連載コラム『Jコスト改革の考え方』 第 3回目
先ずは自社の現状を時間尺度で把握する
先回は現場の評価を
利益率=利益/原価
といった商売1回当たりの利益で見るのでは無く,下式のような時間当たりの利益で
収益力=粗利益/{ (平均原価)×(仕入れから売るまでのLead-Time) }・・・・(8)
評価すべきであると説明し, (仕入れから売るまでのLead-Time)を現場に行って調べ,1分1mmで描き, 赤線・ 青線・ 黒線で加工時間や運搬時間を識別しなさい。そうすればどれ位停滞が在り,Lead-Timeは短縮の余地があるかが分かると言いました。
意欲のある方は早速現場に行って時間測定したと思いますが,在る人は対象とした製品が全く動かないのにしびれを切らし中断したとか,測って停滞が長いことは分かったが,どうアクションを取ったら良いか分からない・・・という状態の人もいると思います。今回は時間の測定の仕方や,仕組みとLead-Timeの関係などを更に詳しく説明致します。
3-1.改善の第1歩は『現状把握』にある
品質管理の世界では『Plan Do Check Action (PDCA)』のいわゆる管理のCycleを廻せと教わります。これは全くのZeroから始める場合は正しいのですが,いわゆる改善マンが取り組むのは 『今までやってきた事をこれからどう向上させるか』というテーマになります。この場合は今までのやり方をしっかり把握すること,即ち 『現状把握』が改善の第一歩になります。
つまり,@Check(現状の把握),AAction(応急処置・暫定対策),BPlan(本対策立案・システム設計),CDo(現場展開),即ち 『CAPDと言う管理のCycle』になるのです。
3-2.『客』や『製品』の立場で現状を把握する
第1回で御説明したように従来の作業者動きや作業時間測定から離れて, 『客』や 『製品』の立場になって,何処で何時間待たされ,何処で何分間サービスを受けたかを観察するのです。以下調査するときの留意点を説明します。
3-2-1.受入場から始める
Supplierから納入された材料や部品は品質と員数を確認して検収し,これによって所有権が自社に移り,『原材料在庫』になります。
確認事項-1 Supplier毎に納入時刻が決められているか?
納入時刻が決められて居れば,Supplierはトラックからの荷下ろし場所確保の為に競って早く到着しなくて良いので運搬時間が少なくて済みます。自社の受入業務は平準化して混雑回避が成されるのでスムーズになります。納入された部品は即ラインに運び使える・・・Lead-Time短縮になる。Supplierにとっても,受け入れ場にとっても,良いこと尽くめなのですが,世間では意外とやられていません。御社が未だなら即実施すべきでしょう。
確認事項-2 納入された部品は使用場所へ送る配送レーンに置かれるのか(Cross Dock)?
もしそうだとすれば,直ちに使用部署に届ける体制になって居ると言うJust In Time体制になって居る事になります。これが一旦別の倉庫の棚に入れられ,生産計画に合わせてPickingしているようだと,数日分余分な在庫を抱えていると思って間違いありません。
確認事項-3 検収は自社の注文書との照合で行われているか?
これが添付の納品書との対比,で行われているのであれば,多大の在庫があっても不思議ではありません。鰻丼を頼んだのに天丼が納品書とともに届けられたばあい,検収をパスしてしまう事態が起こるからです。
このような確認をしながら,受入場で行われている作業を 『扱われている部品の立場』から観察し,所要時間を計測していきます。
確認事項-4 調査目的によって範囲が変わる。
『在庫低減』が目的であれば,受入検収が成された時点で所有権がSupplierから自社に代わりますから,この時点からが調査対象になります。
しかし 『Order-to-Delivery-Lead-Time』を調査する場合は,在庫後補充のLead-Timeを確認する必要があるため,Supplierに発注してから納入・検収までの時間も調査対象になります。
3-2-2. 絵文字を使い見易くする
下図は筆者がものつくり大学時代,卒業研究でLead-Timeを調査したときに学生達が使用した絵文字です。これを参考にして各社自由な発想で決め手頂いて結構なのですが,以下のような分類を明確にして置くと,改善実施時に便利です。
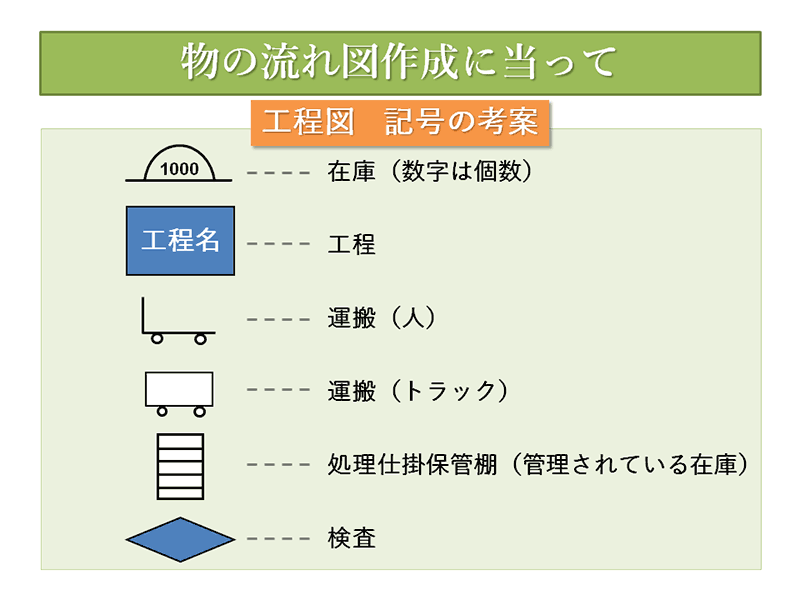
- 運搬は,手の余っている人なら誰でも運べる手押し台車等か資格の要るフォークリフト,クレーン等の区別をすること。
- 在庫は,乱雑に置いてあるだけの在庫は山をイメージする表示とします。種類と数量を管理して居る在庫は棚をイメージした表示にしハッキリと区別します。
- ロットサイズは,明記すること。
等の取り決めをしておきます。その上で実態の調査を始めます。
3-3. 群れを追わずに個の動きを追え
調査しようとしている工場の現場では様々な製品が流れています。
それはあたかも大きな川の流れのようでも在り,駅に出入りする乗客の様でもあります。この流れを解析するには川であれば浮きを投げ入れ,その流れを観察すれば その実態を把握することが出来ます。乗客であればその中の個人に着目し,その個人の動きを追跡してその実態を解明するのです。
昔,物理の時間に勉強したと思いますが,池に石を投げ込むと波が立ち同心円状に広がっていきますが,水面に浮いている葉っぱに着目すると,同じ場所で往復運動しているに過ぎないことが分かります。
トヨタ方式の入門時には,群れ(池の波)を追わずに個(浮いている葉っぱ)を追えと徹底的に教え込まれた上で現場観察に出向くのです。
3-3-1. 具体的に対象物を選定する
原材料が受け入れ場に入り,加工現場,組付け現場を経て完成品になり出荷され納品されますが,大きく分けると次の3形態があります。
【1】 一本道型生産 (一つの粗型材が加工されて完成品になる・・・)
【2】 集約型生産(多くの種類の部品が組み立てられて完成品になる)
【3】 展開型生産(一つの原材料から多種類の製品を作って納品する・・・)
【2】,【3】のLead-Time調査法は来月以降御説明することにして,今回は一番簡単な【1】について以下説明いたします。
【1】は一番簡単で基本となる形態です。出来れば1個を追いかけて欲しいのですが,現実には1個を生産している場合は少なく,大きなロットで生産しているのが普通です。しかもそのロットサイズは常に変動しているので,此処では1個に拘るか,又は1パレット等に,一般的には 『1単位』に着目して調査します。
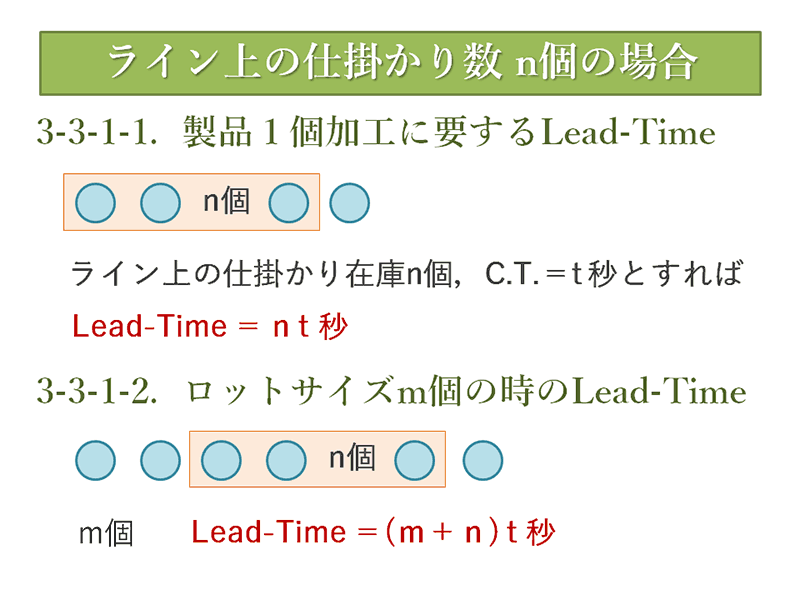
ロットサイズが大きいほどLead-Timeが長くなることが解ると思います。
実際には,所定の加工工程に製品が到着しても他の製品の生産が終わり,この製品の加工順番を待つ時間= 工程待ち時間
順番が来てから着目した製品を生産する準備の為の時間= 段替え時間
等がこれに加わります。現状調査とは,これらをキチンと測定していくことを指します。
下図は時間を測定する準備として4,000個ある材料から1ロット2,000個で次々と加工されていく様子を図示したものです。加工時間は分かっていますが,何時何処の指示で運搬し,加工したかの実態を観測することで製造のLead-Timeを測定出来ます。
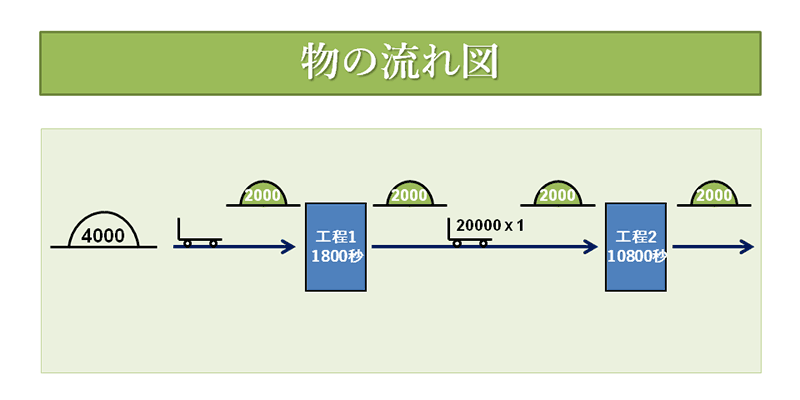
3-4. 個の動きからから管理の実態を描き出す
一般に測定した所要時間(Lead-Time)は,実測値として大切なDataですが,この時間は測定のTimingで大きく変動します。
例えて言えば,それは東京本社から札幌支店に出張するのに要する時間と同じで,実測した時間は貴重なデータですが,出発した時刻によっては大きな差がありそのまま認定するには難があります。会社としての出張所要期間として査定するためには,個々の交通機関の運行ダイヤ,移動の所要時間を調べ上げて合理的に査定していくことが必要です。
このように,移動に要する時間や加工に要する時間は毎回ほぼ同じでも,待ち合わせの時間は実績時間では著しく変動し,その原因は交通機関であれば運行ダイヤ同士の整合性にあります。
生産現場では前工程と後工程との間の運搬のTimingや生産のTimingの整合性が重要になります。『渡りに船』と言うことなら良いのですが,出た後に到着では間が悪いのです。
言い換えれば『生産管理部署』が現場に対して『どの製品を』『何個』『何時から』生産・運搬・検査するように指示しているか・・・・・,もしくは,各工程がどういうルールで計画し・着工しているのか・・・・・等の現場管理の実態を明らかにしないとLead-Timeの査定は出来ません。
その実態を明らかにして図形化したモノが海外で流行って居る 『モノと情報の流れ図(Value Stream Map)』なのです。この描き方の詳細は知りたければ,ネット上に参考文献は多々ありますが,いずれもトヨタ生産方式からの引用で,情報の流れは『かんばん』で表現されていますのでそのままでは使えません。
皆様の会社では生産管理用のコンピューターSystemが導入されており,しかも導入から20年近く経っていますのでその全体像が分かっている人が少ないのが普通です。ですから自社の現状を知るためには,皆様ご自身で現場に出向いていって,実態を確認しながら詳しく調べる必要があります。
この事を犯罪捜査では 『現場100回』と言い,トヨタ生産方式では 『現地現物』と言い,在る人達は 『5ゲン主義』と言います。如何に大切なことであるかお分かり頂けると思います。
調べてみると,コンピューターSystemは現場の隅々まで指示を出しているのは希で, 『着工可能な日時』と 『完成納期』だけを指示するだけで,細部は現場の 『自主運営』に任せている場合が殆どです。つまり,生産指示と現場ルールとが渾然一体として居るので,これを調べるには製品に密着して行き,加工や運搬がどんな指示で行われ,その結果がどう連絡(Input)され,どんなLogicで次の指示に繋がっていくのか逐一調べ,解き明かす必要があります。
その調べた結果を上図のような 『モノの流れ図』に描いていけば,御社流の 『モノと情報の流れ図』が出来上がります。現場でのOperationの実態を書き写し,問題点を発見し,改善していくためのツールですから,自社内で分かれば良く,御社の作業工程に適した独自の描き方を工夫すれば良いと思います。
ただ,『モノと情報の流れ図』として使うためには欠かせない項目があります。
- 各所に置かれている在庫は量を管理してあるか否か
- 運搬は定時(ある時間間隔で運ぶ)か定量(ある量になったら運ぶ)か
- 運搬に要する時間と何処からの指示で動くのか
- 生産のLead-Timeは・・・1個当たり,1ロット当たり,段替え時間
等々が必須です。
現場に於ける生産の実態を調べていくと下図のようないわゆる『日程表』に出くわします。
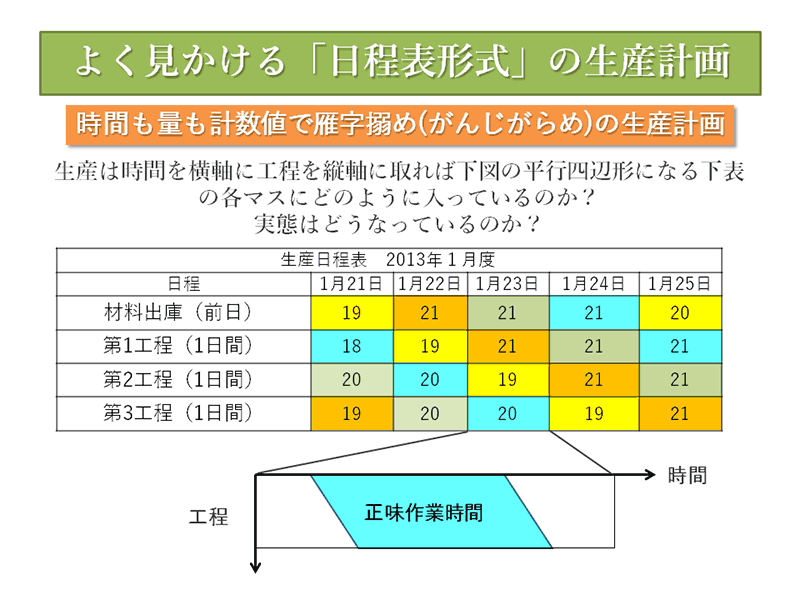
色で材料出庫から第1工程〜第3工程に1日ずつ掛けて製品が完成していく様に生産指示している事を表現しています。
1月23日の第3工程の中味を図示してありますが,この工程はAからDまで4人で作業をして居ました。朝礼の後おもむろに生産準備しAから仕事に掛かりますが,最終工程のDには暫く仕事が来ません。1日の終わり際になるとAは一番先に仕事が終わります。縦方向にA〜Dの作業を並べ,横軸に1日の勤務時間を入れると青色の平行四辺形になり,朝晩に大きなロスがある事が分かります。ロスが一杯あってもこの日には20個しか作ってはいけないので,Lead-Time短縮も,工数低減をも,達成が出来ないSystemになっている事が分かります。
このように,現場の実態を写し取る為の 『モノと情報の流れ図』を描いていくと,生産性の伸びを抑えているのも,Lead-Timeを長くしているのも,実は生産指示のやり方に課題がある事が分かります。 現場は『管理部門』に指示された通りにやっているのです。
これを参考にして再度御社の製造現場はどうなっているのか再度 『現状把握』に挑戦してみて下さい。様々な課題が見つかると思います。
次回は説明し残した【2】集約型生産と【3】展開型生産の調査法について御説明した後で,ナブテスコ様の実践事例を紹介いたします。お楽しみに・・・・。
2017年3月
(株)Jコスト研究所 代表 田中正知