連載コラム『Jコスト改革の考え方』目次
JBpress連載コラム『本流トヨタ方式』
ビジネス情報サイトJBpressにおいて、2008年から2013年までの間に合計104回のコラム 『本流トヨタ方式』 を連載していました。
現在連載中のコラム 『Jコスト改革の考え方』と併せて読んで頂くと、より深くJコストの考え方がご理解頂けるかと思います。是非、下記のリンクにアクセスしてみて下さい。
過去の所信表明
2020年7月
季節のご挨拶
2020年,オリンピックの年として新年を迎えた直後から始まった,新型コロナ騒動,マスク不足を始め,医療機材不足,医療崩壊の懸念,一斉休校,緊急事態宣言,移動自粛とテレワーク,営業自粛等々を経て,日本の感染者は幸い少なくて済み,下火に向かい,お陰様で6月19日から,様々なコロナ対策の自主規制が解除されました.最近感染者がジワジワと増えているのが気がかりですが….
この約半年間,管理者の皆さまは,ご家族の安全と,預かっている職場の異常事態への対応で大変なご苦労をなさったモノと拝察致します.お疲れ様でした.
しかし,水を差すようですが,ここまでの皆さまの対応は,緊急避難として外部から強制され否応なしにやってきた部分が多く,各社・各職場でその対応にはそれほど差があるとは思いません.
今からの対応で,大きな格差がつくと覚悟を決めてください.
7月に入り,東京ディヅニーランド(TDL)が再開したというニュースが賑わしていますが,待ちわびていた来場者は,充分にコロナ対策した上での新しいおもてなしに驚きと新たな感動を味わっていると報道されています.
TDLは閉ざされた空間での数時間の世界ですが,の皆さまの会社では,自由市場に向けた開放空間で,時間制限無しでサービス競争を続行する業態にあると拝察します.その難しい中で,どうアフターコロナの体制を構築するかが,管理者である皆さまのお仕事になります.今回は此のテーマに具体的にどう対処すべきかを考えたいと思います.
今一度スペイン風邪から学びましょう
以前にも言いましたが,今回のCOVID-19パンデミックは,100年前の『スペイン風邪』が免役もない疫病として参考になります.
第1波 | 1918年3月〜6月 | 北米・欧州 | |
---|---|---|---|
第2波 | 1918年秋 | 全世界 | 重篤な合併症を起こし死者が急増 |
第3波 | 1919年春〜秋 | 全世界 | 最初に医師・看護師が感染⇒医療崩壊 |
世界 | 日本 | |
---|---|---|
推定感染者数 | 人口の25〜30% | 人口5.5千万人中2.4千万人 |
推定死者数 | 0.17〜1.0億人 | 39万人(1.63%) |
更に,別の資料では,第1次世界大戦(1914年6月〜1919年11月)の中で,主戦場であった欧州大陸に参戦した米軍兵士から全戦線の敵味方全軍に感染が広がり,敵と戦いながら,スペイン風邪と闘う事態となり,終戦を早めたと言います.又,戦死か病死の区別は,参戦国同士の機密とされ,スペイン風邪そのものの詳細な実態は不明とされています.
一方,米国は,主戦場の欧州に武器,弾薬,食料を売り付けることで巨万の富を手にし,戦後は世界経済の中心に躍り出て,大繁栄したのでした.世界史的にはPax BritannicaからPax Americanaへの変換点でもありました.行き過ぎた好景気が1929年の『世界大恐慌』を巻き起こし,それが起点で世界各国の経済が破綻の危機を迎え,自国さえ良ければ…と過度な保護貿易に走りました.経済的に困った国ではファシズムが台頭して来ます.1930年代後半になるとあちこちで紛争が起き,ついには1939年第2次世界大戦に突入するのでした.1930年から米国ではニューディール政策が打ち出され,多額の公共投資が行われましたが,効果が検証されないまま大戦に突入し,戦争が一番の不況対策だったとも言われています.この伏線として,スペイン風邪の第2波は若年・壮年(65歳以下99%)にサイトカインを起こし死亡者が多かったことで,人口構成に大きな歪みを与えたこともその原因の一つに挙げられ,影響は20年余続いたという説もあります.
現実を直視し覚悟を決めましょう
このスペイン風邪の例から推定されるのは,北半球⇒南半球⇒北半球⇒南半球と,冬季に流行,夏季に収まるを繰り返し,2年間は全世界で第2波,第3波が来ると覚悟しなければなりません.無観客ではオリンピックになりませんから,中止となるでしょう.
自社で出来ることは万全を期しても,このように2年間はパンデミックの中に居るとすると,皆さまの市場は激変すると思います.単に需要の変化を考えても,日々の生活に必要なモノは直ぐに回復しますが,必需品で無いモノは,先行き不安な世相から,客足は遠退きがちになります.
一例を挙げますと,結婚式と卒業式の記念撮影は,人生の区切りとして大切に考える様ですが,貸衣装で済ますことが出来るようになって居ることまでは承知していましたが,最近では『メルカリ』を使って,一寸したお出かけの服装一式を,プロのデザイナーがコーディネイトしたモノを送ってもらい,使い終わったら又ネットで売るのだとか….市場は日々劇的に変わりつつあると痛感した次第です.
従来から,一つの事件によって消費市場が急変することが知られています.日本では1932年冬に起きた日本橋白木屋百貨店火災が有名です.初めての8階建ての高層ビル火災の経験から,消防関係に大きな影響を与えたと言われますが,もっと有名なのは,救出されるとき,乱れた裾を直そうとして片手を離した多くの女性が落下して命を失った…という噂が広がり,瞬く間に女性の下着が腰巻からズロースに変わったと伝えられています.都市伝説だという説がありますが,あるトレンドであったものが,一つの切掛けて一気に広がったと理解すべきで,下着業界にとっては天から降ってきたビジネスチャンスであった事は間違いありません.波に乗れた店と,外した店では大きな差が出たことでしょう.
自社のことは,自社社員の力でしか対処出来ない
少々前置きが長くなりましたが,今直面しているCOVID-19パンデミックは,先ず1〜2年続くという事を覚悟してください.そして通り抜けたトンネルの先は,今までと違った景色になって居るということです.従って扱う商品は様変わりし,何をどう扱うか…は各社違いますから,皆さま御自身の才覚で道を開いていかなければなりません.
これとは別に,職場をどう運営するか,部下をどう育てるのか等は現場を預かる管理者として,一般論として,管理職の皆さまどちら様にも当てはまるお話しですので,今回はこれについてお話ししたいと思います.
それは,今まで2回に分けて説明してきた,改善に向けてのキャッチコピー
- 【A】「常に『目的は何か?』を問い直そう」
- 【B】「ぶつかった壁は『人が作った壁か?神様が作った壁か?』を考えよ!」「人が作ったモノなら変えることが出来るのだ」
- 【C】「ルールは変えるためにある」
これを皆さまの職場に展開しては如何でしょうか…という提案でもあります.
管理職である皆さまが心すべき事柄
[1] この時,管理職に居ることの意味を知るべし…
管理者である皆さまは,御自分の担当する職場の要所要所に,それ相応の人材を配置して業務を遂行していることと思います.その部下が,上司であるあなたの顔色ばかり窺っていたら,あなたは残念に思い,降格を考えることでしょう.
中国の三国志に『赤兎馬』という名馬(≠焼酎)が登場しますが,元々はパワー溢れる暴れ馬でしたが,呂布という名将が乗りこなして大きな軍功を挙げるのでした.乗りこなすとはControlすることで,制御と書きます.『制』も『御』もブレーキを掛けるということです.戦場で命を託する愛馬も,部下も同じで,自分の信念でバリバリ働く部下が頼もしく,行き過ぎがあったら,そこだけブレーキを掛ければ良いとして,存分に活躍してくれるのを待っていると思います.同様に,あなたの上司は,あなたを得がたい人材として今の職に任じ,存分の活躍を期待していると思わなければいけません.
上司と部下の関係に関連したEpisode
TOC(Theory Of Constraints)の創始者であるイスラエル人の物理学者Goldratt博士は,トヨタ生産方式(TPS)をまとめ上げた大野耐一氏を尊敬して居ました.その彼は『一人の男が,世間の常識に逆らって,己の信じる道を貫き,TPSをまとめ上げた事は,現代の奇跡だ!又,信じる道を突き進む部下を,万難を排して守り抜いた上司も奇跡だ.もっと大きな奇跡は,突き進む男と守り抜く経営者が30年間同じ会社で,上司と部下の関係で居たことだ!』と評したと聞いています.
『英雄は英雄を知る』という事なのでしょう.
今,COVID-19パンデミックの中であなたが管理職で居る意味を自ら見つめ直す時です.今この時,この職に居る自分に,上司は何を期待しているのか…?正に『自分がこの職に居る目的は何か…?!』『今のやり方はその目的に合っているか…?!』を自らに問うて頂きたく思います.
[2] 管理者の犯しやすい「行い(罪?)」
管理者の犯しやすい「行い(罪?)」には以下の2つがあると,先輩に諭された事がありました.具体的な例で説明しましょう.
(A) 不作為の作為
自動車には運転免許証が必要な様に,現場には,法律で定められた資格者が従事する必要があります(例:危険物取扱,高所作業,玉掛け…).前任者から,「全て資格者が作業している」という申し送りを受けて,鵜呑みにして1年過ごした状態が『不作為の作為』という『行い(罪?)』なのです.
本来は就任と同時に,その現場に有資格作業の現状と,有資格者状況を調べ,成り行きで行けば,何年持つのかを確認の上,自分の在任中に何人育て上げるようにするかの意志決定し,計画的に資格を取らせている…のが,正常な管理者の務めなのです.
もう一つの典型例は,場内外注業者管理の問題です.創業時には自社社員が行っていた作業であるパレットや木箱等の修理と補充,型保全,場内清掃から保守点検等々,更には場内運搬や塗装工程までが,社外の人に移されて(場内外注化)行ったのですが,現場に密着して作業の授受が,監督者レベルでおこなわれる為,管理し難く,『癒着』が起きやすいのです.
更に拙いことに,『外注化』すると,費用区分が個々の製品の『製造原価』から工場全般に掛かる『一般管理費』に変わるので,『製造部門が頑張った…』様に見えるので,ついつい泥沼に足を踏み入れてしまいがちです.内・外製…特に場内外注は管理者として厳しく見直すべき項目です.
(B) 未必の故意
先の資格者で言えば,調べたら『半年以内で数名が定年退職する』と知った上で,それを放置したときに,これを『未必の故意』と言います.
『通路に陥没がある・・・』『不良の再発防止をしていない』等々,管理者として当然やるべきことを,やらずに過ごしている状態を言うのです.管理者として絶対あってはいけないことなので,この行いは『罪』です.管理者は刑事罰,民時罰も覚悟しなければなりません.
(C) お役所仕事
約50年前,係長に昇格したとき,社内教育で叩き込まれたのは『役所と民間企業との違い』でした.『役所では,決められて仕事を決められたようにやっていれば,何が起きようと法律が役人を守ってくれる』<註:決められたこととは,法律と先輩に教わった事柄を指します.>『民間企業では,法律より上位に「御客様」が居る.御客様のご機嫌を損じたら,会社ごと潰れる場合もある.「速さ」と「品質」と「価格」で御客様の『満足』を得るように全力で取り組まなければなら無い…』ということでした.
今回のコロナ対応で,『お役所仕事』オンパレードを見せつけられて唖然とし,アベノマスクに至っては,怒りを通りこし嘲笑になってしまいました.『納期遅れ』『毛髪等の混入』『不明朗な入札』民間企業なら倒産するほどの不祥事が起きましたが,担当部署の責任者処分は一切無く,国会答弁では『スピード感を持って適切に対処する・・・』といういつもの呪文を唱えるのみでした.
民間会社の管理者は人事権もあるので,異常を兆しの段階から捉えて現場を観察し,絡み合っている業務を解きほぐし,円滑に機能する様に組織を再構築する責任を負います.持てる職権を最大限発揮して早期解決が職務で,言い訳は出来ないと覚悟しなければなりません.あなたがモタついていれば,上司がメンバーチェンジすることでしょう.
(D) 『自分の城は自分で守れ』が民間会社の生きる道
『自分の城は自分で守れ』とは,1950年資金繰りが悪化し潰れかかったトヨタの社長に就任し,徹底した経費節減で資金を貯め,無借金経営の基礎を作り,銀行に左右されず,自らの判断で思い切った投資をして,今日の基礎を作ったと言われる,石田退三氏の著書名でもあり(1968年講談社),座右の名でもありました.
1970年代係長教育で,叩き込まれたのは,以下のようなモノでした.
日本国憲法では,いわゆる『生存権』等々様々な基本的人権が謳われていて,個人が困難に陥った場合生活保護,医療保護等,手厚く保護されるが,民間会社が投資に失敗しても,火事で燃えても,助けてはもらえない.
これは,【B】の『神様が作ったのか?人間が作ったのか?』の文脈からも.『人の命は神が創った…』『会社は金儲けを狙って一部の人が作…』とすれば困ったからと言って関係ない国民が払った税金を使って助ける理由にはならないのです.正に『自分の城は自分で守れ』なのです.それ故,民間会社の管理職は,経営者を助け,従業員の生活を守るという重責を担っていて,留まれば窒息死,慌てれば転落死という状況の中,足許を見定め,一歩一歩確実な歩みを続けるしかないのです.
以上,管理者としてあなたは(A)不作為の作為,(B)未必の故意,(C)お役所仕事に陥らず,(D)自分の城は自分で守る道を歩んでいるか,自らの仕事を常にチェックし,自らを律して行かねばならないのです.
[3] コロナによる需要減を,管理者はどう捉えるべきか
3-1. 職場改革のチャンス到来と喜ぶべき
管理者の皆さまは,今まで『品質』『納期』を守りながらいかに『原価』を下げ会社に利益をもたらすかに日夜心を砕いて来られたと思います.更に良い状態にするためにやるべきこと,やりたいことがあったとしても,管理者として自由に使える工数がなく,悔しい思いをして来たと拝察します.
サッカーやバスケ等のプロスポーツは,シーズン中には出来ない大改革をシーズンオフの間に,選手個人も,又チ−ムとしても行い,これが翌シーズンの成績に直結するとして頑張ってやっていると聞いています.今回のコロナによる需要減は,その後の急成長を見越しての減産になりますから,ある意味,このプロチームのオフシーズンに 似ています.この機に,かねてやりたかった組織としての改革を成さないと,アフターコロナの市場で敗退を余儀なくされると思わなければいけません.
3-2.減産規模と期間を読む
新聞に拠れば,株主総会でトヨタ自動車が2021年3月期の予測として,最悪60%台まで落ち込むが,年平均では80%台に踏みとどまる予測で,固定費削減の努力が実を結び,5千億程度の営業利益を出せると豊田か社長が公言しました.敢えて公言した真意は,全世界で直接取引のある数千社,間接的には数万社に及ぶ関連会社に,狼狽えることなく各社が2021年度の行動計画立案し,アフターコロナに向け着実に改革してもらう為だとのことでした.
では,皆さまの会社では,今年1年間の需要をどのように予測しているのでしょうか?代理店や販売店へのアンケート調査では,大失敗します.御社自らが他社製品も含め市場の様子探求し,購買層の経済状態までも勘案の末,製造会社としてのマインドで需要予測をする必要があります.
3-3.品名が同じでも仕様が変わる
特に注意すべきは,約2年は掛かると言われているコロナの流行中に,市場のトレンドがガラリと変わってしまう可能性があるという事です.
例えば,大型乗用車のミニバンは,従来は家族揃っての長距離ドライブが使用目的でしたが,リモートワークが本格的になると,家が手狭で落ち着いた仕事場が欲しくなります.そうすると2列目に通信機器を備え,デスクとして使える機能を持ったミニバンが,サラリーマンの間では流行る事でしょう….等々,従来にない新機種が持て囃されるようになる事でしょう.ということは,コロナの減産は新製品への切り替えの減産と考えてとり組むべきだと理解出来ると思います.
ここまで管理者としての心構えを中心に長々と説教めいたことを述べてきました.少しでもお役に立てば幸いです.
次回は管理者としてなすべきことを以下のような柱立てでお話ししたいと思っています.皆さまの職場でやらなければいけないことは,管理者としての皆さま御自身が一番分かっていて,既に計画を立て,着着と実施されていることと思います.来月は,以下の項目をお話しさせて頂きますが,それを読んで,皆さまが管理者としての自信を深めて頂ければ幸いです.
- [4] 管理者としての第1使命 在庫管理体制確立
需要減になると,在庫を抱えてしまい運転資金が枯渇して倒産に至ります.経営者は銀行を駆け回り,現金を準備しますが,現場の管理者の使命は,徹底的な在庫圧縮にあります.
- 4-1.在庫量の尺度を『滞留日数』で統一する
- 4-2.小ロット多回生産に挑戦する
- 4-3.在庫管理の見える化と日々の管理
- 4-4.在庫管理System構築(クラウド型試行)
- [5] 管理者としての第2使命 人財の育成
- 5-1.自社のKeyとなるノウハウの伝承
- 5-2.一般技能の伝承
- 5-3.資格者の確保
- 5-4.企業人教育
- 5-5. 後継者の育成(5年後の姿)
- [6] 管理者としての第3使命 職場管理体制の再構築
Value Stream Map(モノと情報の流れ図)
- 6-1.現状確認
- 6-2.『安全』『品質』『生産』の自律管理体制として再整備
- 6-3.通信Net再点検
2020年7月
(株)Jコスト研究所 代表 田中正知
2020年6月
季節のご挨拶
先回このコラムを書いた直後の4月7日に政府から東京圏・大阪圏に対して緊急事態宣言が発出されました.それから2ヶ月経ち,一旦全国に発出された宣言が解除になり,6月1日からは,各企業で業務を本格的に再開されたことと思います.
このコラムが,コロナに伴う売上減,そのための生産減,更に,アフターコロナで激変する市場に対して,自社の生産体制をどうすべきかについて,苦慮されている皆さまのお役に立てればと願っております.
皆さまの会社の業種や置かれている状況が違いますので,具体的な解決案はお示しできませんが,トヨタで現職の頃,仲間とともに使っていた改革に向けた『キャッチコピー』が,その後コンサル業として多くの会社の改革のお手伝いで役に立ちましたので,此処で改めて皆さまの参考になればと思い,ご紹介したいと思います.
先回は
【A】「常に『目的は何か?』を問い直そう」
について紹介しました.
今回は
【B】「ぶつかった壁は『人が作った壁か?神様が作った壁か?』を考えよ!」「人が作ったモノなら変えることが出来るのだ」
【C】「ルールは変えるためにある」
という『キャッチコピー』を紹介します.
これらは,大野耐一氏ものづくりの仕組みを変え,トヨタ生産方式を構築するときに,頑迷な反対派を説き伏せるのに使ったものであると伝えられておりました.
特に,【B】の事例として原価改善活動の中で,『減価償却費』の扱いに関する論争が有名でした.
この話は,改善を志す皆さまにとって大切な事を多く含んでいますので,以下少し丁寧に紹介しましょう.
【B】
「ぶつかった壁は『人が作った壁か?神様が作った壁か?』を考えよ!」「人が作ったモノなら変えることが出来るのだ」
B-1.当時の日本の製造工場の状況
時代は1950年の朝鮮戦争勃発から1964年の初回東京オリンピック開催までの,戦後復興中の日本に戻ります.当時の日本の製造会社の状況を説明しましょう.
当時の事務所には今のような電子機器はなく,通信は電話とテレタイプ,郵便のみでした.計算はソロバンのみ,全て手書きの帳票でした.
生産管理部門は,営業からの販売計画から生産計画を立て,調達品の手配,各工程への生産指示にてんてこ舞いし,倉庫での行方不明部品を含め欠品騒ぎで明け暮れしていました.
それ故,月度内の個々の工程の生産は,製造現場に任せるしかありませんでした.
当時の製造現場は,鋳造・鍛造・機械加工・塗装など,職種別の徒弟制度に裏打ちされた職長を中心にしたムラ社会があり,あたかも職長を社長とした場内外注会社的な存在になっていましたから,本社機能は各ムラに月度生産量を指示するだけで,自律的に生産をこなしてくれていました.
その月の生産計画が,例えばA;10,000個,B;5,000個,C:3,000個であったとすれば,鋳造・鍛造……の職長は,『経理部門から出された原価目標』の評価を上げるために,月初からA⇒B⇒Cの順に生産し,欠品を起こさない様に早め早めに生産し月末の数日間は生産ゼロで,設備の点検をやる……というのが常態化していました.
当時の経営学の教科書には,完成品在庫は『財産』なので多いほど欠品のリスクを減らすので良いとされ,安全在庫を確保しておくことを推奨していて,多すぎると在庫金額の金利負担と,倉庫代がマイナス要因なので注意すること……と記されています.
B-2.大野氏,小ロット多回生産に挑む
トヨタでも同様の状態でしたが,当時大野耐一氏が取り組んでいた改善は,当時の石田退三社長の命令でもあったのですが,資金繰りがつかず倒産の危機に陥っていたトヨタを立て直す中で,棚卸資産つまり会社内に膨れ上がっている在庫を減らすことでした.具体的には,前記のA,B,Cの生産を月に1回から週に1回にすれば仕掛かり在庫は1/4に減りますし,更に毎日生産すれば,仕掛かり在庫は1/20に減ることになります.
B-3.減価償却費等が改善の壁となった
この,小ロット多回生産による資金繰り向上改革に対して,此処の『経理部門から出された原価目標』の中の『減価償却費』に対する考え方などが,改善の邪魔になって来たのでした.
現在でも同じ問題を抱えている会社も多く居ることから,少し詳しく説明します.
固定資産は法的に決められた耐用年数に亘って,定額法とか定率法という違いはあるモノの,取得費用を配分して計上しなければならないとされています.これが『減価償却費』というモノで,例えば7千万円の設備を購入して,法的償却年数が7年だったとすると,定額法では毎年減価償却費として1千万円計上しなければならないという事です.これは毎月83万円余になります.
このように月々高額の減価償却費を計上するので,設備を遊ばせるのは会社の損だとして,『設備稼働率』という指標を作り,当時のトヨタでも,各職場を評価していました.
製造原価の管理は,ある月の生産に要した費用の実績を基にして,製品1個当たりの予算を下式のように決めます.
この予算額に対して,その月の実績値を比較することで,1個当たりの製造原価の管理をしていました.
一目で分かるように,(1)式の中で減価償却費だけは,生産量に関係なく月額いくらとなっていますので,固定費と呼ばれています.沢山作るほど減価償却費の比率が下がって,そのぶん(1)式での計算上の原価が下がっていきます.
直接労務費は,段替えに掛かった時間も加算されますので,段替え回数を減らすほど(1)式の計算上の原価が下がっていきます.在庫は会計上,資産として計上されるので,(1)式をベースにしたKPIのもとでは,在庫はドンドン増えて行ってしまうのでした.
今でも経営学では『適正在庫』という概念があり,欠品による機会損失を防ぐためには在庫を多く持つことを勧め,在庫費用は在庫金額の金利負担と倉庫代だけと説いています.
B-4.人が作った壁であると論破して改革を進める
そんな逆風の中,当時機械工場長だった大野耐一氏は筆舌に尽くしがたい努力を重ね,小ロット多回生産を実現させ,いわゆる「かんばん」を使った小ロット多回生産による『後補充生産方式』(通称JIT生産)を完成させたのでした.
『量産効果』が固く信じられ,『量産効果』とする会計制度に真っ向から反する『JIT生産』は,現場の職長のみか,本社の経理部門までがこぞって反対する中で,大野耐一氏が皆を説得させた論法が冒頭の『神様が作った壁か?人が作った壁か?』だったのでした.
減価償却費が,時間とともに発生するというの『人が決めた概念』である.機械は,停まっている間は何の価値も減らない.稼働させた時だけ動く部分が摩耗するので,生産した量によって減価償却させるべきであり,それ故,神様から見れば『減価償却費は固定費ではなく変動費である』と主張しました.
労務費を1個当たり費用として計算するのは『人が決めたこと』である.人は作業量に関係なく,生きていくためには腹が減るのは『神様が決めたこと』であるから,出勤したら仕事の有り無しに関係なく1日分の給与を払わなければいけない.それ故『労務費は固定費である』としたのでした.
そのことから,多くの会社で使っている『設備稼働率』という概念は使わず,設備のavailabilityを『可動率』と名付け重視しています.又,『JIT生産』の為に増やした段替え回数や運搬回数に伴う工数増も,同じ人員数で,定時内に収まっている場合は,支払い労務費は同じですから工数増とはしません.この考え方で,つねに市場で売れた分だけを最小の在庫で生産していく体制を大野耐一氏は構築したのでした.(2)はその概念式を表します.
B-5.危機の中で従業員を守る方法でもある
この運用を違う立場から説明しますと,工場の生産量と市場での販売量の関係は,下記(2)式のように,常に一致している必要があります.工場の生産量は@従業員数A設備能力,B棚卸資産に関係しますが,会社のノウハウは@の従業員の中にしか存在していません.
今回の新型コロナのような,市場が萎縮した場合は,工場は当然生産量を減らす必要がありますが,工場内のB卸資産量を在庫日数で評価し,早めに手を打ち減少させていく必要があります.多くの会社は原価の8割が外注費になって居ますから,仕入れを先行して減らす事で従業員を養うことができるからです.一個ずつ工程間を手で運んで,極小の棚卸資産で運用するとことまでやるのが『JIT生産』の極意です.
ここまでやって従業員を守り抜き,アフターコロナの新しい成長に備えるのです.
それでも難しくなったら,A設備能力に手を掛け,売却,もしくは廃棄処分にして減価償却費負担を減らします.
その一方で,生産が追い付かないほど売れるときは,段替え時間を惜しんで大ロット生産し,在庫増には拘らず生産量を増やしていくことを意味しているのです.
B-6.管理会計での話ですので違法ではありません
誤解をされるといけませんので注釈を入れますが,会計には管理会計と財務会計(制度会計)とがあります.後者は過去1年間の間の企業活動の成果を法律に基づく計算法で会計処理し,損益計算書,貸借対照表,キャッシュフロー計算書等の財務諸表として公表し,当局に納税し,株主に配当する一連の会計活動を指します.これは自社で勝手に変えることは出来ません.トヨタも何ら違法はやっていません.
前者の管理会計は,目の前の市場の状況から,何をどうやったら利益を確保して企業を成長できるか・・・企業経理の指針を示すための会計で,どのようなやり方をするのかは各社が自由に選ぶことが出来ます.アメーバ会計やスループレット会計が有名です.大野耐一氏が変更させたのは,この管理会計での話でした.
労務費については独自の能率歩合制度で台当たり工数の改善を進め,原価管理は減価償却費を外した直接原価方式でやっていました.
それ故,此処で紹介した改革の方法は,法的に何の違反も無く,皆さまでも即採用できるモノなのです.
『神様が作った壁か?人が作った壁か』のお話しが,皆さまのアフターコロナに向けての改革に参考になれば幸です.
【C】
「ルールは変えるためにある」
これは,個人の暗黙知を形式知に変えに皆で共有し,より良い方向に改善していく活動を表す言葉なのです.
C-1.自己の確立と仲間意識の醸成のため『教育訓練を重視』
トヨタでは入社時に『入門編』,その後職務に即した『実務編』を,更に昇格時『管理者編』を,同期の者を10〜20名単位で部屋に集めて教育し,自職場で展開させ,相互職場訪問させDiscussionさせます.これは陽明学の『知行合一』即ち知識と行為は一体であるという思想の流れを汲むモノでした.普通の会社は『教育課』というところをトヨタは敢えて『教育訓練課』と名付け,いわゆる座学で教育するだけで無く,実践出来るまで教え,実践した結果を確認して初めて『教えたということ』になるとしていて,その覚悟を表す意味で『教育訓練課』としているのだと聞かされたモノでした.
入社同期生を一堂に会するのは,敢えてライバル意識を駆り立ててやる気を喚起すると同時に,同期の中での自分の位置付けを自分で判断させる為もありました.
その同期の集まりのDiscussionを人事係が観察する事で,客観的な人事評価が出来,配属された部署間の偏差を是正し,公正な人事評価に寄与することは,当の教育を受けている人達にも自ずと理解出来るのでした.
その中で行っていた『標準作業による改善活動』という教育訓練は,『トヨタ生産方式』の教育であると同時に,『品質教育』であり『安全教育』でもありました.管理監督者に対しては『部下の育成』の教育でもありました.
C-2.トヨタ生産方式における改善活動とは
この『標準作業・・・』の教育訓練の中味は,一般論で言えば
- Step1)『我流を統合しルール化する』⇒『そのルールを守る』
我流の統合とは,暗黙知を形式知にすることを意味する.そのル−ルを守るとは,皆が標準作業として遵守するという事.
- Step2)『より良くするためにルールを改定する』⇒『改定したルールを守る』
ルールを改定しそれを皆が守るとき,これを『改善』という
- Step3)『更に良くするためにルールを再改定する』⇒『再改定したルールを守る』
常により良い方法を求めながらも,決められた方法を守り,品質と生産性を維持向上させる職場を理想とする.
- Step4)教育訓練で学んだStep1〜3)を自職場で展開し,後輩を育てる.
…………
もう少し詳しく言えば,このように,各作業者の暗黙知としての作業方法を比べ,一番優れた作業方法を,表準作業(オモテ標準作業)と名付け,形式知として皆で守ることに決め,これがスタートラインになります.
ここから改善されたモノを『標準作業』と言い,いわゆるトヨタ式の改善活動になるのです.
更に,ルールには以下の6個の要件を備えていなければならないと教えます.
- いつ,
- 誰が,
- 何の目的で,
- 何を根拠に決め,
- 誰の承認を得たのか.
- それ故,どういう手続きで変えることができるのか
4.の根拠は以下の五種類に分類し,E.だけが現場で変えられるとしています.
- 神様が決めたこと(材質,強度,寸法等図面指示事項等々)
- 国の法律に基づくモノ
- お客様との契約
- 会社の規則
- 職場が決めたルール
5.と6.は,担当する職長と技術スタッフが最終承認することにしています.
それ故,表準作業票には,制作者名,製作年月日,根拠,承認者サインを記入します.改定時も同様にサインを求めています.
C-3.標準作業は会社の財産である
トヨタ生産方式に於ける『標準作業の改善活動』がどんな取り組みで,それが,働いている人たちにどのような誇りとやり甲斐を感じさせ,会社にどのような利益をもたらすか,つたない文章で書くよりも,ネット上の記事をご紹介した方が,思いを伝えることができると考え,『日本の清掃会社がハーバードビジネススクールの教材になるまで』を紹介します.
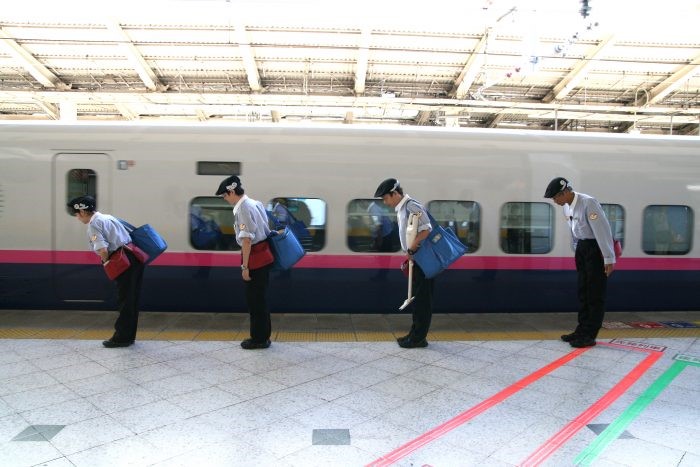
従来は,新幹線が東京駅について乗客を降ろすと,整備工場まで回送し,そこで車内を清掃し,又東京駅まで回送し,ホームで乗客を乗せ出発……だったのを,到着したホームで,乗客が降りた後,たった7分間で車内を整え.そのまま乗客を乗せて目的地に向かう方式に変えたのでした.
これが,鉄道会社に取ってどれだけ貢献しているか,想像してみて下さい.
7分で出来るようになったのは,彼等が改善に改善を重ねて来たから(標準作業を改善し,それを全員で守り,又改善し,又みんなで守る)達成出来たことなのです.
このような奇跡的清掃をやってくれる従業員は宝ですし,そのノウハウ(標準作業)も又,会社の財産なのです.
言い方を変えると,清掃員達の暗黙知を集めてきて,その中の一難良い方法を『表準』とし,全員で展開,その中で改善案が見つかれば,全員でそれを実施する……という,先に述べたことの中味が分かり頂けたと思います.
もし御社の作業現場が,やり方が作業者任せであれば.暗黙知がそのままで放置されており,大変もったいない状況にあるという事になります.
以上,様々なことを書きましたが,皆さまにアフターコロナ対応のお役に立てれば幸いです.皆さまのご健闘を願っております.
2020年6月
(株)Jコスト研究所 代表 田中正知
2020年4月
季節のご挨拶
〜提言〜
常に『目的は何か?』を問い直そう
4月が来ました.年度初めの月,人事異動の月,新学期の月でもあります.新しい職場,新しい仕事,新しい環境で心新たに取り組まれる皆様にエールをお送りいたします.
通例はこのようなご挨拶で済ませるのですが,2020年の今年は様子が違います.
毎日,新型コロナウイルスによるパンデミックにより,ご自身の健康はもちろん,ご家族の安全と,ご自身の職場大変動,市場の大混乱でご心痛のこととお察しいたします.一番のお困りごとは,今のパンデミックが今後どうなり,いつまで続くのか?ということではないかとお察しいたします.
今回は,喜寿を越えた,さまざまな実務を経験したOBの,岡目八目的な異見をお伝えしたいと思い,この文章を書いています.少々長文ですが,社会に,家庭に,重責を負われている皆様の参考になればと,老体に鞭打ってこれを書いています.
今日現在,諸外国は日本のパンデミックに対する対応が違うことを不審に思っています.政府でも企業体でも『高学歴者』がトップに立ち,指揮命令しているのは,その人たちが単なる体験ではなく学問として,『理路整然と整理した人間の行動学としての歴史』を学んだか,『自然現象の観察を通して身に着けた論理的な思考法で先を読む洞察力』を身に着けている…こういった能力を期待しているからでしょう.日本と諸外国との差が,歴史を軽視した教育体系のせいでないことを願うばかりです.
私自身もネットで壮絶な疫病の歴史を改めて知りました.戦争や交易,気象変動により人々が移動すると,土着の風土病だった感染症が免疫のない地域に感染爆発を引き起こし,人口が激減するほどの被害を与えていた,という事件が繰り返されていたことがわかります.
中世ヨーロッパにおける黒死病はあまりにも有名ですが,今の新型コロナについては,100年前の『スペイン風邪』が参考になります.
この例を下敷きにし,『改善マン』として今をどう捉え,何をすべきかの私見を申し述べます.
- 参考資料【スペイン風邪とは…】
Wikipediaによれば,第一次世界大戦中,アメリカから始まったとされています.
北米で発生したインフルエンザで,米軍とともに欧州に入り,戦場である欧州全域に,やがては全世界に蔓延しました.1918年1月から1920年12月まで3波に分かれて流行し,当時の世界人口の1/4に相当する5億人が感染したといわれています.戦時で士気に影響するとして伏されていましたが,推計で死者は1,700万〜5,000万人とされ,戦場では戦死した兵士より病死した兵士の方が多かったと伝えられています.また,この時は他のインフルエンザと比べて,若年成人の死亡率が高かったとも記されています.
スペイン風邪から約100年,中国から始まったCOVID-19というパンデミックが,感染の炎を燃え上がらせつつあります.スペイン風邪の例に倣えば,1波,2波,3波と再発して襲いかかり,ワクチンが普及するか,地域の人口の70%あまりが抗体を持つまで終息はせず,2〜3年は異常事態が続くことを……例えて言えば,人類とウイルスの第三次世界大戦が勃発した……という規模の大事件が起きた,と思うべきです.
こんな,それこそ『未曾有』の時,会社の命運を懸けて頑張る皆様に,贈る言葉があります.それは,
常に『目的は何か?』を問い直そう
という言葉です.これは,私がトヨタで先輩に叩き込まれた言葉でもあります.この言葉の意味は,ある『目的』を達成させようと,ある『手段』を用います.その『手段』がうまく行く様に何か『手段』を講じます.其れを円滑に進めようとある『手段』を……というように,手段が手段を呼び迷路に入り込み身動きできなくなってしまいがちです.この時に「『目的は何か?』を問い直せ!」ということで,これによって全体像が見え,Break Throughが出来るというコトなのです.
この言葉の原点は,20世紀初頭,豊田佐吉翁が織機(機織り機)の改良に取り組んでいたときにあり,この発想で『自働化』という新しい理念を発明し,それは織機に留まらず,現在もビジネス上の重要理念として世界中で役に立っています.
以下,その経緯を具体的に説明しましょう.
当時は,織機に使える動力と言えば 水車か蒸気機関しかありませんでした.当然,今のような電子制御はなく,カラクリで制御する時代でした.そんな環境下で世界中の発明家が,手間暇の掛かる「はたおり作業」を何とか機械化できないかと日夜改良に取り組んでいたのでした.
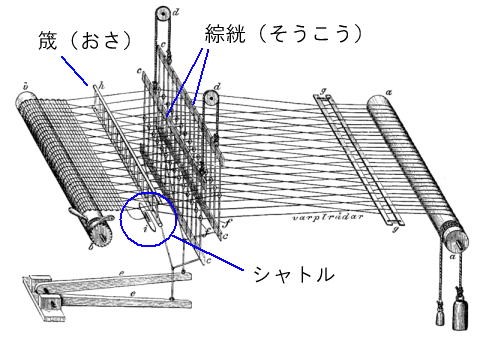
そもそも機織りとは,上図のように交互に上下する経糸の間を,横糸を入れたシャトルを通し,櫛状の「おさ」で押さえ込み,次に経糸を逆に上下させ横糸を通す……これを繰り返して,横糸を一本ずつ織り込んでいく動作を連続させていく作業です.簡単そうに見えますが,『力』の加減で出来上がった布の風合いを決めてしまうというデリケートな作業で,これを延々と続けることでやっと布が織れていくのです.又,横糸を巻いた糸巻きは上図のシャトル(杼)の中に納められていますが,布の途中で横糸が無くなるのは,布としての致命的な不良なので,早め早めに横糸が残っている状態で織機を停めて,シャトルを交換し,又起動させる必要があり,女工さんは機械に張り付いている必要がありました.世界中で,これを前提に,より高速化の改良を進めていたのでした.
つまり『織機一台あたりの生産性向上』に向かって挑戦していたのでした.
豊田佐吉翁も当初はこのトレンドで改良を進めていましたが,織機を停めてシャトルを交換するコトがNeckで機械の生産性は壁にぶつかっていたと言います.
ある時,佐吉翁は,そもそも女工さんに機械を操作させるということが間違いで,女工さんが就ききりでなくても,布を織ることが出来る『織機』を創ることが,目的であると気がついたのでした.
言い換えると,佐吉翁が織機を改善する目的は,世間でやっている『織機の生産性向上』ではなく,『女工さん一人が1日で生産する布の量を多くすること(労働生産性)』にある事に気がついたのでした.ということは,女工さんの監視を必要とせず,
- 機械が自ら横糸が減ってきたことを感知して,無停止でシャトルを交換すること.
- 経糸が切れたらそれを感知して,自ら瞬時に織機を停め,赤ランプで知らせる.
佐吉翁は,このように女工さん達の監視から外れても生産し続けられる機械を,『自働機(自ら働く機械)』と名付け,このような機能を持たせることを『自働化』と名付けました.会社名も一時『豊田自働織機製作所』と名乗っていました.
1924年『自働化』を完全に織り込んだ『G型自働織機』を完成させ,その特許を,織機発祥の英国企業に譲渡し,その資金で自動車の研究を始め,やがて今のトヨタ自動車に発展していったとされています.
佐吉翁の考え出した『自働化』という概念は21世紀の今日,
- 異常があったら直ちに生産を止めて直す
- 社内の異常を顕在化し全員で共有し,直していく
- 機械だけでやっていく仕事と,機械群を維持管理する人の仕事を分離する
- …………
この『自動化』のEpisodeと共に,トヨタでは「壁にぶつかったら『目的は何か?』と見直せ!」と叩き込まれるのです.
参考までに『目的は何か?』の活用例を紹介しましょう.
【例1】五輪選手は再考すべきか否か
新型コロナCOVID-19の影響で,TOKYO2020という名称はそのままに,オリンピック競技大会は2021年7月開催となった模様ですが,各競技団体が出場選手を再選考すべきか否かで揉めています.
この問題を『目的は何か?』を使って考えてみましょう.その前に,そもそもオリンピックの目的は何かを知る必要があります.
- オリンピック憲章1996年版より抜粋
- オリンピック・ムーブメントの目的は,いかなる差別をも伴うことなく,友情,連帯,フェアプレーの精神をもって相互に理解しあうオリンピック精神に基づいて行なわれるスポーツを通して青少年を教育することにより,平和でよりよい世界をつくることに貢献することにある.
- オリンピック・ムーブメントの活動は,結び合う5つの輪に象徴されるとおり普遍且つ恒久であり,五大陸にまたがるものである.その頂点に立つのが世界中の競技者を一堂にあつめて開催される偉大なスポーツの祭典,オリンピック競技大会である.
- スローガン 『より速く,より高く,より強く』
上記オリンピック憲章を要約すると「スポーツを通じて青少年を教育して平和でより良い世界を作る事」が目的で,それを推進するための手段としてオリンピック競技大会がある事が分かります.その根底には如何なる差別も排除するとしています.
もし,テレビの視聴率を上げたい,会場の観客数を増やしたいということを目的にするならば,今年の予選会代表として選ばれた人をそのままにして,練習風景などを中継し続ければ,Totalの出演料も増えるし受けもよい.費用も掛からない.
一方で憲章にあるように,20年開催として決められた選手を既得権益とみれば,その後伸びてきて21年にピークを迎える選手に対して差別することになる.21年度に向けて再度選考会を開けば,より多くの選手が刻苦勉励して,裾野が広がり,本来のオリンピックの目的に合うことになります.
『目的は何か?』で考えれば,何も迷うことなく1年ずらして再選考という結論になります.読者の皆さまはどうお考えでしょうか?
【例2】各社に存在する改革組織の『目的は何か?』
〜ここからが今回お伝えしたいことの本番です〜
マスコミの報道を見ていますと,報道の中味もコメンテーターの突っ込みも,『事の本質を理解せず,字面の質問』が多いのに深く失望しています.
もっと残念なのは,『今日,○○名の感染者が見つかりました』という発表を,そのまま視聴者に伝え,記者としての深掘りのない事でした.
全員を漏れなくて調査出来ない場合の調査方法は,『統計学』として確立されており,『どのような基準で検査対象者を選び出し,その中からn名調べたらp名の感染者がいた,だからSampleとしての感染率は(p/n)である.対象者はN名いるから,全体でP名が感染していると思われる……』という方法です.ニュースでお馴染みの『世論調査』は,結果と同時に調査条件も報道しています.
世界中が注視している中で,調査の条件をあきらかにせず,『今日の感染者○名』と発表する当局には『絶句!』ですが,この不当性を糾弾しない『学会』『野党』や『マスコミ』の姿勢にも『絶望感』を禁じ得ません.この国は『新型コロナ』の前に国家の中枢が『忖度病』に罹患しているようです.
今日現在,世界中のインテリ(医者だけではない)が各国の感染状況を見守っていますから,この稚拙な報道にあきれ返っていて,先進国の関係者は皆,2週間以内に日本で感染爆発が起きると,固唾を人で見守っていると報道されています.現に,英文で日本からの帰国勧告を出している国があるとか…….日本が科学立国とされていましたが,コロナの報道に度に,自ら今は科学後進国であるとアナウンスしているに等しい状態です.残念です.
政府やマスコミはこんなレベルでも,現在全世界を相手に厳しいビジネスを展開している 日本の実業界は,しっかりと科学的に判断して 取り組んでいて,大丈夫だと思います.その中に在って,このコラムの読者の皆さまは,様々な企業に中で『ものづくり』や『Supply-Chain』に関する『改革を推進する組織』に関係する皆さまだと思っております.
その皆さまと,今回の新型コロナのパンデミックが,ものづくり産業にどんな影響を与え,それ故どんな改革をすべきかについて,一緒に考えたいと思います.
【2-1】人類とウイルスの歴史を調べてみる
今回のパンデミック騒動の全体像と役所から次々と出て来る規制・要望の本当の目的を理解する為には,我々は,人類とウイルスの歴史にまで踏み込んで学び,自分で判断出来るレベルの知識と知恵を確保する必要があります.
先ず,ウイルスによる病気の歴史を調べてみましょう.皆さまも文献やネットでお調べ下さい.
戦前生まれに私は,子供の頃ウイルス性疾患の中で育ちました.天然痘は小学校で種痘を受け,麻疹にかかり,百日咳,風疹に掛かりました.この頃言われたことは,これらの病気は一度罹れば二度とかからない事と,更に幼い内は掛かっても軽いが,年を取るほど重くなり,大人になってからは重症になると言われていて,これらウイルスによる疾患は大人になるための『通過儀礼』であるとされていたのでした.実際,長男が幼稚園で『おたふく風邪』に感染した時,私にうつり,長男は寝込みませんでしたが,親である私は1週間寝込みました.
これらのウイルス性の病気は,当時の日本社会とともにあったので,殆どの人が抗体を持っていて,一時的に抗体を持っていない人の間を伝染していっても,間もなく自然に終息するのでした.
ところが,その社会にとって初めての(誰も抗体を持っていない)ウイルス性の病気が流行ると,状況は全く変わります.抗体を持っていないので,1人が2人に感染させるとすれば,2⇒4⇒8⇒16⇒32⇒64⇒…といった形に,指数関数的に増えていきます.急速に感染拡大した場合(感染爆発)は全員が感染します.ゆっくり感染が進む場合は,一旦終息したかに見えますが,2波,3波と続流行し,その地域の約70%の人達が感染し,抗体を持つようになります.こうなると先に述べた麻疹や風疹のようになるのです.
感染爆発の例で言えば,文献によると,15世紀から18世紀にかけてヨーロッパ人の侵攻とともに持ち込まれた麻疹や天然痘等によって,抗体のなかった当時のアメリカ先住民の人口は80%も減少したという研究もあると言います.また,冒頭に述べた,100年前のスペイン風邪は,『1918年のパンデミック』とも呼ばれ,世界中で5億人(当時の世界人口の1/4)が感染し,死者は推計1,700万人(1億人という説もある)とされています.
今流行って居る新型コロナCOVID-19も,誰も抗体を持って居ないので,放置すればスペイン風邪並みに全世界に広がる可能性があります.欧州や米国の当局の対応が早いのは,このスペイン風邪が人々の記憶にあるからでしょう.
【2-2】新型コロナは何時まで続くのか……
『お江戸名物火事・喧嘩』という言葉が残っているように,江戸初期の民家は藁葺きのうえ密集していましたから,一旦出火すれば瞬く間に燃え広がりました.直接火災を消す方法が無いに等しかった当時は,風下の家を強制的に倒壊させて燃えにくくして(火元から隔離して)類焼を防ぐというのが,当時の火消しの方法でした.3『密』の禁止,不要不急の外出自粛要請などは,人と人との間隔を開けて感染防止を図るだけであり,江戸の火消しと同じで,隔離して類焼を防いだに過ぎず,火の粉が飛んでくれば直ぐ火がつきます.
中国は回復しつつあるとか,韓国は山を越えた……等々に話がありますが,取り敢えず火事の火勢が衰えたというだけであり,いつか再び出火し,大火事になるかも知れないのです.現にその中国も,国内では小火が治まっていませんし,外国からの入国制限を厳しく行っています.
パンデミックの専門家である感染学者の見解は,2019年以前の自由な貿易・自由な人の出入りが復活するには,
- (医療崩壊を起こさないことが望まれるが)感染が広がり70%余が抗体を持つ.
- ワクチンが開発され,それを接種して1と併せて70%余が抗体を持つ.
- ウイルスを直接やっつける治療薬が開発され,病院に配られ治療が始まる. 上記1または2+3が出来て初めてインフルエンザ並みになる.
(1) 歴史を振り返ると
Wikipediaによれば,スペイン風邪は下記のように流行したとあります.
- 第1波
- 1918年3月,アメリカで発生,米軍参戦で欧州で5〜6月に流行.
- 第2波
- 1918年秋,世界中で同時流行,重篤な合併症を起こし死者急増.
- 第3波
- 1919年春〜秋,世界中で流行,最初に医療関係者が感染⇒医療体制崩壊⇒感染被害拡大
当時と今の交通量を比べますと,感染伝播の環境が格段に違います.
1920年(大正9年) | 現在 | |
---|---|---|
世界人口 | 約18億人 | 約77億人 |
大陸間交通 | 客船のみ | 航空機(13億人・2014年) |
大陸内交通 | 列車,馬車 | マイカー,バス,列車,航空機 |
(2) 今の世界の感染状況は猛烈な速さで進行中
4月1日現在の状況を見れば,
- 米国で死者4,000人突破.トランプ大統領は死者最大24万人予想.
- WHO事務局長予想:数日内に世界の感染者100万人.
日本では忖度が働いて,科学的Dataで理路整然と言えば『煽るな!』と批判される為,「大変だ」「可哀想」と感情に訴える報道されていますが…….海外では,放置すればこんなに悪くなると科学的に数値で表明します.各国の首脳は『スペイン風邪』を念頭に置いて,国民に訴えているのが分かります.
それゆえ我々は,日本国内の政府やマスコミに惑わされず,ネットや海外放送で世界の客観的なデータを把握し,文献を漁り,自分の頭で理解する必要があります.
一番大事なことは,今報道されていることは,火事で言えば消火作業の実況中継に過ぎず,各都市の火?を鎮めるのにあと何ヶ月かかり,各国として鎮火するのに何ヶ月かかるか,各国の焼失面積はどれ位かを,皆さまは自社の取扱商品の目で,今後の予想を今のうちに見極めることが肝要です.
(3) 自社の業務から見た,新型コロナの流行の期間と規模の予測
繰り返しになりますが,マスコミ報道は,我々自身が感染するか否かに重点を置いて報道して居ますが,我々は製造・物流・販売会社に勤めていますから,自社の業務への影響という観点から,日本各地,世界各国に於ける新型コロナの及ぼす影響の大きさ,期間の長さを,購買・営業・経営企画が中心になって,早期に把握する必要があります.自社のSupply-Chainのダメージ,納入先の動向,政府の方針等々を,拙速でも構いませんから,御社が自ら現地現物で調べることを強くおすすめいたします.
【2-3】新型コロナ流行中の自社改革の実行
〜各社の『生産革新を担う部署の目的は何か?』〜
(1)スポーツ選手は今何をやっている?
新型コロナの影響で,野球やサッカーのリーグ戦開幕が延長になっています.試合がない間,プロの選手は何をやっているのでしょうか?絶対に,部屋に籠もってカウチポテト……というにはあり得ません.グランドは使えない場合でも,体力の維持と,延長が2ヶ月なら,フォームの改造とかその間で出来る強化策を実行していることでしょう.
オリンピックの選手は,丸1年競技スケジュールが延びました.彼等にとっては,世界の強豪だけで無く,1年若い選手もライバルになります.彼等に勝てるように,1年間掛けて身体を作り変える練習に入っていることでしょう.
(2)新型コロナの流行期間をどう見るか?
以下の文章は,私が手の届く範囲の情報から得た結論です.皆さまも,ただ単に他人の情報を鵜呑みにするとか,上司の指示を待つとかせず,ご自身で納得いくまで調べ,ご自身の見解をお持ち下さい.
『疾風に勁草を知る』という言葉があります.日頃は目立たなくとも,異常時に頭角を現し,貢献する人のことを言います.今回の新型コロナでは,北海道の鈴木知事や,大阪の吉村知事などは,政府の指示を待たず,市民のために先頭に立って活躍します.御社に関わる情報は,社員の皆さま以外では収集することは出来ません.
『先ず隗よりはじめよ』という言葉があります.稚拙を承知で,私はこの文章を書いています.これを叩き台にして,皆さまの考えをまとめて,御社の危機突破を立案下さい.
-
日本の主要都市での流行
-
東京(首都圏)
一番の問題は,ギュウギュウ詰めの電車で通勤する首都圏に感染の火が付いたら,大変に厄介なことになります.緯度こそ違え,規模や地形が似ている ニューヨークが大変な基地になって居るので,今回のパンデミックは,東京が,感染爆発するか否かで大きく変わります.
韓国モデルを採用し,検査拡大で発見した軽症者を オリンピック村へ入れ,今は暇な客室乗務員や,オリンピックのボランティアなどを動員すれば,5ヶ月間で一応の終息を迎えることでしょう.(遅ればせながら,4月8日政府は『非常事態宣言』を出しましたが,二次災害を恐れるがあまり,出動した消防士に「ここは立ち入るな!」「ここは濡らすな!」などと活動を縛っているがごときの中身です.出動の効果は期待できず,こここそ『目的は何か』と問いたいところです.)
今のままの単なる自粛で,感染爆発が起きずに維持出来たとすれば,治まるのに10ヶ月程掛かる事でしょう.
不幸にして感染爆発が起きると,否応なしに首都圏が完全封鎖され,感染爆発はおよそ4ヶ月で終息することでしょうが,ニューヨーク並みに多数の死者が出ますし,経済損失は莫大になるでしょう.
関西圏,中部圏は東京圏に準じます.
-
その他の地方都市
規模が小さく,人口が少なく,密集していませんから,a,b,cとも東京より1ヶ月は短いと予想出来ます.日本全体で考えますと,速くて9月末,遅くて来年2月末で国内のみは,一応終息するでしょう.しかし中東・アフリカでは感染は治まらず,海外との出入国は閉ざされたままで居る可能性が極めて大きいと思います.
-
-
世界各国での流行の予測
-
感染は箸で食事をする国から始まった:中国・韓国・日本
これらは感染を遅らせる民俗的要因と思われます.
-
ナイフとフォークで食事する国に移った:西欧系
ナイフ・フォークはテーブルに直置き,固いパン,生ハム・チーズ等は店頭に晒す,土足で出入り等々,感染しやすい要素が在ります.
-
手掴みで食事する国に移りつつある;インド・中東・アフリカ
主食のチャバティ等は露店で手掴み販売,土足で出入り,等々感染しやすい要素あり.一番感染しやすい民俗的要因あり.
このように考えると,現状の国境封鎖状態で,北米・欧州が自国内で感染が鎮火するのに,ほぼ日本と同じで,後5〜10ヶ月間を要すると思います.
今から感染が始まる,インド・中東・アフリカ地域は,感染拡大は速いが,鎮火には内戦の難民等行政の統率が効かない人々が多数存在することを勘案すれば,速くても丸2年,長引けば3年余掛かりそうです.感染者がいなくなったという保証が無い限り,人の自由な出入りが出来ません.その結果,貿易は不活発になります.
私見ですが,このように考えると来年の7月のオリンピックに,インド・中東・アフリカは間に合わず, 2022年に再延期ということも在りうると案じております.
-
(3) 今後の国内の経済を予測する
このように理詰めで考えていきますと,国内での消費市場は,秋まで現在のような低迷が続くことが予測出来ます.そして年末から来年年初に掛けて徐々に回復すると考えられます.
しかし,今まで再三述べてきたように,ワクチンが開発され普及するか,世界の人口77億人の70%が感染して抗体を持つまでは,一旦治まっても,日本国内でも,世界各国でも,散発的に流行する状態が続くので,経済は完全に元には戻りません.
従って速くて丸2年,最悪3〜4年掛からないと,2019年並みの自由な貿易環境は望めないと思います.3〜4年という期間は過去2回あった世界大戦と同じ規模です.とすれば,
- 第一次世界大戦の前後で,世界はどう変わり,日本はどう変わったか.
- 第二次世界大戦の前後で,世界はどう変わり,日本はどう変わったか.
- ならば,このCOVID-19パンデミックの前後で,世界はどう変わり,日本はどう変わるのか.
しかし,一番大事なのは,その戦争中をいかに生き残るかです.生き残りの手段を考え,実行しながらも,終わった後,変わってしまっている世界で優位に立っている必要があります.
具体的には,皆さまが独自に考え 結論を出す問題ですが,幾つか『Jコスト論』から見た『考慮事項』を申し上げます.
『考慮事項』の一つは,オリンピック時の混雑緩和策として準備した『テレワーク』です.今,感染防止の『3蜜防止』活動で 世界中で実践しています.学校教育でも,韓国や米国でネットを使った在宅教育を始めています.このパンデミックが終わった頃は,格段に進歩し,VRやAIと結合して,情報だけを扱う本社機能は,仕事のやり方が激変するでしょう.
東京で言えば,丸の内や大手町の高層ビルに本社の情報処理機能を置く意味は全くなくなります.その上東京には『富士山の噴火』『台風による広大な水害危機』『首都直下型地震』等により,首都機能崩壊のリスクがあるので,先の見通せる企業は,ビルを高値で売り払い,地方に分散されるでしょう.
もう一つはSupply-Chain網です.今回のマスクがよい例で,世界中のマスクが中国で作っていたため,今回の新型コロナで中国政府が差し押さえ命令を出し,一時期,政府の緊急措置で中国の国内消費にまわされたと言います.国家体制を維持するための必須物資は,自国生産する必要性が顕在化しました.御社の扱っている製品も,『地産地消型』にして,ある地方の封鎖でも,ある程度の生産は維持出来るように改革をするべきでしょう.
ちなみにトヨタは,本社は豊田市,工場は,東日本・中部・九州の3ブロックに分割していて,何処で災害が起きても生産は維持出来るようになって居ます.また,今回のコロナウイルスで中国が封鎖された時,何かあると直ぐ停まるとされたトヨタは停まらず,停まらないハズの日産が停まりました.
(4) 自社改革として,どう考え,何をすべきか?!
さて,自社の改革を託された『ものづくり改革』Teamの皆さま,この新型コロナにまつわる操業低下……業種によっては20〜40%の減産で,しかも国内回復まで5〜10ヶ月,と言う事態をどう捉えますか?
『ものづくり改革』関係者は,絶好のチャンスと受け止めて欲しいのです.と言うのは,日頃改革案を提出しても『今は忙しいから・・・』とオクラになっていたと思うからです.
絶好のチャンスを活かすべき具体的な改革案立案と推進体制構築は,御社の改革のプロである皆さまのお仕事ですが,『Jコスト論』としては『こんな点を押さえて欲しい』と言う思いから,以下の文章を書きました.参考になれば幸いです.
-
改革のグランドデザインを先ず構築して下さい
グランドデザインは,
- 改革の目的,KPI
- 具体的な展開法 期間,組織を明確に期す.
-
計画は,
極短期 即時実施するもの 短期計画 1ヶ月間の直近計画 中期計画 国内が鎮火するまでに完了させる計画 長期計画 世界中で終息するまでの計画
-
短期計画までに取りこむべき事柄
以下,『Jコスト論』から導き出される実施事項を列記します.皆さまの改革計画の参考にして下さい.
-
改革推進体制づくり
各部署から一番優秀な人材,幹部候補生などを集めて『改革Team』を編成し,改革の全権を与えグランドデザインを作り,細部計画に展開し全社に指示し実務展開する.同時に,この活動を通じて人材育成を図る.その組織体は,下記のように階層別にし,全体最適に向けた迅速・強力な体制がよいでしょう.
会社全体 社長直属の改革Team 部門単位 役員直属の改革Team 部単位 部長直属の改革Team 課単位 課長直属の改革Team -
最優先は,在庫金額の削減⇒資金繰り対策
- 減産して完成品在庫を極小化する(運転資金確保)
- 減産を活用し,少ない仕掛かりで生産できる体制を構築する
- 仕入れSupply-Chainを総点検し,購入品在庫を低減する
-
事務処理まで含めたOrder-to-Delivery-Lead-Time短縮
-
中長期の改善計画は,次回にお話しします.
皆さまのご健闘を期待しています.
最後に参考資料として『地球大進化』NHKDVDをお薦めします.姉妹編の『地球大紀行』『人類誕生』も参考になります.内容は,生命体は平穏無事なときには進化せず,存続が危ぶまれるような危機に襲われたとき,大きな変化をし,生き延び,変化した種のみが危機が去った後繁栄してきた……と言う歴史を映像化したモノです.
2020年4月
(株)Jコスト研究所 代表 田中正知
2020年1月
代表新年のご挨拶
明けましておめでとうございます。
皆さまの益々のご活躍とご発展をお祈り致します。
お陰様で弊社も昨年は大きな成果を上げることができました。
国内では、足かけ4年ほどの間、一部上場企業様の上級管理者の研修を兼ねた、『Jコスト論』に基づいたOrder-to-Derivery-Lead-time短縮活動の展開のお手伝いをして参りましたが、鋳造管については従来の1/3まで短縮することが出来,又,自ら先頭に立って押し進め大きな成果を上げたことが管理者の皆さまの自信に繋がり,当初の研修目的を果たすことが出来ました。Client様だけで無く,弊社としましてもこの事を誇りに思っております。
中国では、6月に恒例の『Lean Summit in Shanghai 2019』の一環として、丸一日の『Jコスト論』の講習会を実施いたしました。それがご縁となり、河南省にある国営企業様の『Jコスト改革』のお手伝いを9月から開始しました。総経理も董事長も現場をまわり,自分の口から具体的指示を出しています。
着手した時点では,日本との差は大きいのですが,彼等の吸収力,実行力は素晴らしく,2020年度中に成果をあげ,2021年の『Lean Summit』で発表しよう大変意気込んでいて,今年の弊社の主要な業務になります。
さて2020年の重点目標は、
- 『Jコスト論』を英語圏へも広めていきたい
- 次世代を担う若い人たちと更なる『Jコスト論』の研究をしたい
本年もどうかよろしくお引き回しのほどをお願いいたします。
今月は正月に相応しく、中国で感じた軽い話題をお届けします。
【中国に抜き去られた話……】パスポートが切符代わりになった!
中国では高速鉄道の切符を買うのに身分証明書が必要で、外国人はパスポートが必要ですので、昨年末、中国で高速鉄道に乗ることになり、いつものようにパスポートを渡して切符の購入を中国の友人に頼みました。
「買ってきました。」と言ってその友人は私にパスポートだけを返してくれました。「切符は?」という問いかけに、「切符はパスポート内に入っている」という返事でした。
考えてみれば、航空券も、ホテルの予約もパスポートで行われており、もっと言えば入国審査もパスポートが言わば入場券の役割をしているとも言える……ので当たり前とも言えます。
日本では1960年、国鉄の座席予約Systemマルスとして発足し、新幹線網の発達とともに世界に誇れるSystemでありました。それ以降進化は続いていますが、令和の今日では、『裏が磁気テープの紙製の切符』と『手書き帳票』がまだ残っている分だけ、世界のTopランナーから見れば、周回遅れになっていると思えました。
【中国が日本に追いついてきた……】中国でシャワートイレ発見
2015年から習近平国家主席の号令で『トイレ革命』は始まったとされています。大都会のホテルでは、どこでも水洗トイレになってきていましたが、まだまだ日本のシャワートイレには巡り合っていませんでした。
12月末、中国からの帰途の上海⇒名古屋便は、建国70年記念年に建てたという上海浦東机場の新ターミナルからでした。中国の威信を懸けただけあって、大きく豪華な空間で、ビジネスクラス用ラウンジは最上階にあり、設備は完備していました。
トイレに入ると……そこにはなんとシャワートイレがありました!中国で初めての出会いでした!コントロールパネルには『ビデ』の表示はなく、『下身 FRONT』とありました。これが中国の新しい基準となるのでしょう。日本の最後の牙城、シャワートイレ文化が中国の中に溶け込み始めたと思うと、嬉しいような寂しいような複雑な気持ちになりました。
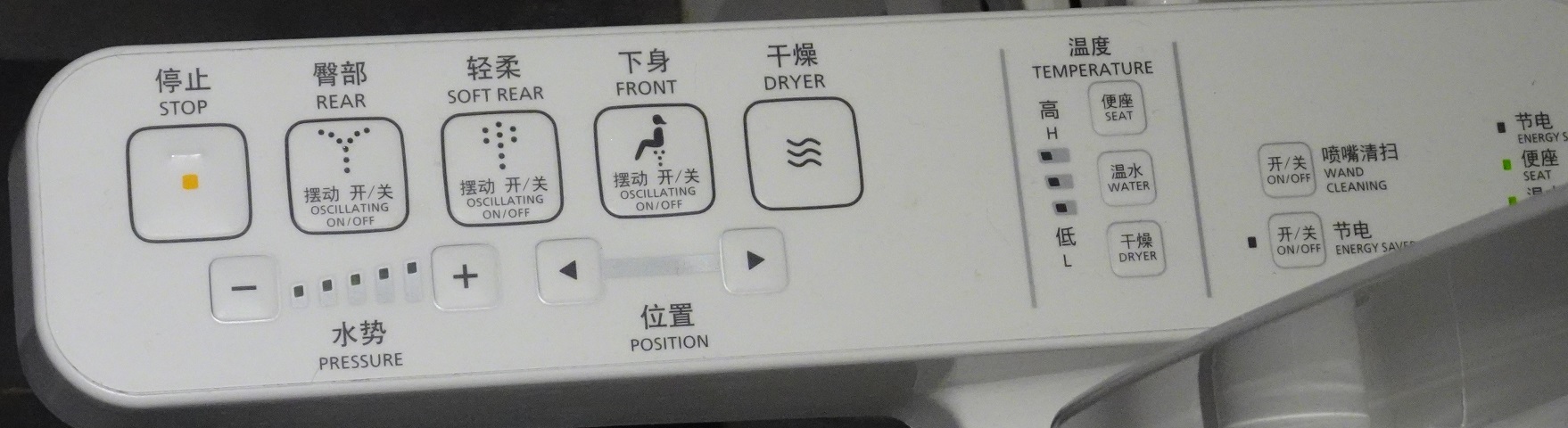
2020年元旦
(株)Jコスト研究所 代表 田中正知
2019年8月
残暑お見舞い申し上げます
令和の御代を迎え100余日が経ちました.今,新入社員の諸君は,入社後の所定の教育訓練を経て職場に配属され,本格的な仕事に取り組み始めた頃と思います.
職場の先輩から様々な職場のルールを教えられ,其れを身につけることで精一杯…という状況と思いますが,今こそ入社式での社長の訓示を思い出してください.出来れば,大学の同期生が就職した先(他社)の入社式での社長訓示をも,ネットで調べてみてください.
もしも御社の社長訓示が,『職場のルールを一刻も早く身につけ,社風に馴染んで即戦力になれ!』のような……,昔の結婚式で花嫁が白い打ち掛けを着て『私は白無垢です嫁ぎ先の家風に存分に染めてください……』と言うように,新入社員の個性・特技を無視したような内容だったら,その会社に未来がない……とお考えください.
一つの例をお話しします.
少し前,ある地方都市で癌検診を受けて間もなく死亡した患者の家族が不審に思い,問い合わせたところ,『要再検査』を間違えて『再検査不要』と転記ミスがあり,その結果手遅れになっていたことが判明しました.
マスコミは転記作業をダブルチェックするルールがあったのに実施してなかったという作業管理上の問題として取り上げて報道していました.
皆さまもこの事件は耳にしていると思いますが,どういう把握をしていますか?
ダブルチェックするというルールを守らせなかったことは役所として大失態ですが,それだけで良いのでしょうか?
もう一つの大きな問題は,本人⇔役所⇔検査機関の情報のやり取りを手書き文書で行うという旧態依然のまま放置してあった事にあると思いますが如何でしょうか?
因みに,先日中国成都にある陳麻婆豆腐の本店で食事したとき,店長が挨拶に来ました.その時,店長は通訳機を片手に私と会話し,『名刺交換』しました.
一方,同行した通訳役の中国人とは互いのスマホ間でQRコードの交換をし,即チャットし,スマホ同士の通信を確認して居ました.
先進国と思い込んでいる日本に比べ,つい数年前まで日本からODAを受けていた中国のEDI (電子情報交換)の普及が如何に進んでいるにか,その現実を目の当たりにしたのでした.
今,『働き方改革』と言う言葉が流行って居ますが,これは日本国中を被っている旧態依然とした業務の仕組みを変えなければいけないという『業務改革』から目をそらし,個人のせいにしてしまう恐ろしい副作用を持っています.
話は飛びますが,農業用語に『客土』という言葉があります.豊かな実りをもたらす土壌を維持するために肥料が毎年投入されますが,人体に於けるビタミンのように,作物が必要とする微量のミネラルは肥料としては与え難く,しかし作物に吸い取られ土壌からは年々減っていってしまいます.そのために山土など,ミネラルを豊富に含んだ別の場所の土を投入することを意味しています.
お話しを元に戻して,日本を代表するような企業の社長は,新入社員に向けての訓示では,先に述べた『客土』の如く,『和して同ぜず』,組織風土にミネラルを補充するが如く,新鮮な感覚で会社の業務を見つめ,問題点を発見し,失敗をおそれず改革に向けてドンドン挑戦して欲しい・・・・旨の内容になっています.
言い換えますと,先に述べた癌検診でのミスのように,『手入力による情報のやり取り』例えば『Fax』などがあれば,『何故EDI化が出来て居ないのか』を問題として取り上げ,その問題解決を自ら買って出て関係部署を説得し,改革を推進する・・・・.そんな姿を御社のTop は期待しているのです.
そのTopの期待に応えるにはどうしたらよいか…というと,新入社員は徹底して周囲に人に,今現在の仕事に進め方について『何故?なぜ?ナゼ?Why?…』と,納得できるまで徹底的に質問してください.2年間からは出来ない,1年目だけの特権だからです.
『何故?なぜ?ナゼ?Why?…』の質問で納得できれば,会社の仕事の仕組みが分かり,バリバリ効率よく仕事が出来る基礎知識が身についたことになります.
『何故?なぜ?ナゼ?Why?…』の質問で納得できなければ,其れを解決するのが『あなたの仕事』になります.自ら上司に具申して,その問題を解決する仕事に取り組んでください.
上司が得意とする分野の仕事を担当することは,部下にとっては『地獄』です.上司の『きめ細かなFollow』がついて回り,上司に褒められるには大変な苦労があります.
自ら具申して取り組んだ仕事の中身は,上司は不得手ですから地獄のFollowはありません.自ら計画し,自ら推進するわけですから,達成感が強く,仕事が楽しくなります.
何より,その範囲では,社内ではトップのスキルを身につけた,プロになれる道です.
トヨタに於ける私の経験では,何か新しいことを始めようとすると,必ず『2-6-2の法則』にぶつかります.つまり関係者の意見が概ね『積極派20%,消極派20%,浮動票60%』と言う構成になるのです.その積極派20%があなたの挑戦を助けてくれます.
そのようにして改革的な仕事を進めると,会社中の20%の積極派(将来幹部に昇格する可能性大)との人脈が出来ます.
会社組織の中での昇進・昇格は,実力だけで決まることではないので努力すれば Top までいけるとは保証しませんが,改革活動を進めて成果を上げてきたという実績は,会社を去った後でも世間から重要視され,その専門性を活かした有意義な仕事に就き,やり甲斐と高収入が生涯ついて回ります.
会社の Top の期待に応えるためにも,会社を成長させ社員を守る為にも,そして何より自分自身がその専門性を身につけ有意義な人生を全うするためにも.新入社員の諸君は『何故?なぜ?ナゼ?Why?…』の質問をぶっつけて,会社の抱える問題点をあぶり出し,顕在化させるところから始めてください.
諸君の御健闘を祈ります.
2019年8月 吉日
(株)Jコスト研究所 代表 田中正知