連載コラム『Jコスト改革の考え方』 第 7回目
『速く作る』と『早く作る』の違いを考える
この原稿を書いているのは8月の末です。皆さまも小学校時代,夏休みの宿題が完了しなくて,丁度今頃 ベソをかいて机に向かった経験をお持ちと思います。
私は母親からは「よい子は休みになると,早く宿題を済ませ,その後遊びに行くのだよ!お前は宿題を後回しにして遊びに行ったからこんな目に遭うのだョ・・・」と言われ続けてきました。
その私は,70歳過ぎた今日になっても,9月に当サイトに掲載する原稿を,締め切りギリギリで書いています。
実は, 『早く』やってしまい,残りを悠々と過ごすやり方と,納期ギリギリまで着工を遅らせて,着工したら 『速く』完成させて納入するやり方が,生産管理の方法として存在しているのです。
前者はどちらかと言えば成り行き任せ的なところがあり,多くの会社ではそうなってしまっているのですが,それを 『フォワード計画』と言います。
後者は完成品在庫をできるだけ少なくするように,納期から必要リードタイムを逆算して生産計画を立てます。是を 『バックワード計画』と言います。
その優劣は,夕食の準備を考えれば解ると思います。成り行きで料理を作っていけば,夕食までに,スープは冷め,サラダは浅漬けになってしまいます。料理名人は,出来たての美味しいときに食べられるように,食事時間に合わせて計画的に料理をしていきます。
『本流トヨタ方式』では前者を 『早い』生産と言い,後者を 『速い』生産といいます。
今回は,この 『早い』と 『速い』のちがいを,話が分かり易いように,抽象化したモデルで考えていきたいと思います。
乙社は,得意先のホームセンター甲社と納入契約を結んでいて,例えば甲社が10月に店頭販売する品物は,7月20日まで内示を受け,8月20日に確定注文を受け,9月に生産し9月末日に1ヶ月分を纏めて納入していました。サプライヤー丙社にも同時に内示,確定注文を行っていて,9月生産分は,8月末日1日前に1ヶ月分纏めて納入する約束になって居ました。
以下,詳細を 【方法-1】から 【方法-4】まで変えていくと,毎日の完成品在庫量材料・部品の在庫量はどのように変わっていくか,ご確認下さい。但し,工程内仕掛かり在庫は100個,完成品の安全在庫は100個のままとします。仕掛かり在庫と安全在庫の減らし方は次回考える事にします。
【方法-1】9月度の受注は400個で,9月30日発送,自社の生産能力は安定せず,ここ3ヶ月はフル稼働で25個〜35個の実績でした。8月末在庫は100個,9月の稼働日は20日間として,どのような生産計画にすべきでしょうか?
最近では,必要部品や必要要員を手計算で出来る人は希で,20年くらい以前から導入されているERP(MRP)に生産計画を登録すれば,自動的に計算してくれる事に慣れてしまって, 『全部お任せ』がまかり通っています。
しかし,MRPには生産計画機能がありません。製品生産量に対してそれに必要な材料や部品の数量を計算し打ち出してくれるだけなので,9月1日から1ヶ月間掛けて使う400個分の資材,部品を一括して指示しますから,全部品が8月中に入荷されてしまいます。生産速さに対する阻害要因は自工程の能力だけになります。
何処の現場にもライン停止恐怖症があって,生産計画は一刻も 『早く』達成したいという力が働きます。
【方法-1】現場任せにする(早く着工,早く終了)
そうすると現場では,毎日目一杯生産していき,30〜35個ずつ生産を続けていくことでしょう。13日目には400台の生産が終え,14日目から月末までは仕事なしで過ごすことになります。
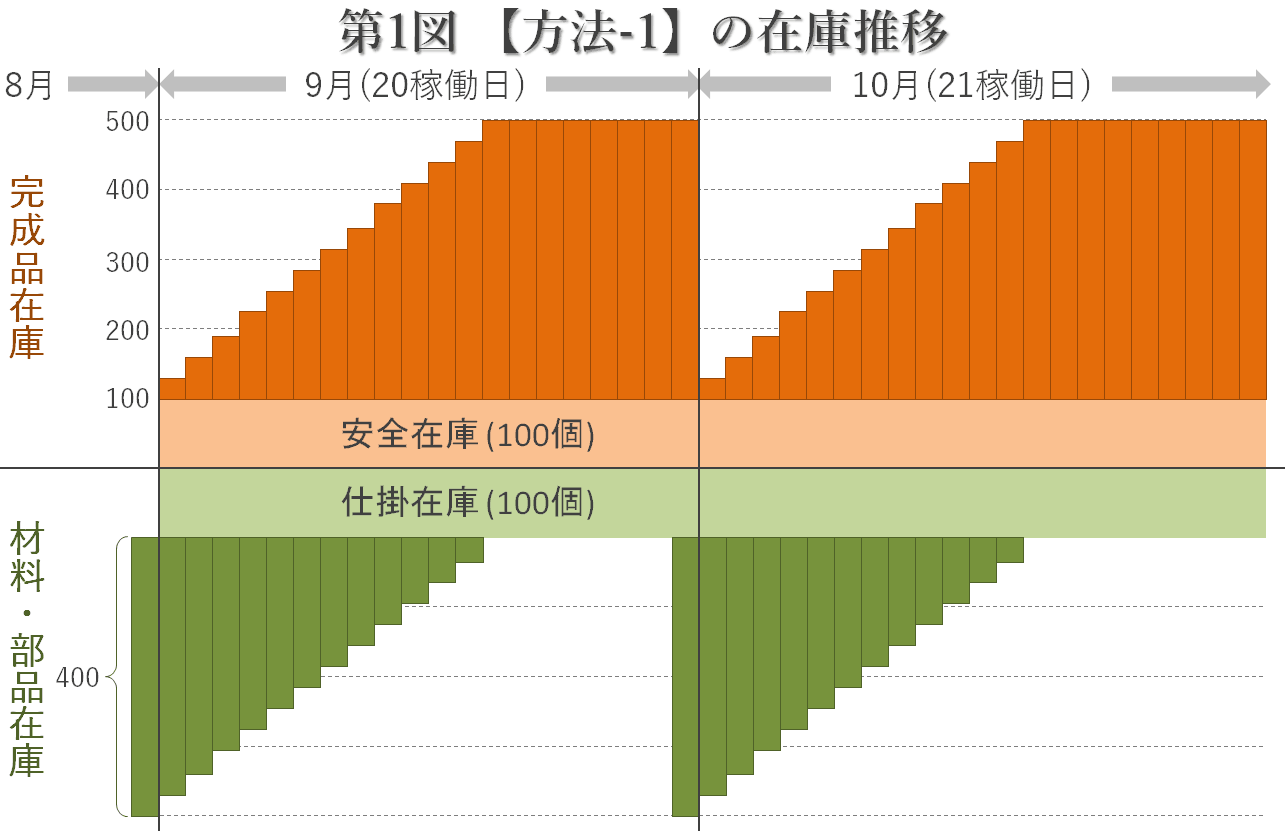
【方法-2】平準化生産する
100個の安全在庫はあるので,ラインが停まるようなことがあっても対応出来ますから,毎日20個ずつ平準化生産させる方法です。最大能力の57%しか使いませんから,同じ要員数で『減産』したら,怠け癖が着いてしまいます。
【2-1】ベテランから生産ラインから外して生産量に見合って要員数に減らします。その結果,未熟練者を訓練しながら生産をする形になります。外れたベテランは,未熟者に着ききりで指導したり,日頃手を付けることが出来なかった設備故障の真因追求や,精度不良対策など,現状の生産ライン抱えている問題の解決に当たります。他部署に応援に出たり,交代要員となって年休を取らせたりもします。
【2-2】現状の要員配置のままで,生産能力向上を図ります。1日(実働7時間)35個であれば,今の最大能力は1個作るのに12分掛かっているという事です。
これを11分更には10分台でバラツキ無しで生産出来るように,毎日20個生産するという枠の中で,ある時間だけ生産してはラインを停めて改善していく方法です。翌月に増産を控えたときには有効ですが,実際の運営は難しく,ロスが多い方法です。
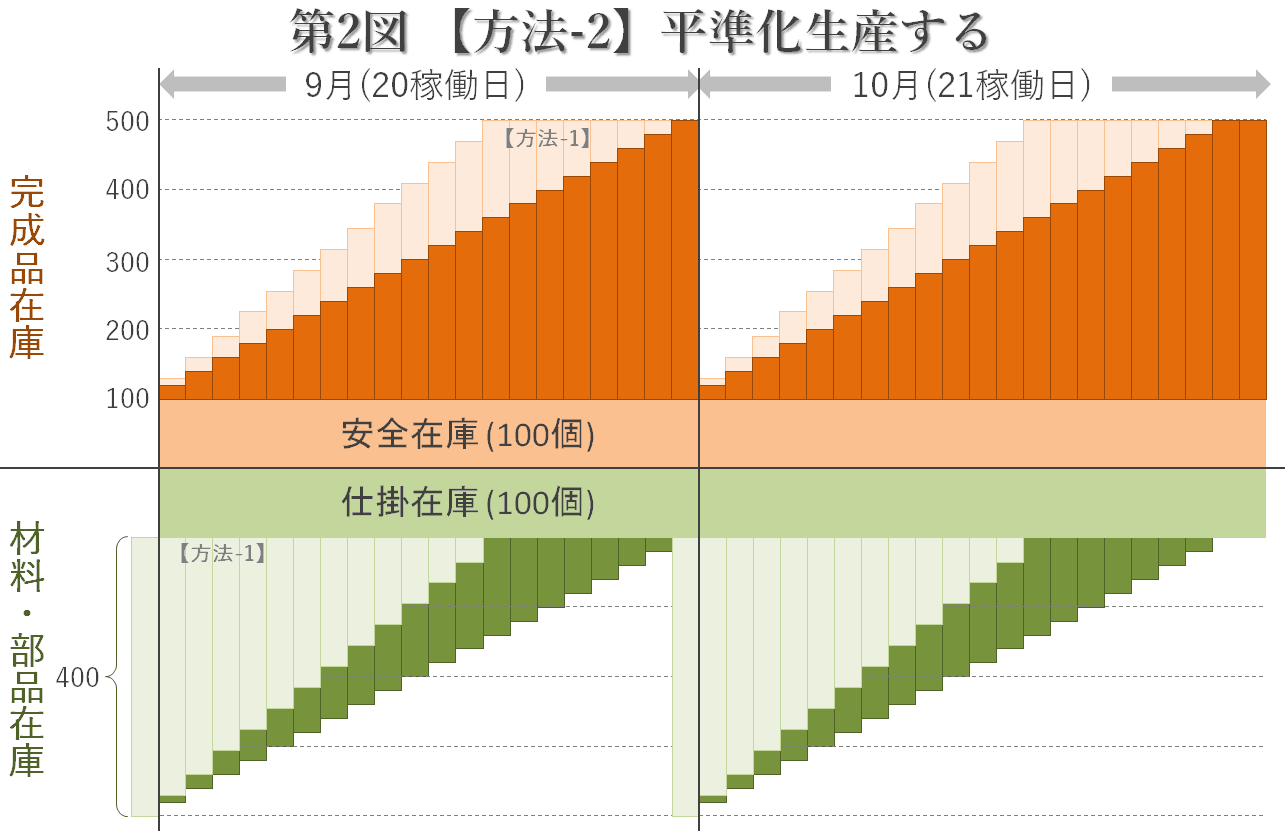
【方法-3】納期逆算で遅らせて着工し, 『速く』生産する
【3-1】今の実力では13稼働日以内で出来る計算になりますから,納期の13稼働日前に着工し,毎日毎日懸命に遅れないように 『速く』つくるやり方です。
【3-2】この考え方をサプライヤーまで展開すると,部品等が必要になるのは,生産が始まる13稼働日前ですから,14稼働日前までに納入すれば良いことになります。
従来から1ヶ月纏めて前月末に納入するために,8月頭から生産し一度に 8月末日に納入していましたが,8月末日の14稼働日前に着工して9月末から14稼働日前に間に合うように 『速く』作れば良いことになります。
【3-3】更にサプライヤーの生産を突き詰めて考えていくと,納入先では1日に最大で35個しか作っていません。ギリギリ遅らせて考えると,1ヶ月分纏めて納入することは必要ではなく, 翌日使う分を前日に届ければ良いことになります。
つまり,9月末の14日前から毎日最大35個ずつ納入すれば良いことになります。

【方法-4】得意先の売れ具合に合わせて遅らせて納品する
得意先は大手のホームセンターで,商品は殆どが(土)(日)に売れています。更に,月末に売れる傾向がありました。そこの購買部は1週間の販売実績を(月)に集計し,(火)にその会社のデリバリーセンターに各店舗に後補充の配送数量を指示し,(木)の10時に各店舗に届けさせていました。
今例に挙げている10月分の得意先からの発注量は,8月末の在庫予測と,10月の販売予測をもとに,甲社の仕入担当が8月20日に決めたものでした。
【4-1】受注量を4等分し毎週月曜日に納品することに
9月度の受注分(10月の販売計画用)は9月30日400個一括納入ではなく,ギリギリ遅らせて,10月2・9・16・23日の4回に亘って100個ずつ納入した方が,得意先のデリバリーセンターのスペース上も都合がよいとして話が纏まりました。そして,10月最後の週30日の分は,ホームセンターの11月販売計画分として9月20日に注文いただくことで話がつきました。
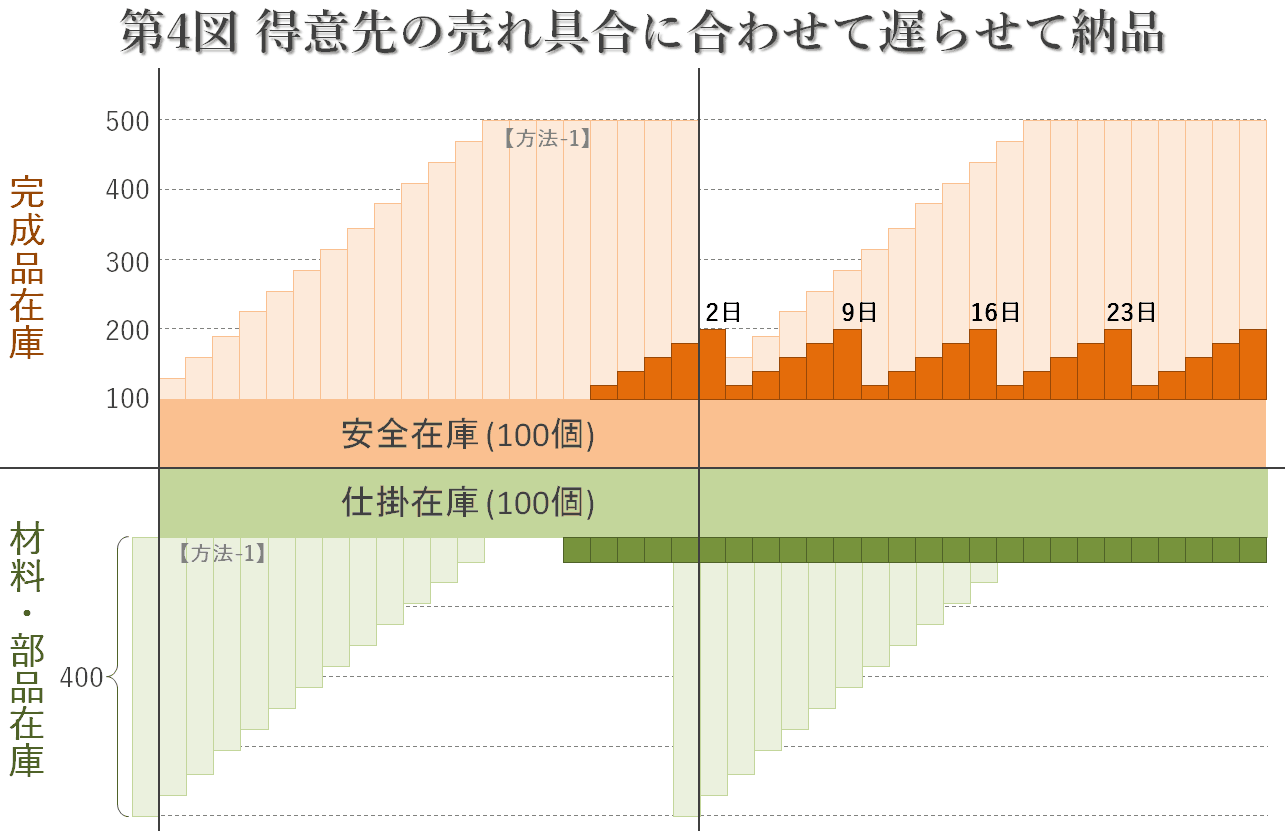
第4図を見て1ヶ月分を纏めて納入していたときと,4回に分け1週間分ずつ納入することで,在庫量が劇的に減ったことが分かります。
それだけではありません。9月生産(甲社10月販売)の開始が9月1日,終了が9月20日頃だったものが最終的には,生産開始が9月25日,生産終了が10月23日となり,1ヶ月間も遅らせることが出来たのでした。甲社からの代金支払い期日は変わりませんから,驚異的に資金繰りが良くなったことになります。
作業改善による工数低減や,品質向上活動は,作業者自身が『自己実現』の為に欠かすことの出来ない大切な『KAIZEN』活動です。しかし,工場のスタッフがやるべき 『改革』は第1図のような現場を,第4図のように変えていくことにあります。
此の改革は未だ道半ばですが, 『 早く着工して 早く完成する』事が会社に損失を与え, 『できるだけ 遅らせて速く完成させる』事が会社に大きな利益をもたらす事がお分かり頂けたと思います。
しかし,工場の優秀なスタッフが 『できるだけ 遅らせて速く完成させる』道を選んだとしてもどれだけ遅らせられるかは,設備故障率,品質不良,無断欠勤が無く,計画通りに合格品を生産出来るという,当たり前の事だけれど,一番難しいテーマ,いわゆる 『強い現場』づくりが必須なのです。そのため現場全員の チームワークと日々の弛まぬ 『KAIZEN』が必要とされているのです。
次回は,此の改革を, 『Jコスト論』で捉えるとどうなるかについてお話しします。お楽しみに・・・。
2017年9月
(株)Jコスト研究所 代表 田中正知