連載コラム『Jコスト改革の考え方』目次
JBpress連載コラム『本流トヨタ方式』
ビジネス情報サイトJBpressにおいて、2008年から2013年までの間に合計104回のコラム 『本流トヨタ方式』 を連載していました。
現在連載中のコラム 『Jコスト改革の考え方』と併せて読んで頂くと、より深くJコストの考え方がご理解頂けるかと思います。是非、下記のリンクにアクセスしてみて下さい。
過去の所信表明
2025年6月
所長 季節のご挨拶
6月に入り,梅雨が始まるや否や猛烈な暑さが襲いました.
皆様いかがお過ごしでしょうか.
テレビでは朝から熱中症対策についての注意を放送し,特に注意すべきは,幼い子供たちで,身長が低いため,路面からの輻射熱を全身受けることになるので熱中症になり易いとのこと,また高齢者は,知覚が鈍くなり易く,暑いという事や,口が渇いた事に鈍感で,熱中症にかかり易いとしつっこく放送しています.
高齢者で,高血糖の筆者は,キンキンに冷やした緑茶とスポーツドリンクで対応しています.
皆さまも,御自分に合わせた水分補給得で,この酷暑を乗り切ってください.
さて,海外に目をやりますと,2025年6月は,世界史の教科書に載るような大きな出来事がありました.その主な出来事と,日本に及ぼす影響を,弊社なりに占ってみたいと思います.
(1) 韓国は『反日』の『李在明』が大統領に就任した.
韓国は1997年通貨危機に陥り,当時はまだ発展途上国であるとして先進諸国からの援助の手が差し伸べられ,危機を脱出しました.その後,奇跡的な発展を遂げたとして,自他共に認める地位を確保しつつ在りました.
当時の経済の専門家たちは,今韓国が中国に売りさばいている製品は,工業の発展とともに中国の方が韓国よりも安くできるようになる.日本と協力して全世界に打って出る体制を構築すべきと提案していました.
文大統領は,『反日』『親北朝鮮』『親中国』に舵を取り,経済専門家の言うとおりになってしまい,その上内政政策の失敗も相まって,韓国の現在の国の借金,企業の借金,個人の借金の三重苦を作ってしまったと言われています.それは,1997年の通貨危機よりもひどい状態になるのではないかと危惧されています.
ちなみに現在日本は台湾とタッグを組み,熊本に巨大な半導体工場を作り世界に打って出る準備をしております.
いよいよ日本と中国に挟まれてきた状況の中で,前期の尹大統領は,今までの日韓関係を精算して日本との関係修復に舵を切り,更なる連携の道を探っていましたが,『反日』を主張する『共に民主党』の強烈な反対運動の前に敗れ,弾劾裁判にまで及びました.
この6月の大統領選で当選したのは,『反日運動』の権化とも言うべき,李在明大統領なのでした.彼が韓国をどう導いていくか,注目が必要です.
因みに,韓国の『反日運動』を一目で理解するには,YouTubeで『韓国ウリカルト図表』と検索すれば,世界中があきれる実態が映し出されます.
その一例等は,おとなしい説明で,お薦めします.
(2) 中国が起点の,世界大恐慌の引き金になる恐れあり
筆者の体験談からお話ししましょう.
2013年から上海にあるコンサル会社と契約し,蘇州,杭州,河南省等で年間10回ほど講演やコンサルティングをやってきましたが,当時は訪問するたびに街の形が変わるほど急激な発展をしておりました.
一応五つ星ホテルに宿泊していましたが,日本との違いはどのホテルも部屋がやたらと広いこと,防毒マスクとコンドームとカップ麺が必ず設置されていることに文化の違いを覚えました.
テレビ番組は約60チャンネルあり,CNN,ABC,NHKは自由に見えました.インターネットもGoogle以外は自由に使えた覚えがあります.
2020年からは中国訪問はコロナで中断し,2024年に久しぶりに訪れた上海は,様子が変わっておりました.
人でごった返していた浦東机場の入国審査場は,すいすいと通過でき,交通量が減っているのを実感しました.テレビ番組は,中国語のみになってしまい,何がどうなってるかよくわかりませんが,スイッチを押すと『政府のお知らせ』『教育番組』『バラエティー・ドラマ』のサムネイルが画面に出てそこから選ぶSystemになっていました.
何よりも驚いたことに,各ホテルでWi-Fiにつなぐことができましたが,外国人がインターネットにつなぐためには当局の許可書がいる様に変わってしまっていました.
結局,日本で契約していったスマホの『海外ネット契約』だけが頼りでした.
中国の政治・経済はマスコミ報道では,2019年からの香港への統制強化,コロナ禍に於ける上海の強制ロックダウン,経済活動に大ダメージ,市民生活の困窮,不動産バブル崩壊・・・.海外資本の引き上げ・・・.等が報じられていますが,筆者の経験から見れば,中国という国は,2019年という年を境にして全く違った国になってしまった,と断言できます.
共産主義政権の寿命という考えでまとめてみますと,以下のようになります.
- ソ連は1920年〜1990年の70年間
- 東ヨーロッパ諸国は1945年〜1990年の45年間
- 中国は1949年〜で75年目
- 改革開放政策1980〜2018は共産主義では無かったとすれば37年目
最近行われた農耕地拡張運動は,毛沢東が犯した誤りと同じことを繰り返すように思えます.中国のあれだけの大きな組織を一党独裁体制でコントロールできるとはとても思えません.近いうちに何らかの形で政治体制に大変化が起きると覚悟しておいた方が良いでしょう.
(3) ロシア崩壊の危機
2022年2月24日から始まったロシアによるウクライナ侵攻は,膨大な戦力を背景にロシアの圧倒的勝利と思われましたが,ウクライナの不屈の反抗で持ちこたえておりました.
2025年6月,ウクライナが独自に開発した各種のドローンと,巧みな作戦によりロシア本土の燃料施設や軍事施設に攻撃を仕掛け,大きな戦果を上げています.
ロシア国民にとってみれば,ウクライナ侵攻は外地の出来事だったものが,ロシア本土の要所要所を攻撃され,しかも市中金利が20%を超えるようになり,物資の不足し生活が困窮してきました.
ロシア庶民の困窮ぶりは,1980年後半のソビエト連邦に似ているので,このまま行ったらロシア連邦が解体されるのでは……という憶測が流れています.
(4) G7 Summit の出来事 米国孤立???
6月15日から17日まで,カナダのアルバータ州で開かれたG7 Summitは,米国のトランプ大統領はイラン問題があるとして初日だけで帰ってしまいました.
YouTube上では,米国抜きの商取引の約束事が話し合われたとされています.
マスコミの裏を取れていませんが,度量衡の世界で,米国のみがヤードポンド法で他国はすべてメートル法になっています.そんな中で国際技術標準がヤードポンド法で書かれているとすれば大きな矛盾です.
通貨も,現在のような高度に発達した通信社会では,為替市場と連動して互いの通貨で決済すれば,国際通貨としてのドルはなくても商取引は可能なはずです.
『お前のセリフが気に入らないから明日から関税を20%上げる……』ような国とまともなビジネスはできません.グローバルな企業と自認する会社は,そんな国と関わりたくなるはずです.関わりたくなければ本社を移してしまえばいいわけです.
例えばアマゾンにとってみれば,世界から品物を仕入れて世界中に売るわけです.その物流のハブをアメリカ本土に置けば,輸入品に全部関税をかけられてしまいます.
アメリカ以外のところにハブおけば,アメリカに売る分だけ関税がかかることになりますから,当然アメリカから出てきます.
トランプ大統領の輸入関税の駆け引きを見ていると,自分の体に刃物を押し当てて,自分の言うことを聞いてくれないと自分の体に傷をつけると言っていることに等しい行いです.
関係者は血を見るのが嫌なのでご機嫌とっていますが,度が過ぎれば『お好きにどうぞ』と言えばいいだけです.関税が完全上がって困るのは米国民です.トランプ大統領が言うような10% 20%の高関税で自国民が生活できるはずがないのです.
さらに言えば,米国民にとってみれば輸入品全部ですが,輸出側にとってみれば,全世界に輸出しますから米国向けはほんの数10%にすぎません.
賢いネゴシエーターは,相手がくたびれるのでじっくり時間をかけて話をするでしょう.
日本の赤澤大臣は,ニコニコしながらじっと時間を待つ作戦に出ています.最高の策だと思います.
裏は取れていませんが,トランプが帰った後のG6 Summitでどうやってアメリカを外して世界を回して行くかが話し合われたものと私は信じます.
つまり,2025年6月を以て,ヒノキ舞台の上にアメリカはいるけれど,誰もアメリカにまともに話しかける人はいない時代が始まったと思います.
(5) アメリカのイラン爆撃
2025年6月22日イランの核施設を米国のステルス爆撃機がバンカーバスター弾を投下しました.『これは広島に原爆を落として太平洋戦争を終わらせたと同じで,必要な選択だった』と語ったそうです.この言葉は日本では物議を醸しました.
元はといえば,イランとの間に核拡散防止条約を結んであったのを,前期のトランプ大統領が不十分であるとして廃棄し,それにイランが反発してウランの濃縮を始めた経緯があります.核を持つ常任理事国の大統領プーチンが,突然ウクライナに侵攻した事と同じ事を,核を持った常任理事国の大統領のトランプがやったということは,プーチンにウクライナ侵攻をやめろという資格がなくなってしまったことを意味します.
まとめ
所長挨拶として2025年6月に起きた大きな出来事を取り上げました.
言い方を変えれば@ロシアのプーチン大統領,A中国の習近平主席,Bアメリカのトランプ大統領の率いる大国が,老人の妄想により全世界をとんでもない危険な状態に陥れている事と,隣国の韓国が経済破綻の崖っぷちにありながら,反日を唱える一方で協力を求めてきている事を紹介しました.
7月以降どのような展開になるのか分かりませんが,リーマンショックをはるかに超える大不況が全世界を襲う可能性が極めて大きいとされています.これに備えての対策に邁進して頂きたく思います.先月申し上げた『人を減らすな!在庫を減らせ!』『省人化ではなく少人化を』等を参考にしていただければ幸いです.
『日米貿易戦争とトヨタの対応』
以下,前回に引き続き『日米貿易戦争とトヨタの対応』についてお話しします.
筆者は1995〜1996年の2年間トヨタの物流管理部長の職におりました.
1995年春,渡米して,GMとの合弁会社NUMMIを視察しました.すると,売れていると言うトヨタブランドのC車の完成車Yardは満タンでした.ところが,売れていないというGMブランドのP車の完成車Yardは空でした.
売れている方の工場在庫が少なく,売れてない方の工場在庫が多いというのが常識ですが,NUMMI では,それが正反対だったのです.現地駐在員に,実態を調べて報告するように厳命をし,帰国しました.
半年後に調査結果が届き愕然としました.内容は以下の通りです.
【A】米国 BIG 3の生産のOrder-to-Delivery-Lead-Time
米国のBIG3は,週次生産・週次決済が基本で,N週の売れ行きを見て,(N+2)週の生産計画を立てて(N+1)週に部品の手配をし,(N+2)週に工場で生産し,(N+3)週中には全米に配送完というLead-Timeでした.(駐在員の報告では,実態はもっと時間が掛かっている……とのことでした)
米国デーラーは在庫販売方式ですから客から見たOrder-to-Delivery-Lead-Timeは,以下のようになります.
- 売れ筋; デーラー在庫(デーラー籍),客; 即納
- 人気車; 各州のセンター在庫(Maker籍),客; 数日後
Makerは週次補充 - 特注車; 受注生産(在庫無し),客; 3〜4週後
ちなみにメーカーの部品+車両のLead-Time(理論値)3週間
【B】日本メーカーが完成車輸出した時のOrder-to-Delivery-Lead-Time
日本メーカートヨタ・日産・ホンダの3社は,ロスのTorranceに本社を構えており,窓から互いの会社の看板が見える状態でした.3社とも,月次生産・月次決済を採用しており日本生産車はM月中旬に日本の生産管理部で(M+1)月の全世界向けの生産計画を決め,部品の手配をします.(M+1)月の十数本の生産ラインで全世界向けの車両の生産が行われ,次々と輸出先別埠頭に運ばれ輸出手続きを済ませます.
当時の自動車運搬船は乗用車換算で4000台積載できましたが,税関が輸出用保税Yardに4,000台揃った時点ででしか輸出用書類の受理をしてもらえなかったのでLead-Timeの大きなロスとなっていました.
船便は日本出港から米国港での荷揚げまで,西海岸で2週間,東海岸まで3週間掛かりました.
一口で言えば,(M+2)月に米国揚げ港に到着となります.
つまり,日本車は,揚げ港に膨大なMotorプール在庫を抱えての在庫販売になります.
米国の客から見れば店頭在庫販売ですから,Order-to-Delivery-Lead-Timeは
- 売れ筋; デーラー在庫(デーラー籍),客; 即納
- 人気車; 各州のセンター在庫(Maker籍),客; 数日後
Makerは揚げ港在庫から週次補充 - 特注車; 受注生産(在庫無し)
日本に発注するので(M+2)月後,客; 10〜14週後
ちなみにメーカーの部品 + 車両のLead-Time(理論値)10週間
【C】当時の米国での日本メーカー 米国現地生産車
日本の生産管理部で,日本で全世界向け完成車生産をするのと同じようにM月に(M+1)月用の『部品輸出計画』を立て,Supplierに日々の個々の部品の納品指示をします.
(M+1)月になると,各Supplierから納品された部品を計画に基づいてコンテナにバンニングして米国へ輸出します.日本側でバンニングしてから,現地組立工場でデバンニング(開梱)するまで海上コンテナで約一ヶ月掛かりますから,M月に生産計画を立てた車両用の部品が全部米国の組立工場に届くには(M+2)月になっています.
結局,M月に日本の生産管理部が計画した生産計画で,現地米国で全て完成車にするには,何と,(M+3)月末になってしまっていたのでした.
これを米国の客から見れば,店頭在庫販売方式ですから
- 売れ筋; デーラー在庫(デーラー籍),客; 即納
- 人気車; 各州のセンター在庫(Maker籍),客; 数日後
Maker各センターに補充 - 特注車; 受注生産(在庫無し)
日本に発注し,届いた部品で製造するので(M+3)月後
客; 14〜20週後
ちなみにメーカーの部品 + 車両のLead-Time(理論値)約14週間
【D】当時のトヨタと国内販売店間のOrder-to-Delivery-Lead-Timeについて
トヨタと各販売店の間で年間の車名別販売台数を契約する.(ファーム制度)
販売店は,お客様と車の仕様の細部(色・タイヤ・オプション等々約20項目)を詰め,トヨタに最終注文すると,3日後その通りの仕様の車がライン・オフします.販売店はフレームナンバーと車庫証明を持って当局に届けてライセンスプレートをもらいます.ほぼ同じ頃車両が店頭に届きます.販売店は車両を磨き上げ,細部のオプションを取り付け,認可されてライセンスプレートを取り付け,納車します.これを米国販売店と同じ様に整理すると
- 売れ筋; デーラー店頭,客; 所有権移転手続き3日後
- 人気車; デーラー内のセンター在庫,客; 約4日後
- 特注車; 受注生産,トヨタ生産3日 + 店頭までの輸送 7日
ちなみにメーカーの部品 + 車両のLead-Time(理論値)1週間
註: トヨタの国内完成車は全てデーラー籍
更に,車両組み立て工場で使う部品は,在庫補充方式を使い4時間間隔でサプライヤーから納入されています.その結果組み立て工場内の棚卸資産回転数は一日以下となっています.
半年後に米国から報告されたこの状態調査結果について,全く驚きでした.
調査結果を受けての物流管理部としての判断
(1) 客の立場で見たOrder-to-Delivery-Lead-Timeについて
米国産車も日本車も、米国の販売方式すなわち巨大な店舗での在庫販売の下では、Order-to-Delivery-Lead-Time 店頭で買い取り所有するまでの時間は、人気車では互角の戦いが出来ている。客のこだわりを入れた特別仕様車では、
米国産車;3〜4週後 < 日本産日本車;10〜14週 < 米国産日本車;14〜20週
と理論的には大差がありましたが、トヨタの販売部門の見解で、実態は下記のような理由で販売店と客との間でいわゆる『Deal』があり、当時の時点でわ特別仕様車のリードタイムを短縮する課題は優先順位が低いとの事でした。
販売店の店頭在庫というのは,モータリゼーションの進んだ米国では色やグレード等々,Userの好みが多岐にわたっていますので,そう簡単にフィットするものではありません.店主が選んだ品揃えでも、半年間売れずにいるという車もざらにあります.このため販売店は,多少値引きしても店頭にあるクルマを客とDealして売り込んでしまいます.
現地の実態調査のLead-Timeというのは、あくまでも理論値であって、店頭に訪れた客にヒットさせるために、販売店はリスク冒してできるだけ多くの在庫を持ち営業しています。その実態を是認すれば、当時の日本車の販売店は米国車の販売店と互角に戦っていたと判断できました。
一番の問題点は,市場が冷えて販売台数が減少してきた時に,どのタイミングでブレーキをかけるかということです.米国内で生産する日本車については,ブレーキがかかるのは3ヶ月後ですから,現地の需要を100%現地生産車で補うことは,売れない車を大量に抱え込むというリスクもありますので,当面は米国内での完成車生産は腹8分目か7分目で納めておき,残りは日本から完成車を輸出するという作戦を改めて確認しました.
ここまでは製造会社の市場応答性という観点で話をしてきましたが、物流部門として改善しなければならないテーマとして、工場の生産ラインの出口から、米国販売店までの完成車在庫(トヨタの棚卸資産)をいかに圧縮するかにありました。
ここから話は脇道に逸れますが、通関業務の実態を知っていただくために当時やった改善事例を紹介します。
当時は保税ヤードに完成車を約4,000台ずつまとめて置き、夫々を船便に引き当てて総局に輸出許可を頂いていました。完成車から見ますと、到着してから数便待って船に乗る状態でした。
一般貨物と違い乗用車は、それぞれフレームナンバーを持っており、工場でラインしてから船に積むまで一本道になっています。ラインをした時点で仕向地が決まっているので。その情報を元にして通関手続きをすれば、船上通関(船に乗せてから通関手続きをする)ことが可能であるとして、あの手この手で当局に訴えました。
当局はなかなか首を縦に振りませんでしたが、後輩たちに後を託して私は定年退職しました。退職して数年後、部下から念願の『船上通関』が許可されたとの通報を受け取りました。これで、運搬船数隻分の在庫を削減出来たのでした。
2008年リーマンショックがあり、世界中が大不況になりましたが、ホンダと日産は、米国市場での販売状況がおかしいとして、4月以降企業トップから減産命令が出されたと言われています。ところが『Just In Time』を表看板とするトヨタが、減産をすることなしにリーマンショックに突っ込みました。その結果膨大な在庫を抱えてしまい、その処理のために数年間、赤字が続きました。
大野耐一の直弟子として張富士夫、池渕浩介、林南八の3名が『トヨタ生産方式』の『技監』と言う地位にあった時の出来事でした。
『トヨタショック』を機に、豊田家の御曹司 豊田章男が社長に着任しました。
彼は『トヨタ生産方式の原点復帰』をスローガンに、社内を大改革し、今日に至るのでした。この辺の詳細は別途『TOYOTAとNISSANの歴史をJコスト論で斬る』コラムで紹介いたします。
(2) トヨタとSupplierの関係
日米の貿易摩擦の解消のためには『部品をあくまでも米国内で生産しろ!』ということになります.ここで日本企業のカーメーカーとサプライヤーとの関係が欧米とは違っていることを再確認する必要があります.
以前にドイツでは,技術部門が車両の完全なる設計図を完成させ,生産技術部門は設計図通りの車両を生産する設計を準備し。製造部門はその設計図どおりの車両を製造すると言う完全分業になっている話をしました.
この完全分業が出来ていれば,部品の品質は設計図でしっかり保証されており,あとは価格交渉で安いところに発注すればよいという考えになります.
それ故,欧米の自動車は水平分業になっており,世界各地のサプライヤーからコスト最優先で部品を集め完成車にする方策が取られております.
米国のビッグスリーもこの法則に従っており,単価の安さを基準に多くの構成部品を海外メーカーから購入しているのです.
これに対してトヨタは全く異なった考え方をしております.
組織の壁を取り払い,コンカレントエンジニアリングという考え方で,開発段階から生産技術や製造現場さらには部品メーカーが入り込み,例えばデザインが決めたヘッドランプの形状の中で,ランプの熱をどう逃がし,隣り合う部品との見栄えをどう向上させるか.関係する車両メーカー,部品メーカーが同時並行に設計おすすめ,そこにそれぞれの製造現場が入り込み,御客様に愛される車づくりを目指してとことんすり合わせをしているわけです.
図面にかけないノウハウで細部を取り決めているのです.
こういうやり方で設計しているので,一緒に開発した仲間以外に部品を発注するという発想は浮かんできません.
先に述べた1995年の頃は,トヨタ系のサプライヤーがまだ充分北米に進出していなかった時代でしたが,その後に,以前述べたように,米国政府の圧力で無理やり米国のサプライヤーから部品を輸入させられることになりました.不良率が高い米国のサプライヤーから物を買うぐらいだったら,日本でお付き合いしているもともとのサプライヤーに米国に進出していただき,現地で生産することにして【D】で書いたような,日本国内のサプライチェーンと同じもの北米に作るのがベストであると誰もが考えるようになりました.
2011年の東日本大震災は,日本からの部品が届かず、2011年4月〜6月に掛けて生産量を半減させたと言います。日本で震災があれば,北米でも生産ができなくなるというのはまずいと誰もが思うでしょう.トヨタが日本を3分割し,どこで大災害が発生してもできれば2/3最低限1/3の生産量は確保できるようにしましたが,これは海外でも同じことで,ヨーロッパ,中国,東南アジア,北米は単独で車両生産ができるような体制を作る方向に舵を切ったのでした.
ただ自動車生産の宿命として新車発売時のピークを100とすると,モデル末期には20〜30まで落ちてしまいます.それゆえ定常状態では市場の販売数の70から80%で稼働させておき,それに対するそれぞれの地区におけるプラス・マイナスは,日本を胴元とし,各地区の乗用車を横持ちすることにより,工場の稼働率を維持し,雇用の安定化を図る政策をとっています.
トランプ関税のニュースで,日系自動車メーカーの現地工場の生産比率が市場の70〜80%とあったのは,生産量を安定させ要員の異動をなくすための方策であったのです.
話がダラダラと長くなってしまいましたが,世界のどこで戦争や大災害が起きても全体を止めずに済むように,地域分散型の生産体制を日本のメーカーはとってきました.
それゆえ,完成車25%の追加関税.自動車部品にも25%の追加関税を課したとしても,日本メーカーは北米における主要車種の生産は北米だけで賄えるようにしてあるので,ある生産台数までは全くトランプ関税の影響なしに生産できるようになっています.
特にトヨタは章男会長の下で体制整備を進めてきましたし,米国民がガソリン代を気にするような世の中になってきますから,優秀なハイブリッド車を持つトヨタとホンダが飛び抜けて有利な状況に置かれると思っています.
読者諸氏も安心して見守っていてください.
またもや季節の挨拶が長くなり過ぎましたので,『TOYOTAとNISSANの歴史をJコスト論で斬る』は今月もお休みさせていただきます.
2025年6月30日
(株)Jコスト研究所 代表 田中正知
2025年5月
所長 季節のご挨拶
我が家の猫の額ほどの我が家の畑に,連休前に植えたトマトは既に膝の高さになり,今年は脇芽の管理をして,長く楽しむつもりです.散歩道の街路樹の桜は新緑に燃え,素晴らしい景色です.
日本は穏やかな初夏を迎えていますが,皆さまは如何御活躍でしょうか.
世界に目をやりますと,隣の韓国では,前政権で高騰した不動産バブルが弾け始め,結果として,家庭債務が急膨張し,その中で頼りのサムスンの売上減が続き・・・不穏な気配とか・・・・中国は,膨大な不動産バブルが弾けだし,消費低迷⇒企業倒産⇒首切り⇒消費低迷の負のスパイラルが回り始めたとか・・・
その中国を相手に改革開放政策でしっかりと儲けていたドイツが,中国の不況でダメージを受け,更に,自動車のEV化で活路を見いだすはずが,より高性能のEVをより安く売り出した中国BYDに後れを取り,大きなダメージを受けています.
そして米国,国内企業との綿密な打ち合わせをしないままに高額な輸入関税を宣言したものですから,世界を股にかけて活動していた大手の米国企業がサプライチェーンの分断という大きな代償を払うことになり,GM,Fordなどの乗用車メーカーのみならずトラックメーカーまでが工場の海外移転を決断するに至りました.さらに広がり,Amazonや,米国の防衛産業担うBoeingまでが,工場を海外に移すという話までが持ち上がりました.
これから先トランプ大統領がどう決着を作るかわかりませんが,実業界が実際に動き始めてしまいましたから,大きな傷跡を残すことと思います.
評論家によってはリーマンショック以上の衝撃が全世界に走ると言っています.現に米国の主要企業は人員の解雇を始めました.
急速に業績を悪化させた日産は,全世界で2万人規模の人員整理をして立て直しを図るということを発表しました.パナソニックも1万人規模の人員整理をし,業績の立て直しを図ると公表しております.これらはトランプ課税による悪影響に備えての動きであると見ることもできます.
貴社はどのような対応をなさるのでしょうか?
[1] 弊社おすすめの対策『人を減らすな!在庫を減らせ!』の解説
不況に差し掛かった時,弊社の『本流トヨタ方式』では『人を減らすな!在庫を減らせ!』を邁進することをお薦めしております.
実例を申し上げますと,2020年から始まったコロナ禍の売上減対策には以下の二通りの対応策が在りました.
【A】多くの企業は『人員整理』を行い,売上減少を乗り越えてきました.
【B】一部の企業は『人員整理』は行わず,仕入れ代金の縮小で乗り越えました.
コロナが過ぎ去って,市場が生き返ってきたとき,
- 【B】の社員を温存した企業は即増産に移り,業績を急膨張させました.
- 【A】の『人員整理』をした企業は,募集しても人手は集まらず,業績回復が思うように行ってない・・・
と聞いています.つまり【B】は『危機』を『機会』に変えたともいえます.どんな方策を取れば,【B】の道を辿れるのか,考えてみましょう.
[1-1] 固定費と変動費を考え直す
以下にお話する事は,筆者が入社した頃(1967年)人事部における入社教育,作業実習に行った先の管理者はもちろんのこと,実習でお世話になった現場の監督者から再三再四言われ続けたことです.
それは1950年当時のトヨタが,終戦後の超インフレと,それを収めるための超デフレ政策(ドッジライン)によって,経理上は黒字だったが資金繰りに詰まり,銀行の追加融資がなければ倒産するという危機に陥ったこと.
この時の社長は,豊田佐吉の長男で,トヨタ自動車を作り上げた豐田喜一郎だった事.彼は『豊田要綱』にある『一,温情友愛の精神を発揮し,家庭的美風を作興すべし』を楯にとって,断固人員削減には反対した事.
銀行団との交渉がもつれ,最終的には,先ず創業者の喜一郎社長が引責辞任し,その後,社員の人員整理を行うことで解決した事でした.
そして,これが『人員整理する前に,社長が引責辞任をする』と言うトヨタの不文律ができたことでした.
作業実習中の休憩時間に,現場の組長が隣に座り『あんたは大学出だから,出世してえらいさんになるだろう.だからこれだけは覚えておいて欲しい.仲間の首を切るような会社にするな…』と話してくれました.
1950年の危機のあとを継いだ石田退三社長以下現場の末端まで,『人員整理』をせずに済む会社にするには,どうすれば良いのか考え,工夫をし,実践してきたのが『トヨタ生産方式』だったのです.
詳しい話は別途『TOYOTAとNISSANの歴史をJコスト論で斬る』シリーズでお伝えいたしますが,世の中が不況になり自社の製品が売れなくなった時,現場はどのようにして耐え忍び,力を蓄えておき,好況になったときそれを爆発させて成長につなげるか・・・についてここではご説明いたします.
1-1-1. 『減価償却費』は本当に固定費か
会計学では,『減価償却費は固定費であり,労務費は変動費』であると教えます.
これに異を唱えたのが,トヨタ生産方式で有名な大野耐一でした.
例えば,プレス型の減価償却を考えてみましょう.ただ置いてあるだけなら摩耗しませんが,生産すれば1回当たり何がしか摩耗を生じ,ある回数を使えば使えなくなるので,どう考えてもプレス型の減価償却費は変動費のはずだと言うものです.
一方従業員は,会社に出てきて仕事をしていても,仕事がなくても腹は減る.生きていくためには毎日食わねばならない.だから労務費は固定費のハズだ!と主張したのでした.
ネットで調べると,家屋などの減価償却費は固定費と決められていますが,プレス型のように,使う回数で摩耗していく機材の減価償却費は,所轄の税務署長の判断で決められるとありました.
経済の専門家たちは,今年の後半からトランプ関税影響で,リーマンショック以上の大不況がきてもおかしくないと警報を鳴らしています.減産時に備えて,固定費を減らし『損益分岐点』を下げておく必要があります.
1-1-2. 省人化と少人化
10人で1時間当たり60個生産していたラインに,自動機を導入して9人でできるようにいたとします.
【改善前】
10人作業; 60個/h (時間) の組み立てライン
【省人化改善後】
D工程に完全自動機を導入し,9人作業で60個/hを達成できたとします.
このように作業を自動機の置き換え人手を減らすのを省人化と称して多くの企業では無条件に進めていますが,ここには大きな落とし穴があります.
生産のflexibilityが失われることで,減産時は返って生産性が落ちるのです.
実際に売れなくなって時間当たりの生産台数が減少した場合を計算しましょう.
- 前工程 60個≧4人,45個≧3人,30個≧2人,……
- 後工程 60個≧5人,48個≧4人,36個≧3人,……
となってしまいます.
【少人化 改善】
トヨタ生産方式では,『少人化』という改善をお勧めします.これは市場の変化に追従して行く為に,常に生産数に比例した要員数で運営できるように改善することを意味します.flexibilityです.設備の制約をなくし,作業員を多技能化しなくてはなりません.
『少人化』されたラインでは,今の例で言えば,
- 60個≧10人,54個≧9人,48個≧8人,42個≧7人,……
となります.このように10%の減産で,省人化に掛けた費用は無駄になり,さらに減産が進めば,自動機がネックとなった少人化ができず逆に生産性を落とすことになってしまいます.トヨタ生産方式では,『省人化』の完全自動化工程はラインの両端に設置し,ラインの途中は簡易的な自動機 (道具の延長)にして『少人化』と両立させる工夫をします.
[1-2] 困窮時,どの順番で削減するかを決めておく
『本流トヨタ方式』では,常に『目的は何か』を問い直して前進させます.
会社経営の目的は,『西欧社会では株主から預かった資金を有効的に使い利益をもたらし株主に還元する….』と考えます.
『本流トヨタ方式』では,日本式経営のEssence『3方よし (売り手よし・買い手よし・世間良し)』をベースにして,『関わった人間集団の末長い繁栄』がその目的になります.即ちGoing Concernなのです.国家に例えれば,国民の繁栄です.
企業が人員削減して成長を期すと言うのは,国家で見れば,高齢医療費を削減するなどの,一部の国民を犠牲にして生き延びる事と同じと考えます.最後の手段で,トヨタでは1950年資金繰りが悪化して倒産に危機に陥った時,創業の社長が先ず引責辞任して,その後,約2割の人員削減を実施し息を吹き返しました.以来,人員削減は社長の首と引き換えにするモノという不文律が生きています.
1-2-1. トヨタ生産方式に於ける減産時の対応順序
トヨタ生産方式の公式は
- 現金支出を削減するために,まず仕入れを減らす
- 『寄せる・停める』改善で作業工程を変更し改善要員を捻出
- 工程内在庫・完成品在庫を減らし,仕入れ量を更に減らす
- 余剰人員を製造ラインから外し,段替えと運搬の多頻度化
- 余剰人員を使って余剰設備の点検修理・改造と保全技能の訓練
- 更に余った工数で,繁忙期にできなかった教育訓練実施
の順序で現場のスリム化を図っていきます.
1-2-2. 減産時の対応を可能にする体制整備
現在ほとんどの会社では,工場内の各工程で生産する品目とその数量は,事務所にあるコンピューターを使って計算され,現場に指示するのが普通です.これをPUSH型と言います.
トヨタ生産方式では,全ての工程に在庫を持たせておいて,後工程に引かれた量だけをその日の内に後補充生産する仕組みになっています.もちろん生産のための原材料は前工程に取りに行くわけです.これをPULL型と言います.
(1) 購買品の納入指示をPULL型 (在庫後補充型)に変更する
ご家庭で調理場を預かっている人たちは,家にある在庫の中で料理を考えて作ります.在庫量として不足した分を買い出しに行き補充しておきます.それゆえに日常は在庫量の中で家族の望む料理ができるのです.
ところが多くの会社では,会議で決められた翌月の生産計画から,『MRP』に基づいて必要量を計算し,自動で発注されます. しかし,来月の必要量を発注するに当たって,今月末に,生産品番毎の残量がどれだけあるか不明ですので,毎回残量ゼロとして必要量を計算します.
さらに,仕入れ量が不足すると生産ができなくなりますが,正常な状態でも,設備の作動確認用,破壊試験用等に余分に納入させる必要があります.それ以外に不良品混在,加工不良時の追加生産等に使われる数量を予測して加える必要があります.更に,最小納入単位という契約があり,1,000個単位だったり,20kg単位だったりします.必要量が103kgでも,20kg袋が納入する単位で在れば,納入量は120kgとなります.
このようにして,PUSH生産,即ち計画生産に基づく発注 (MRP)は必要量より常に多めに発注する性質があります.PUSH型である限り毎月在庫は増えていきます.
一方PULL型 (在庫後補充方式)では,会社の調達品の在庫量は,ご家庭の冷蔵庫の管理と同じで,使って減った分だけ補充するので,最大在庫量は増えて行きません.
『Kanban方式』を採用すれば,在庫量は常に発行してある『kanbanの枚数』以下になります.そして,『Kanban』の枚数を減らせば,即Supplierの完成品倉庫と,自社のライン側までの在庫量を品番別に減らす事が容易にできます.
(2) 工場内の各工程の生産管理もPULL型 (Kanban方式)に変更
実際の工場では何十カ所の製造工程があり,それがサプライチェーンとして?がっていて,時々刻々夫々の製造工程に,『何をどれだけ,どのタイミングで作れ!』と指示するのは,不可能に近いことです.
これを解決するには『Kanban方式』の導入しかありません.
一例としてそれで,『甲』という工程から『乙』の工程へ,A,B,Cの3種類の中間製品を供給していたとします.「A」,「B」,「C」の3種類の連番を付けた『仕掛かりKanban』を準備し,通い箱に取り付けてスタートします.
後工程は「A」,「B」,「C」の3種類の連番を付けた『引取Kanban』を準備します.後工程から取りに来る頻度は,等間隔で10回/直が良いとされています.後工程は,生産によって使った部品の『引取Kanban』を持って前工程に取りに行き,前工程の在庫に掛けてある『仕掛Kanban』を外して『Kanban入れ』に入れ,引取Kanbanに付け替えて持ち帰ります.
前工程『甲』は,外れていた『仕掛Kanban』分を生産して,その『仕掛Kanban』付けて補充しておきます.
ここで大切なことは,全ての工程の材料置き場には品番毎に『引取Kanban』がついており,完成品置き場には品番毎の『仕掛Kanban』がついており,工場の中には一切『Kanban』のついてない通い箱入りの部品は無いということです.
工場内の全工程間をこのように『Kanban方式』で繋ぐ事によって,ただ『Kanban』の枚数を増減させる事で工程間の在庫量を自在に増減できるようになります.
さらに在庫を減らすためには,通い箱の中の収容数を減らして行きます.トヨタには『1個Kanban』という言葉があります.『1個流し』という言葉もあります.
究極の在庫低減は,作業者が,1個の材料を持って工程を回り,仕上げていく事で達成されます.
写真は初代MR2です.Midship-Engine, Rear-Drive, 2Sheater の略で,日本で初めてのミッドシップエンジン車でした.熱心な愛好家がいたため,月販数十台でも販売していました.普通の自動車会社では,量産しておいて,在庫を取り崩して販売するのですが,製造を担当してきたセントラル自動車は,溶接工程では一日1〜2台のボデーを,1枚ずつプレス品を運びながら溶接治具を廻って仕上げていきました.当時,『少人化』のモデル工程として,現場を担当する技術者として見学させてもらいました.
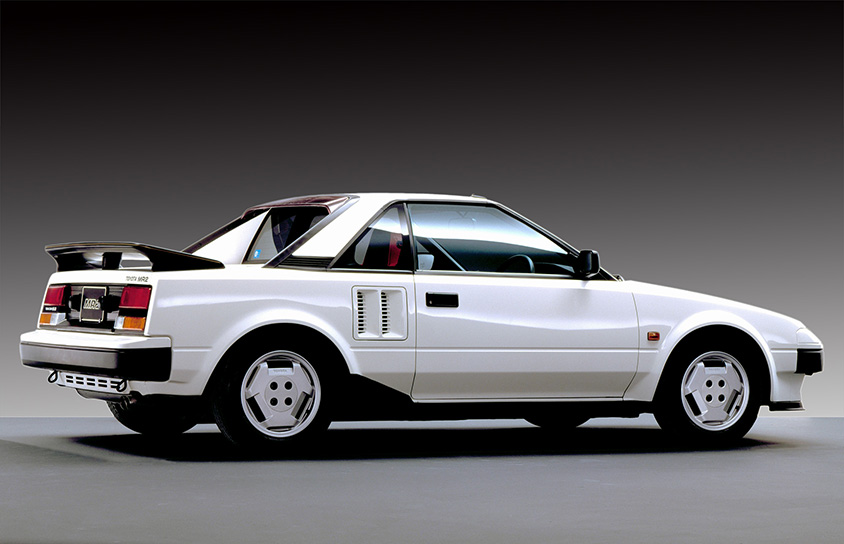
(3) 寄せる・停める改善
先に『少人化』の説明で生産数に比例して作業者数を減らすと説明しましたがここにも『トヨタ生産方式』としての工夫があります.
- 60個≧10人,54個≧9人,48個≧8人,42個≧7人,……
生産量が45個/hだったらどうするのでしょうか?
今月の生産個数が時間50個 (TACT-Time=60分/50個=72秒)だったとすればどのような体制で生産すればよいでしょうか.計算をすれば,54個から49個までは9人で生産が可能です.多くの会社では,9人の作業員に,作業を均等に割り振ると思います.
ここに大きな落とし穴があります.一時間に50個であれば1個当たり72秒.つまり,72秒に一個の割合で作ればいいということになります.一方この総作業時間は一時間に60個を10人で作っていましたので,1個10[分・人]で作れる事になります.9人なら67秒に1個作る実力があったわけです.
67秒に1個できる実力を持った現場を,72秒に1個作る体制にして置いたら,運動選手なら直ぐ解ると思いますが,その現場は,72秒に1個しかできない様に劣化して行ってしまいます.作業速さだけでなく,向上心や覇気も無くなってしまうのです.
トヨタ生産方式では,これを防ぐために『寄せる・停める改善』を行います.誰もがパソコンゲームに夢中になりますが,それは眼前の課題をいかに早くうまく対処できるかに挑戦しているからだと言えます.挑戦しているから,うまく行かないと悔しいと思うし,うまくいけばもっとうまくできないかを思い,時間の経つのも忘れていくことでしょう.
現場作業も同じです.自分の作業の速さに挑戦しているから,うまくいったら嬉しいし,うまくいかなかったら悔しいので,なぜだろうと考える.そしてまた挑戦する.仲間と一緒にやる場合は,どちらが早く終わるのかを競い合うことによって,楽しみが出てきます.そして共に挑戦することによって,働く面白さとプライドが生じてきます.そして生産性が上がり,自分たちの会社の基盤が強くなってきます.
〜Keywordはストレッチ目標〜
自分達の毎日挑戦する目標として,昨日までの実力に対して数パーセントのストレッチ目標を掲げる事にします.今の例で言えば,TACT-Timeは72秒ですから,60個作っていたときに作業時間で,先頭から2秒のストレッチ目標を与えて,74秒分ずつ要素作業を割り振っていきます.
そうすると,次のようになります.
8人のストレッチ目標に挑戦する作業員と,作業遅れをリリーフする1人の作業員と言う体制ができます.
こうすることによって,減産による生産個数の変更をしても,各作業員は実力を落とすことなく常にストレッチ目標に挑戦し,成長し続けることができるのです.
このことを『寄せる・停める改善』と言います.
これによって浮いた工数は,運搬頻度向上させるために使い,工程内の滞留在庫を減らします.
なおこの『寄せる・停める改善』は,拡大すれば製造工程にも適用できます.
大は組立ラインから,小は工作機械まで,早に挑戦するラインと,遅さに挑戦するラインを作り,要員・設備を浮かし,次の飛躍に備えるのです.
『人を減らすな!在庫を減らせ!』の意味は
1987年,トヨタも高級車を生産することになり,田原工場がそれを担当することになりました.そこで,工場長・工務部長・検査部次長・製造部次長 (筆者)が,本場ドイツ行ってその製造現場を視察することになりました.VW,Audi,BMW,Benz等の車両工場を主体に,しっかりと見学し,工場関係者と忌憚なく意見交換をしてきました.
余談になりますが,ドイツは非常に合理主義の国で,BenzとVWは,日本進出に当たって,日本の人口の重心に近いことから,豊橋市に揚げ港とMotor Poolを設置し,此処で再整備をして日本各地の販売店に卸しておりました.
特に,そのドアやフードの建付けは,全数再調整しないと高級車として売れないということで,トヨタの田原工場の手直し要員が高給で引っこ抜かれて行ったとされています.日本国内でご近所付き合いをしていた仲でもあったのです.
1980年代は,ドイツは約百年の歴史を誇り,トヨタは50年目の新参者でしたから,大先輩として若造に教えるような具合で,工場の隅々まで見せてくれて,何でも意見交換ができました.詳しい話はまたの機会に譲るとして,当時のドイツの自動車工業の一面を紹介いたします.
当時のドイツの大学進学率は数%で (現在は30%?),進学するためには,日本で言えば小学年生から高校3年までの進学校『ギムナジウム』に入ります.
数年間の社会 (含む兵役)経験を経た後,自らの将来像を決めて大学の専門課程に入学 (入学は易しいが学位論文は難しい)します。その専門を売りに入社すると『開発』や『経営・管理』の専門職として働きます.
大学進学しない人は,夫々の職業学校に入学し,手に職を付けます.職業学校を卒業すると,国家資格を手に入れた職人 (ゲゼーレ)になります.同時に同業組合に加入します.加入しますと組合の規約によってドイツ国内における標準賃金以上の金額で就職ができます.
就職しますと『同一労働同一賃金』の原則で,勤続年数には関係なく,ほぼ一定の賃金になります.目立った功績をあげると,賃金は上げると言います.
作業員の上に君臨するのは『マイスター』です.
Benzのシュツッツガルツ工場で,あるマイスターのオフィスを見学しました.そこには担当する工程の作業員の全名簿が貼り出されており,勤怠状況が詳しく記入されました.A君は成績優秀である.B君は不良ばかり出している.あと1回不良をだせばクビにする・・・等語ってくれました.
不良の原因追及や,作業指導,部下の育成等の話は出ず.失敗した作業者を排除して入れ替える……と言う『マイスター』の姿勢に,驚きました.
一方,万一クビになっても,ドイツの自動車会社の従業員は強力な労働組合『IG Metal (イーゲー・メタル; 金属産業労働組合)』に加盟しており,再教育・,再就職は容易であると言います.その気があればすぐに就職ができる仕組みになっていると聞きました.
さらに驚くべき労働市場の実態を知りました.自動車の組立工は,組合の認めた標準作業時間に基づいて作業量を決められ,基本となる給与も決められているということです.その作業というのは驚くべきことに,スパナやドライバーを使って手で締め付ける時間を以て標準作業時間と決められていました.
実際の職場でそのとおりに作業時間が割り振られているかどうか,同業種組合の調査員が来て見て周り,規定より多くの作業が割り振られているときは,会社側に厳重に抗議をする……仕組みとなっておりました.
その結果,当時のベンツの一番廉価版のモデルAの組立作業時間は約20時間と聞かされ,トヨタのクラウンが約5時間というと,組合の壁でどうしようもないと残念がっていました.ただ,一人一人の作業量が日本の1/4しか無いことで,完全自動化がやり易いのが取り柄だとも言っていました.
もう一言ベンツの連中は反論しました.製造する工数はトヨタには負けているけれど,販売するための工数はトヨタよりもはるかに少ないと…….
当時のベンツは大変な人気で,注文した米国人はベンツからの知らせを聞いてわざわざシュツッツガルツまで車を取りに出向き,ゲストハウスでワインを飲んでいると,あなたのクルマが間もなくライン・オフしますという案内が来て,参観通路で検査工程を通過するわがクルマを見届け,翌日以降その車でヨーロッパを旅してやがてアメリカに持ち帰る……という話が流布されていました.その場で,トヨタもいくつかそのようになりたいものだと思っていました.
(1990年代,田原工場でレクサスの生産開始時,工場として,案内用の電気自動車とゲストルームを準備しましたが,時期尚早で全社展開には至りませんでした)
話を元に戻しますと,当時のBenzの中では
- 設計 ≫⇒ 生産技術 ≫⇒ 製造現場
の序列が強く,設計は大卒でも多くが博士号を持つ超エリート,生産技術も同様のエリート集団だと言います.
『≫⇒』の記号は絶対の権限を持ち,後工程の発言を許さないことを意味します.
『設計』は約5〜6年掛けて,完璧な車両を設計し,設計図を作成します.
『生産技術』は1〜2年掛けて設計図を基に,工場設計し,設備配置,工程編成をします.
『製造現場』生産技術から,生産設備と製造工程表を受け取った製造現場は,人事部が用意した要員をマイスターが適材適所を配置しています.どの工程に,どの作業員を配置するかは,そして誰をクビにして入れ替えるかはマイスターの権限でした.
『西欧のレストランに皿洗いで就職すると,定年まで皿洗いをさせられる』という言葉があるように,ドイツの自動車の組立工場においても,タイヤを取り付ける人は,その会社にいる限りずっとタイヤを取り付け続ける事が普通で,多くの仕事をマスターさせようとすると,膨大な費用が発生すると考えるからです.
それゆえに,生産ライン立ち上がり当時に作った工程編成は,ベストな編成であると考え,その一部を全自動機に置き換える改善は進めますが,売れなくなったと 言って先に述べた『少人化 (Flexible 改善)』は考えず,数ヶ月分の在庫を積み上げた後,一定期間生産ラインを止め,作業員を解雇します.つまり体制は同じのままで,一定期間生産を停止することで,在庫量を調整するのです.それ故,その環境の下では,労務費は変動費として計上するのです.
そしてその裏には,クビ切られてもある一定の収入を確保できる社会保証制度と,再就職を助ける強力な労働組合があるわけです.
日本の労働環境の特異性 (民間製造業の例)
Benzの社内では,各機能が独立していて責任範囲が明確で,他部署からの干渉を許さない組織でしたが,1987年頃のトヨタの状況は,下図のようなっていました.
- 設計 ⇔ 生産技術 ⇔ 製造現場
『⇔』は,Concurrent・Engineering を表し,トヨタでは1970年カローラ2代目から始まり,全社的に展開していました.ドイツと違い,最終工程である組立現場の班長が設計部門に出向いて行き,開発中の試作車の分解組付けを行ない,作業性向上の提案をしてきました.
これはトヨタの中では,@生産性の向上,A新車開発に参画したというモラールの向上に寄与しました.そして後日,B整備性の良さから中古車価格が上昇し,それが新車販売力に貢献している事が明らかになりました.
日本では,大卒以上の入社者は,有名大学に入学し,有名企業に入社すれば一生楽ができると言う輩が多く,入試科目 (高校課程の一部分)のみを猛勉強し,大学入れば学生生活を謳歌し,ただ楽をするために一流企業に入った……と思われる新入社員を数多く見てきました.受け入れた以上戦力するために,その配属先が,猛特訓して一人前にして育てておだてました.業務を進めながら上司が部下達の人物を見分け,能力のある人間をしごき,後継者として社内で育成してきました.結果として『井の中の蛙的世間知らず』の経営者が多くなりました.
高卒入社については,商業高校は事務所に,工業高校は保全部署等の特技を生かせる職場に配属になり,そこで更に技術を身につけて行きました.
問題はいわゆる普通科の生徒たちです.高校では受験勉強が優先し,社会に出て即役に立つ技能は何一つ身につけていません.この生徒たちは,製造企業においては,現場作業員として採用されてきました.
各製造現場では,戦力として立派に働いてもらうために教育訓練を行ないましたが,それは決して世間一般に通用するものではなく,その会社の,その職場の必要とする仕事ができるようになればよい……というだけの社員教育もありました.
組合活動は活発ですが,それはドイツのように産業別ではなく,会社別の組合でしたから,一旦首になれば会社から離れてしまい,世界に通用する何の資格も無いままに放り出されてしまう状態になります.つまり[人員整理]と言っても,産業別組合の強い欧米諸国に比べて,会社単位の組合しか持たない日本においては,その意味するところは全く違うのです.
読者諸君も,この違いをよく噛み締めた上で,『○○会社は何千人の人員整理を』という記事の社会的なインパクトをよく理解していただく必要があります.
『トヨタ自動車が公言した』とすると物議を醸し出しますのでこの場は『筆者の独断で言うと』としておきますがトヨタが存在するその本質は『共存共栄』にあります.『共存共栄』とは,近江商人の三方良しに似ていますが
- 顧客の満足
- 取引先・地元・環境の満足
- 従業員の満足
- 株主の満足
- 経営者の満足
と考えております.
最近マスコミで,日産の経営状態が話題になり,数が多く,報酬も大きいのに大した働きをしてないとして叩かれていますが,彼らはもしかして,経営者の満足を一番にあげているのかもしれません.この辺のことは後日『TOYOTAとNISSANの歴史をJコスト論で斬る』シリーズでお伝えいたします.
問題は(3) 従業員の満足に在ります.
『労働は神から与えられた罰である』とする旧約聖書の記述を信じるのであれば,皿洗いと言う係に就いたA君が毎日毎日皿洗いのみを担当し,生涯を閉じたというのは,神の命に従ったことで,なんでもないことかもしれません.
しかし,知的好奇心の高い日本社会においては,明けても暮れても毎日同じことを同じルーチンで行うということは,大変な苦痛です.
ラーメン屋でも,いっぱい一杯心を込めてラーメンを作り,客の反応を見ながらさらに美味しくすることはできないか,もっと客に喜んでもらえないかと,知的好奇心を旺盛に働かし,仕事を続ける中に,生きがいがあるのではないでしょうか.
このもっと良いやり方があるのではないかという知的好奇心を満足させる行いをトヨタ生産方式は『KAIZEN』と言います.
製造現場では,工業製品ですので,一定の品質レベルを満足すれば,あとは速さの問題になります.知的好奇心を使って挑戦するのは『作業の速さ』になるのです.
例えば,A君が作業を10%速く完成させる方法を見つけたとします.他の仕事に応用して数%は速くなるとします.
A君の会社が『会社都合で従業員を解雇する場合はまず社長が辞任する』という会社であれば,彼はその案を堂々と皆の前に説明し,皆も仕事が速くできるようになること驚き感動し,A君を褒め称えることでしょう.
A君が,従業員を一人解雇すれば,原価改善に功績があったとして課長が評価される会社にいたとすれば,A君が提案すれば,その結果仲間の誰かが解雇される事に繋がります.つまり改善をすれば仲間が解雇される様な工場では,少しでも良くしていこうという好奇心や精進する心がなくなります.その代わり,どうやって楽をしよう.手抜きをしよう・・・という心が芽生えてきて,職場は静かに崩壊してきます.
みんなが生きがいを持って働き,共に成長することをよろこびあう会社にするためには,『会社都合で解雇はしない』事と『KAIZEN』は必須なのでした.
思わず長話になってしまいましたが,トランプ関税によって世界経済が,リーマンショックよりもひどい状態になるという説もある中で,御社の世界同時不況への備えは万全でしょうか,弊社のお勧めする『人を減らすな在庫を減らせ』がお役に立てれば幸いです.
[2] 先回の続き,日米貿易戦争とトヨタの対応
先回クリントン大統領時の第二次日米貿易戦争についてお話ししました.
米国の強い要望で,GMのキャバリエを『トヨタキャバリエ』として改装して日本全国のトヨタ店を通して発売しました.米車好きの所ジョージまで動員して大々的に宣伝しました.最後は半値以下の叩き売りまでしましたが,目標の5万台には遠く及ばず売れたのは2万数千台だったと言います.
今回は日本におけるトヨタとサプライヤーとの関係の編成についてお話をし,それが米国においてどのように展開されていたか,そしてそれが今回のトランプ関税についてどのような影響を及ぼすかについてお話したいと思います.
[2-1] 1995年阪神淡路大震災時の調達部品状況
1995年1月1日付で,筆者は物流管理部長を拝命しました.
トヨタの物流部門は,国内はもちろん世界の末端まで完成車を運ぶ『車両物流部』,補修用部品を国内・全世界の修理工場まで運ぶ『部品物流部』,国内の遠隔工場および海外の工場で生産するに必要な部品を運ぶ『KD物流部 後に生産部品物流部』,それらを統括し,改善を推進する部署として『物流管理部』の四部から成り立っていました.
着任から間もない1月17日阪神淡路大震災が起きました.現場からの報告を受け,生産担当副社長が生産の全面停止を決め,各部署にかねて決めてあったライン停止時の実施事項を遂行するように命じました.
そして,完成車と生産用部品を博多港⇔名古屋港⇔仙台港を結ぶ専用のRORO船が停止するので神戸港に救援物資を運ぶ申し出でをして,所定の事前申請がないので断られた件は前回お話しました.
工場再稼働に向けて細部を詰めていた時に,東北地方からの部品がトヨタに届かないことが分かりました.
災害を受けたのは阪神地区です.その影響でなぜ東北地方からの部品が欠品するのか?サプライチェーンの問題として,生産管理部・購買管理部が中心になって調査しました.その結果は以下のようなものでした.
ドルショック・石油ショックを乗り越え,1980年代日本経済はバブル期を迎え,人手不足で生産が追いつかない状況に入ってきました.1991年,田原第3工場でトヨタマジェスタが立ち上がったとき,トヨタのSupplierから,『これ以上は作れない!』と言う悲鳴が上がったと言います.
Supplierは一般には一次下請け (Tear1),その下に二次下請け (Tear2)更に (Tear3), (Tear4)まであるとされています.下に行くほどだんだん規模が小さくなってゆき,末端では,ちょっとした道具と人手で行うレベルまでブレイクダウンされ,農家の副業として行われて例もある程,当時は人手不足の中で生産が急拡大して行ったと言われています.
その結果,Tear1が九州だったのに,Tear3は東北に在った等の例が続出したのでした.
トヨタのサプライチェーンマネジメントは,突然の事故,労働争議等を対象に考えており,部品は必ず複社発注とし,品質と価格を公正に競わせ,成長を促してきましたが,それは,トヨタの組立工場は愛知県内に在るということを前提としていました.
1995年現在,トヨタの組立工場は@九州地区,A中部地区,B東北地区に分散しており,地震大国日本では,東・南海地震,関東直下型地震,東北沖地震,北海道地震,富士山噴火等々の大災害尾可能性があります.災害の時こそ自動車が活躍して復興に寄与しなければならないのに,その自動車生産がダウンしては話になりません.
この時,トヨタは日本を『九州地区』『中部地区』『東北地区』の3分割しどの地区に大災害が起きても,他の地区は生産が維持できるようするという大方針を掲げ,グループ一体となって取り組み始めました.
1997年アイシンのPバルブ事件
註 P (プロポーショニング)バルブとは,急ブレーキ時リヤタイヤがロックしないように圧力調整する配管用鍛造加工部品,乾電池ぐらいの大きさ1997年2月1日午前4時頃,アイシン刈谷工場で出火,4時間後鎮火.焼失したのは,トヨタの使用量の99%供給するPバルブ製造工程だった.即全トヨタの工場が停止ました.
アイシン本体は復旧工事を進めるとともに,図面を公開して機械加工メーカーに生産協力を依頼しました.Pバルブの製造を依頼されたメーカーの中で最速で届けたのは2月5日でした.即刻,自動車生産の再開ができました.
機械加工メーカーの協力によって極めて短時間で,所定の性能を示すPバルブを供給できたこと,消失した工作機械を,全力を挙げて製作し工場の復旧ができたこと.トヨタグループとしての稼働停止期間は5日間で収めたことは,トヨタグループの結束の堅さとして話題となりました.
危機回避の観点からのサプライチェーン改革を進めていましたが,言わば外様大名だけに『阪神淡路大地震』の再発防止を図ってきていて,譜代大名には抜かりがあったと,大反省をし,更に力を入れて,『三分割化』に力を入れていきました.
2011年 東日本大震災
3月11日午後被害日本を襲った大震災は,マグニチュード9,0という,観測史上最大級地震でした.その直後,沿岸部に巨大な津波が押し寄せ,多大な被害と多くの人命を失いました.さらにその津波は,原子力発電所冷却装置を壊し,メルトダウンと建物の爆発事故を起こし,多くの放射能を散らしてしまいました.
物流管理部長として,名古屋港は名古屋市の一角にあるのに,仙台港と仙台市がなぜあのように離れているのか疑問を持ち続けていた.大震災の一ヶ月後現地を訪れた時,仙台港は1階部分は津波の被害に遭っていましたが,建物は無事で2階以上は被害がありませんでした.そして仙台市は全く津波とは無縁でした.
関係者に聞くと,伊達政宗が大津波を経験し,海岸沿いに田畑を作るのを禁止,塩田のみを許可した.その痕跡が『塩』や『窯』『釜』の地名に残っていると言います.
しかもここから先は危険という石碑まであると言います.それ故,津波で家屋を流れた被害は,家屋の建設は行政機関許可が要りますから,行政の怠慢ゆえの人災である.と考えざるをえません.
原子力発電所の被害については,近くの女川原子力発電所が,津波を意識して高台に建てたことを考えると,危険を無視して建設費を安く収めた東京電力の経営者責任は免れないものと考えます.黙認した行政官庁も同罪と考えます.
話をもとに戻します.
トヨタ自動車は,震災発生直後,ルーチンに従い全ラインを停止して,現状の把握を実施したと言います.
これだけの大災害対しては,豊田章男社長さっそく現地に飛び,日本を襲った未曾有の災害に対しては,まず人命第一,社会活動の復旧,その次に営業活動に移るべきで,それを実現するために,現地で指揮をしたと聞いています.
そして東北復興のために,岩手県に加えて宮城県にもトヨタグループの工場を誘致して,意識的に『九州』『中部』『東北』の3大生産拠点構想を樹立し,新工場を建設しました.
TNGA (Toyota New Global Architecture)は,次世代の良いクルマづくりのための設計標準と考え,これによって車両の構成部品の標準化が進めば,部品の種類が減り,量産効果が出るという考えで進めていました.
が,東日本大震災の経験は,異常時におけるサプライチェーンの堅牢さをもたらす事を体感し,より実現への力が入ったのでした.
次回は,日本で災害の中で強化されてきたサプライチェーンマネジメントとTNGAによる部品の共通化,常にトヨタと共に進出し,トヨタよりシェアを伸ばす強力なSupplier群の働きによって,トランプ関税課の米国大陸の中で,トヨタがいかに有利な商売ができるのかを,説明します.ご期待下さい.
今月は,有名な会社が堂々と人員整理の話をする姿勢に腹が立ち,弊社のスローガン『人を減らすな在庫を減らせ』に紙量を使ってしまいましたので,『TOYOTAとNISSANの歴史をJコスト論で斬る』は今月もお休みします.ご容赦ください.
2025年5月21日
(株)Jコスト研究所 代表 田中正知
2025年4月
所長の季節の所信表明
4月も早,中旬を越しました.
皆様いかがお過ごしでしょうか.
弊社のある名古屋市緑区の扇川の土手は,住民のための遊歩道として整備されていますが,そこには樹齢30年の染井吉野の並木になっていて,絶好の花見場所でもあります.今年の満開はやや遅く,4月の第1週でした.今週は,近くにある街路樹の八重桜が満開です.
拙宅の庭には,春の味覚を伝える2種類の庭木があります.一つ目は苦心して育てようやく付き背丈前伸びた山椒.もう一つは『五加木』,これは米沢藩上杉鷹山で有名ですが,信州でも春先に食されており,実家から移植したものです.我が家ではこれらを食して春を実感する習わしでいます.今年も例年通り家族で食し,春を実感いたしました.
穏やかな身の回りから目を外にやると,地球規模の大混乱が渦巻いています.
『ロシアによるウクライナ侵攻』,『イスラエルによるパレスチナ攻撃』等に代表される武力衝突.異常気象に起因する食糧危機等々,枚挙に暇がありません.
しかしなんといっても我々の生活に直結する『トランプ関税』こそが一番の問題だと思います.
今月は,トランプ関税問題のうち,筆者が体験した『日米自動車戦争の歴史』をお伝えします.
有名な『孫子の兵法』には,
勝兵は 先ず勝ちて しかるのちに戦いを求め,
敗兵は 先ず戦いて しかるのちに勝ちを求もとむ.
というのがあります.
今回のトランプ関税は,高らかに関税額を歌い上げましたが,株価の下落や 国債の利回りの高騰を見て『朝礼暮改』をしています.孫子から見ますとこれは負け戦です.
日本側の関税交渉団の活躍で勝機を勝ち取ってもらいたいものです.
とは言うものの,いよいよ4月から輸入完成車に25%は4月3日から,輸入自動車部品には5月3日から課税される事になっています.各メーカーとも数カ月分の在庫を抱えていますので,市中の販売価格に変化が現れるのは,在庫が切れてからと言われています.輸入車がどのような価格で市中に出回るか注目です.
TOYOTA在籍中に日米自動車戦争を2回経験していますので,その概要と,それを通じって米国市場でTOYOTAはどのように進化していったのか概要を説明したうえで,今回のトランプ関税に如何に取り組むかをOBとして説明したいと思います.
(1) 第1次日米自動車戦争 1980年〜
- 1973年のオイルショック以降,燃費が良く,品質の高い日本の小型車がアメリカ市場で急速にシェアを拡大して行きました.
- 一方,アメリカの自動車メーカーは,大型で燃費の悪い車が中心であり,品質面でも日本のメーカーに劣るという状況でした.そのため,日本車の攻勢により,アメリカの自動車メーカーの販売台数は減少し,業績が悪化しました.
- アメリカの自動車産業の労働組合(全米自動車労働組合,UAW)や議会を中心に,日本からの自動車輸入の急増に対する不満が高まり,「雇用が奪われている」という声が強くなりました.
- 1980年共和党のレーガン大統領が就任
自由貿易を謳う共和党としては輸入制限を掛けるわけに行かないので,アメリカ政府は日本政府に対して自動車輸出の自主規制を強く求めるようになりました. - 日本の自主規制:
アメリカ政府の強い圧力に対し,日本政府は1981年5月,対米自動車輸出の自主規制措置を導入しました.当初は年間168万台を上限とするもので,その後数年間継続されました.高品質・低燃費の日本車は市中では引っ張りだこで,プレミア付きでの取引きが出るほどでした. - 米国政府の意向を汲んで,日本のHONDAはオハイオ州,NISSANもテネシー州に生産工場を進出させました.アメリカ国内での現地生産を本格化させ,貿易摩擦の緩和を図りました.
- TOYOTAは,GMとNUMMIという合弁会社を設立(1983年)しました.これは,『トヨタ生産方式』を学びたいというGMのスミス会長と,北米の自動車部品の『Supplierの実態と,物流業者の使い方』などを知りたいTOYOTAの豐田英二会長とが意気投合してできた会社でした.
GMから派遣されたNUMMI準備要員と親工場になる高岡工場で合宿し,高岡工場の現場管理資料を精査し英文化していきました.仲間内で育ててきたTOYOTAの現場管理Systemが,GM選りすぐりの優秀な人材と共に逐一英文化する中で,理路整然とした管理体制に再構築されて行ったのです.一番勉強になったのがTOYOTA自身だったと思います.その一つが『改善』という概念は『improvement』では表現できない,欧米にはない文化で『KAIZEN』とすべきだ,と米人に教わりました.1985年に本格稼働開始したこの工場の活躍ぶりは『NUMMIの奇蹟』とネットで検索できます.
話はわき道にそれますが,NUMMI自体は2010年GMの倒産とともに一旦解散しますが,同年テスラ社と業務提携し,此のNUMMI工場は言わば『居抜き』の形でテスラ社に譲渡されます.
『UAW』の影響下には在りますが,北米1番と言われた品質と生産性を持った活きた工場を,テスラは手に入れたのでした.従業員を温存すれば,素晴らしい工場になると誰もが思いましたし,初期のテスラの品質問題は耳にしません.
一方,中国等で,『家電メーカー製のEVが爆売れ』という報道が在りますが,かつてTOYOTAで各工場から人を集め新工場を立ち上げ,新型車ソアラを生産した経験を持つ筆者には,他業種から参入し,爆発的数量を販売しているというMakerの品質保証に疑問を抱いております.暴走・車両火災・再始動不能等々の事故が起きないことを祈るのみです. - 話を元に戻しますが,NUMMIで学んだことをベースに,TOYOTA自力でケンタッキー州にTMMK工場を建設し,同年カナダ オンタリオ州にTMMC工場を建設しました.1986年でした.これにより100万台/年の設備能力を確保したのでした.
日本の自動車メーカーがアメリカ国内で生産を始めることで,アメリカ国内での雇用創出にも貢献しましたが,同時にアメリカメーカーとの競争はより激化しました.GM・FORD ・CHRYSLERのいわゆるBIG3は,強力な労働組合『UAW』の抵抗,旧態依然とした企業風土に阻まれ,軽量化,低燃費化が進みませんでした.
1989年『The Machine That Change The World』発刊
1985年レーガン大統領は,『40年前に焼け野原した日本が,なぜ戦勝国の米国を凌ぐような自動車を作るに至ったのか調査せよ』とMIT(マサチュセッツ工大)の研究グループ『IMVP (International Moter Vehicle Program)』に命じたのでした.
1989年に調査結果が報告され,以下の(A)(B)(C)が日本の飛躍の元であるとされました.
- 米国Deming博士の提唱する『TQC』を真面目に展開している.
その一環として製造現場では『QCサークル活動』が盛んで,現場の作業員が,自分達の職場の課題を見つけ,自分達で改善していく中で,品質向上や生産性苦情を成し遂げるだけで無く,その活動の中に自分たちのやりがいを見つけている……. - 『TWI (Training Within Industry)』を米国から導入して活用している.
日本の製造業は此のTWI を使って優秀な工員を養成し,安価で高品質の商品を生産していたのでした.
註;『TWI (Training Within Industry) 米国で実施された,第二次世界大戦中の招集された工員に代わって動員された主婦などの未経験者を,一刻も早く一人前の工員として働いてもらえるように指導する現場監督者のための教育プログラム』 - MITの経済学者がつぶさに,NUMMI (GMとTOYOTAの合弁会社),日本側の親工場,高岡工場を徹底して調査した結果,驚くべき発見をしました.
全世界がBestと考えていたFord 氏やThrone氏が造り上げた大量生産方式とは全く異なったConceptの『トヨタ生産方式』で,Supplierを含めグループ全体が動いていることが発見されたのでした.
Essenceを紹介すれば,10個の部品から成り立つ工業製品を,10頁の会議資料に例えれば,それを100冊作るのに,『大量生産方式』では,先ず各頁100枚連続コピーし,全部揃ったところで10枚ずつセットして完成させます.『トヨタ生産方式』では1〜10頁分をコピー機に覚えさせ,1部ずつ印刷していく方法を採ります.紙が半分しか間に合わなくても,半分の資料が完成するのです.このようにギリギリの材料で,ギリギリのTimingでも,間に合った分だけの完成品ができる生産方式でした.
米国としての対応は
(A)のTQCについて
米国の現場はHispanicに代表されるように,米語を満足に話せない移民などが多く,日本のようなQCサークル活動は無理であるが,日本の管理者は『問題解決』は現場任せで,上司のご機嫌取りでゴルフ・カラオケ・麻雀に現を抜かせている現状を把握していて,この日本に勝つためには管理者・経営者を対象にした『経営品質』に焦点を絞り,『TQM (Total Quality Management)』と言う手法を編み出して,全米国に展開をした.更にそれを使って成果を上げた企業には『Malcolm Baldrige National Quality Award (マルコム・ボルドリッジ賞)』を国として授与する仕組みを作ったのです.
1990年以降,日本でもお馴染みの米国大企業が受賞しています.(GM・IBM・FedEx・AT&T・Texas Instruments ・Ritz-Carlton Hotel・Kodak・3M・Boeing Airlift・……)
この頃,東芝がLap Top型パソコン,次いでNote型パソコンを発売し,やがて『Windows 95』が普及し,これが米国のOfficeを劇的に変えました.事務処理が標準化され,電子化され,それが大型電算機のERPに繋がり,全社的統合Systemとして完成して行くのでした.
具体例を紹介しますと,1995年,アーカンソー州にある米国の巨大スーパー『ウォルマート・ストアーズ』の本社を訪問したとき,北米全店舗の約10万点の商品の今日一日の売れたDETAと仕入れたDATA等を,自前の衛星通信で本社が把握して,分析すると言います.
北米大陸が広いので,春は南から北へ登って行き,冬は北から南へ降りてきます.
従来の販売実績をもとにして,どこどこの店舗では明日はどの品がどのくらい売れるか.現在の在庫量がわかってますから,明日の午前中に何をどれだけ補充すればよいのか,計算できます.これに基づいてセンターデポから各店舗への配送計画ができ,最小の在庫で最大の効果を上げることができる…….ということでした.
会社としての商品の売れ残りは3%以下に抑えることができ,これがアメリカで一番安い店と言われる所以でもありました.
そのために,ありのままの市場の動向が必要で,販売イベントは一切やらず,『Everyday Low Price 』の方針を貫いているといいます.
『ウォルマートl』自体は日次運営体制になっていましたが,Supplierが週次でしか対応してくれないので,毎週需要予測をSupplierと協議して決め,売れ残りのロスはサプライヤーと折半するというルールで運用していると教えてくれました.
1995年当時最先端はそこまで進んでいたのでした.
一方,当時の日本では,戦後の復興時に先輩たちが自前で作り上げた各社各様の『経営管理体制』で1980年代までの急成長を成し遂げましたが,それを自社の『経営管理』が優れているからと勘違いして『Japan As No.1』の自己陶酔に掛かり,欧米の,事業のGlobal化に対応できる『経営管理System』を学ばずにいました.
1990年代に入ると,日本では,眼前に突然1/30の賃金で働く中国の巨大労働市場が開け,世界規模で見れば資本主義は共産主義勝ったということになり急遽グローバル経済が進んでいきます.全地球規模の市場競争が激しさを増し,経営管理体制の不備から日本がズルズルと遅れをとってしまいました.
(B)のTWIについて
各社は大戦中に実施していたため,米国政府は特に対策を取りませんでした.後日,次の『Lean生産方式』とセットにして一部企業で復活しました.
(C)経済学者と『トヨタ生産方式』との出会い
調査に当たったMITの経済学者達は,『トヨタ生産方式』のConceptに驚きました.しかし,その中には欧米の企業では受け入れにくい要素も多々ありました.そこで彼等は,現在の欧米企業が取り入れ磨きを掛ければTOYOTAに追い付き,追い越せる項目に限って編纂した,ガイド本を発行しました.それが『The Machine That Change The World』(1989年)でした.著者のウォマック博士は,自ら会社を発ち上げ,実践を通して実務編として『Lean Thinking』を上梓しました.これらの本は,米国大手製造会社のTOPに読まれ,特に『Just In Time』は各社に導入されていきました.GE社,ボーイング社などは有名です.
(2) 第2次日米自動車戦争 1993年〜
当時,GDP第一位の米国,第二位は日本でした.
クリントン大統領(民主党)時代に日米自動車摩擦(1993年〜1995年)が再燃しました.その背景として,1980年代後半から,アメリカの自動車産業は自ら痛みを伴う改革をしなかったため,日本の北米生産車に対しても,価格と品質で後れを取り,米国車は市場シェアを大きく失いました.
BIG3の経営陣は,自社の改革よりもロビー活動に力を入れ,日本の市場が閉鎖的であり,アメリカ製品の輸入を阻んでいるのが自動車貿易の不均衡のもとと主張しました.特に自動車分野において,アメリカは日本に対し,部品の輸入拡大やディーラー網の開放を求めました.
主な出来事
1993年
クリントン大統領は,日本に対し,自動車部品の輸入目標を設定するよう求めました.日本は,目標設定は市場原理に反するとして拒否しました.
1994年
日米包括経済協議が開始されましたが,自動車分野での合意は得られませんでした.
1995年
アメリカは,日本車の高級車(レクサス)に対する100%の関税を課すと発表しました.当時のレクサスの革シートは,テキサス産の牛革を使っていましたので,牛革の販売維持を名目にレクサス100%輸入課税の反対運動を起こしてくれました.
州民にとってはTOYOTAという名の『我がテキサスの会社』になっていたのでした.他社のように,減産になっても 業員はLay offせず,地域行事に積極的に参加することで,地域住民に受け容れられたのでした.
テキサス州民たちの反対運動がどれだけ利いたかわかりませんが,レクサスの100%関税な取りやめになりました.
アメリカの乗用車を日本で売る
その代わり,米国から一定額の部品を購入することと,米国車『シボレーキャバリエ』を日本仕様に改造し『トヨタキャバリエ』としてTOYOTAのディーラーで販売することで完成車の案件は収まりました.(1996年〜2000年)
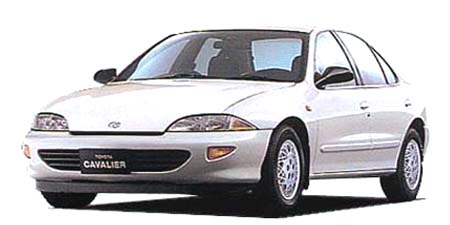
「キャバリエ」は,ゼネラルモーターズ(GM)の小型4ドアセダンである.スポーツカーと大衆車を中心とした銘柄のシボレー製で,初代は1982年に誕生した.
アメリカ車を日本でより多く販売するため,トヨタがGM車を売ることになり,1996年から,3代目のキャバリエの4ドアセダンと2ドアクーペを国内販売したのである.
キャバリエは,元気に走るクルマだった.しかし,エンジン騒音はそれなりに大きく,運転操作に対する走行感覚も荒々しい面があった.1989年に国内の自動車税制が改定になり,3ナンバー車への税額が排気量3.0リッター以下は軽減された.とはいえ,キャバリエ自体の質感で,3ナンバー車の税制や経費を自己負担するのは消費者にとってむずかしかった.
日米という二国間の経済的均衡を保つことは,クルマにおいてはむずかしく,今日なお解決されずにいる課題のひとつといえるだろう.なぜなら,アメリカ人にとって小さなクルマは興味の対象ではなく,逆に日本では大きすぎるクルマは手に余るからだ.さらに上級車種ならまだしも,廉価な実用車で大きいクルマは一部の関心しか得にくい.
CMをバンバン流し,販売店も頑張ったのですが,思うようには売れませんでした.今回のトランプUの場合は,どんな車を売れというのでしょうか……?
この辺りの苦労話は下記YouTube動画で詳しく説明されています.
アメリカ製自動車部品を日本の工場で使う
一定量買わされた米国産自動車用部品については,トヨタとしては重大な問題がありました.『トヨタ生産方式』では『自働化』という概念から,品質問題は工程内で全て解決し,工程を出たモノは全て合格品になるように工程設計します.言い換えると,万一不良品が発生しても,その工程内で対処し,合格品のみが次の工程に行くようにしてあります.
乗用車の組立ラインでは,1,500〜2,000点/台の部品を組み付けて完成車にします.各部品に0.1%の不良品が混在しても,完成車ベースでは合格車が1台も無いことになります.
ところが,当時のアメリカの経済学には『適性品質』と『過剰品質』という概念があり,不良率を0.1%⇒0.01%と下げていくと,製造コストが幾何級数的に増えてくるとし,上限でも3σ(0.3%)位の不良率がコストミニマムであるとされていました.
一方,TOYOTAの現場では,装置産業化されているので,初期設定で不良ゼロにすれば,以下同じ精度で製造できるので,不良率ゼロを追求することが,一番利益になると経験でも実証されていました.
いざ,米国から部品を輸入して見ると,本当に数パーセントの不良品が混じってました.このレベルでは到底トヨタのラインに直接投入できないので,一旦全数検査する工場に送り,そこから組み立て工場に搬入することにしました.
従来のトヨタのサプライヤーからの部品代に比べて,大変高いものになりました.
その後,全米にトヨタ生産方式(Lean生産方式)が行き渡るとともに,自動車業界では,やり取りする部品はあくまでも100%合格品が常識になりました.
以上が第1次・第2次日米自動車戦争の筆者から見たいきさつです.
1997年以降,更に数多くの工場を建設するなど,米国に溶け込むための施策を打っていますが,それは次回をお楽しみにして下さい.
報道機関では,歴史を遡らず,今日のことのみの情報をうわべのみ報道しているのが残念です.
この記事が皆さまの参考になれば幸いです.
尚,連載しています『TOYOTAとNISSANの歴史をJコスト論で斬る』は今回お休みを頂きました.
2025年4月21日
(株)Jコスト研究所 代表 田中正知
2025年3月
所長の季節のご挨拶
3月になり,日差しが暖かくなってきました.
目をやると,拙宅のさくらんぼが満開になっていました.
春が来た!という感じです.
ふと,高校時代に習った唐の詩人,劉希夷の漢詩を思い起こしました.
『年年歳歳花相似 歳歳年年人不同……』
人間世界はどうなっているか,
目を凝らすと,世の中は新しい方向に動いているようです.
今回はその中から次の2項目を取り上げ,所信を述べたいと思います.
先回予告しました『広域(流域)下水道の問題点』は,紙面の都合で来月お話しします.
(1) 初任給が30万円を超えた?
テレビでは,春闘は満額回答が多く,『物価を追い越す賃上げ』に沸いています.
大卒初任給は下図のように1990年頃から20万円が通り相場で,30年あまりのあいだ煙が漂うが如く一定でしたが,今年になって30万円台が続々と現れるようになりました.芝居の文句言えば『こいつは春から縁起がええわい』といったところですが,喜んでばかりはいられません.
停滞していた初任給が急に上がると言うことは,Paradigm Changeが起きたとみるべきです.従来の『年功序列型賃金制度』(勤続年数によって,悪く言えば『休まず・遅れず・仕事せず(敵を作らず)』のまま長居すれば,エスカレーター式に賃金が上がっていく方式)から,『職能給制度』または『職務給』(仕事振りによって昇格し,能力に見合ったまたは役職に見合った給与をもらう一方で,じっとしているだけでは昇給のチャンスはない……という方式)に移っていく事を暗示しています.
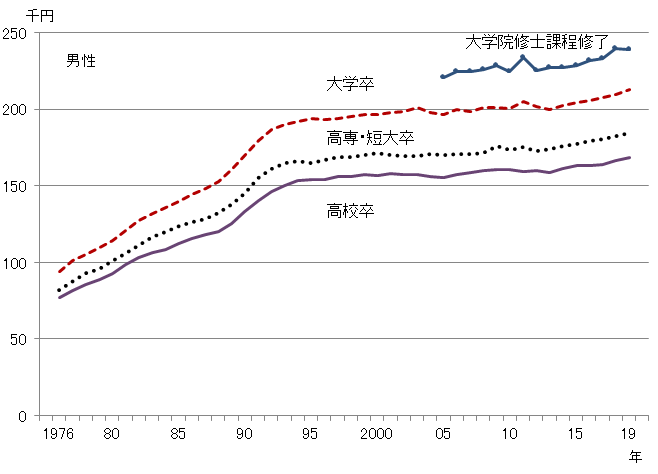
従来の『年功序列型』では,会社は,『大学卒=潜在能力のある人』と考え,現在の個々の能力と関係無く『人材』として一括して採用し,新入社員研修中に人事部が本人の潜在能力を見極め,会社都合で配属を決め,業務をさせながら,OJT教育をして,当時の第一戦で戦えるまでに育て上げていました.この頃は,大学進学率10〜20%しかなく,潜在能力の高い人が多かったこともあり,このやり方で戦後,1960年代から1980年代にかけて日本は驚異的な発展を遂げてきたのでした.
ご存知のように1990年から今日まで30余年間日本は長期低迷に瀕しております.この理由は,会社が闘う相手のレベルが格段に上がった事があり,従来の方式が通用し無くなったことにあります.
1990年代,ある著名な経済学者が,『1980年代までの企業間競争は,スポーツ競技で言ってみれば県大会のレベルであったが,グローバル化された1990年代以降のビジネスの世界はTOP数社のみが覇権を握って商売できると言う,オリンピック大会のような厳しい競争の世界になってしまっていて,メダルを取れなかった企業は退場するしかない厳しい競争になった……』まさにその通りです.
今年は,メジャーリーグの開幕戦が日本で行われることで盛り上がっていますが,その『野球』を例にとれば,どの球団も『年功序列型』のように,『野球の履歴』を問わず新入社員として広く公募して採用しておいて,その中から選手を育てることはしていません.
選手になりたい子供は,小学時代から野球に勤しみ,全身全霊で野球に打ち込み,高校もしくは大学で優秀な成績を修めます.その実力を評価してPro野球球団に採用しています.
ここ10年ほど筆者は中国でコンサル業をしてきましたが,改善の窓口になってくれた部長の経歴を訊くと,大学では名のある先生に師事して学び,学位論文を持って狙いをつけた会社に入社,そこで実績を積むと,次の会社に転職,これを数回繰り返して今の会社の部長職をやっているとか…,複数の会社で様々な体験をしているので,彼等はまさにプロでした.英語はペラペラで,英語を使って世界情勢を把握していますし,ネット上で大変な数の私的な知人を持っていて,そのネットから市場の裏事情を知り,転職の機会を得ている様子でした.
その会社の事務所の壁には個人名が張り出され,週単位の成果が記入されていました.まさに『常在戦場』の厳しい毎日と理解できます.
彼等の通勤に使っているのは,アウディのSUVでサンルーフ付きでした.日本ではおよそ一千万円余します.どれ位の給料をもらっているか想像がつくと思います.
その一方で,その意欲のない人たちは,一生平社員として雑務をこなしています.
そして,毎年,AIを搭載した事務機器が次々と発表されており,凡庸なサラリーマンの居場所は,事務所の中には年々なくなる…というのが,筆者が中国で改革の指導をしていた一流企業の『職能給』の姿でした.
初任給30万円突破という事は,この職能給の世界が日本にも押し寄せてきている…という事です.
『職能給』の世界では,『昔一流大学を出た』は意味が無く『何の資格を持ち,今どんな仕事ができるのか』が問われる時代になったと言う事です.
言い換えれば,お金がありガツガツ稼ぐ必要のない人は,教養を深め,心豊かに生きるために,卒業しても何の資格も得られない『文学部』や『経済学部』に行くのも良いでしょう.ガツガツ稼ぐ必要があれば,専門学校に行き,資格を取って海外で稼ぐのも良いでしょう.因みに,筆者が入試に失敗したらなろうとした『寿司職人』は,今,海外では即月収70万円は固いそうです.
身内に受験生をお持ちの皆さま,先月『豊田佐吉』のお話しの中で,『目的は何か』についてお話ししましたが,『大学進学の目的は何か』に受験生とともにお話しする事をお薦め致します.
(2) 米大統領トランプUがとんでもないことを始めた
先月このコラムで,『心配していました『トランプU』は,大統領選で称えた公約の手前,関税を発表しましたが,具体的には実害を最小限に留める内容のようです.『石破vsトランプ会談』も実現しました.少し安堵しています.』と書きましたが,これは筆者の早とちりでした.
なんと3月になると,カナダ,メキシコ,EUに対し25%の輸入関税を課したのでした.『メキシコの反応は・・・』Copilot(AI)に尋ねると以下の回答がありました.
- 報復関税の導入; メキシコは,アメリカからの輸入品に対して報復関税を課すことを発表しました.これにより,アメリカの関税政策に対抗しつつ,自国の経済を守る姿勢を示しています.
- 対話の継続 ; メキシコ政府は,アメリカとの対話を重視し,関税問題の解決を目指しています.特に,両国間の協力を強調し,貿易摩擦を最小限に抑える努力を続けています.
- 国内政策の強化; メキシコは,麻薬密輸や組織犯罪への取り締まりを強化し,アメリカ側の懸念に対応することで,関税回避の可能性を模索しています.
- 経済的影響の緩和策; メキシコ国内の企業や産業に対して,関税の影響を緩和するための支援策を検討しています.これには,サプライチェーンの調整や生産拠点の見直しが含まれます.
メキシコの対応は,冷静さと戦略性を兼ね備えたものとなっており,国際的な協力と自国の利益を両立させることを目指しています.どの側面についてさらに詳しく知りたいですか? それとも別の話題に移りますか?
Copilotはまだまだ使い物にはなりそうもありません.
肝心な報復処置の一部が抜けていました.それは,メキシコが逆に『自動車部品の輸出を停止する』という事です.米国内の工場で生産している自動車は,売値3万ドルの自動車であれば,Supplierからの購入部品は2万ドル近いと言いますが,全世界の自動車産業は今や『Just In Time』調達になって居てSupply・Chain上に余分な在庫は持っていません.米国の自動車工場も例外ではないのです.
最近日本で自動車用ばねメーカーの『中央発條』で爆発事故が起きたため,トヨタとスズキの組立ラインがある期間停まったニュースがありました.このように,Keyとなる部品が1点でも欠品になれば自動車の組立ラインは停めざるを得ないのです.
メキシコ政府は悪知恵を働かせ,国内法に基づいて,自国の保安部品の工程監査を名目でSupplier工場の生産を止めて監査していけば,その部品が例え1ドルでも代替え部品が無ければ,その部品を使うアメリカの組立ラインが停まり,1台3万ドルの自動車が生産できなくなるのです.どうやらメキシコ政府はこの事をワシントンにちらつかせている様子です.これは,自動車会社には堪えます.
カナダは,もっと激しい反応を起こしています.『カナダは米国の51番目の州になるべき』と言う発言がカナダ国民を『反米』に駆り立て,米国製品のボイコットを始め,米国観光まで減少させました.米国で使う石油・ウラン・肥料に輸出関税を掛け,場合によっては供給停止もちらつかせています.決め手は,
- 米国のニューヨーク州・ミネソタ州・ミシガン州の家庭と企業はカナダの電力に依存しているといい,25%の上乗せ料金を課し,場合によっては供給停止もありうる.
- 米国本土とアラスカ州への物流はカナダ国内の陸路を経由していて,カナダがアラスカの首根っこを握っている状態です.今は通行税増額をちらつかせています.
トランプ大統領は,ウクライナのゼレンスキー大統領を和平交渉の席に着かせるために,Dealとして『軍事情報の遮断』と『武器援助を即刻』停止しました.
トランプがカナダのTopであればDealとして『電力遮断』や『道路封鎖』もあり得ます.と言う事は,追い詰められればカナダの新首相もやりかねず,一触即発の緊張状態が今現在カナダ政府VSワシントンの両国の関税問題の状況になっています.
そして,テスラ株は暴落し,米国株は下落しつつあります.
EUとの駆け引きは省略しますが,トランプが仕掛けた関税戦争を白紙撤回しない限り,全世界はリーマンShock以上の大不況がくると専門家は警鐘を鳴らしています.
筆者が言いたいことは,以下の二件です.
-
1971年に『ニクソンショック』として有名ですが,米ドルが兌換機能を停止し,以来1ドル=360円の固定相場制が崩れ,変動相場制になりました.
今回の『トランプショック』は輸入関税を25%上げると言う暴力?で,相手を脅し,譲歩を引き出そうというモノです.
今回トランプ大統領が仕掛けた関税戦争は,リーマンショック級の悪影響を全世界に及ぼすと言われています.御社はその準備があるでしょうか.日本への自動車の輸入関税は……?その他の産品に関する関税は……
それに対する御社の備えはいかがでしょうか?
-
3月1日の米国トランプ大統領の突然の25%の輸入関税宣言に対して,メキシコでは2024年10月初の女性大統領として当選したシェインバウム氏が早急に国内世論をまとめ,対抗策を決定し,毅然とした態度でトランプ大統領に対峙したことです.この行いに対して,国民の86%の圧倒的支持を得たと言います.
一方のカナダは,当選したばかりのカーニー新首相が国内世論をまとめ上げ,毅然とした対応策を数日でまとめ上げ,トランプに迫った.同時に,EUと連携を取り,互いの交易により対米依存度を減らす協議を開始したという.
一国のTopとしてLeader-Shipに感服する次第である.
そこで我が国のLeaderに目をやると,関税戦争はどこへやら,10万円の商品券で大もめに揉めている次第.我が国を支えている乗用車の対米輸出に25%の関税を言い出されたらどうするのか,どんな影響があるのか……??
国会もマスコミもただ見守って居るだけに見えます.
万一に備えて事前に国内法を整備する必要があるのに……
静かな事が返って恐ろしいと思って居ます.
どうか日本政府も,密かに準備室を設けて水面下で策を練り,交渉を重ねていて,万一,米国トランプUから関税の宣言が出たら直ちに,カナダやメキシコに劣らぬ,毅然とした回答をし,行動を起こして頂きたいと念じています.
日本国の存亡が掛かっていますから…….
〜以上〜
2025年3月吉日
(株)Jコスト研究所 代表 田中正知
2025年2月
所長の季節のご挨拶
心配していました『トランプU』は,大統領選で称えた公約の手前,関税を発表しましたが,具体的には実害を最小限に留める内容のようです.『石破vsトランプ会談』も実現しました.少し安堵しています.
この冬一番の寒波が来てる中,その寒さの中で昨日,拙宅の小さな菜園で『菜花』が見つかりました.
青菜は日照時間の変化を読み,菜の花の開花の準備を始めています.この開花に合わせて蝶が蛹から羽化して現れ,花の蜜を吸いながら受粉を助け,葉っぱに卵を産み付けます.産み付けられた卵は孵化して青虫になり次の植物の葉っぱを食べて成長し蛹を経て蝶になることを,春から秋にかけて4〜5回繰り返して蛹で越冬します.一方菜の花は受粉出来たお陰で菜種を実らせ,地中に蒔いて生涯を終えます.
誰が仕組んだかは知りませんが,寿命が1年未満のこの蝶と青菜の2種類の生命体の織りなす現象は,毎年毎年正確に繰り返され,実にめでたいことです.
人間世界では,1月28日に埼玉県八潮市で道路が陥没し,そこにトラックが落下した事故が起きました.関係部署の懸命な努力にもかかわらず,未だに運転席の救出ができずにいます.マスコミではそれを毎日放送していますが,『何故このような事故が起きたのか』『諸外国ではこのようなことは起きているのか』『再発を防ぐにはどうすべきか』と言った建設的な……行政を見直すような報道はなく,『大変だ』『可哀想』『住民の困惑』のみを伝えております.これでは文字通り『埒が開きません』.
4半世紀前になりますが,現役の管理職であった頃は,様々な体験をしてきました.TOYOTAの社内では,問題が発見されると必ず『何故・ナゼ・なぜ・Why……』と,その原因を遡り『真因』を徹底的に追求し,その『真因』に対して再発を防ぐための『本対策』考え,実施しておりました.
通常『本対策』は時間が掛かるので,実現するまでの間は,『暫定対策』を行います.
現場に任せ切りにすると,忙しい現場は日常業務に追われ,『暫定対策のレベルでも良いのではないか……』と易きに移り,多くの場合本対策には届きません.そうしている内に『再発』させてしまうのが常です.責任者が強い意志を持って『決めたことを成し遂げていく事』が大事なのです.責任者というのはそのためにいるのです.
よく『安全第一』とか『品質第一』と言われますが,『安全』と『品質』は数値化が難しいので,具体的なレベルは経営Topが決めなければいけない」という意味が込められています.
付け加えますと,決めただけでは駄目で,『安全』と『品質』の具体的レベルは,トップ自らがある頻度で確認する必要があります.業務監査という行事はその一つです.
因みに今のTOYOTAの車両品質は,章男会長が自ら『マスタードライバー』の任に就き,自社の試作車を自ら運転し,品質と安全を確認して『GO!』サインを出し,時には抜き取り検査的に自社製品に乗っている……と言います.それ故,普段はレクサスやクラウンのような高級車に乗っていては評価の軸が崩れるとして,他社製の軽四や大衆車にも乗って,今の市場の動向を掴んだ上で,自社製品を評価していると聞いています.TOYOTAの哲学『現地現物』の極みと言えます.
このような『トヨタ流ものの見方・考え方』から今回の道路陥没事故を,『そもそも論』から考えて見ましょう.
各家庭には一般的には下記のように8種類のライフラインが接続されています.
- *電線 (100V,200V)
- *通信線 (光ファイバー)
- ガス管 (燃料用都市ガス,プロパンガス)
- 上水道管 (飲料水)
- 下水道管 (生活排水,汚水)
- 雨水管 (雨水)
- *電話線 (銅線)
- *その他 (ケーブルテレビ等)
各々の所轄官庁が違うこともあり,各ライフラインが個別に国交省管轄の道路に許可を受け,各々が勝手に埋設しています.
*印は電柱等を経て空中で分配している場合が多いのですが,10年前まで住んでいた駒込駅付近では写真のようになっていました.
![]() |
![]() |
右側の写真は,電線・電話線・光ファイバー線が入り乱れて居る状況の例,家が建ったり,新規設備を導入したりするたびに請け負った業者がそれぞれの方法で配線したために,このような複雑な形になってるのだと思います.
もし地震で電柱が倒れたら,どのような手順でどのように配線していったらいいのか誰も説明できない状態になっているのだと思われます.
左側の写真は,民家の頭上に6,600Vの高圧送電線と,110V家庭用送電線が張り巡らされていて,細い電柱の上の大きな変圧器で6,600Vから110Vに降圧している状態を撮影したものです.
地震で電柱が倒れて民家の上に覆いかぶさると,この変圧器が民家に落下することになります.変圧器の重さと6,600Vの送電線が,住民の上に覆い被さりますから,タダで済むはずがありません.想像するだけで恐ろしくなります.
それで私は10年前名古屋市の丘陵地帯の現住所に引っ越しました.
これらライフラインは,諸外国ではどうなっているのでしょうか?
米国,西洋諸国には電柱が無いのは常識です.中国は北京・上海は大都会だから電柱は無いと予想できますが,地方都市はどうかとお思いでしょう?
次の写真は,2024年6月の河南省新郷市の風景です.写真に写っている2輪車,3輪車,小型の4輪車は,ポンコツ再生の鉛バッテリー式のEVです.いわゆるゴルフカートで,安くて通勤用には便利なので,都市交通の庶民の足になって居ます.
中国のEVの躍進が話題になっていますが,その原点は,これらのゴルフカートまがいの小型車にあると思います.
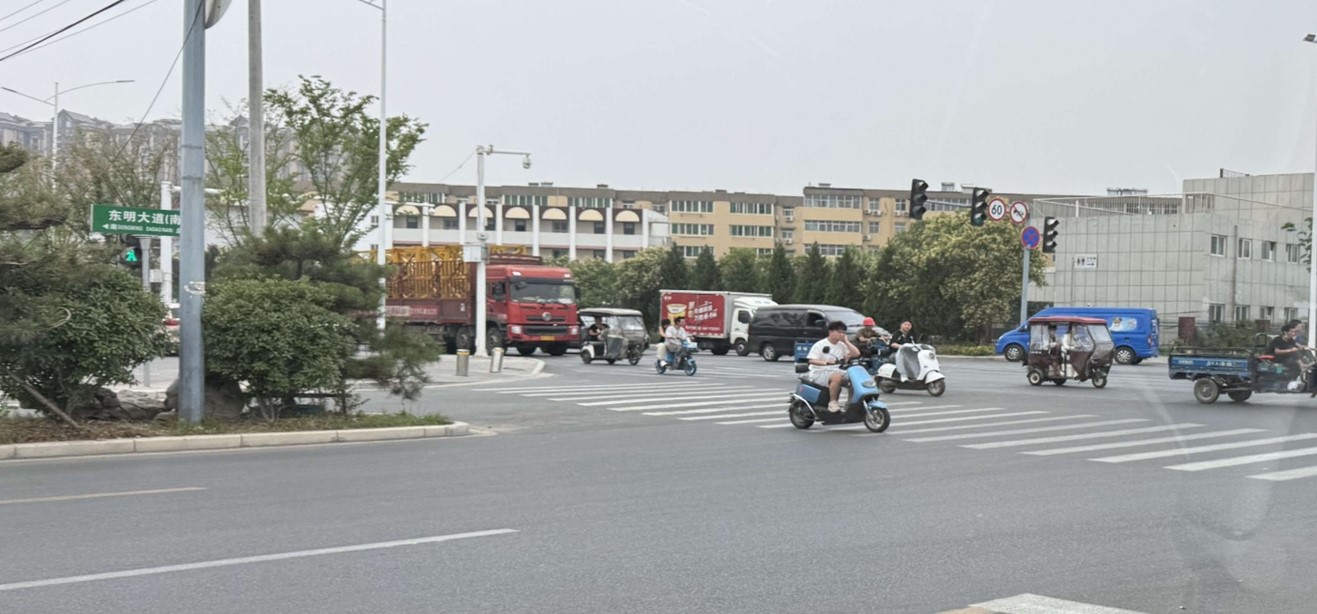
話を道路に戻しますと,車はゴミゴミしていますが,道路はすっきりしています.電柱は一切ありません.道路環境は欧米先進国と同じです.東京とは違います.
下図は横浜市のHPからの引用ですが,左が現状の電柱と『個別地中埋設型』のライフラインを,右側は道路に大きなトンネル『共同溝』を設け,その中に各ライフライン(1)〜(8)を整然と並べ,常時点検と修理できるようにしたものです.
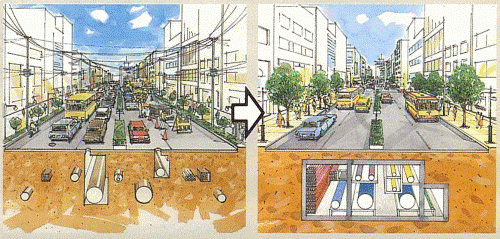
共同溝には,道路両側の雨水溝を大きくして活用するタイプもあり,現場の状況によって様々なバリエーションがあるようです.
従来の『個別埋設方式』は,3月末日の年度末にあわせて,個別のライフラインが点検周期毎に道路を掘り返し,埋め戻しております.(1)〜(8)のライフラインは監督官庁が違うので協力体制が組みにくく,共同溝方式が望ましいことは分かっていても,船頭が多くて未だ一部地域しか実現してないようです.
毎年,『国土強靱化予算』が総額で5兆円ほど計上されています.てっきりライフラインの共同溝化が大きな柱になっていると思いましたが,調べてみますと,議員さんが地元の要求で勝ち取る予算のことのようで,肝心のライフラインの共同溝化は入っていませんでした.
東南海地震,首都直下型地震等々が迫ってきているという中で,今年もあちこちの道路を掘り起こし,ライフラインの点検修理を行っています.平均寿命が80歳を超えた日本の社会で,菜の花と蝶のように毎年同じ事の繰り返しでは能がありません.日本も諸外国のように,ライフラインの共同溝化に向けて歩み出すときと思います.
マスコミは,本来の『ジャーナリズム魂』を呼び起こし,道路陥没事故を,『日本国の国土強靱化のメインテーマの一つ』として取り上げ,国家として何時までに,何処まで共同溝化していくか』をフォローしてほしいものです.
2024年度の訪日観光客は3千万人を超えるとか……と言う事は,林立する電柱と,蜘蛛の巣のような電線,毎年掘り起こす道路を,珍しい景色として彼等に自慢して見せるのか,恥ずかしいこととして一刻も早く直すのか,その決断を世界が見ていると考えなければなりません.
次回は,バブル時代に論争になった『浄化槽方式』と『広域下水同方式』の違いを『本流トヨタ方式』で論じます.
最後に,不明になっている運転席の一刻も早い回収を念じております.
2025年2月吉日
(株)Jコスト研究所 代表 田中正知