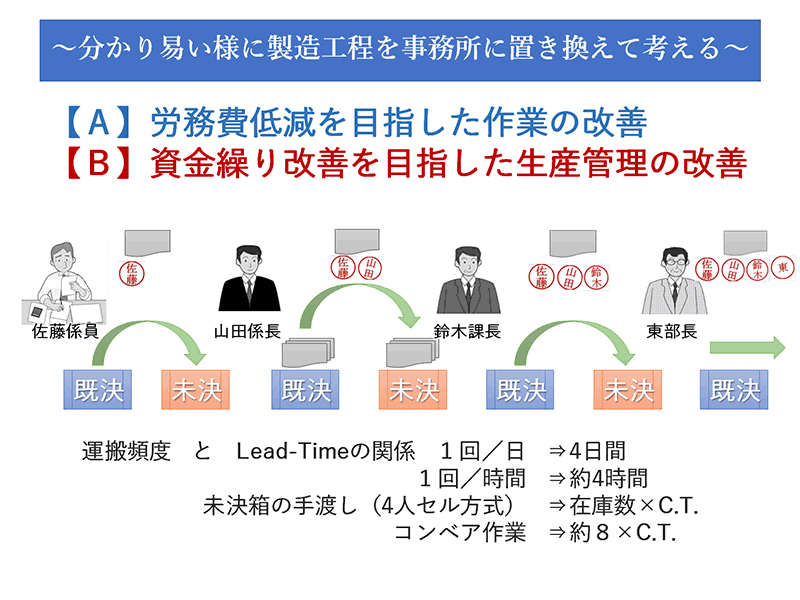
図-1の『未決箱』は加工前の材料置場,『既決箱』はその工程の完成品置場を表します。
IE(Industrial Engineering)が生まれたという100年前は全てが手作業でした。例えばBolt1本締めるにスパナで手締していましたから,ねじ1山あたり2〜6回締め付け動作をすることになります。レンチの持ち方から締める角度など細部に亘って作業のやり方を教え,訓練し,その結果を観察し無駄な動作を取り除いていくと言うIE活動の必要性が理解出来ると思います。これは図で言えば係長から部長までの作業に注目し,速く正確にすることで生産性を上げていく取り組みになります。
今日では,Bolt類はエアーや電動等の動力工具を使って締め付けるので誰でも1本あたり1秒足らずで締め付けることが出来ます。機械加工も部品をセットして起動ボタンを押せば,機械が加工してくれるようになり,IEの寄与度は大きく減少してきたのです。
そこで中国の起業家達は先進国から最新の製造機器を導入し,最新のERP(管理System)を導入し世界の工場と言われるまで躍進しました。
21世紀の今日,賃金格差が減じてくるに従って『精益活動(Lean生産方式)』が活発になり,どの会社も現場には『5S』に関する記述が掲示されるようになりました。ところがその実態を見ると,Supplierからの納入部品は
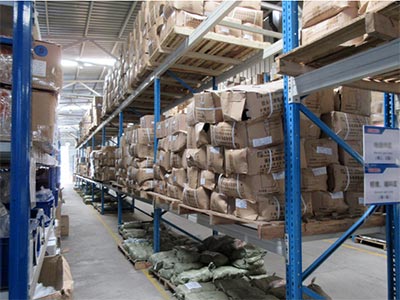
図−2のように倉庫に山積みされております。
作業現場に行くと,図-3のように人の作業はそれなりのレベルになって居ますが,『未決箱』に相当する材料や,『既決箱』に相当する完成品置場は図のように大量の在庫を抱えています。
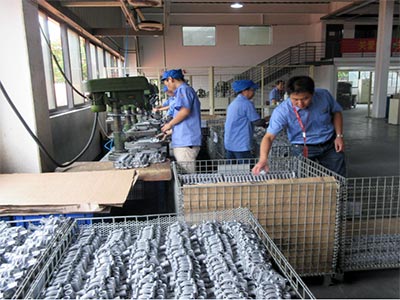
更に歩を進めて完成品倉庫に行くと図-4のように巨大な倉庫にメーカー在庫として堆く積まれています。
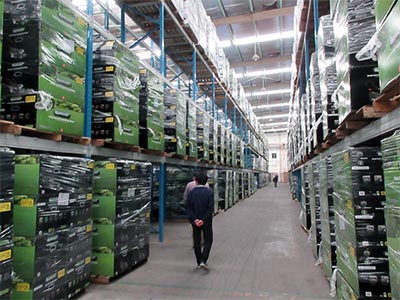
現在の日本国内のものづくりはどうなって居るのでしょう。
巷間で『トヨタ生産方式』といえば『5S活動』であり,『ムダ取り』とされています。先ず職場から不用品を排除し,無駄な動作を避け,部品や工具類を取り易いストライクゾーンに配置し,区画線を入れ,表示をキチンとすると現場は見違えるほど綺麗になります。これは図−1の係員から部長までの机の作業空間を整備したと同じ事です。
そして改善効果を計算すればかなりの工数低減が計上されますが,それは潜在能力のを表し,その分だけ仕事を増やせるキャパがある事を示していますが,現実にはその品目の生産に関与した人数(口数)は減っては居ない(会社利益に貢献していない)のが普通です。つまり,図の係員から部長迄各工程に手待ち時間を作っただけで終わっていることを意味しているのです。残念ながらこれが巷間のトヨタ生産方式導入効果なのです。
その一方で,中国企業と日本企業の受入部品在庫,工程内在庫(『未決箱』『既決箱』),完成品在庫を比べて見て下さい。中国ほどは多くないとしても,同じような症状を示しているのが現状です。御社は如何でしょうか・・・・・・・・?
『Jコスト改革』は上記とは全く異なる取り組みをします。
それは,図-1の係員から部長に至りまでの人に対する取り組みが出来ている事を前提にして,次のStepとして製品1単位に着目し,Supplierからの納入された瞬間から,完成品として客先に渡すまでの時間を『製造のLead-Time』として正確に把握し,この時間は今の会社の仕組みの結果であると捉え,その仕組みそのものを改革していくのです。
従来の作業方法の改善では現場Leaderや職長が主体の活動でしたが, 『Jコスト改革』では,営業・調達・製造・品質管理・生産管理・物流管理のTopから部課長が活動の対象になるのです。
この活動には新しく定義した以下のようなKPIを使い基礎収益力を向上させるために如何にした棚卸資産回転数増やすか,どういう仕組みにしたら着工から完成までのLead-Timeを短縮出来るのか,全社の仕組み,仕事の進め方を改革していくのです。
基礎収益力≡売上総利益/棚卸資産
≡(売上総利益/売上原価)×(売上原価/棚卸資産)
≡売上原価粗利率×棚卸資産回転数
次回は ナブテスコ社で伊牟田様を先頭にして工場一丸となって取り組んだ事例を交えなから,更に詳しく『Jコスト改革』に付いてお話しします。
2017年1月
(株)Jコスト研究所 代表 田中正知