連載コラム『Jコスト改革の考え方』 第 9回目
工場の仕掛かり在庫(製造Lead-Time)短縮に挑戦する
第7回で 『速く作る』と『早く作る』の違いを考える
第8回で 『早く』から『速く』に変えた効果を『Jコスト論』で測定する
のお話しをしてきました。その改善内容は,作業工程を対象にした工数低減活動ではなく,サプライチェーン全体を見ての在庫低減,短縮に着眼した改革で,毎月1回の材料仕入れを毎日にし,毎月1回の得意先への納品を毎週1回にすると言うものでした。
その結果の在庫日数の低減は,第1図のようになりました。
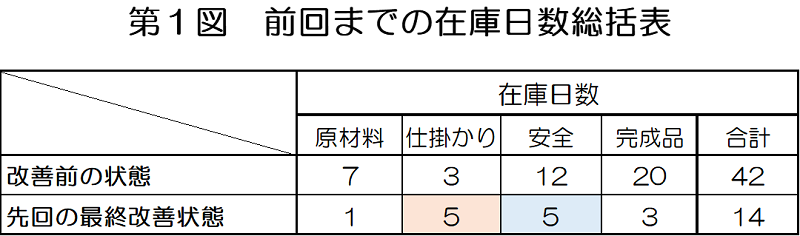
表から分かるように,原材料と完成品在庫に比べ,仕掛かり在庫と安全在庫が多すぎると気がつきます。そこで先回お約束したように,今回は仕掛かり在庫の現状解析と改善を行っていきます。安全在庫については,仕掛かり在庫量から決める場合が多いので,後から考えることにします。
【1】仕掛かりの現状の把握
製品は,木製の洒落たテーブルをイメージして以下のお話を展開し行きます。この説明を通じて,『現場の見方』,『改善の仕方』をご理解ください。
先ず,生産現場はどんな指示で動いているのでしょうか,現地現物を確認することから始まります。確認すると第2図のような『日程表』で現場指示が成されていました。
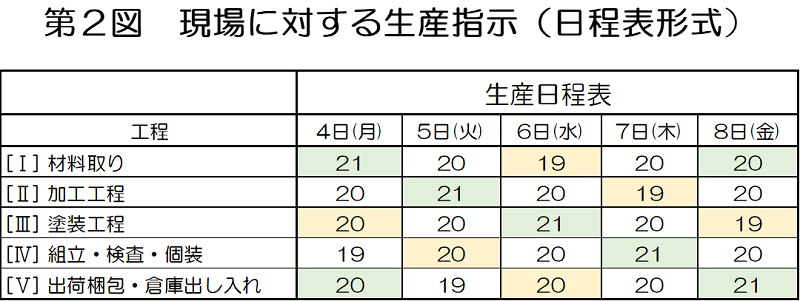
分かり易いように第2図では,日当たり20個だったり19個だったり日々の変動を入れ,薄く色づけてありますが,この表で指示していることは,各工程で1日当たり平均で20個ずつ加工して翌日に次の工程に移しなさい,と指示していると言うことです。言い換えれば,完成品があってもその日の内には移動させず翌日に移動させる事を指示しているのでした。
次に各工程の作り方を観察しまました。
第3図は,今までの材料取りのやり方を縦軸に数量,横軸に時間を取って図示したものです。此処は工場全部の部署で使う部材を切り出しているので,午前中に棒材の切り出しを行い,午後には時間の掛かる板材の切り出しをしていました。対象としているテーブルについて言えば,午前中に脚部の材料を1日分切り出し,午後は天板になる板材を1日分切り出していたのです。
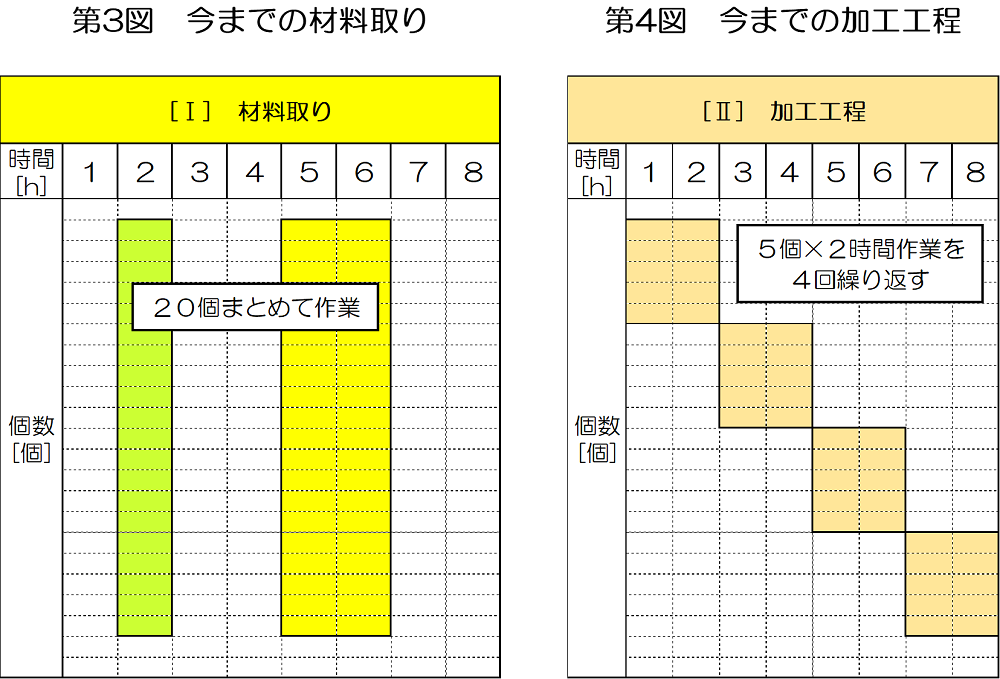
第4図は部材の加工工程で,天板と脚部とを5個ロットで手分けして2時間で加工し,それを4回繰り返して20個生産し1日分まとめて次工程である塗装工程に送っていました。
次の塗装工程では,下地塗装・中塗り塗装・上塗り塗装・検査とタッチアップの4工程に分かれて作業が行われて居ました。塗料の乾燥炉で時間が取られ,完成まで4時間かかるので,10個ずつ午前1回,午後1回の2回に分けてロット生産していました。
それを図にしたのが,下の第5図です。この図で色を変えているのは,下地・中塗り用の乾燥炉と上塗り用乾燥炉は,使用条件が違ってるので,別の炉で乾燥させていることを表現しているのです。
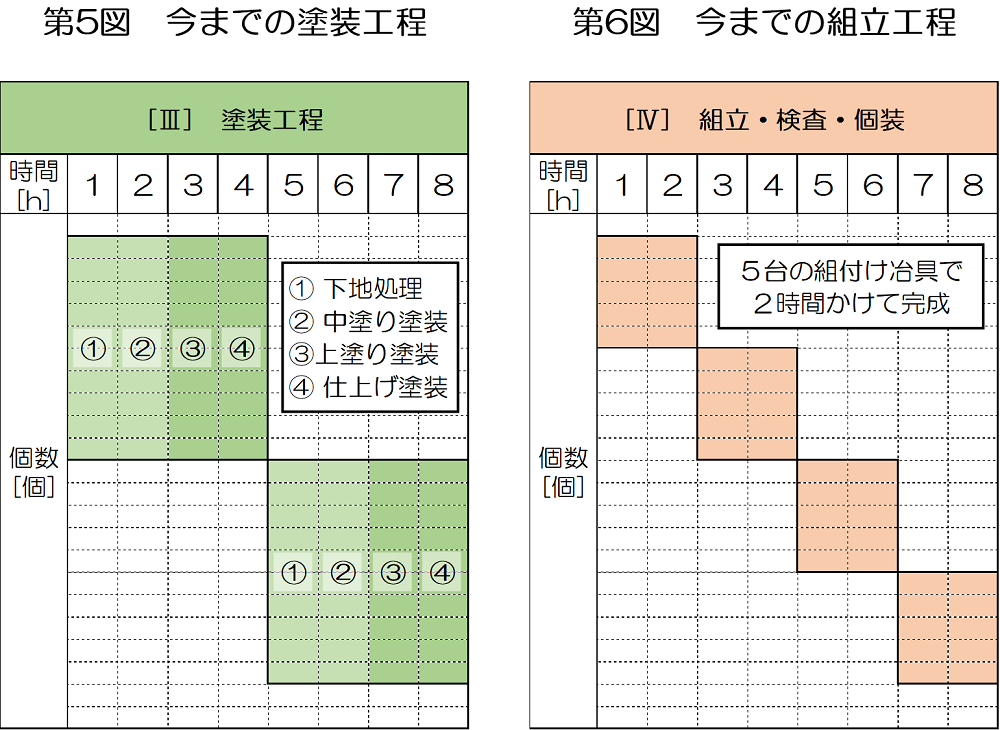
第6図は組立工程の作業状況を表しています。此処では5台の組付け治具を使って,部品接着,取付穴加工,金具取り付けをやっています。位置決めや,接着剤が硬化するまでの養生のために1時間余固定する必要があるために治具を使っていて,その後外観と剛性を確認検査してから梱包しやすい大きさに分解し,1個ずつ段ボール箱に詰め(個装)て置き,1日の終わりに次の工程に送っていました。かなり仕事量も多いので5個作るTACT-Time2時間を更に短縮するのは容易でないことが分かりました。
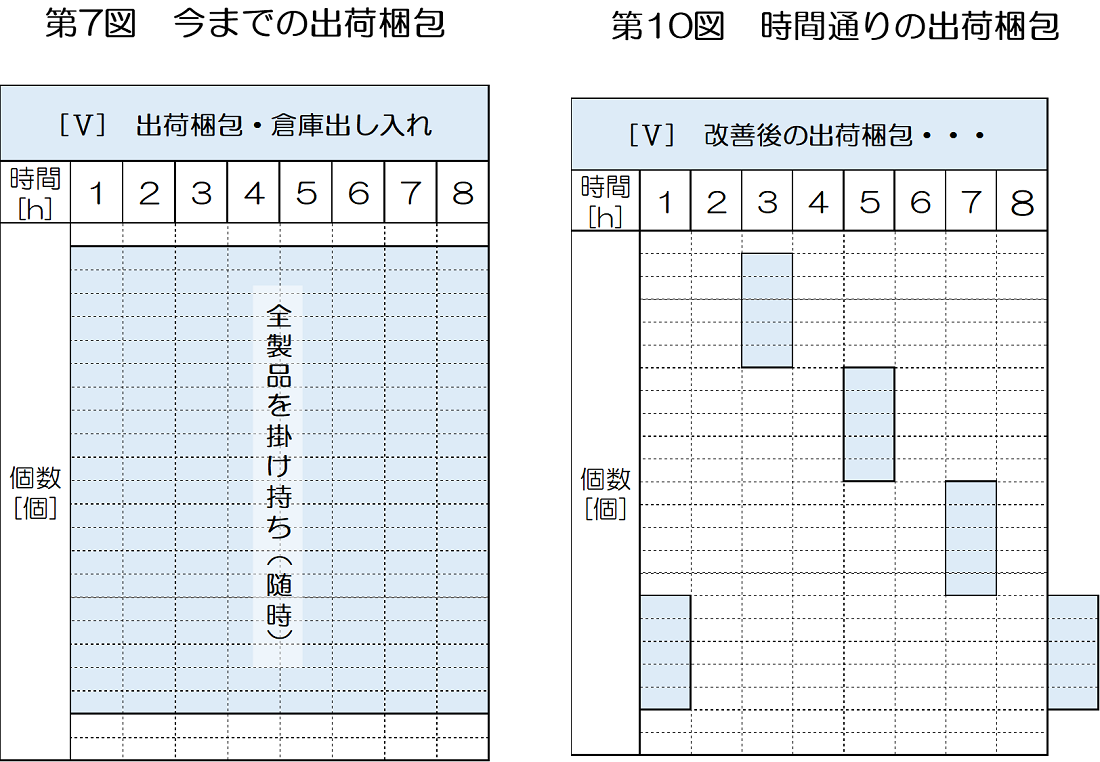
第7図は組立・検査工程で段ボールに個装された製品を受け取り,5個ずつ出荷用の大きな段ボール箱に詰め,それをフォークリフトで倉庫に運び,所定の場所に置いてくることと,週1回の出荷日には,出荷場に荷揃えすることですが,工場全体の同様の作業を掛け持ちでやっていて,あちこち動き回りながら,出くわした作業をやっていく・・・・というものでした。このやり方をトヨタ生産方式では,仕事を求めて街中を走り回るタクシーになぞらえて「流し方式」と呼びます。工場の運搬方式としてはいちばん手っ取り早いのですが,一番ロスが多いやり方です。工程が安定して来て,運搬が必要とされる時間が決まっていますから,定期巡回バス方式にすることが可能と分かりました。
【2】先ず各工程のTACT-Timeを揃える
現状を把握した結果,第4図の加工工程と第6図の組立工程は,5個ロットで2時間のTACT-Timeで生産していました。第7図に示した出荷梱包を,前工程である第6図の組立工程に同期させてやれば,第10図のようになり,充分余裕を持って定時巡回バス方式が出来る事が分かりました。
又,第5図の塗装工程も,下地・中塗りと上塗り・仕上げを分けて考えて,更に今の10台ロットを5台ロットにすれば,組立てと同じように2時間のTACT-Timeで廻すことが出来る事が分かりました。そうすると下の第9図のようになります。図ではみ出して描いてあるのは,この仕事は当日の内には終わらず,翌日の最初の仕事になるという意味です。このようにサイクリックに繰り返されて行くのです。
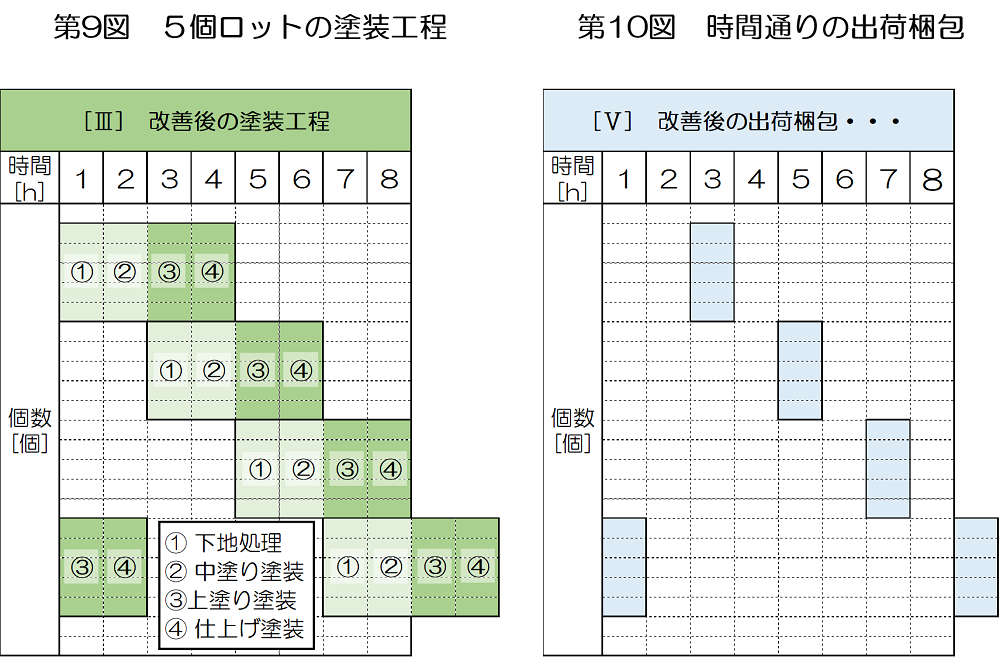
ここまで解決して来ると,残るのは最初の木取り工程(第3図)です。此処では工場全体で使う材料を1日分ずつ準備(木取り)していますが,最後に準備する順番に当たった部署はその日に生産出来ないわけで,今のままでは次の加工工程との間にほぼ1日分の在庫がある運用になってしまいます。工場全体の部署に2時間分ずつ小分けして材料の準備が出来れば,後工程との間の在庫は2時間以内で押さえることが出来ます。トライしたところ,平板もの(天板)と角材もの(脚部)とは同時ではありませんが,両方を2時間サイクルで準備できる事が分かりました。その状況は第8図に示すとおりです。
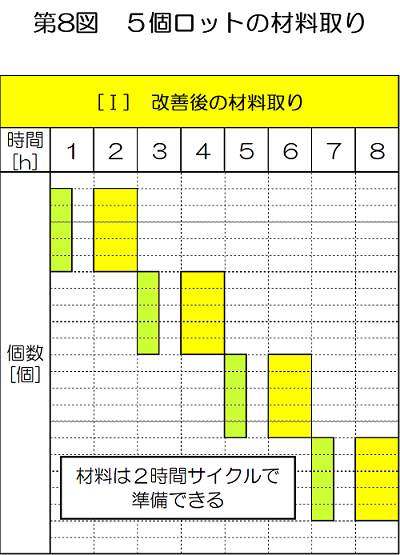
【3】TACT-Timeが揃ったので工程を連結できる
ここまでの改善を実施すると,最初の材料取りから最後の出荷梱包までの全工程に亘って,5個をTACT-Time 2時間で作ることが出来るようになります。そうすると1本の生産ラインとして連結できます。その結果,第2図にあるような日程表形式の生産計画表から卒業して,第11図にあるような,1本の生産ラインとしての生産指示表になります。工程を途中の停車駅と見立てれば,1本の線路の上で次々と運行されていく列車のダイヤに似ています。それで,この表を 『生産ダイヤグラム』又は 『ダイヤグラムタイプの生産計画表』と呼んでいます。
分岐・合流がなく流れていく生産ラインを『整流工程』と呼んで『トヨタ生産方式』では望ましいという形としていますが,ここでは同じTACT-Timeで連結された淀みのない 『ライン化』と言う更に上位の理想の姿にすることができたのです。
【4】生産計画表から,仕掛かり在庫を測定する
第11図の生産ダイヤグラムから,時々刻々の仕掛品の動きが掴めます。これを基にして仕掛かり在庫が時々刻々どのように変化するのかを追っ掛けてみましょう。
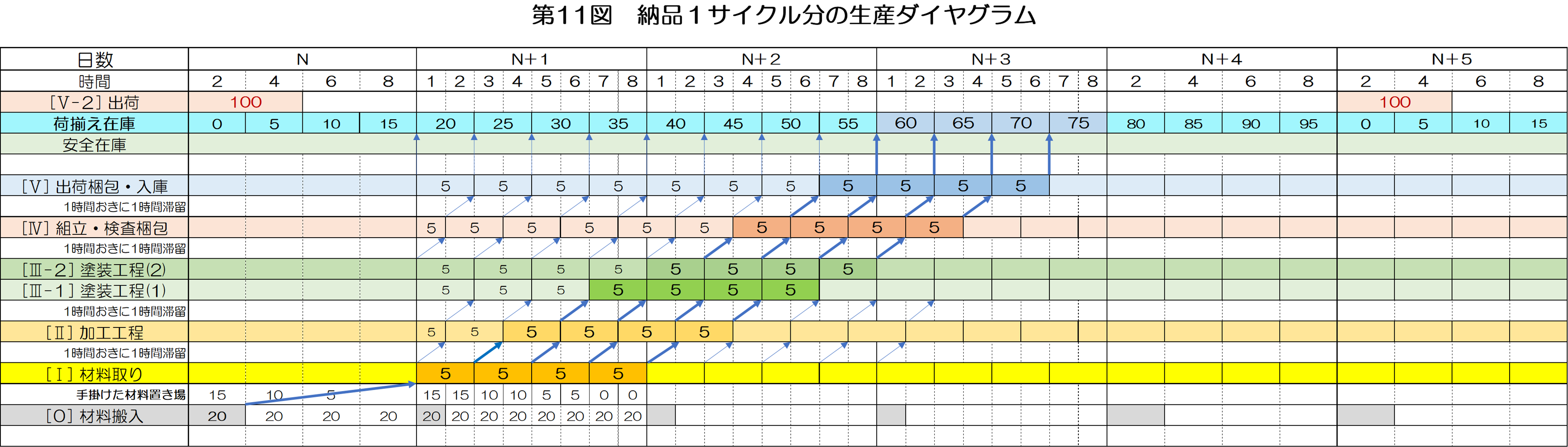
- [O]材料搬入工程
- 毎日一定時刻にサプライヤーから材料が搬入されます。交通渋滞等の恐れがあるので,今回はここに安全在庫もかねて搬入時には手掛けず,翌日の一番から使用することにしてあります。それ故ここには常に20個(1日分)の材料在庫がある設定にしてあります。
- 手掛けた材料置き場
- 材料搬入から材料取り工程の間には,2時間に5個ずつ材料取りするので,15⇒10⇒5⇒0と言った具合に,残ったものを置く場所があります。ここの平均値は10個(0.5日分)と査定できます。
- [T]材料取り工程
- 2時間毎に5個分の材料取りするので,例え数十分で作業が終えても,他の工程と同じで常に工程内に5個分の仕掛かり在庫があると見なします。
- [T]と[U]との間の仕掛かり在庫
- 工程間に多少の遅れ進みがあっても,円滑な運営が出来るように,2時間に1回1時間のクッション代を設定してあります。平均すれば2,5個(1時間分)の仕掛かり在庫があると見なせます。これは,[U]〜[V],[V]〜[W],[W]〜[X]の間でもまったく同じに計算できます。全部で4カ所ありますから,全部で4時間分(10個)あると見なせるのです。
第11図から分かることは,N日に納入された材料は,材料置き場にその日置かれます。翌日(N+1日)朝イチから2時間分ずつ材料取りがされ,その後,次々と加工され,N+3日中に全て完成させて出荷場まで行くという事が分かります。と言うことは,材料置き場に1日,工程内仕掛かり在庫3日間と言うことが出来ます。現場の実力が上がるにつれて更に少ない在庫量で生産出来るようになりますが,この段階では改善に向けて動き出すのが一番大事なことですから,充分な在庫を持って立ち上げる計画にしてあります。
【5】安全在庫を考える
最後に世に言う『安全在庫』を幾つにするか決めなければなりません。因みにトヨタ生方式ではこれを『安心賃』と言って多くすることを戒めていました。その理由は,なんとなく欠品が不安であるからと言って心配すれば,在庫は幾つ有っても不安です。その一方で,在庫は上司の許可なく増やせるのが普通であり,その工程の責任者にしてみれば,万一設備故障が起きて後工程に迷惑を掛けると上司から叱られるのが目に見えていますから,多くの現場では,心配の余り置ききれないほど各工程の出口にその工程の完成品在庫を持ってしまうのが常です。そう言う会社は多くの場合,資金繰りに困って居たりするのです。幾ら欠品の心配が無くなったとしても,会社の運転資金がショートすれば不渡りを出し,会社は潰れてしまいます。
このようなことを踏まえて『トヨタ生産方式』では, 『様々なムダがあるが,1番のムダは作りすぎのムダである』と戒めています。
因みに良く『七つのムダ』と言われますが,『無くて七癖』という言葉から沢山あるという意味で『七つ』と言っているまでで,場面場面で『必須』であったり『ムダ』であったりしますが,それは 当事者である皆さまご自身がお決めになる事です。
さて,具体的に第11図にある『安全在庫』を考えるには,其処にどんなリスクがあるか,それにどう対処するか・・・具体的に考えていく必要があります。
(1)『材料の納入』が遅れたら?
材料は,朝一番に納入される約束になって居ますが,その日は手掛けず,翌日の朝イチに材料取り工程に運ばれることになって居て,現状で充分すぎる在庫を持っていますから これ以上の在庫は不要です。(今後の改善テーマとすべきです)
(2)『材料取り』『加工』『塗装』『組立』等の作業が遅れたら?
各工程は2時間サイクルで作業をしており,工程間は1時間分のクッション代を持っていますから,たまたま2時間で終わる作業が3時間かかったとしても,そのクッション代で吸収され, ラインを停める心配はありません。むしろクッション代は半分の30分で可能になるように工程の安定化を図るのが次の改善テーマでもあります。
(3)納品先の売れが増加した場合
第11図にあるように,現状は2時間サイクルで5個ずつ生産していて,1日20個,1週間(5稼働日)で100個生産しこれを毎日繰り返して生産して行く体制を示しています。『ものづくり』と言うのはこのように体制を固めて常に一定量生産していくことを得意としているのです。
さて納品は100個/週という約束になって居ますから,第11図のやり方では納品の瞬間は,出荷倉庫は在庫ゼロになります。100個/週というのはあくまでも需要予測に基づくもので,納入先(得意先)と合意の上で決めたものに過ぎません。実際の毎週の売れ具合は,御客様の動向で如何様にも変化します。そしてそれは,週単位での変動に加え,長期的に見ればどんな商品も市場においては寿命があり,発売当初は沢山売れても,時間とともに徐々に売れなくなって行くのが常です。それ故,売れが増加した場合には 完成品在庫に欠品が生じ,売れが鈍化すれば 完成品在庫が増えてしまいます。
つまり,常に一定量を生産して行きたい工場と,常に変動している市場を繋ぐためには,クッション代としての在庫が必要になってきます。それが 『安全在庫』であり,その必要量は,生産のやり方によって大きく変わってくるのです。
ここで,『安全在庫』が,生産方式によってどのように違ってくるのか,考えてみましょう。
【6】完成品の安全在庫量と生産方式
今回取り上げている製品のでは具体的にどうなるのか詳細の説明は次回に譲るとして,今回ここでは,生産方式によって安全在庫はどのようになるのか,定性的に御説明します。
[6-1]完全受注生産方式
オリジナル設計の戸建て住宅がその典型です。建設業者の立場で言えば
- 基本Concept,細部仕様を伝えて設計開始
- 出来上がった設計図を承認を得る
- 納期・価格・引き渡し条件・支払い条件を明確にして受注
- 部品買い付け,業者手配,施工・・・
- 完成検査・諸手続・引き渡し・・・
と言ったプロセスを踏んでいきます。住宅だけでなく,他社名の付いた芝刈り機等を受注して自社で生産する時も(OEM生産),設計から自社でやる場合や,生産のみを受注する場合等,様々な形態はありますが,受注数量が例えば2,018個であればその個数分の部品を発注し,生産し,納品しましから『安全在庫』を考える必要はありません。それが毎月繰り返されても,その都度注文された数量を納める契約であれば,『安全在庫』は必要ない事になるのです。
[6-2]予測生産方式(計画生産方式)
自社製品の市場での月々の需要を予測して生産計画を立て,その計画に基づいて生産する方式を言います。丁度100年前全盛を誇っていた自動車,T型FORDが有名ですが,運転しやすく高性能なこの車は黒1色しかなく,需要予測がし易かったと言います。強気の需要予測を立て,その台数を如何に効率的に生産するかに腐心し,有名なベルトコンベア方式を発明して生産性を画期的に向上させますが,その成果を低価格化に向け,更に需要を喚起して行きます。この好循環で大成功を収めたことは有名です。ここから大量生産方式が生まれたと言って良いでしょう。
米国の自動車業界では強気の需要予測をし,その台数で最も生産性の高い生産設備を整え,フル生産します。やがて生産量と市場での販売量との間で乖離が生まれ,完成品在庫(今まで論じてきた『安全在庫』)が積み上げって行きます。
ある限度を超えると,従業員に最低賃金を保証した上で一定期間工場の操業停止をします(レイオフ)。在庫が減ってくると再稼働すると言う生産形態を取ってきました。
因みに1970年代,モータリゼーションの波に乗って日本の自動車の販売台数は急増していましたが,当時のトヨタは販売を担う『トヨタ自販』と生産を担う『トヨタ自工』とに分かれていました。需要予測は年間台数,向こう三ヶ月の予測があり,それに基づいて翌月の確定生産台数を工販合意の上で決める会議が毎月20日頃行われていました。
この会議には工販の副社長以下が出席し,まる半日掛けて,机を叩いての大激論をしたと言います。この場で決まった車名別生産台数を,生産管理部がそれぞれの組立工場及び生産ライン別に割り当てます。各組立課長は,そのラインの持つ生産性のBestレコードでやっと定時に生産出来るような人員計画案を作り,人事部に増員又は減員の要員計画を立て,台数に似合った工程数にします。従って,毎日20分程度の残業をしないと生産出来ない状態に自らを追い込んでいました。
更に各車両の細部の仕様は,販売店が御客様の注文をもとにして『トヨタ自販』経由で『トヨタ自工』生産管理部に伝えられ,それをもとにして翌日の各工場の生産ラインの日々の実行計画が作られていました。従って当時の『トヨタ自工』は月産20万台余生産するTop-Makerでしたが,その実態は1台1台が日本国中の系列販売店の紐付きの『受注生産』だったのでした。
[6-3]限量生産方式
商品の需要予測をした上で,市場への供給量を需要より低い水準で維持し,ブランド価値を維持する市場戦略を指します。大は,いわゆるBrand品で,高品質だけでなく,希少価値を含めて高価格を維持することで,所有者に対してプライドと満足感を与えて居ます。小は街角の専門店で,良く限定何個という店がありますが,これが同じ戦略を採っていると考えて良いでしょう。
2000年代,大学教授の間で流行ったパソコンは,Appleとレッツノートでした。私もレッツノートを愛用していましたが,それは頑丈さと高性能に惹かれてのことでした。他のパソコンが10万円台に値崩れするのに,このレッツノートだけはいつまで経っても値崩れせず,20万円台を維持していましたが,常に品薄になるように生産量を抑えていた成果であると聞き及んでいます。商品に魅力があればこそ出来る芸当なのです。
この生産方式では,時々欠品になるように,ここで云う『安全在庫』は限りなくゼロに近い状態で維持していることが窺えます。
[6-4]在庫後補充生産方式
飲茶を思い浮かべてください。店に入ると蒸し器に様々な点心類が並んでいて,茶を飲みながら気の向くままにそれらを食す事が出来ます。空になった蒸籠は直ちに回収され,新しい点心を入れて蒸されます。この飲茶と同じように, 完成品の在庫を揃えておいて売れた分だけ直ちに生産して後補充しておく方法を言います。屋台で売っている大判焼きや,たこ焼きなどがなじみ深いと思いますが,トヨタ生産方式の目玉である『かんばん方式』は,その工程の完成品を『仕掛かりかんばん』を付けて棚に並べて置きます。後工程の人が必要な品物の取りに(買いに)来て,『仕掛かりかんばん』を外して,代わりに持ってきた『引き取りかんばん』を付けて持ち帰ります。その結果,ある時間内に売れた(引き取られた)品物の総数が外された『仕掛かりかんばん』の総数になるので,その工程では所定の時間内でその製品を作って棚に入れておきます。
この繰り返しで,工程間の完成品在庫量は全種類所定の数量に範囲内で維持されることになります。
『平準化生産』と言う条件の下で行われる『かんばん方式』は,実は『在庫後補充生産方式』であったのです。
[6-5]材料や中間製品を在庫後補充にする生産方式
[6-4]の在庫後補充は理想的ではありますが,現在のように扱う品々の種類が多い場合,全点在庫を置くには膨大な数量になってしまい,管理しきれません。それで,原材料や中間製品の形で準備しておいて,注文に応じ即時に作り上げてお届けする方法が採られるようになりました。
その典型が中国料理の店です。メニューは一冊の本にもなるほど豊富です。5〜6人で食事をする場合10皿余注文しますが,中には砂時計を卓上に置き,間に合わなかったら1皿サービスすると言う店もあるくらい,たった数分間で全料理がテーブルに載ります。その調理のコツを聞いたところ,中国人店主曰く『食材は調理しやすいように前準備してある』事と『注文が調理場に届いた順に,一皿ずつ料理することだ』と言っていました。これは正にトヨタ生産方式の教える極意と同じでした。
[6-6]三種混合生産方式
市場の競争は地球規模に広がり,オリンピックさながらの各国を代表する強者の競争になって来ました。同じ原材料を使って創る商品同士では,かかる原価はほぼ同じになります。すると競い合うのは性能(品質)と納期になります。
客から見れば注文してどれだけの時間で入手出来るか(Order-to-Delivery-Lead-Time)が問題になります。
Makerとしては棚卸資産回転数(着工から完成までのLead-Time)が 問題になります。
そうすると中国5千年の歴史から生まれた『飲茶(在庫後補充生産)』『一般中国料理(短いOrder-to-Delivery-Lead-Time)』『受注生産』の3種類の作り方を,売れる数量によって使い分け,顧客の要望を,少ない在庫で対応させるという混合型生産方式が一番競争力が強くなります。これの詳しい説明は次回以降に致します。
【7】安全在庫は変化させず改善を評価する
さて,話を元に戻しましょう。
問題は,工程内の生産方式を2時間というTACT-Timeで5個単位で生産する連結した生産ラインを作って,工程内在庫を減らしたけれど,いままでの約束であった毎週100個ずつ納入し,100個は安全在庫を持つという約束はどうすべきかと言うことです。
日々変化する『売れ』と変化させたくない『生産』との間にはクッション代としての『在庫』はどうしても必要ですが,具体的に『販売現場』と『製造現場』どんな戦略で臨むかの合意を得ないと前に進めないことが【6】の説明でお分かりのことと思います。
それで,ここの安全在庫は100個(5日分)のままとします。そうすると,第13図のようになります。
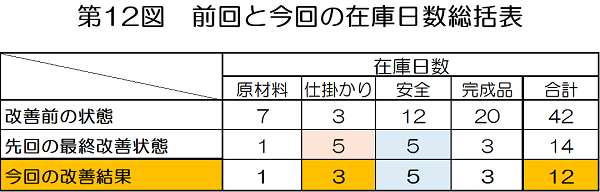
次回は販売サイドと協議して,今流行の情報の活用を図り,安全在庫を減らして行く取り組みを研究します。
2018年2月
(株)Jコスト研究所 代表 田中正知