連載コラム『Jコスト改革の考え方』 第 5回目
自社の現状を時間尺度で把握する(その3)
先回は,多くの部品が結合されていって一つの製品になって行く集約型生産のお話しをしました。今回はその真逆の,ひとつの素材から多くの製品を生産していく生産していく方式 『展開型生産』について考えていきます。
【4】展開型生産
(一つの素材から多くの種類の製品が生産される)
原油を分留して各種の化学原料を生産する工程や,溶鉱炉から出た銑鉄をもとにして,鋳鉄・鋼鉄・特殊鋼を生産していく工程などが,生産管理の教科書では 『展開型生産』の典型とされています。
しかし,よく観察してみると原油の分留工程は下の第1図のように,「石油ガス留分」「ガソリン・ナフサ留分」「灯油留分」「軽油留分」「残油」が同時に生成されてきます。これを 『同時型展開型生産』と名付ける事にしましょう。
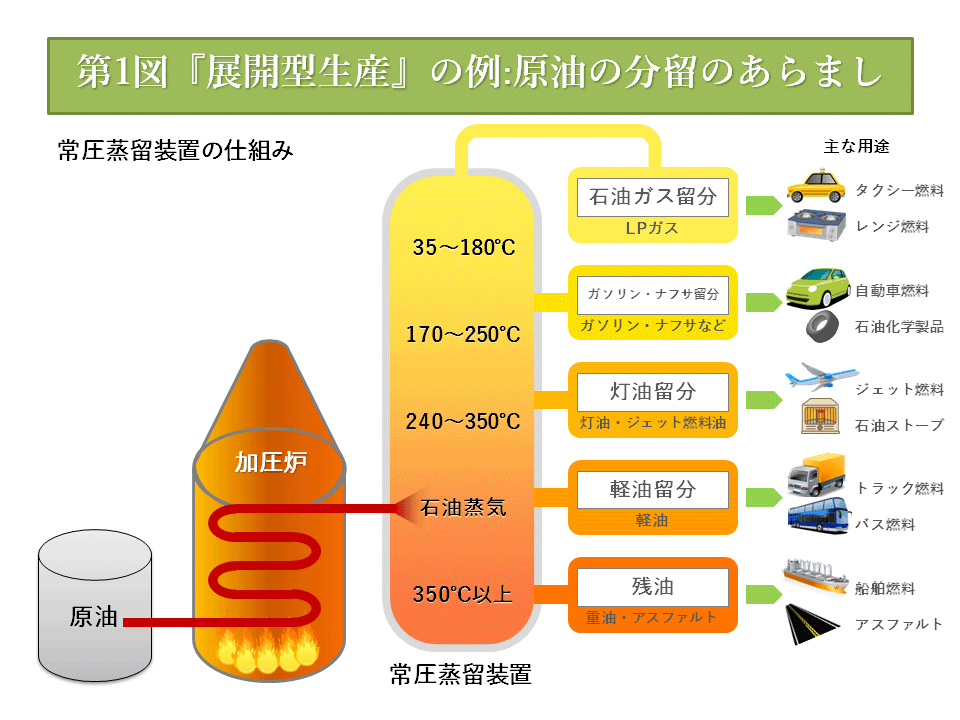
一方で溶鉱炉から取り出された銑鉄は転炉に入れられ,酸素を吹き込む事で溶け込んでいる炭素やリンなどの不純物を取り除き,鋼鉄に変えます。その後型に流し込んで固体にし,赤熱のまま棒鋼・L字鋼・鋼板などを多段ローラーからなる圧延工程で生産していきます。
鋼板は更に数十ミリの板厚の船舶用鋼板から,板厚1ミリ前後の自動車用鋼板,更には板厚0.25ミリのトタン板まで生産します。鋼板の場合はこのように生産計画に合わせて逐次個々の材料を仕上げていきますので, 『逐次型展開型生産』と名付けます。
4-1. 同時型展開生産型のLead-Time の捉え方
典型とされる原油の分留は,特定の企業でしかやられていませんが,一つの材料から 同時に多くの製品が生産される工程は幾つもあります。その一つは,成形工場内で1種類のペレット材料を幾つもの射出成型機に供給し,同時に何種類もの製品を製造する場合です。第2図はそのイメージ図です。
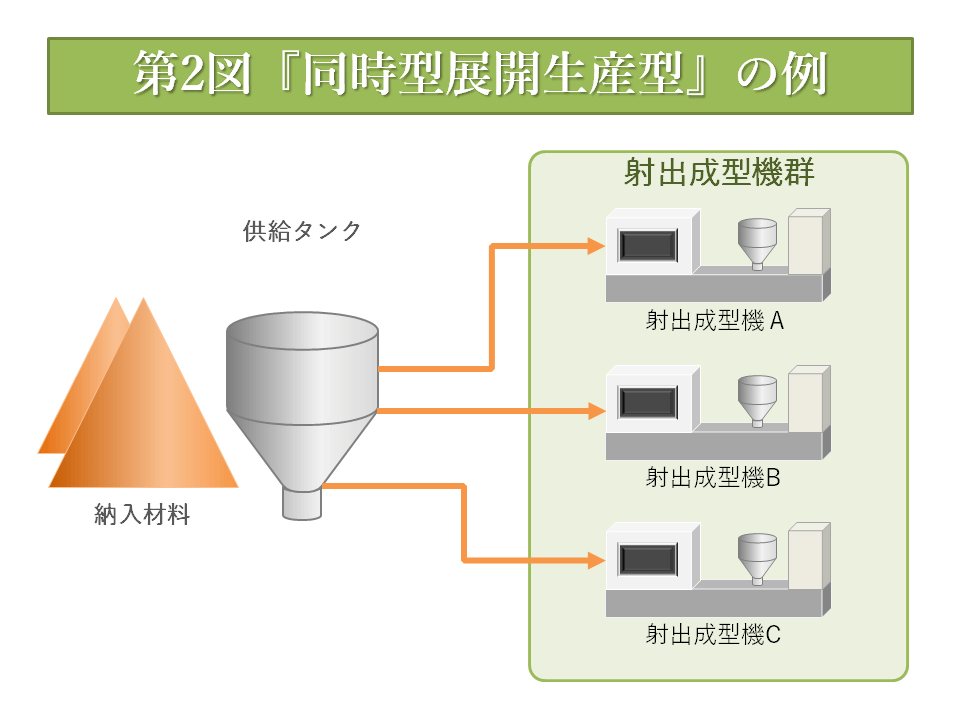
この図に於いて各射出成型機で使う1日当たりの平均使用量をQa,Qb,Qc kgとすれば,供給タンクから毎日供給される材料の量Q(=Qa+Qb+Qc) kgとなります。
では,この時,射出成型機Aで使う材料のLead-Timeはどのように考えたら良いのでしょうか・・・・。
それは,同じマンションの住人が駅からタクシーを相乗りいて帰った場合と同じと考える事が出来ます。材料受け入れから供給タンクの出口までは,樹脂ペレットは同じ動きをしますから,タクシー相乗り区間に相当し,ここまでの平均Lead-Timeは,受け入れ場の平均在庫量と供給タンクの平均有効在庫量(デッドストック分を除いたモノ)の和を平均使用量Qで割ることで求めることができます。
A・B・C・Dの材料平均Lead-Time=(受入場と供給タンク内の材料)/Q・・・(a)
A・B・C・Dの材料単独の動きのLead-Timeは, 相乗りタクシーから降りて各自の自宅までの歩いた時間に相当しますから
単独での材料Lead-Time=(個別配管とホッパー内材料)/個別使用量・・・・(b)
最終的に求める射出成型機A・B・C・D別のLead-Timeは
上式(a)と(b)から求められる事になります。
御社の場合は何日くらいになって居るのでしょうか・・・・?
4-2. Valeo社Lyon工場での実施例
1999年中部IE協会の欧米視察団で南仏リヨンにある自動車ランプ専門Makerとして有名なValeo社(傘下にCIBIEを持つ)のリヤコンビランプ専門工場を訪問しました。
工場内が明るく,見通しが良く,部品箱の少なさに驚きました。
やがてその原因が構内物流の基本姿勢にあることに気がつきました。御承知のようにISO規格のパレットは800×1200で大型トラックの車幅2500と小型トラックの車幅1700に対応していて素晴らしいと思っていましたが,この工場ではそれを四つ割りにした400×600のプラスチック容器をリヤコンビランプの通い箱に設定し,これを小さな手押し台車に乗せ,人が多頻度で運搬することで,滞留が無くなっていたのでした。
当時開発されたばかりの最新鋭のリヤコンビランプ射出成型機は,ストップランプの赤色,方向指示のアンバ色,バックランプの無色の三色のレンズを同時一体成形するという離れ業をやっていました。そして彼等はヨーロッパで生産されている車の大半のリヤコンビランプを作っていると豪語していました。
レンズの色は法規で決められていて,どの射出成型機でも同じ三色の樹脂ペレットを使っているので,ここで説明している 『同時型展開型生産』の典型となります。さぞかし立派なパイプシステムで供給タンクから樹脂ペレットが届けられてきていると思ったら,この最新鋭工場では25kg入りの紙袋(通称セメント袋)の荷姿で,しかも手押し台車で供給して居ました。その上,射出成型機についている材料を入れるホッパーは小型で約30kgしか入らないような,日本で見慣れたモノより小さなモノでした。
再度,第2図をご覧下さい。この図に描かれている納入在庫は,実は1トン入りの大きな袋で,受け入れ場に沢山並んでいて,しかも供給タンクにはその袋単位で供給できるように,2トン以上の容積を持つのが普通でした。共通のタンクから供給を受けるのが成形工場の常識でした。そのため,個々の射出成型機からどれだけの材料を受け取ったかの管理がやりにくく,型替えの時のロスは出し放題になりがちでした。
工場見学で我々はValeo 社の工場長から自慢げに以下のような説明を受けた事をおぼえています。
『Valeo社はフランスを代表する会社である。EUの通貨統合(1999〜)になれば,為替レートの壁が無くなり,EU内で価格と納期の厳しい戦いになる事は見えていた。我々はどうやったら欧州第1のランプMakerとして生き残れるか懸命に学んだ』ということです。
Valeo社Lyon工場の中でCash Flowを詰めてその結果が, 『Value Stream Map(モノと情報の流れ図)』を描き,自社の全体像を把握した上で業務を整理統合し,Lead-Time短縮して Cash Flowを良くすることに活路があると理解したと言います。筆者の立場からは 『トヨタ生産方式の経営者レベルの理解』ですが,彼等は誰かに教わったと言わず,自分達で考え,自ら出した結論がといっていました。この 『自分達で考えた』と言えることが一番大切なことです。
視点を変えると,Valeo社は各自動車メーカーと共同開発であったり,設計まで代行して『承認図』で採用されたりして,生産している各型式のランプは,全く別の時にはライバル関係の自動車会社に納品しているので,工場のスペースを納入先別に仕切り,専用の射出成型機でいわば代行生産しているような形にしていましたから,自社の利益確保のためだけでなく,納入先へのアカウンタビリティー(accountability)としても,1個当たりの材料使用量を把握し,しかもLead-Timeも短縮させているという事が理解出来ました。
成形工場に関係している読者は,18年前のValeo社と現在の自社とどう違うか比較してみて下さい。成形工場に関係ない方は,この基本的な考え方を理解しておいて下さい。きっとヒントがあると思います。
4-3. 逐次型展開生産のLead-Time
この典型的な例として鋼材の特に鋼板の圧延工程を例にお話ししましたが,この工程は皆様の日常と関係なさそうなので,以下は日常見かける工程の例で説明します。
1種類の帯鋼コイルからA・B・C・Dの4種類の部品を生産するプレス機械の稼働
- 4種類とも大きさは100mm位なので帯鋼1巻当たり5,000個出来るとします。
- プレス機はSPH1,000(1時間当たり1,000個出来る)とします。
1直8時間勤務なので8,000個/日の能力を持っている事になります。 - 現状は型段替えと初品確認に約30分掛かっているとします。
- A・B・C・Dの4種類の部品は自工場内で使う部品で,平均すると
A;2,000個,B;1,000個,C;500個,D;500個 毎日必要とします。 - 収容数500個の通い箱で,1日1回必要量を引き取る。
という前提条件で,作り方とLead-Timeの関係を考えます
【1.当初の段取り替えを最小にする対応】
1日の必要量は4種類合計4,000個で,帯鋼1巻で5,000個出来るので,材料や,プレス型の取替えの最小を狙い,在庫後補充生産を行っていました。
具体的には,全品目発注点を5,000個に設定し,生産ロットサイズは帯鋼1巻(5,000個)で生産していました。
実際運用してみると,同時に発注点になる日や,生産がない日が多発しますが,
A>B>C>Dの優先順位で仕掛けることで,全体で30,000〜24,000個の在庫(7.5〜6.0日のLead-Time)でプレス工場内は回っていました。(エクセルでSimulationして見て下さい)
【2.毎日,使った分を翌日生産へする対応】
プレス生産時間4,000個⇒4時間,段替え時間⇒0.5×4回=2時間
合計6時間で,2時間アイドル時間あり,十分間に合うのでこの案にしてLead-Timeの短縮改善を試みる事にしますが,後工程が毎日1回で必要量を引いていくとなると,生産するTimingと消費するTimingが違うために,欠品になる恐れがあります。
それで安全を期して,その日の生産順番が前後してもプレス工場の製品置き場の最小在庫量を1日分確保出来るように,最大在庫量を日当たり消費量の3倍に設定し,直間で在庫数との差異を調べその不足分を生産する方式にしました
プレス工場内の平均在庫量は直間では約2日分と推定されます。
【3.1日8回段替えし平準化パターン生産で対応】
『本流トヨタ方式』では,段替え時間が長いのは訓練不足に為であると考えます。時間の許すかぎり段替え作業を増やし,訓練を重ねると同時に,在庫低減を狙います。プレスの能力が不足気味の時は,自働化を進め,「昼休み」と「直間」に自動運転でプレスさせます。(この休み時間に異常停止した場合は保全が処置する・・・)
この例では,必要量はプレス機の4時間分ですから残りの4時間全て段取り替えに使えば8回出来る計算になります。それで以下のような500個ずつのパターン生産をすることにします。端数が出たときは最後の回に反映させます。
A(500)+B(500)+A(500)+C(500)+A(500)+B(500)+A(500)+D(500)
この生産が可能なように後工程からの引き取りは1日1回引き取りから,500個入りの通い箱で無くなったら取りに来るいわゆる 『定量不定時』引き取りにします。
これによってプレス工場内の在庫は,A・B・C・Dそれぞれ500個入りの通い箱各2〜1箱の在庫で回るようになります。つまり4,000個〜2,000個で廻ることになります。
これはLead-Timeで見れば1.0〜0.5日分になります。
このように,やり方を変えただけでプレス工場の製品在庫は
【1.】 7.5〜6.0日
【2.】 2.0日
【3.】 1.0〜0.5日
このように劇的に減少させることが出来るのです。
(使用部署の在庫も減りますが,今回は省略)
4-4.展開型生産の纏め
展開型生産は,原油精製や製鉄・製鋼,製粉業,ゴム製品工場,ソーダ工場など原材料を作っている装置産業に多いのですが,一般の製造業でも,プレスや鋳鍛造,射出成形工場など,工程の最初の方に存在しています。
今回の事例でお分かりのように,やり方一つで大幅にLead-Timeが変わるという性質があります。
今回の例を参考に,『自社の実態は如何に・・・・?』と,皆様の会社の実態確認をお薦めします。
2017年5月
(株)Jコスト研究所 代表 田中正知