連載コラム『Jコスト改革の考え方』目次
JBpress連載コラム『本流トヨタ方式』
ビジネス情報サイトJBpressにおいて、2008年から2013年までの間に合計104回のコラム 『本流トヨタ方式』 を連載していました。
現在連載中のコラム 『Jコスト改革の考え方』と併せて読んで頂くと、より深くJコストの考え方がご理解頂けるかと思います。是非、下記のリンクにアクセスしてみて下さい。
過去の所信表明
2022年4月
季節のご挨拶
昨年末から急速に増えたオミクロン株は減り始め,3月22日には蔓延防止法の適用が全国的に解除されました.
いよいよ桜の開花とともにアフターコロナに向けてアクセル全開,という矢先にロシアによるウクライナ侵攻が始まりました.
武力をもって他国の領土に攻め込むなどとは言語道断と,西側諸国は経済封鎖に踏み切りました.この経済封鎖によって半年も経てばロシア経済はガタガタになり,戦争遂行は不可能になると報じられていますが,規制する側にもエネルギーや鉱物資源が市場から減ることによって成長が鈍化し,物価が急上昇するとされています.
このように世界中の企業は今,
- コロナからの復帰と,
- ノンカーボン化に加え,
- ロシア経済制裁による世界市場の激変
に対応すべく,2022年は大変革を迫られています.
その中にあって日本はどうすべきか……今から30年前,バブル崩壊前の日本の企業であれば,欧米諸国に負けないように頑張りましょう!でことは済んだと思いますが,コロナ対応で明らかになってきたように,1990年以降の日本経済・社会はズルズルと世界の趨勢から置いてきぼりにされ,かつては『危機の円買い』とも言われていましたが,今回のウクライナ危機に関しては,逆に円が売られ,ズルズルと安くなって来ていて,不気味です.
バブル崩壊の1990年はソ連崩壊の年でもありました.ソ連は解体され15カ国の共和国に分かれ,計画経済から市場経済に大変換しました.日本の明治維新に相当するほどの変化であったと想像できます.その中の優等生は,バルト三国の北の端の人口130万人の小国エストニアで,いち早く電子立国を目指し,行政改革を断行して電子化し,サーバーを海外の数か所に分散して持ち,NATOに加盟した上で,海外のIT企業を誘致し,『昔シリコンバレー今エストニア』と言われる程になったと言います.
大きくて豊かだったウクライナは,地方豪族の内輪もめと汚職が蔓延しているところロシアに攻め込まれ,クリミア半島を失いました.そこで目を覚まし,エストニアを見習って電子立国を目指して改革を進めて行きました.そしてNATO加盟も目指したところ,プーチンの逆鱗に触れ,それが今のロシアの侵攻に繋がったとされています.
ウクライナのデジタル担当大臣が,イーロンマスク氏が準備していた衛星通信サービスを使わして欲しい頼み込み,3月10日にトラックいっぱいの通信機と蓄電池が届けられ,ロシアによって破壊された中で唯一の生き残った通信網として大活躍しているという話も伝わってきています.
今まで見ることができなかった戦争の惨状が,これを通じて全世界に伝わり,世界の世論を動かしているということを知りました.
3日で陥落するとみられていたウクライナが,しぶとく抵抗し,一部で反転攻勢に出ているのは,電子立国を目指して整備されたインフラが,たとえ建物が爆破されても,機能していて,ウクライナ全土でスクラムを組んで頑強に抵抗しているのだと推察されます.
振り返って我々の国,日本を見たとき,他国の侵攻だけで無く,首都直下型地震,東南海地震による津波,富士山の噴火等,30年以内に高い確率で起きることが予言されています.ウクライナの惨状を見ながらも,明日は我が身と思って,個人としても,国家としても,身の回りを見直し,備えていく必要があると痛感しました.
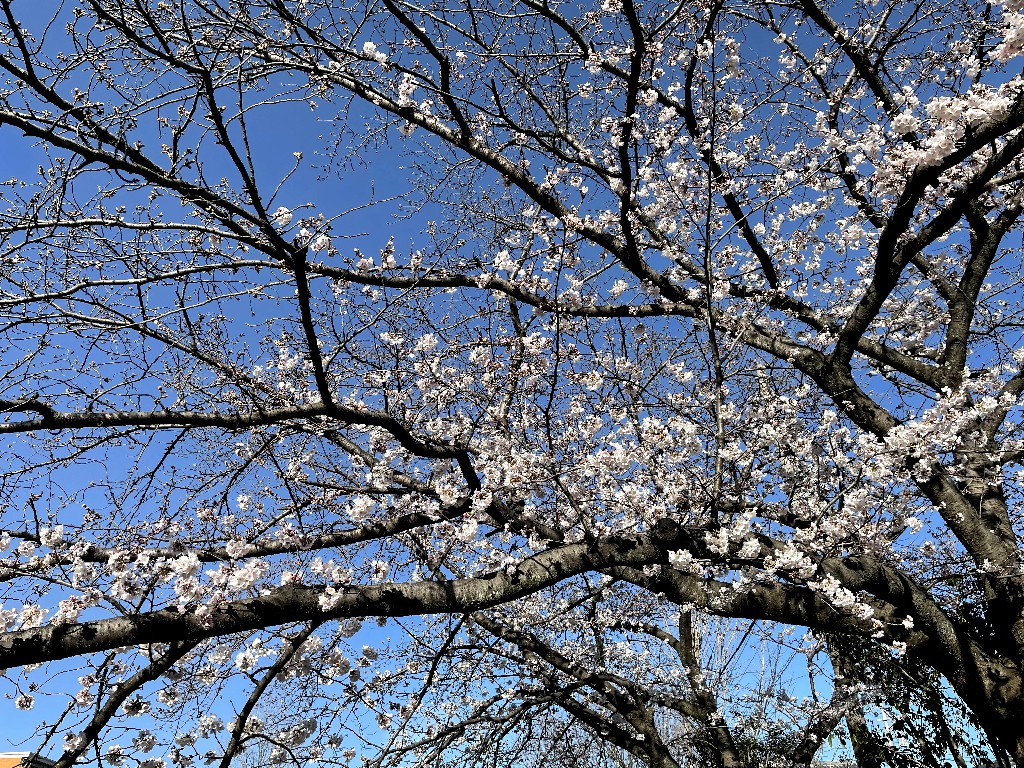
窓の外に目をやれば,のどかな日差しの下で桜が満開です.物事をスタートする4月がきました.諸官庁は年度変わりですし,民間会社の多くは期の始めです.千里の道も一歩からと申します.気持ちを新たにして業務に取り組み『危機』を『飛躍の機会』に変えるご活躍を期待しております.
若い世代にとってみれば4月といえば入学式であり,入社式であると思います.そこで以下のようなテーマで数回に亘ってお話ししたいと思います.
大学と大学校はどう違うのか
目次
次回の目次
- [3] 日本と正反対のドイツの大学
- [4] ここまでの仮説で自分自身の生涯を振り返ると
- [5] 焼け跡から奇跡的復興の日本がこの30年間,なぜ取り残されたか?
- [6] 今後どうすべきか
[0] はじめに
事の始まりは,本コラムで紹介している『Jコスト論』が何故拡がらないのか?という疑問からでした.
『Jコスト論』をお話しすれば誰もが納得してくれます.今のやり方は時間概念が抜けて居ると賛同してくれます.
でも,これを自社に展開しようとする人はなかなか現われませんでした.現れたとしても展開して行く途中で頑強な抵抗に遭います.
ところが先々回からこのコラムで御紹介しましたように,2019年,自ら進んで『Jコスト論』を展開したいと申し出る会社が中国に現れました.実際の現地指導はコロナ禍のために四ヶ月で中断しましたが,連絡が途絶えた後も自力で展開していき,1年間で見事な成果を上げました.そのやり方も今までにないもので,総経理が先頭に立ち,経理部が事務局になり,『社内業務の進め方改革』から『社内教育資料』までの改革を進めたのでした.
振り返れば,『Jコスト論』の論文発表は2003年.2005年から始まった東大MMRCインストラクタースクールでは『ものづくり会計学』として講義し,2009年『トヨタ式カイゼンの会計学』上梓(1万部余販売)しています.出版と共に講演依頼も来て,毎年20回程講演して廻りました.
縁あって5社ほど導入に取り組みましたが工場敷地内の改革に終わりました.もっとも大々的に取り組んだのが2015年からのK社で,かなりの成果を上げましたが,経理部門は参加せず工場改革の規模となっています.
中国では,2015年に『トヨタ式カイゼンの会計学』中国語版出版を機に現地コンサルタントと契約し,多くは講演会でしたが,5社の改革の手伝いをしました.著書出版から数えて日本では10年経っても現れなかったのに,なぜ中国では,3年目に,総経理が手をあげて導入を求める会社が現れたのか?これが疑問でした.
広く世界に目を転じると,2020年のはじめから全世界にコロナパンデミックが始まり,各国の政府が『コロナ対策』という同じ問題に同時に対峙し,その対応と結果には,大きな差が白日のもとに晒されることになりました.全世界の行政が共通一次試験を受けて,その結果が発表されたようなものでした.75年前まで同じ国だった韓国と台湾は,IT技術を駆使して日本よりも遙か先を走っていました.韓国は民度の違いか?ここ数か月は日本より多い感染者を出していますが,台湾は依然としてトップランナーを維持しています.欧米諸国では,日本に比べて桁違いの感染者数を出しましたが,政府の対応策は理路整然としていて,理系の私には納得できるものでした.
一方で,日本の官僚機構は太平洋戦争直後の混乱からの奇跡的な回復成し遂げたとして高い評価でしたが,今回のコロナ禍では『アベノマスク』で代表される体たらく,例えばPCR検査の母数を数えず,陽性者数のみまちまちの時間にFaxで送り,そのFaxの山を暇な時に手入力で集計し,本日の感染者数として発表,それをベースに政策立案をしていました.すべてが出たとこ勝負,行き当たりばったり……に見えていました.
トヨタ式の『何故・なぜ・ナゼ…』を繰り返して行きますと,本来大学で学ぶべき『未知なるものへの取り組み方』,『科学的アプローチ』が,日本社会から抜け落ちているという疑いが出てきました.
これを突き詰めて,私なりに立てた仮説が今回のテーマなのです.
『大学』と『大学校』はどう違うのか
この発想の原点は,たまたま社命で『ものつくり大学』準備段階から出向し,どんな大学にすべきか侃侃諤諤と議論し,大学を『教授』としてゼロから作り上げるという極めて稀な経験をしたことにあります.
[1] Technologistとはどんな人?
『ものつくり大学』設立の根拠となる『ものづくり基本法』では,ドラッカーの説に従って,これからの社会に必要なテクノロジストを育てるためにものつくり大学を設置するとありました.しからば,テクノロジストとはどのような要件を備えた人間なのか?準備委員会のメンバーでありドラッカーの翻訳の大家上田敦生先生に講義して頂きましたが,要約すれば以下のようなことでした.
“極めて多くの知的労働者が,知的労働と肉体労働の両方を行う.そのような人たちをテクノロジストと呼ぶ.テクノロジストこそ先進国における唯一の競争力要因である”
多くの人は,知的労働と言うと事務所,肉体労働というと現場作業を連想すると思いますが,ここでは違う定義と考えて下さい.料理人を例にとりましょう.決められた通りのレシピで料理を作り続けるのが肉体労働です.
一方で,客の好みと体調を見極め,手元の材料の状態からレシピを変え,客に喜んでもらえる味の料理を作る時,その料理人は知的労働と肉体労働の両方を同時にしたと考えるのです.事務所でもルーチン通りの業務を進め続ければそれは肉体労働で,状況に応じて業務の進め方を変えれば,それは知的労働と肉体労働の両方を同時にやったテクノロジストの仕事になるわけです.
ものづくり大学においてはテクノロジストの定義を医学知識を身につけた上で,自らメスを持って手術をする外科医のように,工学の知識を身につけた上で,みずからの手でモノが作れる万能エンジニアと定義し,開設準備を進めました.
[2] "大学"と"大学校"とは何が違うのか
ものつくり大学設立委員会の我々にとっての当面の課題は,厚労省所管の『能開大(職業能力開発大学校)』(K系)に対して,文科省・厚労省が共同で経営する『ものつくり大学』(D系)は,どう違う機軸を生み出して運営するかでした.我々が出した結論は以下の通りでした.
(2-1) 大学(D系)は学問(真理の研究)を行う場である
大学(D系)は,学問の自由が保証され,多くの研究者(教授等)が自分の研究室を持ち,そこで様々なテーマの研究を行っています.教授たちの評価は,いかに優れた研究をし論文を発表したかにかかっています.そのために国庫から研究費が出ており,テーマによっては年間数億円というのもあります.研究とは未知なるものを手の内に入れ形式知化することを言います.
もう一つの業務は,自分のゼミナールを持ち,後継の研究者を育成することです.教授は,学生に見せながら自分の研究することで必要な技術・手法を学ばせ,ディスカッションすることでものの見方考え方を鍛えます.学生を育てるためには手間が掛かりますから,一人当たり何がしかの手当が付きますが,何人の学生を育てようが,学者としての業績にはなりません.
大学は学生から見れば大規模な屋台村に似ています.それぞれの屋台(研究室)では世界最先端の美味しそうな研究をして居ます.どの屋台に立ち寄り,どの研究をかじるかは学生の自由です.席には限りがありますから先手必勝です.ぼんやりしているとろくな食事も取れず,終わってしまうこともありえます.
文部科学省の目線で見れば,いつかは世のため人のためになる研究をさせるために,一流の学者を集め研究させているのが大学であると同時に,今の学者より優秀な学者を育てて次世代に備えるのも,その大学の任務としているのです.
このことを言いかえれば,大学内では教授は真理の探究が仕事であり,学生はそれを見習うのが仕事であると言えます.裏を返せば,実社会に出た後の『食い扶持を稼ぐ能力』は大学には期待されていませんから,ぼんやりと大学を卒業し,食うに困るか否かは本人の心掛け次第ということになります.
後から説明しますが,食い扶持に困らない技能技術を身に着けるのは専門学校の役目だということです.
大学の歴史を紐解けば,中世ヨーロッパで始まり神学・法学・医学が主体で,牧師,弁護士・裁判官・検事,医者,等の職に就く事になっていました.現在の大学では理系3/文系7で圧倒的に文系が多いのですが,文学部と経済学部は実業界からかけ離れた学問となっているので,会社に入っても直接役に立つモノは無いと考えた方が良いのです.例えば,英文学を専攻したから通訳ができると考えたらとんでもなく甘いと言わざるを得ません.ビジネスの会話は,社運をかけた駆け引きの場ですから,英国とビジネスをするのであれば,会社としては英国のことを知り尽くした有能な英国人を社員として雇って責任ある地位につけるのが一番なのです.経営学を学んで実社会に出るのであれば,中小企業診断士の資格を取得する事をお勧めします.この資格を持っていれば,会社のどの部署に行っても即戦力として働ける知識があるからです.
(2-2) 大学校(K系)は技能技術者を育てる機関である
学校の『校』の訓読みは『かせ』で,拘束する意味も含まれていて,『学校』は学ぶ建物という意味の他に,目的に合わせて既存の学問体系から必要な部分を切り出してきて,それのみを学ばせ,目的とする人材を育てる機関という意味も持っています.
教える人は教授ではなく『教諭』と呼ばれ,その分野の名人・達人が当りますが,彼には研究活動は期待されて居ません.学ぶ人の学習目標は教師のレベルに近づくことであり,教師のレベルを超えることは期待されていません.新技術を開発することも期待されていません.
教育する対象者は,小学校では児童,中学校・高等学校は生徒と呼ばれます.高校を出た者が学ぶ学校は,多くは『○○専門学校』と呼ばれますが,『○○大学校』と名乗る学校もあります.『大学校』には法的な制約は薄く,自由に設置でき,現に企業内研修施設で大学校を名乗っているところもあります.公的には『防衛大学校』『気象大学校』等が有名です.高校を得てから学ぶ大学校や専門学校の卒業生は,研究者では無いので『学位』は与えられませんが,社会に出て直ちに役に立つ『資格』を得る事ができます.会社にとっては即戦力となる貴重な人材になります.
言い換えると,『大学校』卒業生は,即戦力になるので会社では,現状の業務をテキパキと効率良くこなすことを期待されますが,時代に合わせてより効率的な仕組みに再構築することは,彼らには期待されていません.それゆえ彼らだけの会社になると,日常活動は支障が無い安心しているうちに,世間の進歩からは置いてきぼりになる恐れがあります.
このように,『大学校』は実務のプロを育成する機関であり,『大学』は,真理を探求する研究者を育てる機関である.大学卒業生は会社で採用しても即戦力にはならないが,社内で再教育することによって先を読み,現状を変えていく人材,即ち管理職から経営陣となる人材になる事が期待できるのです.
(2-3) 大学受験勉強とは何か
2-3-1. 共通一次試験で満点でもクイズ番組でしか役に立ちません
本稿のテーマでもあるので繰り返し述べますが,お受験と称し,幼稚園から高校まで進学に有利な学校を出て一流大学に入学しようと猛勉強する風潮があります.しかし,大学入学試験は,広い学問体系の中から文部科学省が選定した『高校教育課程』の中で,採点しやすい問題しか出題されません.私の頃は『傾向と対策』という言葉が流行って居ました.しっかりと日日の授業を受けて勉強すれば,文部科学省が期待したような立派な社会人としての『歴史認識』や『人生観』と言った教養を身につけることができます.
しかし受験勉強としていかに効率よく良い点を取るかという姿勢で勉強したときは,試験に出るところだけを重点に勉強することになり,単なる暗記作業になってしまいます.このようにして学んだ学問は,たとえ共通一次試験で満点を取っても,断片知識の寄せ集めに過ぎず,テレビのクイズ番組で賞金稼ぎするぐらいしか役に立たないのです.
因みに,1970年代のトヨタでは商業卒は事務員,工業卒は技術員として配属されましたが,普通高校卒は,教養は高いのですが,会社で即戦力となる特技がないので,適性検査と訓練を受け現場作業員として配属されました.能力のある人間はたちまち現場で頭角を現し,教養の高さを活かしてリーダーから職長に,更に製造課長に出世しましたが,事務・技術員から課長になるのは稀でした.普通高校で教養を身に付けただけではダメで,その後の努力が大事だということが言いたいのです.
2-3-2. 大学は自ら学ぶ場所,ぼんやりしていると何も身につかない
ここからはこの4月から大学に入った新入学生の目線で説明します.
小学校から高等学校までの先生は『教諭』と言い,教育心理学などの専門知識を学んだ上,教育実習をして教職免許を取得したその任に当たっています.教えることだけが仕事ですから落ちこぼれを出さないように生徒たちに手取り足取り教え込みます.
ところが大学教授は,教職免許は全く関係なく,立派な論文を書き学位を取った人がなるのです.つまり教える技術はどうでもいいということです.そして学ぶ方は『学生』と呼ばれ,自立したオトナであるという意味が隠されているのです.
入学したての教養課程では,教室での講義はありますが,1時間の講義を受けたということは,予習に1時間,復習に1時間合計3時間勉強したとみなしているのです.
講義の内容は担当する教授が自ら選んだ時代の最先端をゆく理論であるのが普通です.筆者の思い出では,理系の数学の初日,高等学校でやってきたことは初等数学と一言で片付けられ,学部の研究に耐えるように高等数学の基礎知識を学びますが,必死に食らい着きましたが全部は理解できませんでした.
高等学校までは先生は教えるだけが仕事ですから生徒の理解度を確認しながら授業を進めていきますが,大学の先生は自らの研究を進めることが第一の仕事で,教える事は二の次ですし,教えたい事が沢山あるので,個々の学生の理解度を確認している暇がありません.期末テストは,成績の差を作るだけですが,講義が理解できてない学生は単位を与えません.単位が欲しければ来年再度授業を受ければよいのです.
大学運営と言う観点から見れば,費用は授業料だけど賄えないので,多額の入学金を徴収しています.そのため留年する学生は経常上不利になるので,よほどのことがない限り卒業させてしまいます.
巷の噂では,懸命に受験勉強した学生ほど入学すると安心してしまって勉強しなくなると言いますが,先に言いましたように共通一次試験百点満点でもその中身は『高校課程』のつまみ食いに過ぎませんから,実社会で稼げるのは,クイズ番組の回答者になるしかありません.
更に,先にお話ししましたが『大学』とは,学問すなわち真理の探求の場であり,次世代の研究者を育成する場所でもあります.何をどれだけ研究しても自由です.学生たちは,ここで研究している教授等のもとで,学問の方法学び,自らの力で師である教授を超える新しい分野を開拓し,その証の学位論文(学士・修士・博士)を提出,認められると学位を授かりますが,一般には実務に直結するモノではないので『大学』や『研究所』以外では,学位では飯が食えません.
法学部卒は司法試験,医学部卒は医師免許,教育学部卒は教員免状と言うように,資格を持っていないと,ICTが発達し,AIの活用が本格化した今日,希望する職種への就職はきわめて困難になっています.
学生諸君は,卒業後の人生に比べて,大学在学期間は時間にゆとりがあります.大学での高邁な真理の追求を通じて『未知のものを形式知化する』ノウハウを身につけ,将来の会社幹部としての素養を得た上で,将来やりたい仕事の近くにある『資格』を大学在学中に取得しておく事が,肝要です.
今年めでたく大学入学を果たした学生諸君は,このことを念頭に勉学に励んでいただきたいと願う次第です.
2022年4月吉日
(株)Jコスト研究所 代表 田中正知
2022年1月
2022年 年頭のご挨拶
遅ればせながら,明けましておめでとうございます.
本年もよろしくお願いいたします.
このホームページも, コロナ禍の影響で 丸一年お休みを頂いてしまいました.
誠に申し訳ありませんでした.
2022年度は,『Jコスト論』 普及のために頑張っていきたいと思っております.
TQCの基本原理は通常PDCAと覚えます.更地に計画を立てる場合はこれでよいのですが,前年に引き継いだ業務を今年どのように展開させるかという場合は,まず今までの反省があって,その上に立って次の展開をする必要があります.
つまりこの場合はCAPDつまり,前年度の反省が1番にあり,それを分析した結果,今年度の実施計画ができるわけです.
この文脈に従って,まずこのコラム2019年12月号の記事の続きからお話ししたいと思います.(さかのぼって,その記事をお読みください…)
2019年6月,中国河南省にある国営企業『新航グループ』と改善支援の契約を結び,9月に幹部に『本流トヨタ方式』と『Jコスト論』の研修会を実施し,10月から翌年4月まで第一次展開として4工場の改善を現地指導することになりました.
ところが突然のコロナ騒動で2020年から渡航禁止になり,以後2022年の今日まで中国には渡れない状況が続いております.
田中が行けなくなった状況下でも,彼らは自分達だけで改善を進め成果を上げ,コロナの影響で悩む全中国の企業にこの成果を伝えるべきだという董事長の判断で,2019年〜2020年の活動内容は10月21日に中国全土に向けてネット配信されました.この件はこのHP内でもご案内いたしましたが,ご覧になられた方もいると思います.
今はもう配信されていませんが,下記に写真で記録してあります.
この改善成果に関する弊社のコメントは12月号に詳しく記載しましたが,中国における精益活動の元締めである趙克強博士は,この成果発表を高く評価し機関誌『PlanetLEAN』に投稿しました.是非ご覧ください.
The J-Cost theory - Planet Lean on boosting financial results
『Jコスト論』が第三者によって英文で紹介された最初の事例となりました.
2020年秋からは,この活動を残りの工場全部にも展開していきました.時々リモート会議を持ち,質問に答え,改善の急所の講義もしました.
2021年秋,『新航グループ』から大きな成果を上げたので,その報告と,感謝の意の表したい,同時に田中の80歳の誕生祝いをしたいと連絡がありました.
10月10日10時(日本時間),『新航グループ』『佐吉諮問(提携コンサル)』『趙克強博士』『Jコスト研』4者が国際リモート会議を行いました.
最初に『新航グループ』のプロモーション動画がありました.
その後,副総経理から改革の総括説明があり,
『会社としては,点から線へ,線から面へと物の見方を広げてきたが,Jコスト論を学んで新たに時間軸を加えることによって,会社の中の事象が平面から立体に変わった心境である…
経営目標は売上高利益率(PL)から資産利益率(BS)に変更し,現場では生産の流れを速くし,全社的には資金の流れを速くする活動に転じ,全社一体となった活動が開始され,着々と成果を上げつつある…』
旨の報告がありました.
その後現場の推進者の声を集めた動画の上映があり,各工場の改善リーダーたちが,
『こんな転換ができた…』
『このようにして現場を指導した…』
『工場で働く全員が滞留させてはいけないと思っている…』
等々自信を持って発言していました.下記がその動画です.
それから,リモート会議は誕生祝賀会になりました.
その時,趙克強博士から中国語で祝辞があり,日本語の手紙を渡されました.
その後副総経理からは,田中の傘寿の誕生日を祝う綺麗な『寄せ書風小冊子』を頂きました.そのPDF版が後日届きました.
小冊子の表紙には『水を飲む者はその源を思い,成果を出したときに師を思う.』その後に『田中先生80歳の誕生日おめでとうございます』と続いていました.
小冊子の中味は,指導したときのスナップ写真と,会社幹部のこれからの取り組みに対する決意表明でした.
下記がそのPDFです
田中にとっては,80年の人生で初めての出来事で,感慨深いものがありました.
中国のこの会社の裏話として,経理部長がそれまでの改善活動に疑問を持ち,拙著『トヨタ式カイゼンの会計学』中国語訳を読み,『これだ!』と総経理を説得し上海の講演会場まで連れてきたとか…
改善契約が成立すると彼女は事務局を買って出て,今まで金額でしか把握していなかった工場各部署の原材料や中間製品の在庫量を,毎日の平均使用量で割って,在庫滞留日数何日分と言う指標を併記し,全工場に提示しました.
この経理部長は自らも在庫金額と滞留日数の表を片手に,時には総経理のお供をしながら工場長とともに現場で実態を確認し,対策の推進を促して廻ったといいます.
添付写真をご覧ください.2020年成果をNet背信したときの1コマですが,この女性が件の経理部長で後ろに写っている工場長に対して,在庫データを押し付け改善を進めさせたのでした.
因みに,製造現場にとっては原価低減は人員削減であり,厳しい負荷ですが,在庫低減はいかようにでも対応できます.しかし,在庫を減らしても欠品にならないようにするためには,品質不良や設備故障の低減,出勤率の安定化等,職場体質の強化が必須になります.
実際,職場内の滞留を無くすことで,人員,設備に余力があることが分かり,工場スペースはガラ空きになります.何より,職場内の在庫が現金になり浮いてくるのです.
粗利2割,月商10億円の会社が,滞留3ヶ月を2ヶ月(回転数を4回⇒6回)に改善すればPL上の毎月の粗利2億円の他にキャッシュフローとして約8億円の現金が手元に入ります.
この余ってきた経営資源を,新製品開発に廻すなどして会社は更なる飛躍を遂げる事ができるのです.
中国のこの新航グループはそれを理解でき,その方向への改革に乗り出したのでした.そして,この『Jコスト論』に基づいた在庫低減活動こそは,2021年1月のこのコラムで,皆さまにお伝えし,お薦めした2021年度アフターコロナに向けてやるべき社内改革でした.
恐れ入りますが,もう一度2021年1月の所信表明の記事を熟読した上で,今回掲載した『新航グループ』の発表を見直してください.
2019年に田中が彼等に教えたことは
「トヨタ生産方式の二本柱は,『自働化(品質を絶対確保)』して『JustInTime(滞留をなくしできたての商品をおとどけする)』ようになれば,利益は付いてくると言うことを意味している.
この世にあるあらゆるものは時間とともに動いている.
たとえばこの瞬間倉庫にあるAと言う100万元の在庫は,何日間で使い切ってしまうのか,Bと言う10トンのインゴットは何日でなくなるのか,無くなるまでの時間を把握すれば,今の仕組みから見て適正か?多すぎるか?が分かる.
減っていく速さを正確に把握するためには,先ず市場で毎日平均何個売れているかを把握する必要がある.次にその売れる速さに合わせて生産するには,できるだけ小ロットで多回生産する必要がある….
『JustInTime』生産の模範は中国料理のレストランである.
迷ったら中国料理を食べに行けば答えが出る.
その彼等が『自ら考えて,自ら成す』的に,自分達でやってきた事を発表しているのですが,その内容は,2021年度のアフターコロナに向けて日本企業がやるべきこととして纏めた内容を辿っていることを気づいて頂きたく思います.
このことを違う形で表現すれば,2019年10・11・12月の3ヶ月間しか現場改善指導できなかった『新航グループ』は,総経理以下全社一丸となって2021年まで『Jコスト論に基づく改革』を進める中で,
部署毎の在庫品名と在庫量から在庫期間を計算し,改革開始時からどれだけ削減したか計算でき,更に会社全体では基礎収益力(≡粗利÷棚卸資産)がどれだけ向上したか測定するプログラムを作成したこと
各工場単位で改革推進チームを編成し,工場の実態を反映させた業務分掌を作製し,更に社員に対する教育資料を編纂,教育実施してきたこと
改革を進めていくと,従来の調達・製造・営業・納品物流等の工程別管理では限界があることに気付いたこと
今回,このコラムでは敢えて『新航グループ』から頂いた資料をそのまま掲載しました.その意図は,読者の皆さまご自身で
- 【A】2021年末における皆さまの工場の実態
- 【B】2021年1月弊社がアフターコロナに向けてお薦めした取り組み
- 【C】2021年10月に『新航グループ』から頂いた資料
位置付けが明らかになれば,御社の2022年度方針で重点を置くべき事柄が明確になります.万一欠けていることがあれば,追加すれば良いのです.
『過ちては改むるに憚ること勿れ』です.
岸田新内閣は,その範を垂れています.国民もそれに従いましょう.
コロナ禍はオミクロン株による第6波が迫ってきていますが,感染力は強いモノの幸い軽症の様子です.桜が咲く頃になれば,暖かさで流行が収まると思われます.この時からいわゆる『アフターコロナ』の経済活動が先進国から始まるとでしょう.
このうねりに乗り遅れることなく御社が飛躍することを願ってやみません.
2022年1月吉日
(株)Jコスト研究所 代表 田中正知
2021年1月
2021年 年頭のご挨拶
遅ればせながら,年頭の御挨拶を申し上げます.
御社のますますのご発展をお祈りいたしますとともに,本年も相変わらずのお引き回しの程をお願いいたします.
ところで,正月の伝統の七草粥を心静かに味わっていたとき,ものづくりに携わる我々にとって大きな影響を受ける次の事件が起きました.
- 【A】米国現職のトランプ大統領がけしかけた議会乱入事件……
- 【B】東京で1日に2447人のコロナ感染者……
昨年末を約束したお話しに入り前に,まずこれに触れてみたいと思います.
【A】について
- 自由陣営のリーダーで,巨大国家アメリカの正体を世界に露呈してしまい,これが今後の世界情勢にどのような影響を及ぼすのか……心配されます.自浄作用が働き始めたので,救いがあります.
- アカウント永久停止等は,国民に選ばれた大統領より強い力を持っている事になり,全世界はGAFAに屈したということなのか……心配です.
- ヒトラーは,ナチスを結成し,草の根から14年掛けて天下を取ったのに,トランプ氏Twitterで,司会業から7年で大統領になりました.信者は全盛期7千万人とか……,彼は天性だけでここまできたが,ナチスの技法があれば,核のボタンを片手に世界制覇も可能だったという話があります.この事実を知ってしまったので,世界のあちこちで,第2,第3のトランプ氏が生まれてきそうで,怖さを感じてしまいます.コロナ以上の恐怖です.
【B】のニュースを聞いて,先ず頭に下記都々逸と,ミッドウェイ海戦でした.
♪『ああ』して『こう』すりゃ『こう』なるモノと,知りつつ『ああ』して『こう』なった ♪
- ミッドウェイ海戦とは
-
1941年12月の真珠湾攻撃時,米軍空母の姿がなかったので,洋上の味方艦隊が米軍機に攻撃される事をおそれ,第1波攻撃だけで引きあげたといわれて居ます.
一方,1942年6月のミッドウェイ島攻撃時も,米国空母の姿は無かったのに,『洋上の味方艦隊が米軍機に攻撃される事』は考えず,『絶好のチャンス』として,第2波の攻撃を決定,その準備中の最悪のTimingに米軍機の攻撃を受け,空母の甲板上の爆弾が誘爆し,全空母と全艦載機,何よりも優秀なパイロットを失ってしまったといいます.軍の極秘事項とされ,処罰どころか責任追及も無かった……とされています.この話は以下の『言霊信仰』や『空気の話』が関係していそうです.
- 『言霊信仰』
-
ある言葉を発すると,その言霊が万物の霊魂に働きかけ,その言葉を実現してしまうという信仰が,社会の隅々まで広まっています.親が病気になったとき,遺産相続の話は,『縁起でも無い』と咎められます.
逆に『コロナなんか直ぐ消える』とみんなが考えると言霊が消してくれる,と無意識のうちに考えている……最悪の事態を考えず,上手くいった時だけを考えてものを実行する.
- 『空気の話』
-
昔,山本七平(イザヤ・ベンダサン)が,会議の席では上司に忖度し,同僚に気を遣い,理路整然とした論理では無く会議室に漂う『空気』で物事を決めてしまうと嘆いていました.
1月は多くの会社にとって,年度替わりの月で,おそらく会社の年度方針が出されたり,御自身が自部署の方針をお作りになったりしていると思います.
今一度 ここに書いた 日本人の性でともいえる『言霊信仰』や『空気の話』の観点で論理は『理路整然』か,実行計画は5W1Hの観点から見て,細部に展開されて居るかをご確認下さい.
さて本題に戻って,年末の続きのお話をいたします.続きですので,第7章から始めます.
最近,DX(デジタル・トランスフォーメーション)が脚光を浴びています.
デジタル技術を駆使して,戦略的な経営をやってこうということだと理解していますが,その前提としては各社の工場がよく訓練された軍隊のように『俊敏に対応できる』ことが大前提と思います.
この『俊敏に対応できる』工場こそが弊社が永年推進してきた『本流トヨタ方式』が目指す工場の姿そのものなのです.『御社にDXを導入するには如何にすべきか・・・』と考えながら第7章をお読み下さい.
[7] 2021年 日本のものづくりは何を目指すべきか
7-1. 今までの改革は,的外れではありませんか?
カルロス・ゴーン氏が,非合法な手段で日本から逃亡して1年になりますが,1999年に彼が日産の倒産の危機を救い,V字回復させた事は事実です.
当時の日本の産業界は 『労働生産性という落とし穴』に嵌まっていて,重症患者が日産自動車だったのでした.この辺のことは,このホームページの連載コラム『Jコスト改革の考え方』第15回に詳しく書いてあります.先ずそのコラムを熟読して頂きたく思います .
ゴーン氏は1999年の『日産リバイバルプラン』の中で,日産の間違いを以下の様に指摘しています.
購入費用 | 60% | @ | |||||||
一般管理費 | 23% | A | |||||||
製造原価 | 17% | B | … | 研究開発 | 6% | C | |||
内製加工費 | 11% | … | 減価償却費など | 6% | D | ||||
労務費など | 5% | E | |||||||
DE:筆者推定 |
当時の日産がやっていた活動で低減しうるのは,E労務費(原価の5%)に過ぎないことが分かっていなかった……
ゴーン氏は役員会の言語を英語にして(『言霊』を排除),TQMの手法で成果をコミットさせ,全方面で改革を断行し,2003年までの4年間で2.1兆円の借金を返済したといいます.
筆者は,自社内のみならずSupply-Chainの隅々まで点検し,あるべき姿に向かって改革を押し進めていく……会計的に見れば,PLだけでなくBSもCFも原因に遡って見直していく……という部分は賛成します.
20年あまり経ちましたが,大変残念なことに,大学の先生たちはゴーン氏の指摘を理解できず,かつて恩師から教わった通りの百年前のGMのスローン氏の経営技法や,テイラーシステムを旧態然と学生に教え続けています.
経営者も,『労働生産性の落とし穴』に嵌まり『生産性本部』とか『ものづくり革新本部』といった組織を作り,優秀な人材を投入し作業改善に力を入れています.
彼らスタッフに掛かる費用は丼勘定で一般管理費に計上され,現場改善効果は支払い労務費に計上されますから……費目が違うので『費用対効果』の測定はやっていないと思いますが,費用の10%でも回収できていれば御の字と思います.
7-2. 自社を,より繁栄させる為にはどうするか?
各企業で設置されている『生産性本部』の本来の役目は『自社をより繁栄させるため』だと思います.では具体的に何をどうすればよいのかの問いに,以下の3つの【答】が考えられます.
- 【答-1】売上は現状維持とし,原価低減して利益額を上げる!
- 【答-2】設備投資等をして増産を図り,売上を増やし利益を上げる!
- 【答-3】投資せずLead-Time短縮という切り口で業務改革を推進する!
以下順を追って吟味していきましょう.
【答-1】売上は現状維持とし,原価低減して利益額を上げる!
これは もっとも多くの 企業で取り組んでいる方法です.現状の売上高に対して生産能力に余剰があるので,その分の人員を減らし,設備を減らす,と言う活動になります.
このテーマを追求すると『新聞売り子の問題』という古典的なOR(オペレーションリサーチ)の問題に辿り着きます.講習では『統計的に計算した数量を余分に仕入れて置く』と言う解と共に,実行すると客はドンドン減っていき,潰れるという『オチ』も教わります.買えなかった客の心理は数式では解けないというORの限界も教わります.
新聞と違い一般の製品は在庫を持って,生産・販売していきますが,長期的に見れば売れなくなっていき,最後は生産打ち切りになります.原価低減を狙って売れに合わせた生産規模を縮小して行くことは『店じまいへの道』でしかありません.
植物達が 毎年花を咲かせ実を成らせ子孫を増やすように,会社も寸暇を惜しんで子孫(新製品・新製法)を産み育て,更なる成長をねらっていくべきでしょう.
【答-2】設備投資等をして増産を図り,売上を増やし利益を上げる
積極的な意欲的な話で大変結構なことですが,資金回収に時間がかかるという欠点があります. 例えば新工場を建設して機械を設置し,人を集めて訓練し生産に移るとなると2〜3年掛かります.製品は市場に出荷され,代金を回収されるまでにはさらにまた時間がかかります.
残念な例としては,シャープの危機が有名で,亀山工場で作った液晶パネル『亀山モデル』は有名となったので堺に巨大な工場を建設し増産に打って出ましたが,市場が伸びず,赤字が積み上がっていき,最終的には台湾企業に下りました.
急速に成長して行った『いきなりステーキ』も 流石に店舗数が増えすぎて,共食い現象になり, 最近はまた 急速に閉店が続いている様子です.
国産初のジェット旅客機は,開発が長引いたところにこのコロナで,1兆円余の損失を抱え,先が見えなくなっています.
このように,業績を伸ばせれば大変に結構この上ないのですが,失敗のリスクが高いのも確かです.
こうして見てきますと,次の二つは,どなたにもお勧めできる方法ではないことがわかります.
- 【答-1】売上は現状維持とし,原価低減して利益額を上げる!
- 【答-2】設備投資等をして増産を図り,売上を増やし利益を上げる!
残ったのは【答-3】投資せずLead-Time短縮という切り口で業務改革を推進する!となります.これはまさに『本流トヨタ方式』で,弊社のお勧めの道筋です.もしDXを導入して,戦力的に市場で闘うのであれば,必須条件になります.長文になりますので,章を改めてご説明いたします.
7-3. Lead-Time短縮という切り口で業務改革を推進する!
<設備投資はせず,仕事のやり方を変える>
下記の順にご説明いたします.
- [Step-1] 受注⇔納品のLead-Time短縮で市場競争力確保
- [Step-2] 検収⇒納品のLead-Time短縮(在庫低減)で体質強化
- [Step-3] 浮いた経営資源を活用し,更なる成長
[Step-1] 受注⇔納品のLead-Time短縮で市場競争力確保
受注⇔納品のLead-TimeのことをOrder-to-Delivery-Lead-Time(略してODLT)と言います.
-
飲食業界は昔から客を待たせない事を競ってきた
-
中国の例
店に入ると客はテーブルの上のQRコードをスマホに読み,出てきたメニュー(写真と説明)から料理を選び,店員に転送すると,砂時計を置きます.時間内に全品届かないと上海では1皿サービスされます.
-
日本の例
『飲み物』と『お通し』で時間稼ぎ
-
中国の例
-
どこの顧客もOrder-to-Delivery-Lead-Time短縮を望んでいる
-
見本市では
-
中国企業
『電子データを送ってくれれば1週間後に現物を日本に届けます』といった売り込みをかけてきています.
-
日本企業
高品質と安さのみを強調……日本のものづくりが心配
-
中国企業
-
ODLTをダントツ短縮したら断り切れないほどの仕事が来た
筆者の仲間が,Order-to-Delivery-Lead-Timeが3週間と言われる業界で,5稼働日(正味4日間)にまで短縮したところ,客が殺到するようになり,プレミア付けると言う客まで現れ,今では客を断るのに困っている……収益も上々と言う自慢話を聞かされました.
Order-to-Delivery-Lead-Time短縮が,いかに市場における優位性を発揮するかを改めて知らされた次第です.
-
因みにトヨタのSupplierは
Order-to-Delivery-Lead-Timeが原則0.5日です.
トヨタの組立工場⇔サプライヤーは『かんばん』でやり取りしており,通称1-4-2 (1日4回納入の2回遅れつまり半日遅れ)という関係で繋がっています.
-
見本市では
[Step-2] 短縮したOrder-to-Delivery-Lead-Time維持した上で, 検収⇒納品のLead-Time短縮(在庫低減)で体質強化
ここでは,社内の業務推進体制を『Lead-Time』という概念で捉え,そのタイミングを調整(JIT化)することTotal Lead-Timeを短縮し,(在庫低減)俊敏に動く社内体制に再構築して行く活動になります.
[2-1] Lead-Timeという概念の行う在庫低減例の説明
上の図は病院の待合室で,A〜Gの人が診察を待っている状態を表しているとします.また,診察には1人あたり5分かかるものとします.
-
この状態を『人数で表現』しますと,
- 待合室にはAからGまで7人が待っている
- 今来たHは8人目なので,7人が診察を終わるまで待たなければいけない
- この状態を『所要時間(Lead-Time)で表現』しますと,診察には1人あたり5分かかるので,
- 待合室にはAからGまで診察時間35分相当の人が居る.
- 今来たHは30分間待たないと診察を受けられない.
- Bは5分,Cは10分,Dは15分……待たなければいけない
このように,
- 『人数で表現』すると,人数を減らす手段が見つかりませんが
- 『Lead-Timeで表現』すると,人数を減らすには病院に来る タイミングを工夫すれば良いとわかります.
これを受けて最近の病院では,事前予約が取れるようにしており,患者は病院に来てから帰るまでの時間(Total Lead-Time)は短くて済みますし,病院の駐車場や待合室はガラガラになります.
待合室 | ⇒ | (a) 原材料倉庫 | 患者数 | ⇒ | 原材料在庫量 | |
診察室 | ⇒ | (b) 製造工程 | 患者数 | ⇒ | 仕掛在庫量 | |
会計待ち | ⇒ | (c) 完成品倉庫 | 患者数 | ⇒ | 完成品在庫量 |
上のように読み替えれば,[Step2]の改善のヒントになります.
[2-2] 財務諸表から自社の棚卸資産の実態を知る
会社棚卸資産は『貸借対照表(バランスシート)』に記載されています.
前期末の棚卸し時の状況になりますが,
金額のままでは,どのように減らせば良いか分かりませんので,『損益計算書(PL)』から売上原価$U [\text{円}]$を持ってきて,
[Step2]の課題は,財務諸表上の棚卸資産(単位は[円])を減らす事ですが,先の[2-1]と同じように,時間(ヶ月)で表現すると対策が打てるようになります.
(7-3)式にあるように時間で表現すれば,次のように表現できます.
棚卸資産金額 | ⇒ | Total Lead-Time |
原材料在庫金額 | ⇒ | 原材料 Lead-Time |
仕掛かり在庫金額 | ⇒ | 仕掛かり Lead-Time |
製品在庫金額 | ⇒ | 製品 Lead-Time |
ということは『棚卸金額を半減させる』ことと『在庫リードタイムを半減させる』とが等価であるという意味になります.具体的に言えば,外注先からの納品を10日前に入れさせていたものを,5日前に変更すれば,原材料在庫金額は半減するという事です.
現場では,良かれと思って『早め,早め』に手配し・着工して居ますが,会社のためにも『ギリギリまで遅らせて,速く間に合わせる』が一番の理想と教えるべきです.
[2-3] 同業他社,業界等と比較して,自社の課題を明確にする
このHP のコラム『Jコスト改革の考え方』第6回目より
この式の 縦軸に売上原価粗利率をとり横軸に棚卸資産回転数を取ったグラフ(下図)を収益性分析図と名付けました.図は業界の違いを表したものです.各社の財務諸表は法律によって公開されていますので,ネットで調べて同業他社の収支分析することが容易です.
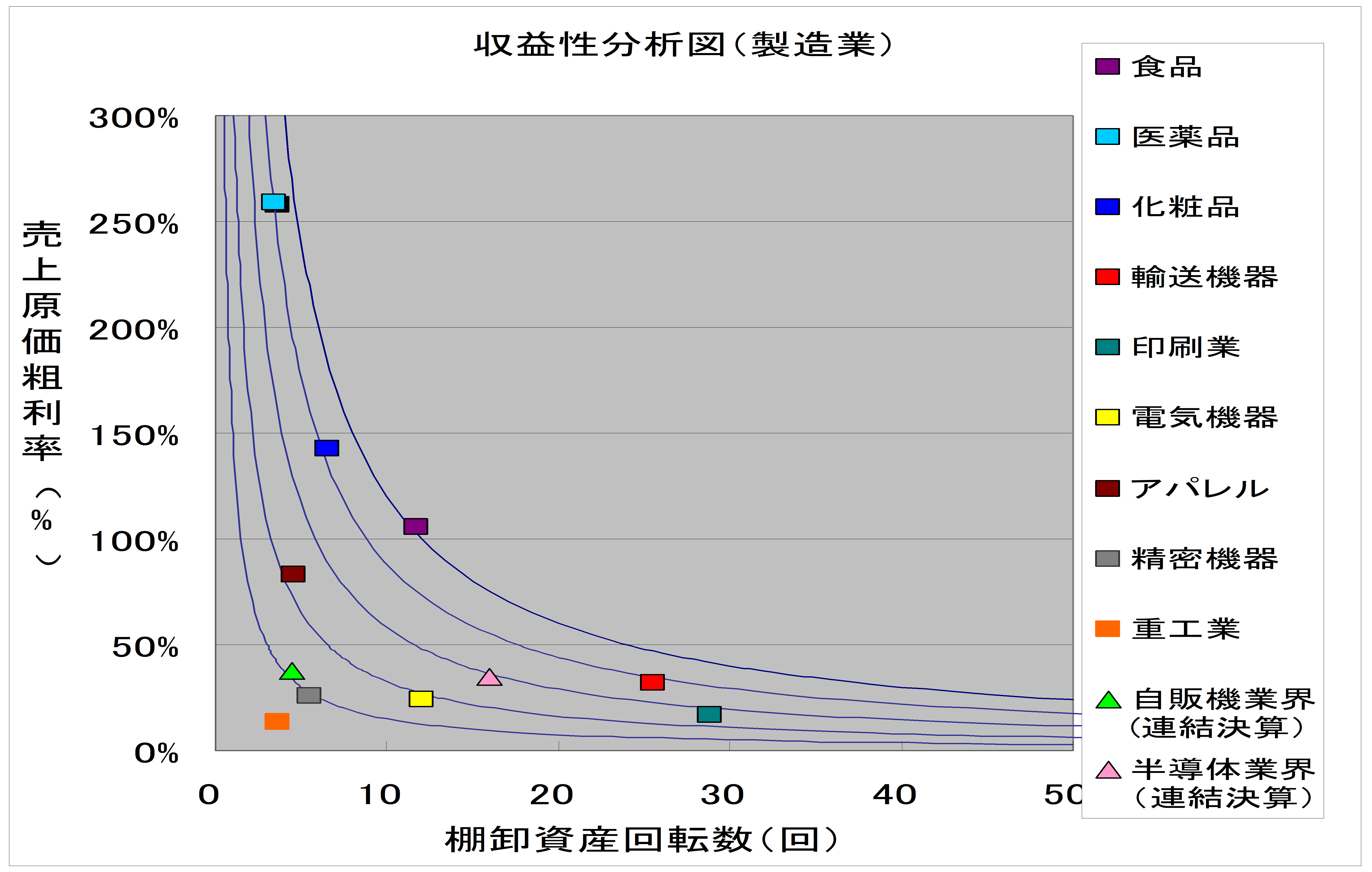
さらに同業他社と比べて,原材料在庫が多いのか, 仕掛在庫が多いのか,完成品在庫もいいのか,どこに問題があるのかも調べることができます.他社よりも悪いところを,他社並みに改善するということには現場も燃えますし,比較的容易だと思います.
このように 闇雲に改善するのでは無く, 他社の動向と比べて進める事も有益だと思います.
[2-4] Lead-Time短縮には『小ロット・多回』が特効薬
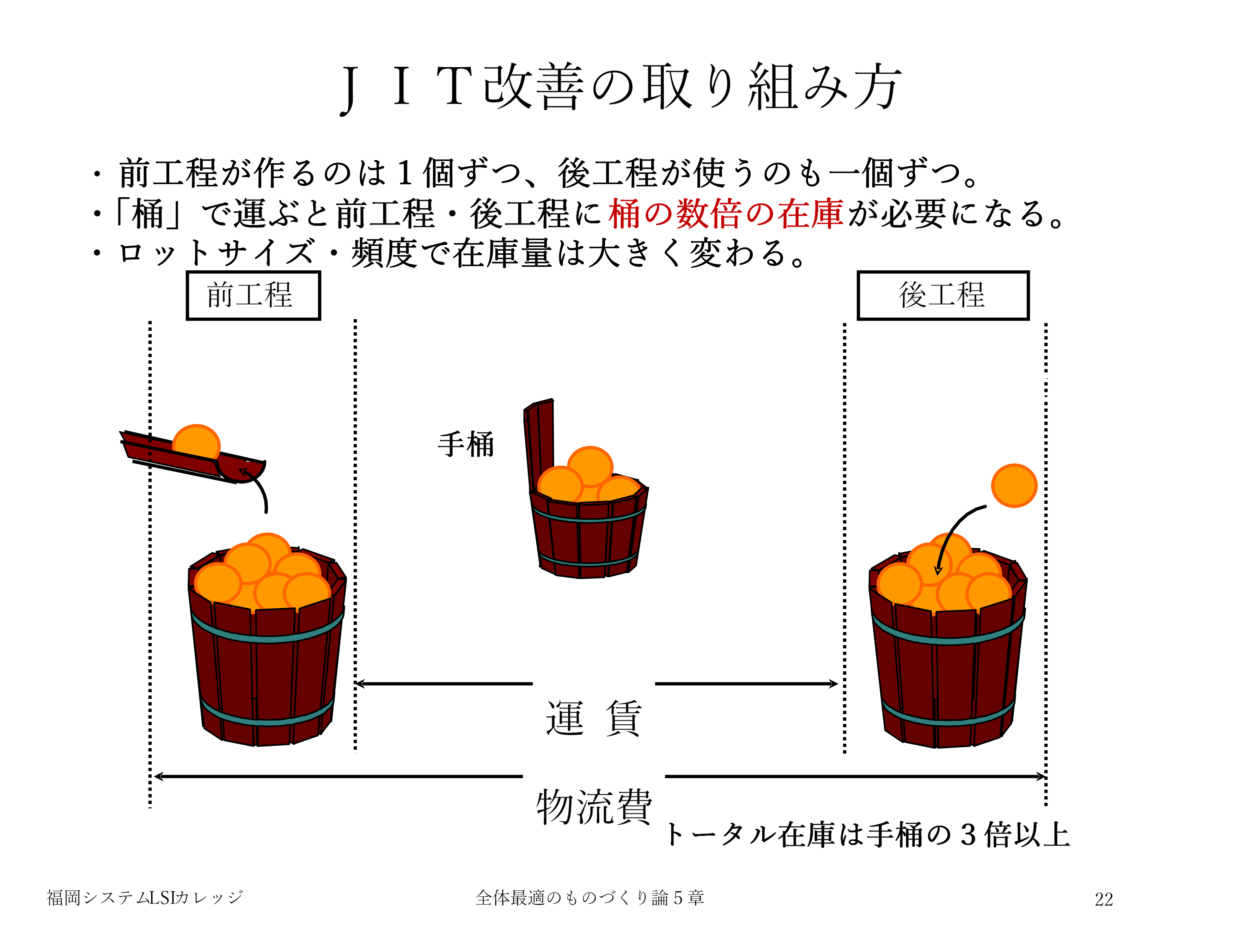
上図は,ロットサイズと在庫の関係をモデルにした図です.手桶で10個ずつ運ぶためには,Timingのズレも配慮しますと,上流に手桶でとりに行った時に15個くらいにと心配です.届けた先も5個くらいの残っていないと心配です.経験上,ロットサイズがn個であれば,上流・下流・運搬中の合計在庫は最低で3n個必要で,実態は4〜5n個で運用しています.
東西の道路と南北の道路が交差する交差点の信号を考えてみましょう.赤信号がもし1時間続いたとすればどうなるか考えてみて下さい.大渋滞になることでしょう.実際の交差点の信号は最大で2分間とされているそうです.そのお陰で東西も南北も,さしたる渋滞無く流れているのです.これぞ『小ロット・多回の極み』と言って良いでしょう.
[2-5] Lead-Time短縮を阻む組織の壁
日本の会社組織は機能別に縦割り組織になっており,そのトップは,社長の座を窺う専務クラスになって居ます.
(a) 原材料・外注品在庫 | …… | 購買部門 |
(b) 仕掛かり在庫 | …… | 製造部門 |
(c) 完成品在庫 | …… | 営業部門 |
それゆえ[Step-2]の改革にあたってプロジェクト・チームを立ち上げる時,その推進責任者には,(a),(b),(c)の上位にある『会社Top』か『経理』が就任しないと改革が進みません.これが改革推進の『胆』になります.
[2-6] トヨタ系サプライヤーの工夫例
[Step-1]で紹介したOrder-to-Delivery-Lead-Time 0.5日の中でのTotal Lead-Time削減の工夫の幾つかを紹介します.
- (6-1) 原則,『在庫後補充生産』
使用量の多い品番は1日4回 生産,極少量品番は月1生産.
- (6-2)上記を可能にするのは,トヨタの『平準化生産』があるから!
その裏にはトヨタの『共存共栄』思想.
- (7)トヨタはSupplier棚卸資産回転数は……30〜50回.
(在庫を押しつけてはいない)
国際競争力は強く,デンソーの30%余を先頭に,アイシン,自働織機,紡織等はトヨタの約10%を遙かに凌ぐシェアを獲得しています.
[Step-3] Total Lead-Time短縮するとは……
どのようになってるかを実体験を基にした一般論でお話します.
[3-1] モデルの設定
自動車用板金製のホイールキャップをイメージして,@板状ステンレス材料を,Aプレスして,Bバリ取り仕上げをし,C塗装し,D1台分ずつ梱包して,E出荷する……工程を想定
当日も出荷量は,前日に確定.平均A40台,B30台,C20台,D10台バラツキは±10%である……
従来から在庫後補充定方式,1週間単位で生産をした.毎日後補充生産に変更し,在庫を減らした.
以上を前提に,現場がどう変わっていくかのお話をします.
[3-2] 『仕掛かり在庫』減による製造現場変化
- 『1週間分ずつ生産』
A200台,B150台,……,D50台の連続生産では,完成品在庫は通常必要量の1.5倍〜0.5倍の間で管理していた.
- 完成品在庫
A300〜100台,……,D75〜25台あるのが普通.
- 『毎日生産』
朝からA40台,B……,D10台をその日に生産する.完成品在庫は;A60〜20台……,D15〜5台で管理
-
小ロット多回生産の効果(課題の顕在化)
『1週間分ずつ生産』Aは平均200台の完製品在庫持っての2日間 連続生産,設備故障・不良に容易に対応でき,ダラダラとした生産だった.
『毎日生産』A40台,……,D10台を,時間通り生産が必要!設備故障・品質不良等はすぐ顕在化します.速く直し,再発防止を図る必要に晒される.⇒ 現場には緊張感が走り,キチンと仕事し,再発防止の徹底を図る,理想の職場になって行きます.
-
作業完了の在庫が少ない効果(背水の陣効果)
Aプレス ⇔ Bバリ取り ⇔ C塗装 ⇔ D梱包 A〜Dまでの工程間⇔にある仕掛り在庫は,仕事を中断されることを嫌がるため,1日分または1ロット分以上の在庫を置いて生産をする という風習があって,この場合 どこにNeckがあって生産の速さが決められているのか分からないまま,ダラダラと生産していました.
『毎日生産』になりますと,@〜Dまでのどの工程も,A,B,C,Dを1日分ずつでも合計100台分作らなければならなくなります.準備・後始末等の時間を除いた,正味稼働時間を400分とすれば10台を40分間で作っていけば良いことになります.
トヨタ生産方式には『チョロ引き』と言う改善手法があります.チョロとは下図にある利便性の良い猪牙舟のことです.
この例では,各工程間を10台分ずつ40分間隔で移動(運搬)させます.
チョロ引きの導入で運搬工数が増えると思いがちですが,今までは前工程の溜まってきた中間製品を,頃合いを見計らって,一時置き場へ運んでいき,収納します.
次工程の材料置き場が空くのを見計らって,先に置いた一時置き場からからピッキングして次工程の材料置き場に補充していきます.
この時の運搬作業を,仕事を探して走り回って居る様を揶揄して『流しのタクシー』と呼びます.
一方『チョロ引き』は,前工程の完成品置き場から後工程の材料置き場へと一定時間間隔で一筆書きのように廻るので,通称『定期バス』と呼びます.改善マンの間では,『流しのタクシー』から『定期バス』に代えると運搬工数は経験的に1/3に減るとされています.
各作業工程では,チョロ引きした直後の在庫量で『生産の遅れ進み』が一目でわかるようになります.遅れている工程はみんなで改善したり,進んでいる工程から時々応援したりして,安定した生産ができるようになっていきます.安定したら更に工程間の在庫を減らしていきます.
このようにして,日々の生産能力向上活動が活発になり,日々が勝った・負けたのゲーム感覚で仕事ができ,長期的には成長が実感できるようになり,会社に行くのが楽しみになります.
10台分を40分というTACTを発生させる事で,作業にリズム感が出て来て,増えた段取り作業時間を差し引いても,経験的には10〜20%生産性が向上します.
-
生産の柔軟性向上
10台当たりの生産時間を把握できていますので,在庫後補充生産により納入量日々の変化や,自工程の設備故障などにも,生産時間の増減で,柔軟に対応することができます.
-
工程間在庫スペースが不要に
普通,この改善をすると,工場がガラガラになり,設備を間締めすると通常半分のスペースが有効活用できる空き地に変わります.
[3-3] 『毎日生産』による外注品倉庫の変化
1週間分ずつのまとめ生産であった為,外注品(原材料)は1週間分の一括注文になり,物流費もまとめた方が安くなるので前の週の内に一括納入となっていて,検収作業や検品作業,それを倉庫に収納作業で,納入日は丸1日てんてこ舞いだったが,残りの4日間は,倉庫から製造現場への供給のみの仕事になり,暇だったのでした.
『毎日生産』では,A,B,C,Dほぼ毎日,在庫後補充という形でほぼ一定量が納入されます.品質の抜取検査だけで, その日のうちに使い,過不足が判明しますから 受入時の員数検査の必要はありません.
-
受入即・製造工程へ供給
受け入れた外注品は,約100台分なので,トラックから荷卸しするついでに指定の場所に平置きするだけでOK.後からチョロ引きが,そこからラインに供給します.
-
受入時刻管理
等間隔で 納入することで,安全在庫を縮小できます.仕入れ先毎に毎日指定時刻に受け入れることで,トラックの混雑緩和のみならず,自社の社員は,他の仕事と掛け持ちが可能になります.
-
保管倉庫廃止
以上のような変化により,外注品用のラックビル,収納・Picking作業倉庫そのものが不要になります.
[3-4] 『毎日生産』による出荷準備場の変化
従来は,製造工程で完成した大ロットの製品を 1旦 完成品ラックビルに収納し,その後 出荷指示に合わせてピッキングし,出荷準備場に並べておくと言う手順でした.
『毎日生産』になると,『出荷荷揃え場』を『当日用』『翌日用』『翌々日用』と3カ所決めて置いて,次々とでき上がってくる,A,B,C,Dの完成品を,出荷指示に従って荷揃え場に置いていく作業になります.
- 完成品ラックビルは全く不要になります.その空間も不要になります.
- 当然ラックビルへの出し入れが無くなるので運搬作業量は1/3以下になります.
- 出荷時刻を決め,厳密に守らせる事で,全体の進捗管理が可能になります.ここを押さえれば,工程内の仕掛かり在庫を更に削減していけます.
[3-5] 『週次ロット』から『毎日生産』に改善した効果総括
-
【在庫低減】 21.5日分⇒6.0日分 15.5日分減
原材料在庫 10〜5日分 ⇒ 2〜1日分 …… △6.0日分 仕掛り在庫 工程上;0.5日分×4 ⇒ 変わらず 工程間;1.5日分×3 ⇒ 40分×3×3カ所 …… △3.5日分 完成品在庫* 10〜5日分 ⇒ 2〜1日分 …… △6.0日分 -
【工数低減】
運搬作業 受入・出庫,工場内,出荷場で各1/3に低減 製造工程 顕在化されたNeck工程の改善で2割向上 段替え増の工数は不明 -
【工場スペース】
原材料在庫(6.0日分),仕掛在庫(3.5日分),完成品在庫(6.0日分)が,ラックビルとともに不要になる
上記のように浮いてきた『経営資源』をOrder-to-Delivery-Lead-Time削減で新規獲得したら,顧客に向けての増産に使うも良いでしょう!製品寿命を考えている 次のモデルの生産準備をするのも良いでしょう.
ここでご説明した改革は,設備投資は一切行わず,知恵とやる気で,達成可能です.
Withコロナの時代にやるべきAfterコロナに向けての改革の1例としてご紹介しました.この改革はまた政府が推し進めようとしているデジタル改革の対応でもあります.ご参考になれば幸いです.
次回は,改革を押し進めるための『経営者と管理者と監督者の役割分担』について考えてみたいと思います.
2021年1月
(株)Jコスト研究所 代表 田中正知
2020年12月
2020年末のご挨拶
1年間のご愛顧ありがとうございました.
『東京オリンピックの年!』と一杯の希望と期待と持って迎えた2020年でしたが,新年早々から全世界が COVID-19パンデミックの襲撃に遭い,大変な年でした.その2020年も早いものでもう冬至となってしまいました.
1年間を振り返ってみると『疾風に勁草を知る』という言葉がありますが,全世界が同時に同じ困難に遭遇した事によって,強い風に押し倒される草と,凜として耐え抜く草(勁草)の存在が顕在化しました.
国のTopの指導力の差が顕在化し,台湾,ニュージーランド,ドイツのTopは女性で,指導力に長けていました.不幸にも日本の行政は勁草ではなかったこと.民間各社の業務推進体制,特にデジタル化も勁草ではなかった事が『リモートワーク化』で明らかになってしまいました.
個人としても,この事態に遭遇し『自分は会社で回覧書類を読んで昼飯食って帰るだけ』だった事を思い知らされ,ショックを受けている方も多いのではないでしょうか.ショックなのは,75年前までは日本だった『韓国』や『台湾』に対しても,大きく出遅れているということでした.今後の世界の中での日本の立場が心配になります.それを受けて菅内閣は,ハンコゼロ運動から始めて,行政のデジタル化を推進し始めました.皆様に会社は如何でしょうか?行政に遅れないように改革がすすむことを祈ります.
先回このコラムで,10月以降感染が伸び最大級の第3波が来ると書きましたが,残念にも,その悪夢の方向に進んでいます.ワクチンが実用化されたという朗報がありますが,これが行き渡り,鎮火させるまでに約1年かかるでしょう.ということはまさに来年1年は,コロナ開けに備えて,力を蓄える年と位置づけられそうです.
総括すれば,東京オリンピック2020は蓋を開けたら.『国対抗のパンデミック退治』のオリンピックでした.後半戦の来年は日本が追い上げて,上位入賞することを願わずには居られません.日本が上位入賞を果たすための皆様方の『アフター・コロナへ向けての改革』参考になれば……と思いを込めて,弊社の特記事項をご案内致します.以下長文になってしまいましたが,最後までお読み頂き,少しでもお役に立てれば幸いです.
それは,昨年末3か月間だけ指導した中国国営企業が,新型コロナの中で,独自の改革推進体制をとり,自力で『Jコスト改革』を成し遂げたというものです.そのやり方は,各組織が本来業務を真面目に遂行したというものであり,何処の会社でも成し遂げることができるやり方なので,ここで紹介し,弊社のお歳暮としたいと思います.以下順を追ってお伝えしましょう.
[1] 弊社のそれまでの中国企業への関わり状況
拙著『考えるトヨタの現場』,『トヨタ式現場の人材教育』,『トヨタ式カイゼンの会計学』の中国語版がご縁となり,ここ10年ほどは,年に20〜30日間ほど中国に出張し,『講演会』や,現場改善の指導をしてきました.
日系企業からスピンアウトした若手コンサルの会社『佐吉諮問』が,弊社の中国代理店的な役割を担って頂き,南京の国営企業『SUMEC社』や,杭州市にある大手監視カメラメーカー『Dahua社』などの現場改革のお手伝いをやってきました.
当時各社は事業拡大に勢力を入れていて,PL(利益計算)重視の弊害を是正には本腰を入れていず,日本の大企業と同じように業務が『購買』,『営業』と副社長クラスから縦割り組織になっていて,その組織のKPIは『支払い費用の低減』になっていた為に,各組織の人達は,少しでも費用を安くすることで組織間の覇権争いをしていました.
原材料の仕入れを例にとれば,1トン単位の購入よりも,100トン単位の購入の方が値下げの要求が容易です.購入した原材料を消費するのに半年かかろうが1年かかろうが,仕入れ単価が安ければ,購買部門としてのKPIは向上し,会社への貢献と評価されるわけです.
高度成長していた当時の中国では,問題が顕在化しませんが,日本のように成長が落ちてくるとそれぞれが安く……安く……とする結果として在庫量が増え資金繰りが悪くなり倒産の危機を招くのです.資金繰り(全体)は社長の責任で支払費用(個別)は各担当の責任という,部分最適と全体最適の分離が始まります.大企業の業績が悪化するのはここにあるわけです.
そして2018年頃から米中貿易摩擦が始まりました.その結果,中国の対米輸出は減り,在庫が問題になるようになってきたのでした.
[2] 出会いは『Lean-Summit In Shanghai 2019』
中国での精益活動を主導している趙克強博士のお招きで,毎年6月に行われる恒例の『Lean-Summit』の前座として『Jコスト論』の講習会を丸1日掛けて実施しました.たまたま出席していた河南省にある中国国営企業『K社』様の董事長と総経理が,自社の改革に使えると判断され,話はとんとん拍子に進み,先ず半年間で5工場の改革を手掛け,その進捗を見て全工場に展開するという合意を得ました.9月に2日間掛け『トヨタ生産方式』と『Jコスト論』幹部研修会を行い,第一期として10〜3月,毎月5日間で5工場を現地指導する形で『棚卸資産回転数(基礎収益力)』向上改革活動に着手しました.
[3] 全く新しい改革の取り組み方
国営企業『K社』様の改革への取り組みは,従来と全く異なったものでした.以下順を追ってご説明します.
3-1. 明確な改革目標
取引価格は現状のままで,仕入れから販売までのLead-Time短縮(棚卸資産圧縮)を追求し,下記の基礎収益力向上をはかる.
- 参考
- 一般には改革目標は『生産性向上』という曖昧なものに成り,中身は原価低減・工数低減・可動率向上・正味作業時間等々,活動の的が絞れず,以前やった改善を並べお茶を濁す事が多かった.
3-2. 推進体制 経営会議場を使ってTop自らが陣頭指揮する
議長 | 董事長,総経理 |
---|---|
事務局 | 経理部長(女性) |
- 参考
- 一般には,議長は生産性本部長(平取),議事進行は課長クラス.工場長は会場にいるのみで,実施事項の説明は工場改善Teamの係長クラスが行い,その内容はミクロ的に見た,ある工程の工数低減だったり,ある設備の故障率の低減などが主体で,工場長が管理すべき財務会計的な改革の評価は無いのが普通.(経理部はモノづくり改革運動に関与しない)
3-3. 具体的な進め方(会議室編)
- 経理部が財務会計計算から,先月の会社全体の進捗状況と,各工場の棚卸資産額・回転数の実績を総経理に報告する.
- 各工場長は自ら先月の取り組み状況を説明した上で,今月の取り組みと,目標に対する達成見込み状況を自ら総経理に説明する.
- 弊社が出席している場合は,改革の進展に合わせた注意事項や他社の参考事例の紹介等をする
- 総経理が各工場の進捗を評価し,董事長の訓話で締める
- 参考
- 一般には,各事業部を横並びに見る生産本部長には,工場長を査定する権限が無く,課長層や職長層にADVICEするだけである.工場長の直属の上司はボードメンバーの事業本部長で,各事業本部長は社長の前で,PL(売上や収益)で競って居て,BS(在庫量や資金繰り)は通常話題にしていない…….工場長の中には,会計オンチな人も居る.それ故,Lead-Time短縮や在庫低減と言った,企業体質(BS)向上への取り組みは,遅々として進まないのが各社の実情(これは日本も同じ).それ故,K社様の取り組みは画期的と言える.
3-4. 現場指導編
- 工場長(or責任者)が,現場の現状と改革の取り組みを現地で説明
- 弊社の指導は,以下の考え方で行った
中国には,飢えている人に
@ 釣った魚を与える ✕:依存心が生まれてしまう A 魚は与えず吊り具を与える △:壊れたらお仕舞い B 吊り具の作り方も教える ◎:自立できる という諺があります.
弊社はBの方式を採用し,漁場(現場)で魚(解決すべき課題)を見つける訓練をし,吊り具(解決する方策)を工夫させ,釣り上げて(問題解決)させて自信を付ける……という指導をしました.
具体的には現場での説明に対して『何故』『なぜ』『ナゼ』『Why』……と徹底的に質問して行き,『現地』で『現物』を見,その背景にある『実情』を聞きだし,それによって歪められている『実態』を確認します.その『実態』を『是』としてしまえば,『ミイラ取りがミイラになった』事になります.『上に政策あれば下に対策あり』の言葉通り,あるべき姿に向けての道を探っていくと同時に,粘り強く『実情』を変えていく努力も続ける……事を教え込みます.
- これにより,『自ら考え,自ら成す』人材を育成もして行きます.
- *『K社』様では,Topである董事長か総経理のどちらかが同行し,現場の実情・実態を把握した上でTopとして社内の制約条件の見直しを進めて居ました.
上記で,*印が『K社』様で初めて実現したものです.
[4] 新型コロナ発生!連絡途絶えるも,自力で目標達成!
10・11・12月と指導会実施し,順調なスタートを切りましたが,2020年1月から,新型コロナの発生で中国への渡航ができなくなりました.2〜3月は非常事態で,中国国内でも『K社』様と『佐吉諮問』の間の連絡もままならない状態になりました.4月以降は,危機は収まったものの人的移動は憚られたので,リモートワークを使って 河南省の『K社』様が上海の『佐吉諮問』と連絡を取り,時には日本の弊社にまで質問が届きながらも,ほぼ自力で成果を上げて行き,着手1年で所定の成果を上げました.
[5] 中国全土に向けて改革成果発表
董事長が中央政府と関係が深いこともあって,中国全土の『ものづくり改革』の参考になるとして,ネットを使って今回の活動の自動車事業部編を公開しました.
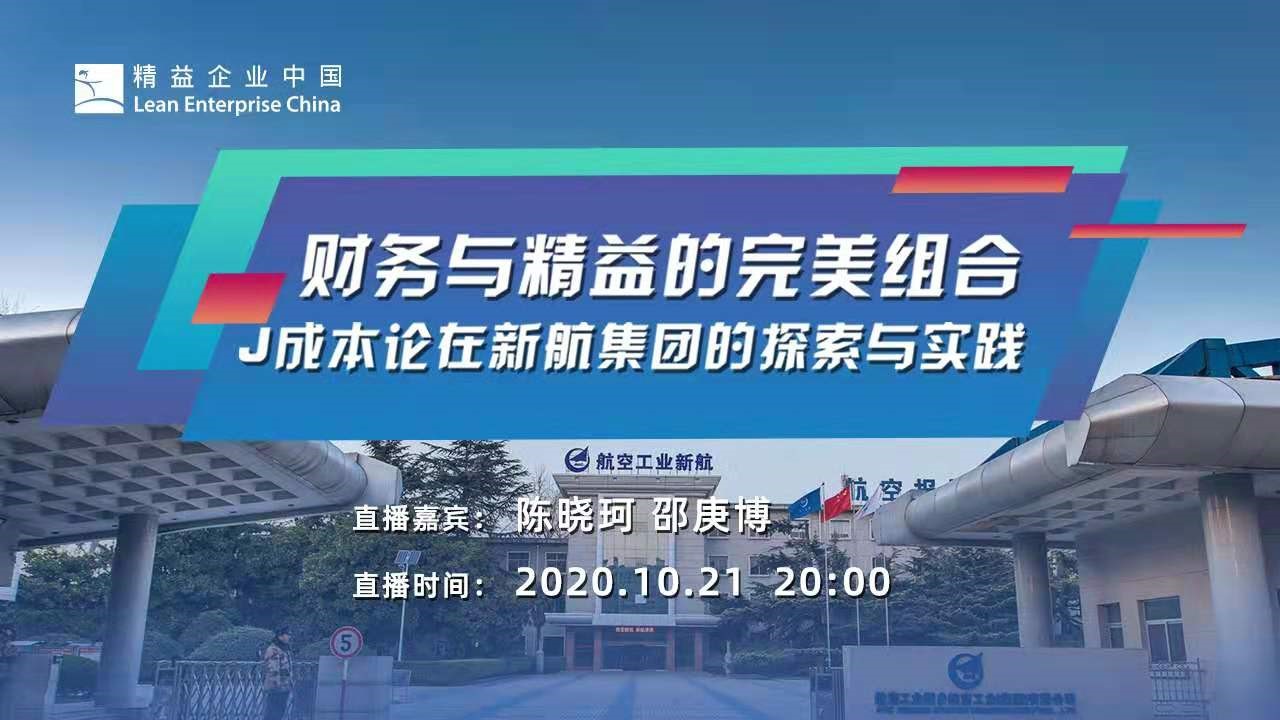
中身は中国語ですが,先ず女性の経理部長が登場し,2000年から自動車部品生産に参入し急成長を遂げてきたが,ここ数年は成長が鈍化し,在庫が気になる状況になってきた.新しい管理方法を探していたところ『Jコスト論』に巡り会った.昨年6月,上海でその研修会に参加し,導入を決めた.社内の推進体制を構築,9月から導入し改善活動に入った事を説明しています.
後半になって,自動車部門の事業部長(男性)が登場し,推進組織と具体的活動を説明,ある製品はTotal Lead-Timeが改善前285Hだったものを129Hに短縮した.その結果,基礎収益力が6.9から14.7まで向上させることができた……と発表しています.
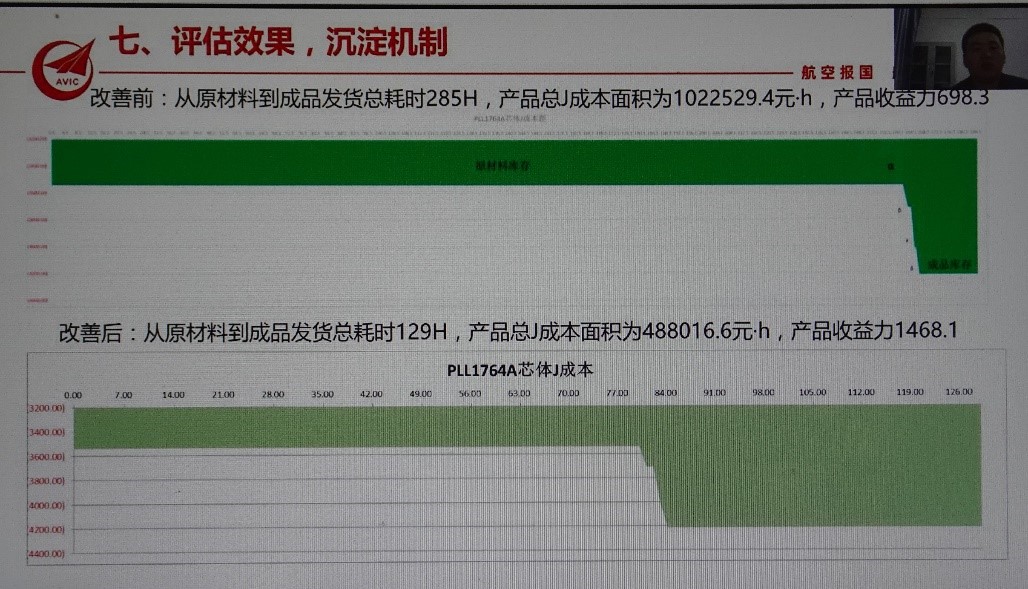
ここで言うTotal Lead-Timeとは,原材料検収から完成品納入までの所要時間で下記式から計算できます.
日本企業の年間実働250日で1日16時間稼働とすれば,4,000時間/年です.発表にあったTotal Lead-Time 129時間は棚卸資産回転数31回/年に相当します.
一方,『佐吉諮問』からは,各事業所の棚卸資産回転数の月々の推移グラフが送られてきました.自動車部品事業では下図のようになって居ます.
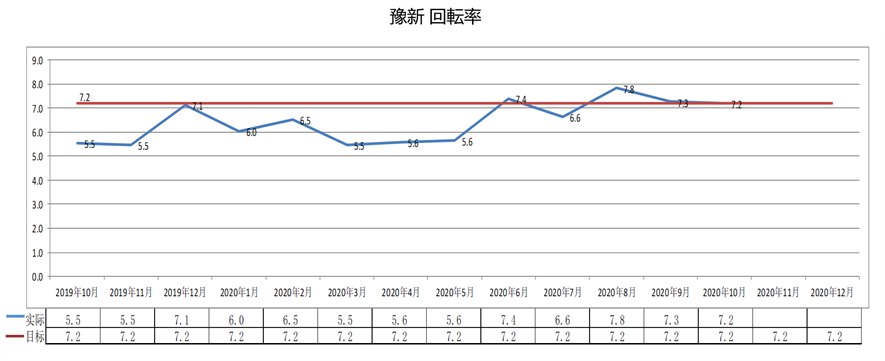
図から,事業所全体の棚卸資産回転数は,1年間で5.5回/年から7.2回/年へと,新型コロナによる大減産を経ても,目標通り30%向上していることが分かります.
皆さまの会社の現状は如何ですか……自社の財務諸表を出して計算してみて下さい.計算した上で,以下の文章をお読み頂くと,弊社がお伝えしたいことの真意をご理解頂けると思います.
[6] 弊社のコメント
6-1. とてつもない大改革です!!
ここまでにご覧頂いた資料は,現地に行けない状態なので,あくまでも伝聞情報です.図3にある棚卸資産回転数の推移を見てください.年間6回転から8回転というのは,日本で言えば中位の改善進んだ企業という位置付けになります.皆様の会社の今年に推移と比べてどうでしょうか?
1番凄いと思われるのは,新型コロナの中で,2〜4月は出荷量が大幅に減ったと思います.日本の自動車は40%減でした.中国でもほぼ同じ減産であったと聞き及んでいますが,その中にあって,改善着手時の『5.5回転』に踏み留まり,今年後半にはどんどんと在庫を減らして行き,5月から10月までの半年間で着手前よりも30%も回転数を上げたということです.中国に於いては自動車の売れ行きは好調だとされていますので,おそらく来年末には事業部として年間12回転まで持って行くでしょう.
貴貴社と『K社』様の,2020年度の棚卸資産回転数の推移を是非比べてみて下さい.
日本の企業では,回転数の絶対値が『K社』様よりもっと多いとしても,殆どは春からドンドン悪化していって居ると推察されます.今年末に年初の回転数まで戻っていれば,優良企業として『◎;二重丸』どころか『花丸』で評価されることと思います.
多くの日本企業は,コロナの影響で減産になった時にはかなり在庫を増やしていると思います.そして稼働率を上げるために,つまり会社としての利益を確保するために,その在庫をなかなか減らせないでいるというのが実情ではないでしょうか?
第2図の重点推進モデルとした製品の『Jコストモデル図』を見ますと,余りにも早く納入されていた原材料を,生産日に近づける改善をした事が分かります.ICTを駆使すれば,納品先(自動車会社)の生産計画で自社の原材料の枠取りをしておき,本番では得意先での自社製品の減り具合に合わせた『後補充生産(電子かんばん方式)』に近いSystemができるのですが……,現在日本でトヨタに納入している優良メーカーが,30〜40回転ですから,この部品生産で,そのやり方のひな形ができた(急所が分かった)という理解もできます.
弊社としては,早く現地を見て確かめたく思っております.
6-2. 中国の一般市民の活力を知るべし
幕末,ペリー艦隊に招待された江戸市民が,翌日模型を作ってきて現物と見比べていた.将来日本はアメリカにとって代わるのではないかと,ペリー提督の日記に書いてあったと聞いたことがあります.太平洋戦争後,支給された小麦粉でパンができると,伯父が両側に銅板を張った箱に重曹を入れてこねた生地を入れ,電灯の電源で焼き上げたものをご馳走になった記憶があります.今の日本にはそのような知的好奇心やバイタリティが欠けている気がします.
中国行って珍しいものを見ました.写真1は二輪車に取り付けた雨傘です.写真2は寒い中国の通勤に使う手作りの風防用半纏です.
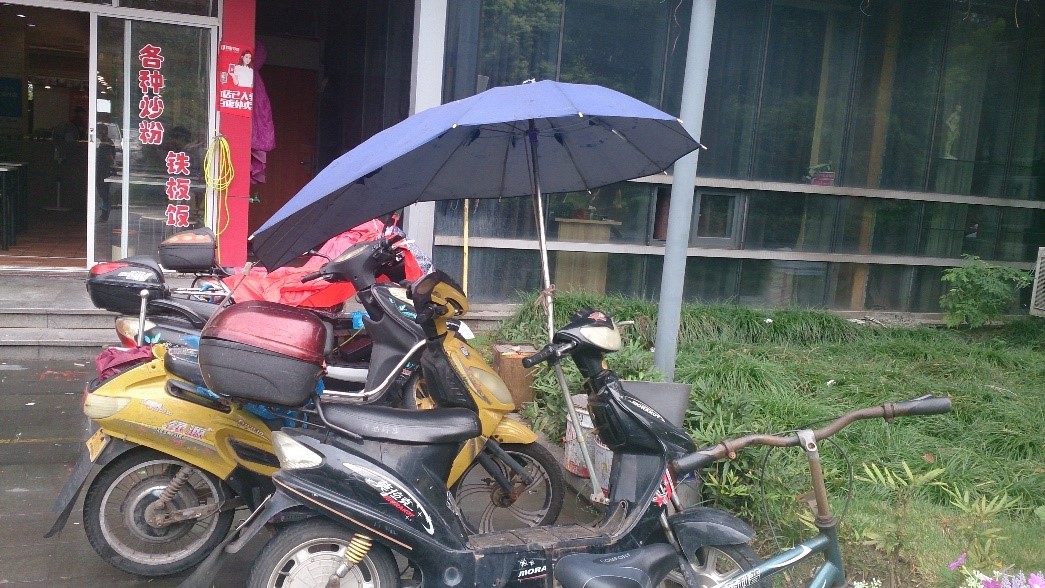
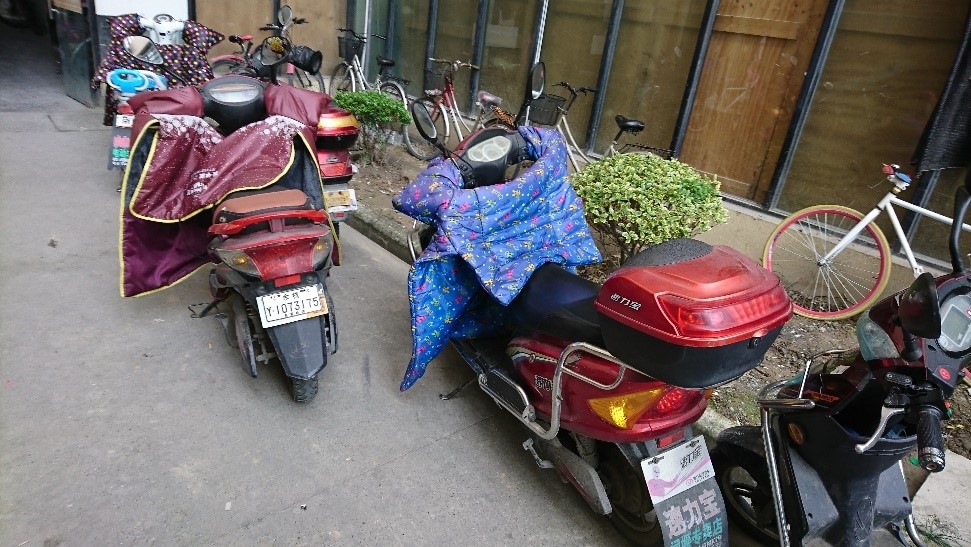
中国の街を歩くと,このような自分たちで工夫した様々な道具や料理に出会います.彼らは困ると何でも自分で作って問題解決します.『上に政策あれば下に対策あり』という諺は,実態をよく表現しています.
今の中国の活気はこの市民の『知的好奇心』や『バイタリティ』から来ていると思います.我々も何とかして,この市民の『力』を取り戻したいものです.
6-3. 中国人は東に住んでいるユーラシア大陸人……日本人は島人
中国に出入りし接した『中国系企業』も,『外資系企業』も,1人ひとりの仕事と責任は明確になって居て,成果は週単位で明確に評価されて居て,差は感じませんでした.
中国人の生活は,北部では主食は小麦粉で,肉を食べ,家の中では土足で椅子に座りベッドで寝て居て西欧と同じです.国境で他民族と接し,いざ戦争となれば,歩兵軍団と,騎馬軍団と戦車軍団が,将の命令で統率の取れた動きで闘います.この点はヨーロッパの民俗と同じです.
ただ東洋の文化として,身分の差が激しく宦官などという身分さえありました.女は男の所有物で,纏足などという風習もあり足が小さいほど美人とされていました.1949年の共産党革命によって,身分の差,男女の差を取り除かれた後,学校教育で徹底して男女平等を教え込んできました.もともと中国語には,男女の差や敬語はないので,男も女も上司も部下も納得するまで議論し,この点も西欧と同じです.
工場では女性は化粧していないので,丁度中学校の教室の雰囲気です.中国語の分からない者から見ると,言語能力に優れた女性陣が優勢に見えます.
因みに日本の工場での会議に,女性の姿は在りませんから,日中のものづくり産業の活力に差の一因は,『女性活用の差』にあると確信しています.
更に加えると,大学入試は1年に1回しかないそうで猛勉強しています.大学で勉強しようとしたとき中国語の文献が少ないので勢い英語文献に頼っていきます.スマホへの入力はアルファベットでしかできません.国内に外資系企業がいっぱいある等々,英語が浸透しています.現に通訳が席を外すと中国人は英語で話しかけてきます.要するに大卒の中国人は英語がペラペラなのです.それで,ネットを使って瞬時にして世界の最新情報を手に入れています.そのことを我々は考えておかねばなりません.
それ故,中国人を日本人と似ていると考えるのは間違いで,競い合う多民族が入り組んで住むユーラシア大陸人で,たまたま西に住んでいるのがヨーロッパ人で,東に住んでいるのが中国人と考えるべきです.
日本企業と中国企業の違いを感じた1つの例を説明しましょう.
Lead-Timeを減らすために,個々のSupplierからの直納をやめ,ミルクラン集荷を提案し時のこと,女性を含む数名の部長が,机を叩いて大議論を始めました.通訳は,「怒鳴り合い」に聞こえるかも知れないが,熱心に議論しているだけだと教えてくれました.程なく総経理を呼んできて,そこで又大声での激論が始まりました.最後に総経理から『斯く斯く条件でミルクランをやれ』と言う,具体的な業務命令が出されました.この間約2時間.翌週から実施されました.
その道のプロとしてヘッドハントされてきた人材が各機能の部長職に居るので彼等の合意が自社のその時の最善策であり,やるか否かは総経理が決める.そして,即決即断こそが企業経営の要という明快なLogicで運営されていました.
6-4. ここまでのまとめ
長い文章になってしまいましたが,中国企業が最近まで,安い人件費を武器に放漫な管理でも世界市場で有利な戦いをして勝ち進んできました.相手の米国は,多額の貿易赤字を抱え,失業者が出たとして悲鳴を上げ,2018年から米中経済戦争が始まり,中国からの輸出が滞り始めました.
共産党政権ですからウルトラCの手法を繰り出して国内経済は維持すると思いますが,個々の企業にとってみれば資金繰りが問題になり,今までのような放漫な経営では成り立たなくなります.
今回紹介しました『K社』様は,これを先読みし,在庫を絞った筋肉質の体勢に変えるにはどうすれば良いかと探し,弊社の『Jコスト論』に辿り着いたのでした.
『K社』様の強みは,董事長・総経理・経理部長が同じ問題意識を持ち,真剣に『Jコスト論』を学び,自ら先頭に立って会社組織を挙げ,一丸となっての改革を指揮したことです.その結果,従来の悪癖であった各工場(各事業部)をPL競わせる事をやめ,『棚卸資産の削減』という1点で競わせる事になりました.
上のフローで,【購買】や【営業】の事務処理は確かにまとめて行えば効率的に見えますが,今はERP(業務用Computerソフト)が処理します.全体を見れば,【購買】,【製造】,【営業】の3者が同じ速さであれば,在庫減ることは誰でも分かることです.それ故,最後のお客様が買って頂く速さに合わせて【購買】,【製造】,【営業】の業務を行えば棚卸資産は最小になります.
会社経営の現場では,様々な事情が入り組んでいて図のような単純なものではありませんが,『K社』様のTopはこれを経営の場での舵取りのノウハウとして掴んだということです.2021年度は,各業界のプロとしてヘッドハンティングされてきている【購買】,【製造】,【営業】の長が,これを競って具体的な実務体系へ展開していく事でしょう.
中国人はユーラシア大陸人だと言いましたが,その意味は,日本人なら生涯会社の為に滅私奉公するのですが,『大陸人』は『K社』様での業績を売りにして,更なる高みを目指して転職して活躍し,業界として幾何級数的高度化していく事が予想されると言うことです.まもなく迎える2021年では,中国はafterコロナ時代に入ったとして,飛躍的な発展を留めていくことと思います.一方我々はそれを,指をくわえて見ているわけにもいきません.我々日本人はどうするかについて,新年のご挨拶でお話しすることにします.今日ここに書いたことをお読みいただき,年末しっかりと来年度の貴社の取り組み方をお考えください.
最後に1年間のご愛顧ありがとうございました.皆様良いお年をお迎えください.そして,新しい日本を構築しましょう.
皆様良いお年をお迎えください.
2020年12月
(株)Jコスト研究所 代表 田中正知
2020年10月
季節のご挨拶
10月1日は中秋の名月です.煌々と照らす名月のもとで『お月見団子』を頂きました.
お月見というと 縁側にすだれを敷き,ススキの穂を立て,三方の上に団子を積み上げ,名月にお供えする風景を思い描きますが,最近の住宅では縁側がないため,このようなお供えがなくなってしまいました.
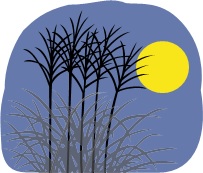
昔から,子供はお月様の使いであるとされ,この日だけは,名月へのお供えモノを盗んでよいとされていました.これを『お月見泥棒』と言い,子供会の行事になっていました.お供えのない家でも,この日のために菓子などを準備していて,口々に『お月見泥棒』と唱えてやってくる子供に与えます.子供達とご近所が奏でる微笑ましい行事です.
最近は,不気味な魔女や,カボチャのお化けを飾る得体の知れない『ハロウィン』が商業主義から打ち出され,グッズが店頭に並んでいます.聞けば古代ケルト族の悪魔崇拝に起源があるとか…….毎年この季節になると,外来の得体の知れない『ハロウィン』をやめて,日本民俗に基づいた『お月見泥棒』を復活して欲しい……と願っています.
8月になって梅雨が明けたと思ったら,今度は猛烈の暑さ!自宅 庭の温度計が40℃を越え,テレビでは,コロナだけでなく熱中症の注意が叫ばれていました.流石に私もバテ気味で,原稿書く元気がなくなり,つい8・9月はお休みとしてしまいました.申し訳ありませんでしたが,元気を出して又筆を進めます.
10月になって涼しくなり,元気を取り戻した皆さまには水を差すようですが,100年前のスペイン風邪では秋から第2波が更に強い勢力となって襲いかかり,10月がそのピークで特に若い人が重症となり大きなダメージを与えたとされています.特に欧米諸国は海流の関係で気候は比較的温暖ですが,緯度が非常に高く,冬は白夜と言われるほど日照時間は非常に短くなります.人の口から飛び散った唾液は空中に微細なミストとして漂い,紫外線弱い中では殺菌されず,空中に浮遊し続ける……と専門家は警鐘を鳴らしております.どうか,スペイン風邪の轍を踏まないように祈るしかありません…….
では,7月にお約束したように,以下の項の御説明を致します.
[4] 第1使命 管理体制確立させた上で徹底した在庫削減
ウィズ・コロナの期間は,感染が大波・小波と繰り返し約2年に亘ると言われ,業種によっては売上が平時の7〜8割まで落ち込むとされています.その間にも,御客様の好みが変わり,扱う商品が新しいトレンドに変わっていきます.極端な言い方をすれば,今ある在庫の銘柄が全部入れ替わる可能性があるということになり,現状在庫を最小限に抑える必要があります.
4-1. 原価管理体制を全部原価方式から直接原価方式に転向する
在庫削減をしようとする時,一番の障害は現場の『原価管理体制』です.今までの平常時は,限られた経営資源の中で,いかにたくさん作るか!ということを狙って構築した原価管理体制になっていますので,予定よりも余分に作ればその分が黒字になり,予定数量に達しなければ,赤字になるという仕組みになっています.
この仕組みのままでは, 在庫削減は不可能だと思うべきです.
それゆえ在庫削減をしようと思えば,まずは在庫削減すれば評価される方式の『原価管理体制』に変更する必要があります.これは工場だけではなく経理部門も含め全社で一緒になって取り組むべき課題です.
会計学が苦手という方のために 手短に御説明いたしましょう.
数ヶ月前,マスコミで『大手の企業が銀行から融資枠を取り付けた……』と言う趣旨の報道がなされました.如何に大手企業といえども,売り上げが減れば,資金繰りが悪くなり倒産の危機が有り,その先手を打って企業から銀行に融資の予約を取り付けておき,『支払いができなくなる事態を避けた』という報道だったのです.
つまりこの時期,全企業に降りかかる課題は,売上減の中如何にして『資金繰り』を確保するか,ということです.
企業が運転資金を確保する……というのは,人間の身体で例えれば,循環する血液量を確保するという事です.例えば,消化器系の大手術をする為に1週間余絶食することがありますが,点滴や輸血によって血液の量を保ち,循環を確保しておけば命に別状はありません.
一方,軽い傷でも血液の流出を止めなければどんどん血液が減っていき,死に至るのです.一番肝心なのは血液(企業を廻す資金)の量を確保するということなのです.
売上減という異常事態に対応出来る会計管理方法としては,減価償却費や間接費用を配賦と言う形で個々の製品の製造原価に上乗せして考えるフルコスティング(全部原価法)ではなく,現場で直接管理できる費用だけを現場で管理させる直接原価法(ダイレクトコスティング)が良いとされております.
直接原価法の一例として,2003年までトヨタでやっていた直接原価管理法の紹介をしましょう.
トヨタ式原価管理法(大野耐一氏主導の方式 2003年まで実施)
- (1) その特徴
-
トヨタ方式の根本原則は,売れた分だけ作る……にあります.
売れる量は極めて不安定ですから,
- @ 製造するときは全直投球させ,1個当たりの製造原価の推移を見ることで,現場の努力と実力を掴みます.
- A 注文が来なくて生産が止まった時間を顕在化することで,販売能力と 自社の工場における製造能力とのギャップを把握します.
- B 製造能力が高ければその能力を生かして拡販に持って行くのか,新製品の開発に持っているのか,経営者の責任と捉えます.
因みに上記@ABを体系づけて論じたLean-Accountingが研究され,書籍(英文)になっています.
- (2) 絶対評価ではなく相対評価(日々の成長を評価)
-
A,B,Cの3工場で甲,乙という製品を作っていたとします.
普通の会社では,製品甲,乙の 標準作業時間,標準材料使用量は本社で決め,実績でA,B,Cの工場を評価します.
トヨタでは,A,B,Cを3軒の家の一子,二子というように捉えます.身長,体重は違って当然.成長する力も違って当然.
大事なのは日々どのように成長しているのか,です.改善への取り組みとその成果を……つまり,月々の変化率を評価します.この評価方法が,職場の元気・活気を醸し出すのです.
- (3) より具体的 に言えば
-
\begin{equation} 労務費 = 実績直接作業時間 [\mathrm{s}] \times 標準レイト [\mathrm{s}] (製品1個あたり) \end{equation}
ここで,
\begin{equation} 総時間 [\mathrm{s}] = 出勤人員 \times (定時 [\mathrm{s}] + 残業時間 [\mathrm{s}]) \end{equation}\begin{equation} 生産時間 [\mathrm{s}] = 総時間 [\mathrm{s}] \times 0.92 - 他責時間 [\mathrm{s}] \end{equation}8%は教育など生産以外に使う時間です.また,他責時間は他工程の責任で停止した時間で,減産分も含まれます.
\begin{equation} 実績直接作業時間 [\mathrm{s}] = 生産時間 [\mathrm{s}] \div 検査合格数 \end{equation}
\begin{equation} 材料費など = \sum (標準材料原価[\mathrm{kg} ^{-1}] \times 実績使用量[\mathrm{kg}]) \end{equation}一旦,細部の使用実績を明確化して評価する.
但し,当時のトヨタはかんばん方式により,徹底して在庫低減をはかる仕組みになっておりました.
このトヨタの例は,コロナ禍による減産になかでは何処の会社でも参考になると思います.
4-2. 在庫量の尺度を『滞留日数』で統一する
従来の生産計画においては生産の単位を 『○○万個』だとか,『▽千個』とか丸い数字を使っていると思います.しかし 在庫を本当に減らそう考えるならば,今ある在庫は何日分あるのかと言う捉え方が1番大事になります.例えば在庫後補充生産方式で,毎日すべての製品を後補充生産するのであれば,バラツキを考えて完成品在庫が1.5日分あれば,欠品せずに廻すことが出来るでしょう.
このように在庫を,「金額や個数」ではなく『滞留日数』で把握することにより,誰にでも次にどのような行動をとるべきか,自ずとわかるようになるのです.
4-3. 小ロット多回生産に挑戦する
具体的にはどうすればよいのか,考えてみましょう.
例えば今までは何も考えずに1万個単位で生産したとします.ここに先の『在庫滞留日数』という尺度を導入します様子が一変します.
1万個とは,製品Aとってみればそれは滞留日数3日分であるかも知れませんが,製品Bにとっては10日分だったりします.製品Cでは何と50日分にもなっていたりします.
当然,先に紹介したように,前日に売れた分だけ後補充する場合という考えが出てきます.これが1つの模範解答であるのは間違いありません.
しかし,多くの場合,生産する時に製品Aから製品Bに生産を切り替えるとき,段取り替え(準備)時間が掛かります.
一般公式として,1ロット($m [\mathrm{個}]$)を生産するのに要する時間を$T [\mathrm{s}]$とすれば
という式が成り立っていて,多くの場合 全商品を生産すると,段替え時間がNeckとなり 後補充しようとする数量が生産出来ません.
その場合,各製品に対して,それぞれ 最大在庫量・最小在庫量を決めておき,最少在庫量にまで減った順に,最大在庫まで生産するというやり方をします.
当然,売れ筋の製品は毎日生産し売れないものは数日分まとめて作るということになります.通称ロングテールと言われる,売れ筋でない製品の在庫量は出来るだけ絞り,在庫量を多く抱えても直ぐに売れていく『売れ筋の製品』の在庫を多めにすることで,Totalの在庫量を縮小していけることが分かって来ます.さらに限界に挑戦し続けることから『段取り替え時間』は現場の工夫と訓練によって,段々と 短縮できるようになって行きます.
常に限界に挑戦するという姿勢でこの取り組みを行うことに依って最終的には驚異的なほど在庫を減らす事が出すことができるのです.同時に,現場の規律とやり甲斐,達成感も醸し出されるのです.
在庫管理の詳細は,本HPの連載コラム『Jコスト改革の考え方』 第9回目を参考にしてください.
4-4. 在庫管理の見える化と日々の管理
中国の古典に『入る』を量り『出る』を制すべしと言う言葉があります.本来は,『国を治めるに当たっては,歳入をしっかり把握して,それで賄えるように,歳出を抑えろ!』という意味で,国家予算の10年分の赤字国債を抱えている日本政府のようになるな!と言う警告なのですが,此処では,会社の実態に合わせて 週次の生産計画であるとすれば『今週の売上金額の枠内で』『来週を予測して』原材料を調達せよと捉えて頂きたく思います.
今週に比べて来週は売り上げが1割減ると予測された場合,MRPを使っての資材調達では,1割減で発注してしまうと思います.しかし,完成品在庫もあるわけですから,その在庫も又1割が削減しなければいけませんので,一口で言えば2割削減する事が必要となります.
見える化の方法は多岐に亘り,此処では言い尽くせませんので,このHPにある『Jコスト改革の考え方』を参考にして,御社に見合った方法を工夫して下さい.
最近では50インチの4Kテレビが10万円台で売っています.中古のスマホが極めて安価に入手出来ます.社内にNetを張れば,極めて安価に,生産管理,入出庫管理をリアルタイムで把握し,全員で共有する仕組みが構築できます.
こう言った自前のツールを使って,市場の変化に最小の在庫で,素速く対応する仕組みの構築が,御社のコロナ禍に中での生き延びる術なのです.
4-5. 在庫管理(生産管理)Systemの再構築
2020年全世界を襲ったCOVID-19パンデミックは,各国の行政の抱えている問題点を白日の下に曝け出しました.
職を失った人々への補助金を支給するのに,申請したら3日以内に届いたという在外邦人のインタビューがある一方,3ヶ月しても届かないという東京都民の訴えが報道されたり,総理大臣が,感染か否かを判断するためのPCR検査が,直ちに受けられるようにすると国会で答弁したのに,4ヶ月経っても,主治医が申請しても後回しにされ,症状が悪化してから検査が受けられる良いになった……等々.日本の行政システムが, いかに時代遅れであるかということが露呈されました.
マスコミは,日本と欧米諸国と比較して議論していますが,私は75年前までは日本領として同じ行政組織であったハズの『韓国』と『台湾』との差を問題にしたいと思います.
試金石として,『トップの座に女性が就任したか否か』を採用すれば,韓国は先代の朴大統領は女性でしし,台湾の蔡総統は2期目の女性総統です.『コロナの新規感染者数』を採用すれば,台湾はゼロを続けており,韓国は64人,日本は571人(2020年9月30日)となっています.このように,国の行政組織の遅れは明らかで,新たに発足した菅内閣が『デジタル庁設置』や『押印制度の見直し』を前面に出して取り組み始めた事に期待したいところです.
『生産(在庫)管理体制』に話を戻しましょう.
私は『上の好むところ,下自ずと風をなす』という言葉が好きでよく引用しますが,その意味するとことは,何事も上位組織のレベルの影響を受けに下位組織も同じレベルになりやすい……という意味です.
国の行政組織が遅れていれば,民間企業の事務処理も同じレベルに留まっている……だから1980年代世界で冠たる活躍をした日本企業も,今は時代遅れで,韓国や台湾に後れをとっている……と,全世界のビジネスマンが疑念を抱いていると考えるべきです.
コロナ前は,『日本企業だから安心だ』と思われていたのが,コロナ後は『日本企業だから心配だ……』と思われて始めた と考えるべきです.一刻の猶予もありません.コロナ前に思われたと同じレベルの日本企業としての,在庫管理をはじめとする会社の事務処理能力を,世界の最先端レベルまで持って行くことが,アフターコロナに向けての最大の改革目標になります.
改革向けての参考になるように こうなってしまった原因について考えてみましょう.その1つの原因は入社(採用)制度にあると思います.
『野球』を例にとって考えてみましょう.プロ野球はもちろんのこと,実業団野球においても,新人を採用するに当たっては,出身校名ではなく,実際に甲子園でどの程度活躍したか?6大学でどんな実績があるのか,個人の能力を見定めて採用を決めております.その結果入社して即戦力になるし,他の球団に移籍しても,即戦力という選手たちが活躍しているわけです.
一方,全世界の強豪企業と競い合っている企業の,競争力の一つの鍵でもある事務業務,例えば『生産管理』について考えてみましょう.高校でも大学でも『生産管理』について専門知識は一切教育されていません.全くの素人の学生を,学校名だけを頼りに採用し,即戦力に使っているのが日本企業の実態です.その結果,職場の先輩から教えられたことをいかに『忠実に実施するか 』ということだけ汲々としており,世界の競合他社と比較して自社がどうか,あるべき姿とどんな乖離があるか,ということを考える暇ありません.言い換えれば日本の各社の『生産管理』は,先輩から代々の言い伝えて頼っていて,『伝言ゲーム』で実証されているように,伝える毎に劣化しています.私はこれを『隠れキリシタン現象』と呼んでいます.
因みに,正規に再教育された人々は『潜伏キリシタン』として苦難に耐え信仰を守り向いたとしてカソリック教徒から賞賛されていますが,再教育を拒んだ集団は『隠れキリシタン』として異端扱いになっていると聞いています.
このように,表に出にくい事務部門の業務は,競業他社と定期的に比較検討しないかぎり,すべて『隠れキリシタン現象』にある……と思っています.もし,御社の自己資本費利率が高く,銀行の監査が入らない状況であれば,『隠れキリシタン現象』は重症である……と思って間違いありません.
改革志す皆様にオススメしたいことがあります.それは皆様自身がクラウド型ERPをサブスクで入手し,自社の業務処理方法と比較することです.
日本でERP(事務部門の業務全般を電算化したもの)を導入した1990年代は,「世界に冠たる自社の業務処理方法は,市販のソフトでは動かない」として,代々受け継いだ各社の業務処理に会わせた専用ソフトを数十億円掛けて開発し,導入していました.
20余年経った今日,経営環境は様変わりし,ICT(情報通信技術)が格段の進歩を遂げています.それに伴って,世界各社の業務処理が激変してきています.
消費者レベルでの一例として,中国での経験を紹介しましょう.飲食店では,店に入り,テーブル上のQRコードを読むとスマホ上にメニューが写真と詳しい説明が掲示され,それで注文します.食べ終わった後レジで,スマホで口座情報を掲示することで勘定を済ませます.タクシーを呼ぶには ,ネット上の「自動車の型式」と「運転手の評価」の一覧表から乗りたい車を選ぶと,運転手につながり, 何分後に到着するかの確認が出来ます.目的地に着いたら,代金決済も スマホで行い評価も追記します.これらスマホを通じた商取引はNet上に保管されているので,不正も防ぎます.
このように21世紀になると日本にいては想像できないほど,世界の商取引は日々劇的な進化を続けているのです.
2020年全世界を襲ったCOVID-19パンデミックは,感染防止のために全世界でテレワークを余儀なくされました.ICTを使いこなして業務改革を進めてきた企業にとってはテレワークは,さらなる改革のきっかけとなり,ますます生産性を上げて行くと思います.
一方,今までの事務処理方法に固執している企業にとっては,テレワークは晴天の霹靂だと思います.例えばA氏は出社して事務机に向かい,回覧書類を読み,喫煙室で仲間とだべり,未決箱の書類に目を通して押印する……仕事をしていたとします.A氏は,テレワークは無理……と主張するでしょう.しかし,高度100bから自社の業務を鳥瞰すれば,A氏は業務の流れを滞留させるだけで,何の付加価値もない事が明らかになることでしょう.
私がこう主張するには背景があります.1988年からトヨタではTop主導で『ハンコ三つ』運動が展開されました.平社員が起案するような案件ならば「係長⇒課長」で発効,部長が起案するような重要案件ならば「担当役員⇒常務」で発効,といった具合でした.2000年から勤務した半官半民の組織では,何と『ハンコ16個』でした.誰がどの部分を確認するのか不明のまま,押印欄に16個の印章が並ばないと発効しません.最低で一週間掛かった覚えがあります.
世界の最先端の生産管理Systemが,自社のそれとどんな差があるかを見るためには,一つの手段として,21世紀になって急成長した中国をはじめ東南アジア諸国が活用しているというクラウド型ERPの研究をお勧めします.サブスクリプションとして数万円/月で誰でも使える状態です.あるソフトウェアの専門家の話では,日本では数十億円かけて自社独自のERPを作ると言う風潮があるため,安くて済むクラウド型のERPは日本では一切,宣伝しないことになっているそうです.
『敵を知り,おのれを知れば百戦危うからず』敵が使っているというクラウド型ERPと自社の現在のやり方を調べ上げ,自社との業務展開の違いを確認するところから,御社の改革はスタートすべしと考えます.その上に立って,最小の在庫で回す仕組みを構築して下さい.
次回は,以下のことをお話しします.
- [5] 管理者としての第2使命 人財の育成
-
- 5-1. 自社のKeyとなるノウハウの伝承
- 5-2. 一般技能の伝承
- 5-3. 資格者の確保
- 5-4. 企業人教育
- 5-5. 後継者の育成(5年後の姿)
- [6] 管理者としての第3使命 職場管理体制の再構築,Value Stream Map(モノと情報の流れ図)
-
- 6-1. 現状確認
- 6-2. 『安全』『品質』『生産』の自律管理体制として再整備
- 6-3. 通信Net再点検
2020年10月
(株)Jコスト研究所 代表 田中正知