連載コラム『Jコスト改革の考え方』 第 11回目
自社工程を再構築する
第9回目でやった自社内の改善では,材料切り出しから完成まで,2時間で5個生産という同一のTACT-Timeを設定し,整流化することで,工程間在庫を削減させ仕掛かり在庫量を5日分から3日分に短縮しました。これは一見素晴らし改善に見えますが,此処で改善の手を止めると,組織体としては自己満足に陥り『墨守体質』になりやすいのです。
その昔,トヨタでは1970年代大野耐一氏が『今は拙いやり方だと思え』,『常にもっと良いやり方があるはずだと思え』と言っていました。1990年代になると,奥田社長は『今日のトヨタの敵は昨日のトヨタだ』『変わらない奴が一番悪い』と常に口にしていました。
最近はどうか知りませんが,昔は良く職場の先輩から「お役所仕事」と言う言葉を聞かされました。役所では,入社すると先輩から仕事を教わり,教わった通りに仕事をし続けることをもって先輩から「良し!」と評価され,先輩より旨いやり方を考えついて実施すれば,先輩の面子を傷つけ,出世に差し障りがでる…と信じられており,だから仕事のやり方は改善されず,ドンドン劣化していくのだ…と聞かされて居ました。
一方,民間会社は,自由競争の中でライバル会社を差し置いて御客様にご愛顧頂きながら,尚かつ年々給与を上げていかねばならない。 そのためには常に現状の仕事を「目的は何か」を問い続け,先ずは客様のために,次には自社のために今のやり方で良いのか?もっと良いやり方はないか?真摯に問い続けていくことが求められている…と教えられてきたものでした。
具体的な例を挙げて御説明しましょう。現場に行くのにヘルメット着用が義務付けられている職場があります。法的に着用が義務付けられた作業はありますが,作業するわけでもない訪問者にヘルメットを着用させるのは,事業主である製造課長の判断なのです。多くの製造課長は何も考えず歴代課長の方針を踏襲(墨守)しているようです。しかし,職場の安全を追求する製造課長であれば,ヘルメットを着用しなくても良い職場を目指すべきで,現状では〇〇と△△が不安全なのでやむなく着用させているが,来年度までに対策し,ヘルメット不要の職場にする・・・・というのが有るべき姿なのです。この文脈で考えると,ヘルメット着用というのは,神社の御札と同様の安全祈願のお呪いでしかありません。
最近,大企業で品質保証に関する不祥事が相次いでいますが,これは先のヘルメットと同じで, 「現状を真摯にもっと良いやり方はないか真摯に問い直す姿勢」が欠如していた為ではないかと推察されます。
冒頭に述べた危ない状況とは,これ以上の改善はないと思い込みやすいということなのでした。そこで,更なる改善に挑戦しましょう。
以下にお話しするのは,改善への取り組み方,考え方のヒントになればと筆者が考えたフィクションです。実際は改善に当たっては秒単位で作業時間を査定しなければいけませんし,読んでいて疑問が湧く部分が多々あると思いまが,そこはご容赦ください。
11-1. 現状(第9回で実施した改善内容)の確認
先回の第10回で御説明しましたように,『自社』の後工程には甲,乙,丙,丁等の各社があり,そのうち先回までは『自社』と甲社間の『洒落た木製机(B)』を例にとって改善の説明をしてきました。今回改善の対象になる『木製机』でいえば,乙社と丙社にそれぞれ『木製机(A)』,『木製机(C)』の二種類を供給していて,合計三種類の『木製机』を供給していました。商品開発は甲,乙,丙社と独自に行ったため,大きさはほぼ同じですが,天板の形状や脚の太さが違っています。
そのため,第9回でお話しした工程において『木製机(A),(B),(C)』の作り方は
- [0]材料調達工程…………(A)(B)(C)共通で計画発注
- [0]と[T]の手掛けた材料置き場…………(B)のみを改善
- [T]材料取り工程…………(B)のみを改善
- [T]と[U]の間の仕掛かり在庫置き場…………(B)のみを改善
- [U]加工工程…………(B)の専用工程のみ
- [V]塗装工程…………(B)の専用工程のみ
- [W]組立・検査・個装工程…………(B)専用工程のみ
- [X]出荷梱包・倉庫入れ工程…………(B)のみを改善
となって居り,木製机(B)のみを取り上げて改善し,評価したものでした。
11.2. 今回の改善 (混流1個流し生産を目指す…)
今回取り組む『木製机(A),(B),(C)』の作り方は,市場の量変動にFlexibleに即応出来る体制を確保しながら,仕掛かり在庫を低減することを狙い以下のよう改革を実施することにしました。
- [0]材料搬入工程………… (A)(B)(C)共通で後補充発注
- [0]と[T]の手掛けた材料置き場………… (A)(B)(C)共通で改善
- [T]材料取り工程…共通工程………… 在庫後補充生産化
- [T]と[U]の間の仕掛かり在庫置き場………… 共通で最大/最小間で在庫量の管理
- [U]加工工程………… (A)・(B)混流生産,(C)専用生産
- [V]塗装工程………… (A)・(B)混流生産,(C)専用生産
- [W]組立・検査・個装工程………… (A)・(B)混流生産,(C)専用生産
- [X]出荷梱包・倉庫入れ工程………… 共通…顧客に向けて配送手配
11.3. 各工程の改善内容と所要時間の査定
木製机(A)(B)(C)の夫々の工程での詳細な作業内容の実態を調査し,混流生産による1個流し実現のための改善内容と,改善後の所要時間を査定すると以下のようになりました。
[T] 材料取り工程
天板はL2400×W1200の定尺ものから,全て共通の1100×790の寸法に切り出す作業をしています。 脚は断面90の角材で,長さ1800 の定尺ものから全て共通の長さ800の寸法に切り出して居ます。従来は,前日中に翌日分の生産指示が天板何枚,脚何本という形で来ますので,午前中に天板を準備し,午後に脚を準備して居ました。
第9回に述べた改善では,木製机(B)だけを2時間単位で5個分ずつ,つまり天板5枚と脚20本を準備するようにしましたが,残りは,従来通りいその日の内に準備すれば良いという状態でした。(机は『脚』という単位で数えるのが常識ですが,本稿では脚を違う意味で使っているので,『個』という単位で表す事にします)
【今回の改善】
今回の『混流1個流し化』については,天板は一枚の材料から3枚取れるので,最大在庫9枚,最小在庫3枚の範囲内で「在庫後補充生産」して行くことに決めました。加工に要する時間は6分/3枚と査定しました。
1本の角材から脚は2本取れるので,天板と合わせて,12本単位で脚を切り出すようにして,最大36本,最小12本の間で「在庫後補充生産」にし,所要時間は6分/12本と査定しました。これにより,(A)〜(C)共通の材料取りが1カ所で行われ,生産変動に柔軟に対応出来るようになりました。
[U]加工工程
木製机(A),(B),(C)の三種類は,同じ粗型材から作り出していますが,一番古いモデルである(A)は,直線がテーマとなっており,平面図は長方形で4隅が50Rの丸みがついています。脚も一辺85の4角柱に10Rの面取りをしただけのモノでした。
(B)は丸みを強調したデザインで,天板は四隅の丸みが100Rと大きくなって居ます。脚は同じ一辺85角で20Rの面取りをしてあります。
(C)の4隅は100R程ですが,長辺も短辺も緩やかな曲線で構成されています。脚の断面は天板に似せて,4面はかまぼこ状に膨らみを持たせ,稜線は10Rの丸みを持っています。
木製机(A)が最初に35個/日…<生産能力 13分/個>の生産計画で立ち上がり,更に(B)も同様に35個/日の計画立ち上げられ,最後に(C)が,加工量が多いけれど,高性能な機材を入れる事として前者に同じく35個/日の能力で生産準備して立ち上がりました。
このように,工場の空いている場所を選んで逐次立ち上げていったため,(A),(B),(C)は離ればなれの専用ラインとなっておりました。市場の変化により,今では,一番古いモデルの(A)は約10個/日…<TACT-Time 46分/個>,次に古いモデルの(B)は約20個/日…<TACT-Time 23分/個>,最新モデルの(C)は30個/日…<TACT-Time 15.3分/個>で生産しています。
1セット分の脚(4本)の生産能力は天板のそれと同一に設定されているため,(B),(C)の要員は天板と脚夫々1名ずつで廻しており,(C)は生産量が少ないので天板と脚を1人で廻していて,合計で5名おりました。
前日与えられた計画に基づいて,1日単位の生産を行っていましたが,先回(第9回目)の改善では,(B)のみを5個ずつ2時間で生産するように変えたのでした。
【今回の改善】
生産設備の互換性を調べてみると,天板,脚とも最新鋭の(C)の設備に一寸した段替えをすれば(B)も(A)も生産が出来る事が分かりました。更に(B)の設備でも小規模の段替えで(A)の生産が出来ることも分かりました。また生産実績を見ると(A)〜(C)の個々には変動はあるモノの,(A)〜(C)合計の変動は比較的小さいことから,(A)〜(C)の三カ所での生産を,(A)〜(C)の天板専用工程と,(A)〜(C)脚部専用工程の二カ所に統合を図ることにしました。具体的には,互換性のない(A)の設備は使用しないことにして,天板も脚も(A)用と(B)用は従来の(B)の設備で小段替えしながら混流生産し,(C)用は従来通り(C)専用設備で生産する事にし,高負荷時には(B)用も生産するようにしました。
先回(第10回)説明したSupply-Chainの改革をすると,後工程の販売会社との間の在庫を大幅に減らす必要があります。そのために一時的に操業をDownさせる必要があります。その操業Downの時間を有効活用して,今回の社内の大改革を実施する計画にしました。
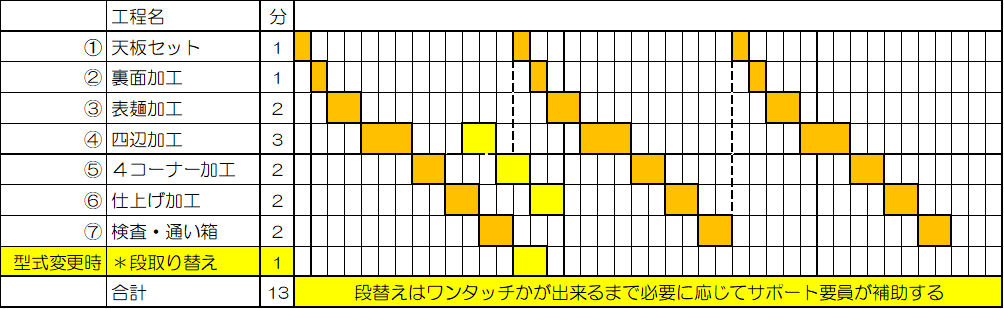
(A)(B)(C)は共に同じ上記の標準作業組合せ票のようにCycle-Time 13分で作業が出来るようになって居ます。(B)用設備で(A)を加工するときは平面形状が違うので,治具の段取り替えが必要になります。これがワンタッチで出来れば,従来5人掛かっていた加工ラインが,理論上は天板,脚各々一人の,合計2人で出来ることになります。
しかし今回の改善テーマは要員削減ではなく,(1)製造Lead-Time短縮して市場への応答性を高め,(2)更に市場変動に即応できるように生産能力に余裕を持たせることによって,安全在庫を縮小することにあります。そのために現在人員の5名は温存し上記テーマ(1)と(2)がうまく行くような配置を考えました。現状では,加工機に天板をセットした後,外形を整え,端面をトリミングし,表面と裏面を仕上げる…の3工程は混流生産時にはツールの交換を要します。この作業のために専任者を天板工程に貼り付けます。脚の工程も同様で手返しの要員を貼り付けます。最後の1人は工程間の1個流しのための要員としました。
これにより,上図の生産ダイヤグラム(この場合は人が付ききりなので『標準作業組合せ票』と同じ意味になります)が成り立つようになりました。結果として,(A)と(B)ラインは天板,脚(4本セット)に対してTACT-Time 15分(30個/日),に対してLead-Time 13分,Cycle-Time 13分で廻せるようになりました。
2人で作業する前提でいますが,1人作業では第11-1図の黄色の作業(段替え作業)が加わるためにCycle-Timeは19分になります。
緊急に増産が必要な場合は,@+A+B+C=7分+段替え2分,D+E+F=7分+段替え4分という作業分担にすると,Cycle-Timeが7分から11分で生産が可能になります。在庫を圧縮してOrder-to-Delivery-Lead-Timeを短縮するためには,市場の変動を上回るような瞬発力があることが理想とされています。そもそもこの改善は,筋肉質の強い会社にするのも目的の一つですが,もっと大きな,市場に於ける競争力を増し売上を目指すという目的もあるからです。
ここまでの改善は,加工工程が半自動で,要員が加工機に付ききりで作業することを前提に行われています。トヨタ生産方式に基づいた改善であれば『自働化』の考えを導入し,人の仕事と機械の仕事を分ける事によって,加工完了を待たず,加工開始を確認して次の加工機に移っていく作業に変更出来,これによってより少ない工数で,より短いLead-Timeでの生産が可能になりますが,これは次回の改善テーマとします。
[V]塗装工程
(A)(B)(C)用加工工程に対応した塗装工程が3カ所,日当たり35個の生産能力で設置されていました。
第9回目で説明した改善は,加工工程と同じ(B)の生産工程のみで行われました。具体的に言うと,二つあった乾燥炉に入れられる量単位で,下塗り⇒中塗り⇒上塗りと大ロット生産していたものを,当時の生産量が1日20個であったことから,1日4回,一つ目の乾燥炉を第1工程として,5個ずつ下塗りし,2つめの乾燥炉を第2工程として,5個ずつ中塗り・上塗りをするようにしたのでした。
今回は,加工工程と連動し,最も売れている(C)は従来通り専用ラインで塗装し,売れの鈍り始めた(A)と(B)は混流とし,(B)用の塗装ブースで生産する事を目指し,検討を重ねました。一般に塗装工程では,乾燥炉で加熱する時間が決められ,混流生産すれば,今までの1日20個から,(A)と(B)で1日30個ベースの生産になり,元々,35台/1直の能力を前提に作られていますが,『1個流し生産』が可能か否かが改善上の問題だったのです。
塗装工程の詳細を説明しますと,塗装入口で空気洗浄されてから塗装工程に入り,形状が全く違う,天板と脚とは塗装工程の中で別ルートを通りますが,先ず塗装治具のセット(約1分間)し,必要な部分は一度に塗装できるようにします。次に,下地塗装(約2分間)を行い,炉に入れて乾燥(約22分間)させ,炉から出てきた下地塗面のサンディング(約3分間)をします。ここまでが塗装の第1工程です。
塗装の第2工程は,中塗り(約2分間)から始まります。塗装セッティング炉(約10分以上)で塗面を生乾きながら平滑にした後,上塗り(約2分間)し,乾燥炉(約20分間)に入れます。乾燥炉から出して,塗装検査(2分)して完成品用通い箱に入れて作業完了となります。
ロット生産から1個流し生産にするために,乾燥炉の中にレールを敷き,入口から押し込むことでコンベアの機能を持たせ,出入り口を二重扉にして保温機能を持たせました。
正味加工(塗装)時間は,
- 第1工程=取り出し1分+セット1分+下地塗装2分+乾燥炉40分+サンディング3分=46分
- 第2工程=中塗1分+セッティング10分+上塗1分+乾燥炉20分+検査2分+治具外し1分+塗装完成品置き場1分=36分
となります。
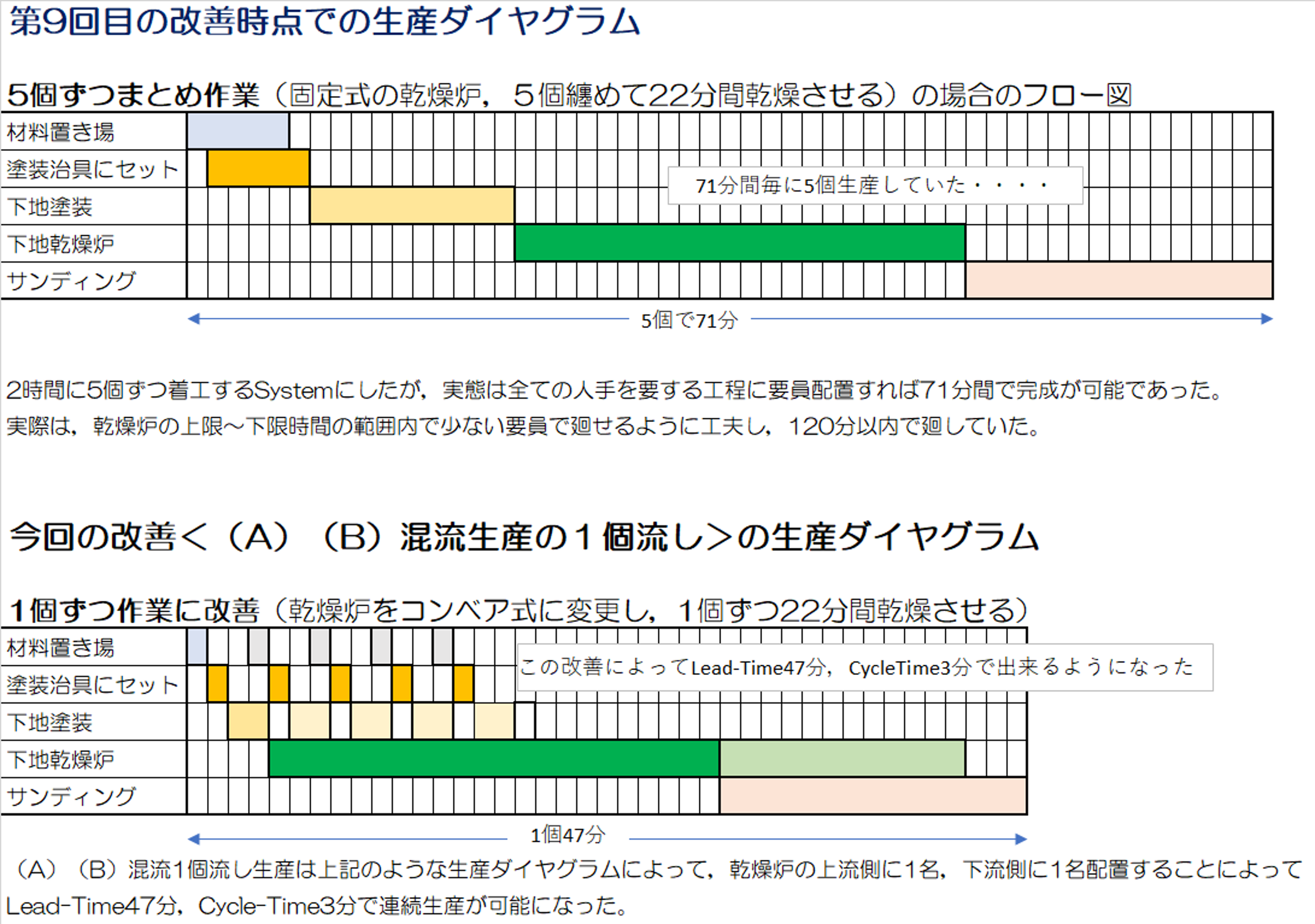
上記の第11-2図に塗装第1工程における,第9回目で述べた改善点と,今回の改善点を生産ダイヤグラムで表現してあります。塗装工程の特色は,例えば乾燥炉では,塗料が固まるための最短時間と,焼きすぎて劣化してしまう最長時間の間の許容時間が長く,この特徴を使って柔軟に作業に組合せをしています。標準作業組合せ票では,最小の工数で最大の生産量を確保する為のTimingを表現したモノとは違っています。ここで描いた生産ダイヤグラムは,人手の掛かる場所全部に要員が居る場合の 最短生産Lead-Timeを表していると認識してください。(これは一般論では無く本稿限りのお話しとご理解ください)
図から分かるように,改選前の5個ロットで生産では,5台塗装を完了させてから乾燥炉をスタートさせますから,その間がロット待ちになり,71分掛けて5台生産という作業を1日4回繰り返していた……ということになります。これを1日6回繰り返せば,426分間で30台生産という理屈になります。
一方,今回の1個流し改善では,11-2図の下部にあるように,着工したら1個47分後に完成し,連続して生産すれば,3分間隔で完成していくことになります。1日を450分とすれば130個以上生産出来る計算になります。(A),(B),(C)全てこのラインで余裕を持って生産出来る計算になりますので,次回の改善テーマになります。
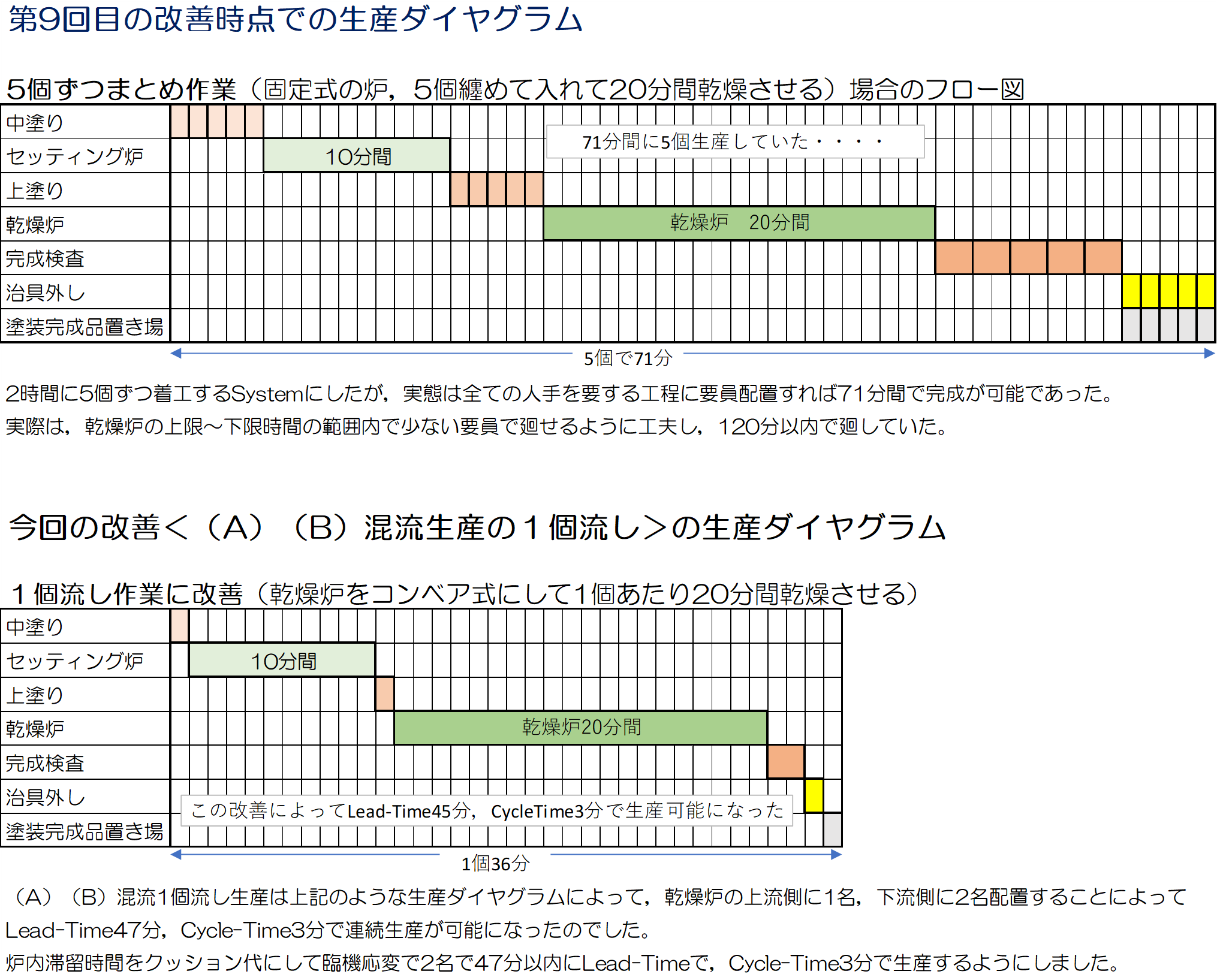
第9回目で説明した生産方法は生産ダイヤグラムで表しているように,5個ずつまとめて塗装していくので71分毎に5個生産されていくものでした。これは第1工程と同じで,通常は1日4回繰り返して20個生産するものでした。フルに6回繰り返すと1日30個生産出来る経産になります。
今回の1個流しの改革は,下部に描いた生産ダイヤグラムのようになりました。最短の生産Lead-Timeは36分で生産は出来ますが,第1工程とCycle-Timeを合わせて3分に設定すると,中塗りと上塗りに1人,塗装完成検査1人,治具外しと完成品収容で1人の3人掛かりにすれば,1日130個にベースで生産出来ることになります。
[W]組立・検査・個装工程
ここでは,全ての作業が組付け治具の上で手作業で行われています。先回の改善では,(B)だけを2時間単位で5台ずつ完成させるというものでした。しかも塗装済みの天板と脚も5台分ずつ2時間間隔で届けられるという中での取り組みでしたので,5台分一度に生産に取り組むという発想が生まれ,(B)用の組付け治具5台揃え,1人で同時に生産していく方式が採られていました。この時の生産ダイヤグラムを図示すると第11-4図になります。ここでは,110分掛けて5台作っております。
作業が遅れそうな場合は,5台の治具のうちの2台に応援者を入れて挽回を図ります。机3台が65分で出来,2台が44分で出来る計算になります。
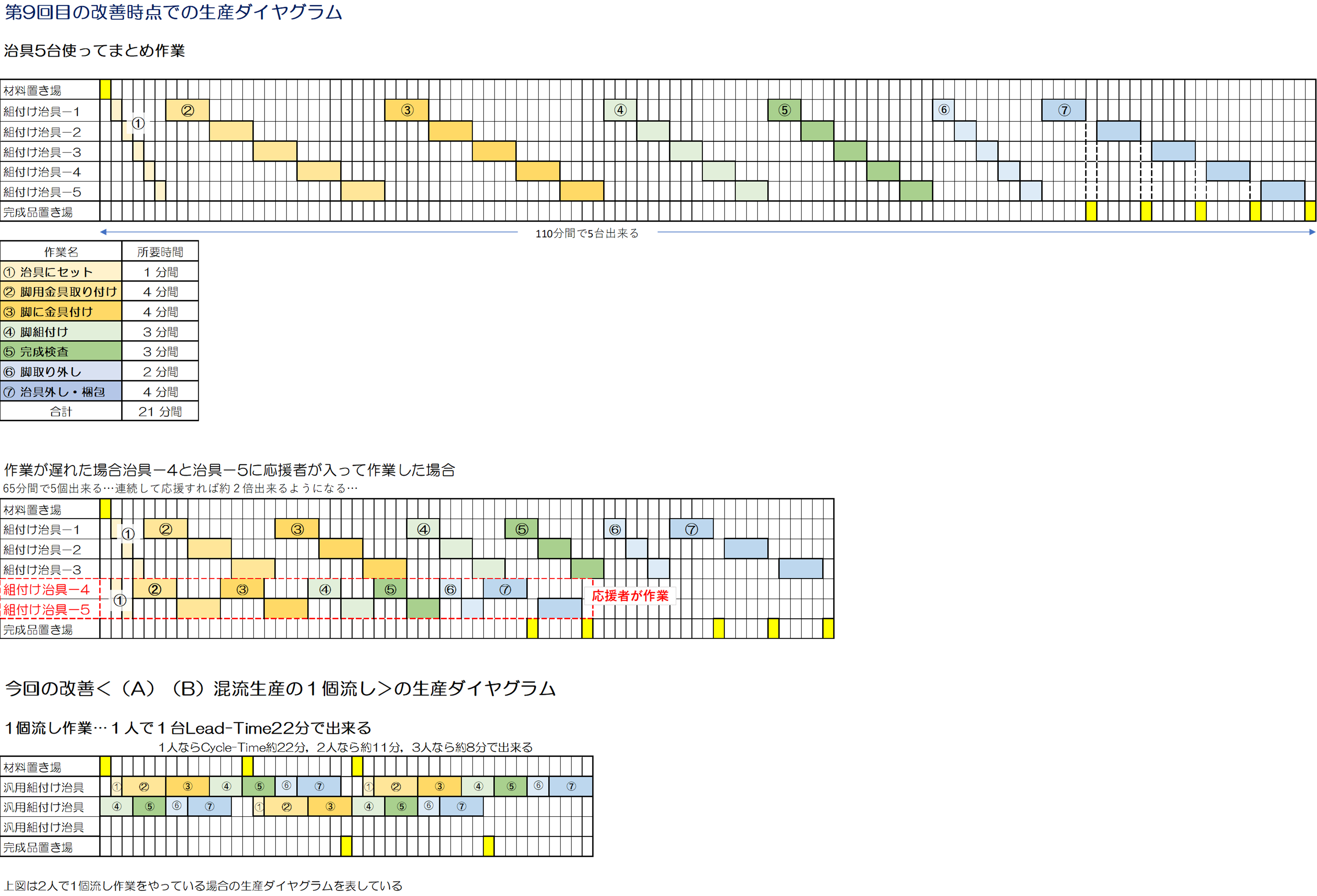
さて,今回の1個流しの改善は,(A)と(B)合計平均30個を,定時内に生産することですが,市場の変化に対応するために,急ぐときは出来るだけ多くの生産が出来る方策を準備することにありました。
そこで(A)(B)どちらも生産出来るように改良した汎用組付け治具を3台準備して置き,定常時には要員2名で作業する体制にしました。(第11-4図下部)
専用治具があると,それが原因になって順序が狂います。汎用機にしておき,計画した順番,又はその工程に到着した順番に着工し,完成させていくことがLead-Time短縮のためには必要になるのです。その結果この工程のLead-Timeは22分で,Cycle-Timeは11分で生産出来るようになりました。
工数的に見れば,(A)専用工程で1人,(B)専用工程で1人+αでやってきたモノが,(A)(B)混流生産の1個流し化にすることで2人で余力を持って廻せるようになったのでした。
[X]出荷梱包・倉庫入れ工程
この工程は全種類の共通の工程になっていましたが,以前は毎日の完成品を4個ずつ出荷梱包した上で倉庫に入れ保管し,週1回の出荷日には各得意様に向けて合計で600個(平均)の出荷荷揃えをしていました。
今回の改革によって,完成品出口は,従来の3カ所から(A)(B)生産工場と,(C)生産工場の2カ所に統合され,更に出荷梱包は無くなり,個装のままで倉庫内は扱います。後工程の商社から納入先と納期が届きますから,それに合わせて配送先宛名ラベルと貼り付け,宅配業者別の出荷場に並べていく作業に変わりました。注文は日々変わりますし,販売店は(土)(日)がよく売れ,工場平日ほぼ平準化生産しますから,此処の作業は殆どが,完成と同時に出荷荷揃え場に直行というようになり,一部分だけが棚に入れるようになり,工数は激減しました。
11.4. 改善成果のまとめ
ここまで個々の工程の改善内容を一覧表にまとめると下表のようになります。
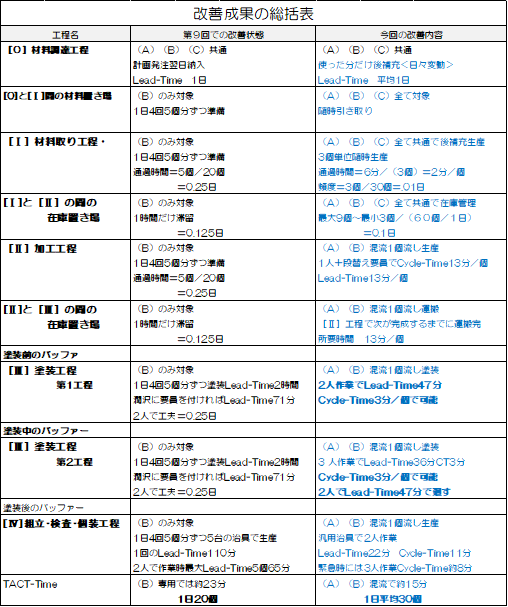
更にこれを社内の生産全体を表すダイヤグラムで表現すると第11-6図のようになります。分かり易いように,朝一番から加工工程で着工した机が,工程間をどのような時間経過で最終工程まで辿り着くかを表したもので,列車のダイヤ表に似ていることから『生産ダイヤグラム(線図式)』と呼んでいます。1個1個の製品が流れていく様がよく分かります。因みにロット生産をするものはある工程での滞在時間が長く,線図では表しにくいので,着工から完成までを長方形で表します。これを,『生産ダイヤグラム(ブロック式)』と呼びます。第11-1図から第11-4図まではブロック式で描いたダイヤクラムに当たります。
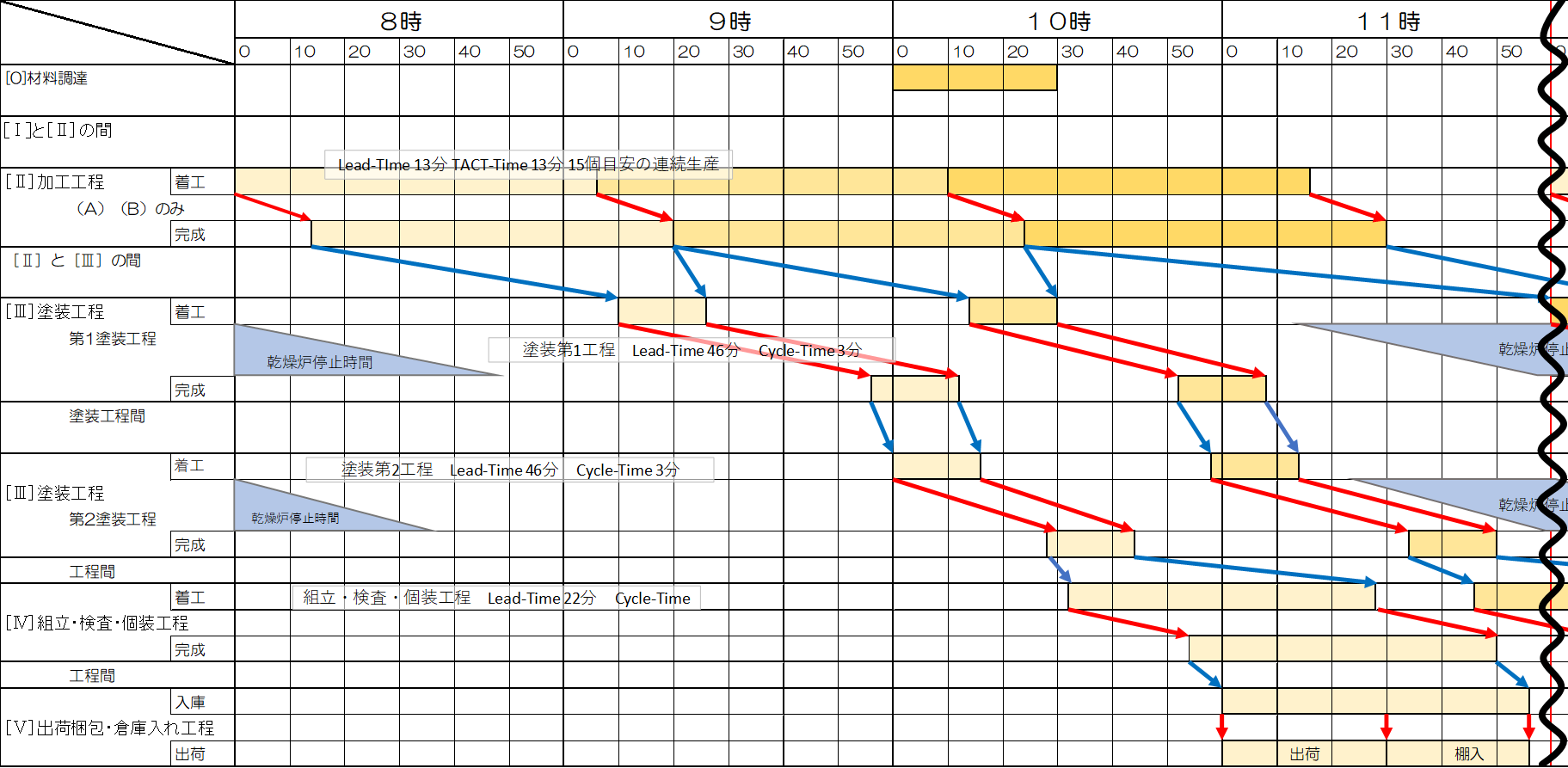
この図で注意しなければいけないところは,乾燥炉の停止時間です。ダイヤグラムの中で灰色の三角形,平行四辺形で表現してあるのは,乾燥炉の停止時間です。文中で乾燥時間には最小時間と最大時間があり,その範囲内ではクッション代として使えるといいましたが,それは数十分の範囲内のことで,昼休みや直間乾燥炉の中に入れっぱなしではOver-Bake(乾燥しすぎの不良)が起きますし,エネルギー費のむだになります。昼休み等は乾燥炉を空にして火を落とすのが定石です。その時間帯を表現したものです。
さて,図を観察しましょう。朝の掛かりに加工工程で着工した5個の机は1個ずつ塗装工程に運ばれ,TACT-Timeの違いがあるため5個ずつロット形成され塗装工程に入ります。第1塗装工程,第2塗装工程を経て,先頭は10時半には組立工程まで到着します。その後一つずつじっくりと組み立てられ,最初に着工した5個全部が午前中に完成して倉庫に届きます。
と言うことは午後一番に着工したものがその日の夕方に完成し,午後着工したものは翌日の午前には完成することを意味しています。[T]の材料取りは平均在庫6個分(0.1日分)ですので,材料取りから完成までのLead-Timeは0.6日分と査定出来ます。
第9回目改善では,従来の仕掛かり在庫5日分を,2時間に5個ずつ流すようにして,各工程を整流化させて繋いだことによって3日間に短縮したのでしたが,今回は(A)(B)二種類の机を混流生産にした上で1個流し・1個運びに変えることで,何と3日間から0.6日分なで短縮出来たのでした。
次回はこの改善によって,安全在庫,完成品在庫がどのように変わっていき,全体としてどんな効果が得られたのかについて御説明します。ご期待ください。
2018年7月
(株)Jコスト研究所 代表 田中正知