連載コラム『Jコスト改革の考え方』 第 4回目
自社の現状を時間尺度で把握する(その2)
先回は,一番簡単な一つの粗型材が加工されていき完成品になる一本道型生産をモデルにして調査方法の要点を説明しましたが,今回は,引き続き集約型(合流工程がある)と,展開型(分岐工程がある)についてお話しします。
【2】集約型生産
(多くの種類の部品が組み立てられて完成品になる)
集約型の代表的な例は自動車生産でしょう。最終組立ラインではエンジンやシート,タイヤなどおおよそ2千個の部品を組み付けて完成させます。そのエンジンは又数百点の部品から構成されています。全部を分解すると1台の車両は約10万点にも達すると言われています。更に航空機は数百万点にも達すると言われています。
部品の多さに惑わされてはいけません。小川が集まって大河になって行くのと同じで,細部を見れば,ひとつ一つの小川が合流していくのに過ぎません。
川の流れを見るには「浮き」を投げ込みその流れを見るように,工程の流れを見るために,製品1単位に印を付けて流して測定する事を先回一本道型生産の説明で述べましたが,今回の合流の部分をどう工夫したら良いのか・・・を理解すれば解析は容易です。
以下合流のある場合のLead-Time測定法と,Lead-Timeを長くしている要因のチェック方法を説明します。
今流行のPPAPの工程図(下図)を例に取り上げて説明します。
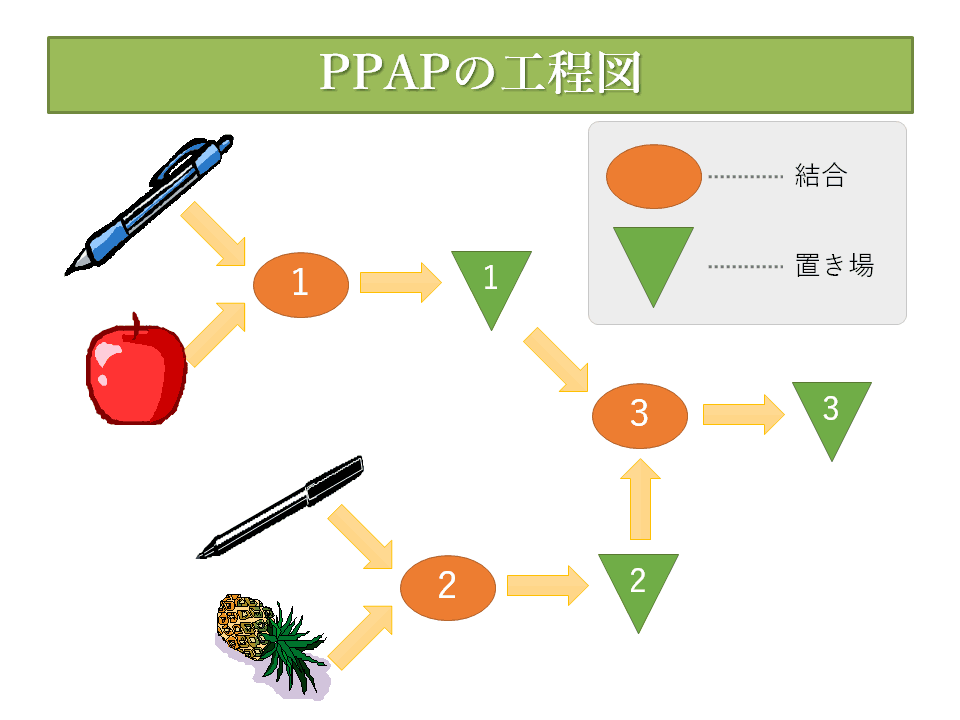
- 第1工程
- Pen-1を取りだし,Appleを取りだし,結合させ置き場-1に置く。
- 第2工程
- Pen-2を取りだし,Pineappleを取りだし,結合させ置き場-2に置く。
- 第3工程
- 置き場-1,2からApple-PenとPen-Pineappleを取り出し結合させ,置き場-3に置きます。
具体的調査法
- 流れの整理をし,本流と支流に区分けして考える。それはある地域に降った雨が小川に流れそれが合流して大河になって海に繋がるが,どの大河も本流と支流に分けて管理しているのと同じです。
- 量に制約があるとか,コストが高いとか,構成部品の中で
最も重点を置いて管理すべき部品を指定して,その流れを本流に据えて全体象を描きます。PPAPの事例では沖縄から週1便で入荷するパイナップルから始まる流れが即ち,下図が本流となります。
PPAP工程の本流 - コンベアライン同志で合流させるときには,同じTACT Time(流れの速さ)に設定してあっても,実際に工程を稼働させるといわゆるチョコ停などが頻繁に起きていて,相対的にとちらかが遅れる場合が頻発し,全体の進捗が遅れていくという現象が起きます。それを防ぐために,合流点の支流側にクッション代としての在庫を持たせ,本流を停めないようにする工夫が必要になります。これが重要なチェックポイントになります。
- ここに挙げたPPAPの例では置き場(在庫)から手に取って組み付けるので,この合流点から遡って前回の一本道の解析のやり方で個別に解析していき,最後に時間軸を頼りに合成すれば下図のようになります。
PPAP工程のLead-Time図 この図は出来上がった姿を概念図として表現していますが,実際には個々のリードタイムは現状をつぶさに調査して結果を基に 理論値として『査定』しなければなりません。
-
仕入れ品の受入倉庫の在庫量は・・・・
【A】後補充ならば, A-1定量不定時補充か? A-2定時不定量補充か?
【B】計画発注方式ならば,着工何日前に納入日を設定してあるのか?
更に最小発注単位(=収容数×箱数)等々をもとにして使う速さ(タクトタイム)を求めて,在庫量を金額でも重さでもなく使い切るのに要する時間(Lead-Time)を求めて図示したモノです。 信じられないほど多いことがあります。 -
運搬工程は・・・・
受け入れ倉庫から工場内の組付け場へ・・・・等々各工程間を材料や完成品を運びますが,どのTimingで何個運ぶか,各部署の在庫量の管理は誰がどうやっているのか,在庫の動きは『現場管理の結果』である事を認識して調べ, 運搬所要時間はLead-Timeとして図示し,1回に運ぶ量(時間単位)を書き添えます。 -
組付け工程は・・・・
何処が作業管理をしており,Cycle Timeはどれ位で,1バッチ何個単位で日当たり何回生産しているのか? - 上記(5)(6)(7)で調べ上げたことを 『モノと情報の流れ図Value Stream Map』を作成し,現状の生産管理の全体像を把握した上で,各Lead-Timeを査定します。その結果を図示したモノの例が 『PPAP工程のLead-Time図』なのです。
- Lead-Time短縮改善とは,在庫時間を可能な限り短くすることにありますが,同じ待ち時間でも,原価の高いモノの在庫時間を短くする方が効果的です。
そのことを顕在化させるために,PPAP工程図の帯グラフの幅を金額比例で表現すると次のようになり,これを一般には 『Jコスト図』といいます。『PPAP工程のJコスト図』
利回り=利息/(預金金額×期間)に対応させた
収益力=粗利益/{(平均原価)×(仕入れから売るまでのLead-Time)}・・・・(8)
上式の分母が表現している面積に当たるのです。 - 冒頭の
『自社の現状を時間軸で把握する』というテーマに対しては先の
『PPAP工程のLead-Time図』がその答にはなって居ます。この図に従ってLead-Time短縮改善をするのは一つの解決法ですが,
『PPAP工程のJコスト図』は更に先を行く改善です。
会計学的には,このJコスト図ではPPAP1単位を生産するのに要した棚卸資産を表しています。この面積を減らした分だけ分母が減り,収益力が上がるのです。
【3】集約型生産の『モノと情報の流れ図』作成の苦労話
今回ここまで御説明してきた改善手法は,約6年前にナブテスコ社鉄道カンパニーでの 『Jコスト改革』で展開してきた改善手法のあらましです。
しかし具体的に自社で展開するに当たっては複雑な自社工場内の製品の流れを再点検し,部下に改善趣旨を徹底し 『Jコスト論』に沿った現状調査し, 『モノと情報の流れ図』を描き上げ,それによって明らかになった課題を解決して,最終的には 棚卸資産を半減させました。
その時,その改善を中心になって進められたナブテスコ社改善Teamの田中宏樹様が,これから改善を進めようとする皆様の参考になるようにと弊社HP用に書いて頂いた 『苦労話』を紹介いたします。
モノと情報の流れ図 苦労話
ナブテスコ鉄道カンパニー
部品納入から出荷までの工程を把握して問題点を抽出する為,“モノと情報の流れ図”を作成するよう田中先生から指示を受けたので,当時の主力製品であったブレーキ制御装置について作成することにした。
正直,“モノと情報の流れ図”を少しでも楽に作成できないか?と考え,管理工程図の活用を検討して実行しようとしたがこれが甘かった。
モノの運搬や停滞を表現するには詳細の工程が分からず, 管理工程図はほとんど参考にならなかった。現場に張り付いて現状確認をしないと”モノと情報の流れ図“を完成できないと考え方を変え,現場へ出向いて工程把握を行い,現場管理者へのヒアリングによりモノの流れ(工程),作業の5W1H,指示系統(指示書,帳票)を 約1ヶ月かけて調査をした。
初めての取組だったので調査方法が手探りであったことや,調査者の製品,工程知識不足もあり, ヒアリングに非常に時間が掛かり,根気も必要でしたが, 現場に協力してもらいながら作成を進めました。
完成させたつもりの“モノと情報の流れ図”も,次工程への引渡“押込み”や“引張り”が表現出来ていなかったり,作業場や停滞場所が不明確であったりと, 分かり難い点が多数指摘された為,第三者が見ても分かるような形に様々な修正を加えながら現在の“モノと情報の流れ図”を完成させていきました
完成した“モノと情報の流れ図”(模造紙サイズ 6m X 1.2m)をプロジェクトメンバで確認すると
- 停滞回数の多さ(部品早期納入,早期作業着手,部品納入遅れ,載せ替え)
- ルールの無い運用,指示,作業順序
- 次工程への引き渡し情報伝達不足
- 基準情報不備
- 目的がはっきりしない作業(慣例作業)
など,多数の問題が挙がりひとつひとつ改善していきました。
最後に, “モノと情報の流れ図”の作成には現場の協力や時間と根気が必要です。
しかし,なぜ停滞が発生しているのか?何に基づいて作業しているのか?なぜその作業が必要なのか?など疑問や問題点が把握できるので工程の現状把握や問題点抽出には有効なツールです。
以上
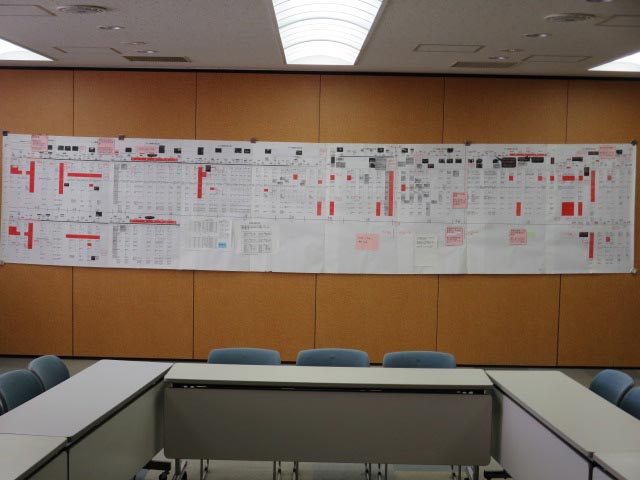

皆様に参考として頂きたいのは,丁寧に調べ上げて表示すると写真にあるように会議室に壁一杯になるほどの大きさになる事です。当該部品はナブテスコ様がSupplierとして納めている『ブレーキ制御ユニット』という車両の主要構成部品です。更に複雑な製品になると壁を3面余使うほどになります。
更に,コンピューター化されたために,現場の全体像を把握している人が居ず,現場作業の支点,終点で何をどうするかの指示が,何処からどのTimingで出ているのか抜けなくチェックしなければなりません。そのためにナブテスコ様は,上図の"モノと情報の流れ図(横スクロール)"の左側にある 赤枠に囲んだようなチェック表を作りました。これも是非御参考にして下さい。
次回は【4】展開型生産の説明を致します。
2017年4月
(株)Jコスト研究所 代表 田中正知